20 BBL Brewing Equipment
Commercial brewing equipment in the 20 BBL Brewing Equipment range allows medium-scale production for microbreweries and brewpubs. This guide covers key considerations for 20 BBL brewhouse systems from sizing to operation.
Overview of 20 BBL Brewing Equipment
20 BBL Brewing Equipment with an annual capacity of ~3,500-7,000 barrels are well-suited for expanding microbrewers seeking to grow production while retaining craft brew qualities.
A complete 20 BBL brewhouse package contains major equipment like:
- 20 BBL Mash Tun
- 20 BBL Lauter Tun
- 20 BBL Kettle
- Whirlpool
- Heat Exchanger
- Fermentation Tanks
- Brite Tanks
- Piping, pumps and controls
Additional equipment like milling, filtering, CIP systems, cooling towers and compressors are also included in turnkey systems.
When equipping a 20 BBL brewery, key factors to consider include:
Production Volume
Matching brewhouse size to annual barrelage output ensures optimal utilization rather than over-capacity. Expect ~150-300 barrels per 20 BBL batch.
Floor Space and Layout
Adequate floor space is required for safe movement of mobile vessels, storing supplies and expansion capacity. Proper equipment layout promotes material flow and brewhouse efficiency…
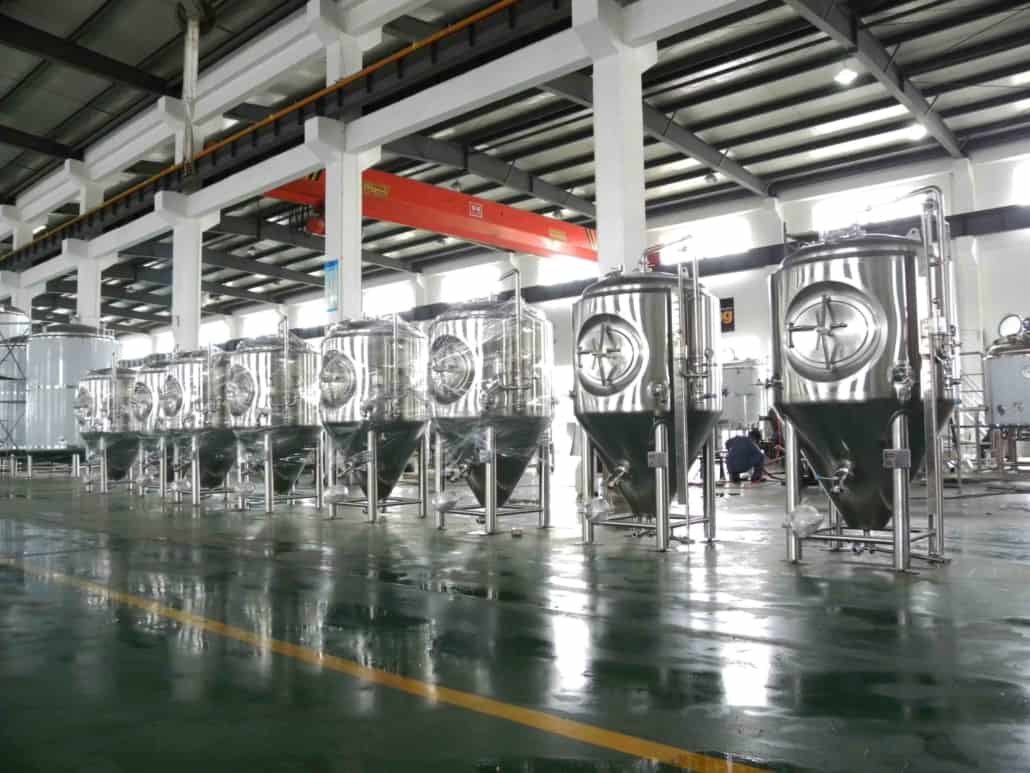
Types of 20 BBL Brewing Equipment
Major vessels and components in 20 BBL Brewing Equipment include:
Equipment | Description |
---|---|
Mash Tun | Mixes crushed malt (grist) with hot water to convert starches into fermentable sugars. Often dual purpose mash/lauter tun. |
Lauter Tun | Separates sweet wort from spent grain after mashing. |
Kettle | Boils wort with hops for aroma and bitterness. Often steam heated. |
Whirlpool | Settles hops, coagulants and protein trub after boil. |
Heat Exchanger | Cools hot wort quickly to pitching temperature. Plate or shell and tube types used. |
Fermenters | Convert sugars into alcohol and CO2. Usually stainless steel or stainless-insulated. |
Brite Tanks | Carbonate, clarify and store beer before packaging. |
Piping | Food-grade stainless steel piping connects vessels for transferring liquids. |
Pumps | Move liquid between stages. Centrifugal or rotary lobe constructions. |
Controls | Automated system measures and regulates process parameters. |
Customization
Brewhouse systems can be customized by capacity, raw materials, brewing methods and automation level to match operational needs and budgets…
20 BBL Brewing Process
A typical 20 barrel brewery utilizes a modular 4-vessel brewhouse system with the following process flow:
Milling – Barley malt is dry milled to crack kernels expose starch. Specialized roller mill equipment used.
Mashing – Milled grist is mixed with hot water in mash tun to convert starches to fermentable sugars via natural enzymes. Mashing may be done in single or multi-step infusions targeting different temperatures and conversion profiles.
Lautering – Mash is transferred to the lauter tun where sweet wort is separated from spent grains. Spent grain exits while clear wort recirculates to clarify before transferring to kettle.
Boiling – In the brew kettle, wort is boiled with hops for bitterness, flavor and aroma. Evaporation concentrates wort to target original gravity.
Whirlpool – Coagulants help settle hop particulates, proteins and trub into a cone in the middle of the whirlpool tank when rotated. Clear wort is then decanted..
Cooling – A plate heat exchanger quickly cools hot wort minimizing risk of contamination to yeast pitching temp ~50-60°F.
Fermentation – Yeast is added to cooled wort in fermenters. Over 5-7 days yeast convert sugars into CO2, alcohol and flavor compounds.
Conditioning – Beer is carbonated to style specifications and allowed to clarify in conditioning tanks prior to packaging.
Packaging – Bright beer transfers to bottling, canning or kegging lines for packaging final product.
20 BBL Brewing Equipment Suppliers and Pricing
Supplier | Price Range |
---|---|
SMB Machinery | $250,000 – $750,000 |
Ss Brewtech | $350,000 – $650,000 |
Psycho Brew | $300,000 – $800,000 |
AAA Metal Fabrication | $200,000 – $700,000 |
Portland Kettle Works | $400,000 – $900,000 |
Premier Stainless | $250,000 – $800,000 |
Pricing varies based on materials used (stainless vs. carbon steel), valves, automation level, customization and optional equipment.
Key Price Factors:
- Stainless steel kettles, mash tuns and tanks add ~25% cost versus clad carbon steel.
- Automation for measurement, valves and controls from ~$50,000.
- Grain handling systems $20,000+.
- Reverse osmosis filter $15,000.
- Installation, shipping and taxes additional. Get quotes from at least 3 vendors…
Operation, Cleaning and Maintenance
Activity | Description | Frequency |
---|---|---|
Calibration | Ensure sensors and metering devices give accurate readings. | Monthly |
Inspections | Check vessels, valves and pipes for damage or leaks. | Weekly |
CIP | Clean-in-place automated cleaning cycles. | After each batch |
CO2 line purging | Extended CO2 soaks prevent oxidation, infection. | Quarterly |
Preventative maintenance | Tunings, lubrication, adjustments etc. | Annual |
Thorough cleaning and maintenance is critical for ensuring quality, safety, efficiency and longevity of 20 BBL Brewing Equipment…
How to Choose a Brewhouse Supplier
Factors to evaluate in selecting a 20 BBL Brewing Equipment partner include:
Criteria | Considerations |
---|---|
Budget | Total equipment price, installation fees, shipping costs |
Lead time | Production planning, financing |
Customization | Match equipment layout, dimensions and flow |
Automation capabilities | Level of automation sought for operation, cleaning |
Track record | Years in business, number of systems built |
Service | Installation services offered, maintenance contracts |
Certifications | ASME, OSHA, UL, CRN for North American standards |
Warranty | Coverage terms for labor, parts, vessels |
References | Feedback from existing customers |
Getting quotes from multiple vendors allows balancing price, quality of construction, and service reputation. Prioritize suppliers who offer custom options tailored to your operational needs…
Pros and Cons of 20 BBL Brewing Equipment
Pros | Cons |
---|---|
Optimized batch sizes for micro and pub brewers | Larger equipment has higher fixed costs |
Flexible production planning with multiple weekly brews | Additional infrastructure needed for grain handling, wastewater, etc |
Capability for wide range of beer styles and innovation | Increased QA/QC overhead |
Significant growth runway before reaching capacity | Seasonal variations challenge consistent utilization |
Reasonable equipment diversity without excess redundancy | – |
Key Takeaways
- 20 barrel systems offer the “sweet spot” capacity for rapidly growing brewers
- Careful supplier selection and customization is key
- Additional investments required for infrastructure, storage, etc.
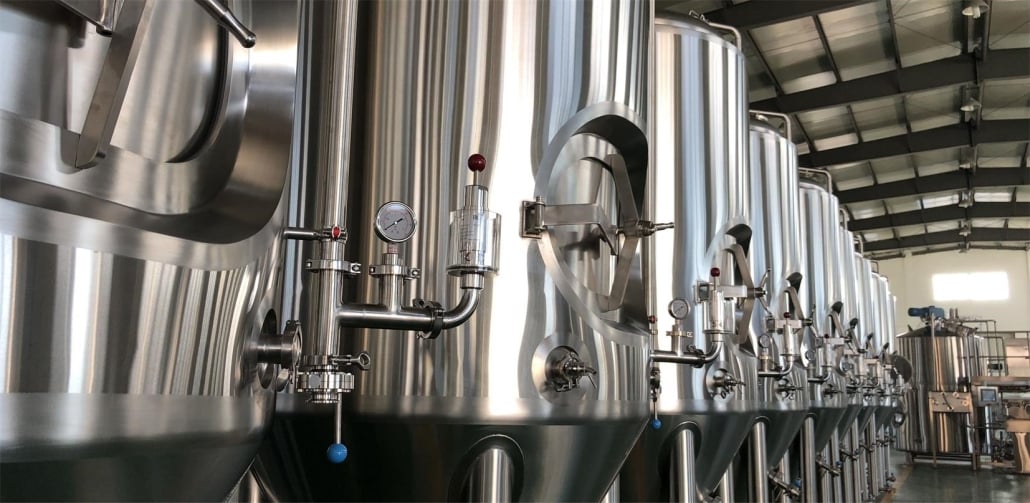
FAQs
Q: What size batches can a 20 BBL brewery produce?
A: With roughly 300 barrels annual output per batch, 20 BBL breweries can produce 3500-7000 total barrels per year operating at ~50-75% of theoretical capacity.
Q: How much can a new 20 BBL brewery expect to spend?
A: An turnkey 20 BBL brewhouse with fermentation hardware often ranges $400,000-$900,000. Additional costs for infrastructure, supplies and working capital must be accounted for.
Q: What raw materials do 20 BBL breweries require?
A: Key consumables are malt, hops and yeast with brewhouse requiring ~500-1000 lbs per batch. Other items include filtration media, cleaners, lubricants etc. Proper storage areas must be allocated.
Q: Should breweries buy new or used equipment?
A: High quality new equipment ensures long operational life, easy maintenance and avoids “surprises”. But used equipment costs 50%+ less. Reputable sellers offer rehauled vessels. Evaluate costs carefully.
Q: How many people are needed to operate a 20 BBL brewery?
A: Excluding serving staff, a 20 BBL production brewery can be operated by head brewer plus 3-5 full time employees handling cellaring, packaging, inventory, distribution and assistant brewing roles. Use contractors for maintenance and seasonal spikes.