Purchasing and Operating a 15 Barrel Brewhouse
15 BBL Brewhouse is a common system size for rapidly scaling craft breweries producing 3,000-10,000 BBLs annually. This complete guide explores what Owners need to know when investing in 15 BBL brewing systems, comparing equipment options, manufacturers, pricing, installation considerations, operation procedures, cleaning needs, pros and cons, and FAQs.
Use this comprehensive resource to make informed decisions when upgrading capacity to accelerate your craft beer production goals.
Overview of 15 BBL Brewhouse Systems
A brewhouse contains vessels for mashing, lautering, boiling wort, and whirlpooling finished beer before fermentation. Here’s what a typical 15 BBL system looks like:
Table 1. 15 Barrel Brewhouse Equipment Overview
Vessel | Overview |
---|---|
Mash Tun | Converts malt starches to fermentable sugars via hot water steeping |
Lauter Tun | Separates sweet wort from spent grains |
Brew Kettle | Boils wort with hops for aroma, flavor, preservation |
Whirlpool | Settles hop particulate matter, pumps clear wort to fermenters |
Control Panel | Automated recipe programming and data capture |
With integrated grain handling, wort boiling, and transfers between vessels, 15 BBL systems allow 1-3 brews daily to keep multiple fermenters filled. Output scales easily with additional fermentation and brite tank capacity.
Now let’s explore the various equipment options and configurations to consider.
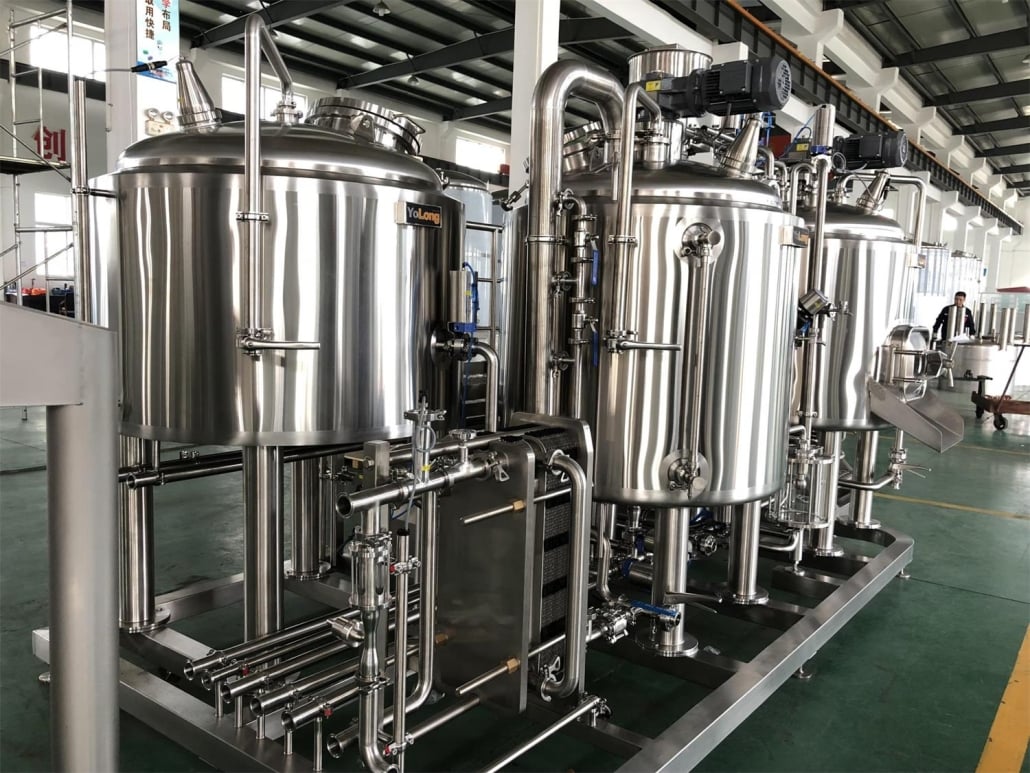
Types of 15 Barrel Brewhouse Configurations
While 15 BBL denotes batch size, many variations exist around heating methods, automation, vessel differentiation, and custom add-ons:
Table 2. 15 BBL Brew System Configurations
Type | Description |
---|---|
3-Vessel | Mash/lauter tun + kettle + whirlpool |
4-Vessel | Separate mash tun and lauter tun + kettle + whirlpool |
2-Vessel | Combined mash/lauter tun + kettle |
Steam vs Gas Heating | Steam boilers and injectors vs natural gas burners |
Direct vs Indirect Heat | Heating elements immersed vs external heat exchanger |
Automated | Programmable recipes, sensors, motorized valves and material handling |
Custom Fabrications | Add milling, sparging, grain out conveyance, hop dosing, etc |
While a basic brewhouse contains manually-operated mashing, boiling and whirlpooling functionality, advanced systems automate the entire brewing process for repeatability. Custom fabrications can tackle upstream milling or downstream fermenter fills or cellar transfers.
Weigh options around vessel differentiation, heating methods, automation needs and any specialty equipment integrations needed for operational efficiency in your facility. Getting the right system configuration to match your brewing style, skill level and growth plans is crucial before making this major investment.
Leading 15 BBL Brewhouse Manufacturers
Reputable commercial brewhouse fabricators offer configurable 15 BBL systems built to last decades. Here are prominent US manufacturers to evaluate:
Table 3. Notable 15 BBL Brewhouse Manufacturers
Company | Location | Price Range |
---|---|---|
JV Northwest | Canby, OR | $250,000 – $500,000 |
Specific Mechanical | Victoria, BC | $300,000 – $600,000 |
Premier Stainless | Escondido, CA | $350,000 – $750,000 |
AAA Metal Fabrication | Oregon City, OR | $275,000 – $525,000 |
Psycho Brew | Louisville, CO | $325,000 – $625,000 |
Craftwerk | Baltimore, MD | $250,000 – $700,000+ |
While many more brewhouse suppliers exist across North America, these companies provide high quality systems matched to the 15 BBL craft brewery market. Compare warranty programs, component manufacturers used, reference brewhouses installed, and customer reviews when selecting your vendor.
Now onto navigating the myriad equipment options and add-ons available.
Key 15 Barrel Brewhouse Components and Customization Options
Beyond standard vessels, customizable options exist for material handling, brewing efficiency, cleaning and automation enhancements when specifying your 15 BBL system:
Table 4. 15 BBL Brewhouse Components and Optional Customizations
Part | Standard Equipment | Optional Upgrades |
---|---|---|
Grist Case | 500 lb capacity | Larger capacity, integrated magnets, automated mixes |
Grist Hydration | Hot liquor spraying | Automated temperature and flow control |
Grist Out | Rotary feeder | Integrated screw or vacuum conveyor |
Mash Tun | Rakes, sensors, valves | Multi-step infusion programming, insulation, more rakes |
Lauter Tun | False bottom, sparge arms | Grant attachment for automated vorlauf and wort collection |
Kettle | Sight glass, sample valve, manways | Whirfloc addition, automated hop dosing, quick disconnects |
Whirlpool | Tangential inlet, side take-off | Automated valve switching to fermenters |
Steam System | Basic boiler, injectors | Redundancy, automated blowdown, advanced controls |
Control Panel | Basic analog, digital controls | Touchscreen interface, data logging, historians, remote monitoring |
CIP System | Basic manual CIP ball | Automated CIP recipe programming |
Grain Out Conveyor | none or basic conveyor | Integrated spent grain lift and dump automation |
Start by identifying must-have functionality based on your beer recipes. Then assess options balancing initial cost, long term labor savings, and final beer quality improvements that justify equipment investments. Consult with vendors around package pricing deals for common configurations.
Cost Breakdown – How Much Does a 15 BBL Brewhouse Cost?
While exact pricing fluctuates and depends heavily on your chosen manufacturers and custom options, here is an overview of typical 15 barrel brewhouse costs:
Table 5. 15 BBL Brew System Pricing
System Type | Price Range |
---|---|
Basic 3-vessel manually operated | $250,000 – $400,000 |
Fully automated 4-vessel | $400,000 – $750,000 |
High-end Steam brewery | $500,000 – $1,000,000 |
As shown above, costs for a brand new 15 BBL brewhouse span from $250,000 on the low end for a basic manually operated 3-vessel system, up to $750,000+ for a polished, shiny F1 racecar with highest degree of automation and customization from mash-in through fermenter fills. The sky’s the limit when adding specialty equipment onto every operational facet.
Get multiple quotes around desired functionality before making this game changing investment for your brewery. Now let’s cover physical brewhouse layout and infrastructure considerations.
How to Design and Lay Out a 15 BBL Brewhouse
Beyond equipment costs, allocating the physical space and infrastructure for your 15 BBL system is critical for installation and an efficiently designed brewery.
Table 6. 15 BBL Brewhouse Layout Planning
Consideration | Details |
---|---|
Space | ~1,000 sq ft+, ideally 40′ x 25′ empty span |
Floor | 8-12″ thick reinforced concrete slab, no cracks |
Doors | Double doors 16′ wide to fit vessels |
Ceiling Height | 20-30′ height, no obstructions |
Electrical | Full 3-phase 480V distribution panel, 150+ amp |
Potable Water | 2-3″ main line, high flow to support |
Sewer Drains | Floor trench drains able to handle hot liquid discharges |
Steam Lines | Schedule 80 main steam header line routed with good pitch |
Platforms | Stair / railing access around vessels |
Lighting | Vitally important – install lots! |
Ventilation | State and federal emissions regulations may apply |
Pay special attention to floor slab quality, drainage slopes, steam line professionally fabricated piping plans, and access within brewhouse cells for safe material handling. Investing in proper infrastructure avoids expensive change orders or Band Aid-fixes down the road after equipment arrives.
How to Install a 15 BBL Brewhouse the Right Way
Proper 15 BBL brewhouse installation ensures systems function optimally for years while avoiding safety hazards:
Table 7. 15 Barrel Brew System Installation Best Practices
Step | Checklist |
---|---|
Offloading | Forklift capacity, loading bay, rigging equipment |
Staging | Temporarily place vessels near final homes |
Leveling | Use lasers and shims to perfectly level vessels |
Pipe Fitting | Connect steam headers and returns properly |
Wire Electrical | Separate high and low amperage correctly |
Plumb Drains | Ensure adequate slope and trap primers |
Insulate | Wrap vessels, piping, valves for safety and efficiency |
Test | Commision equipment fully before first batch |
Safety | OSHA guard rails around vessels, signage |
Bringing in cranes or forklifts may be needed to place heavy vessels. Take the time to thoughtfully install infrastructure to avoid shortcuts leading to problems down the road. Passing inspections and testing before making commercial beer is mandatory.
With infrastructure and equipment in place, let’s tackle operations.
How to Brew on a 15 Barrel Brewhouse System
Skilled brewers utilize brewhouse equipment to produce consistent, quality beer batches after batch. 15 BBL systems involve larger recipes and equipment but generally follow standard brewing process flows:
15 BBL Brewhouse Brewing Steps
- Measure out grains and water volumes per recipe in the heated mash tun
- Mix thoroughly and rest during saccrification phase (~60 minutes)
- Recirculate wort, sparge to lauter tun and vorlauf until clear runoff
- Transfer cloudy sweet wort to the brew kettle
- Boil vigorous for 60-90 minutes, adding hops per schedule
- Whirlpool to settle hop trub, then transfer hot wort to fermenters
- Pitch freshly propagated yeast strains into cooled wort
- Ferment under controlled conditions per beer type
Brewers must expertly control temperatures and timing across vessels, monitor quality with lab samples and sensory checks, adjust water chemistry if needed, and ensure proper sanitation and yeast health for quality beer. Let’s shift to cleaning.
15 BBL Brewhouse Cleaning and Maintenance Needs
Keeping your scalable brewhouse in tip top running order through periods of heavy production requires diligent cleaning and preventative maintenance:
Table 8. 15 BBL Brew House Cleaning and Maintenance
Activity | Frequency | Tips |
---|---|---|
Daily rinse | After each brew day | Rinse vessels and pipes with hot water before residue dries |
Weekly deep clean | 1 full day each week | Full hot caustic CIP cycle followed by sanitizing pass |
Inspections | Monthly | Check each vessel, walk platforms/ladders, test emergency stops |
Gasket checks | Quarterly | Replace any worn out seals on manways or valves |
Passivation | As needed | Re-oxidize stainless surfaces losing sheen |
Major maintenance | Annual 2 week shutdown | Inspect inside vessels, replace rakes, hoses, gaskets etc |
Building these essential activities into the master brewery schedule ensures equipment keeps operating safely and efficiently with minimized unplanned downtime over decades of operation.
Next let’s run through key decision factors weighing the pros and cons of investing in 15 BBL capacity.
Pros and Cons Analysis – 15 Barrel Brewhouse Systems
If exploring the sizable investment into a brand new, scaled up brewhouse, here are salient points to consider around benefits and limitations of 15 BBL configurations:
Table 9. 15 Barrel Brew House Pros vs Cons
Pros | Cons |
---|---|
Efficient batch size for 5000 BBLs annual output | Major capital investment $500K+ |
Headroom for growth beyond current capacity | Significant space required, equipment footprint |
Automation possible for labor savings | Learning curve for new brewers to master systems |
Steam heating advantages | Potential bottlenecks around fermentation capacity |
Higher quality control capabilities | No flexibility around much smaller specialty batches |
Improved consistency and efficiency | Locked into equipment supplier long term |
Carefully weigh tradeoffs to determine if indeed stepping up to this midscale equipment size matches your brewery’s production goals, budget, and long term business strategy amidst competitive craft beer market dynamics. An engineering consultant can run ROI analyses around the significant spend.
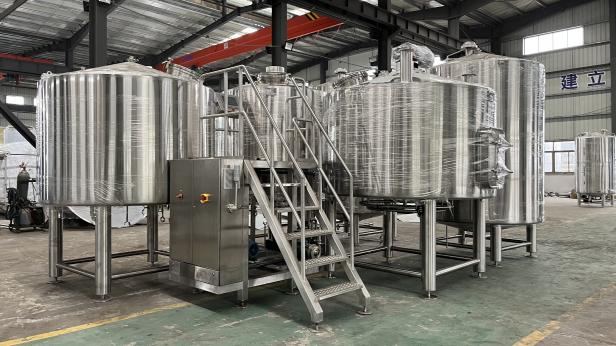
FAQ
Here are answers to some common questions brewers have around functionality when exploring 15 barrel system capabilities:
Table 10. 15 Barrel Brewhouse FAQs
Question | Answer |
---|---|
What’s the difference between direct vs indirect heating? | Direct steam injection or heating elements contact the wort, while indirect uses external heat exchangers. Direct can scorch wort if not closely monitored. Indirect allows finer temperature control. |
How long does it take to brew a 15 bbl batch? | With a single infusion mash rest around 60 minutes, 60 minute boil, and 45 minute clean-up, expect at least 3 hours but likely closer to 4-5 hours if including heating, sparge, whirlpool and transfers. This allows 1-2 brews daily. |
What are the pros and cons of steam vs gas heating? | Steam transfers heat very efficiently for faster ramp up. But natural gas gives more control over direct flame intensity during the boil. Steam condenser water usage can also drive up variable production costs if not reclaimed efficiently compared to gas. |
What are the differences between a 3-vessel vs 4-vessel brewhouse? | 4-vessel separates mash and lauter functionality into distinct tanks whereas 3-vessel combines them. 4-vessel allows further customization and parallel operations but takes up more space. Evaluate differences through quote comparison. |
Is automation worth the investment? | While automating the brewing process requires substantial controls engineering and equipment investment upfront, long term it provides labor cost savings, better recordkeeping, reduced human errors, and recipe repeatability batch to batch. |
What other brewhouse sizes should I consider? | Look above and below too – comparing quotes for 7bbl nano, 30 bbl or even 60 bbl systems against 15 bbl provides perspective on price per barrel and scalability up or down from your current production before committing. |
Further analyze any additional questions you have around vessel sizing, options, or configurability when determining the optimal system for your brewery. Identify the right brewhouse technology partner as well – you’ll collaborate over decades of growth together.
Key Takeaways – Investing in a 15 Barrel Brewhouse
In summary, while buying a new 15 BBL brew system represents major spending, expanded capacity unlocks revenue growth potential for 5000 barrel breweries looking to scale up production in coming years. Carefully weigh:
- Brewing functionality must-haves vs nice to have equipment customizations
- Various system configurations and add-ons spanning automation to infrastructure
- Tank heating mechanisms, vessel differentiation, and specialty integrations
- Quote comparisons around pricing, capabilities and manufacturing quality
- Getting layout and installation right from day one
- Training and safety considerations for smooth operations
- Prioritizing cleaning and maintenance for longevity
While navigating the dizzying array of brewhouse options, keep central focus on producing high quality, delicious beer cost effectively. Finding the right technology partner committed to transparently configuring systems perfectly matched to your brewing style, business objectives and growth enables leaping confidently into this exciting next chapter of expanded 15 BBL production capability.
Share this entry
Interested in learning more about Brewing Systems including additional details and pricing information? Please use the form below to contact us!
YOLONG BREWERY EQUIPMENT FAQS
- Commercial Brewery / Craft Brewery / Microbrewery / Nanobrewery
- What is The Difference Between Craft Beer and Industrial Beer?
- The Bespoke Differences In Custom Brewing Systems
- Everything You Need to Know About Kettle Souring
- How to Choose Brewing Equipment for Your business?
- How To Choose The-Best Partner To Build Your Commercial Microbrewing System?
- Two Detection Sensors That You Need To Use In Your Brewhouse System
- Remote Control Applications in Brewing Equipment/How does it work?
- How To Clean Your Brand New Brewery Tanks?