10 bbl Brewery
The world of brewing is expansive, especially when it comes to craft breweries. If you’re venturing into brewing on a larger scale, a 10 bbl brewery (10-barrel brewing system) might be the perfect setup for you. Whether you’re opening a new microbrewery or upgrading your brewing equipment, a 10 bbl system offers the capacity to brew substantial quantities without the overwhelming scale of industrial setups. But what do you need to know before diving in? This guide will walk you through every detail, from equipment specifications to operational procedures.
Overview of the 10 bbl Brewery System
A 10 bbl brewery refers to a brewing system with a capacity of 10 barrels of beer, which is roughly 310 gallons or 1,170 liters per batch. It’s a popular size for mid-level craft breweries, offering a balance between production volume and manageability. The 10 bbl system is large enough to meet growing demand yet small enough to be flexible for experimenting with new recipes.
For breweries aiming to sell locally or regionally, this size provides a sustainable operation without overextending resources. In this section, we’ll delve into the details of what makes a 10 bbl brewery a great choice for expanding or starting your brewing journey.
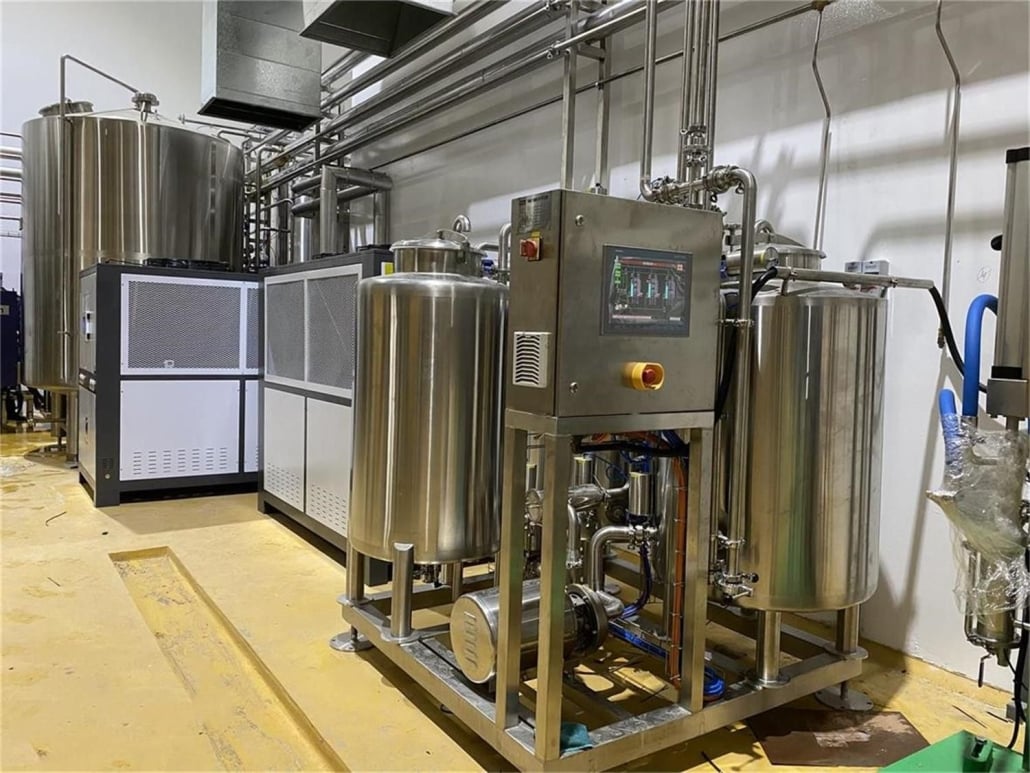
Equipment Guide for a 10 bbl Brewery System
A 10 bbl brewing system consists of various essential components that work in harmony to produce beer. Understanding each piece of equipment and its role in the process is vital to ensure efficient brewing operations.
Key Components of a 10 bbl Brewery
Equipment | Description |
---|---|
Mash Tun | This is where the mashing process happens. The malted barley is combined with hot water to convert the starches into fermentable sugars. |
Lauter Tun | After mashing, the lauter tun separates the wort (sugary liquid) from the spent grains. |
Brew Kettle | The wort is boiled in the brew kettle, where hops are added for flavor, bitterness, and aroma. |
Whirlpool | The whirlpool helps clarify the wort by removing hop particles and proteins before it goes to fermentation. |
Fermentation Tanks | After boiling, the wort is cooled and transferred to fermentation tanks, where yeast is added to begin fermentation. |
Heat Exchanger | A crucial component that rapidly cools the hot wort to an ideal temperature for yeast pitching, typically between 65°F and 75°F. |
Pumps | Pumps are used to transfer liquids between the brewing vessels. |
Control Panel | Modern systems are equipped with control panels to monitor temperature, pressure, and timing. |
CIP System (Clean-In-Place) | A cleaning system designed to automatically clean the brewing tanks and piping without needing to disassemble the equipment. |
Brewing Process in a 10 bbl Brewery
Brewing with a 10 bbl system follows the standard brewing process, though with slight variations to account for the scale and system specifics. Here’s a breakdown:
- Mashing: In the mash tun, milled grain (usually malted barley) is mixed with water and heated to activate enzymes that convert starches into fermentable sugars. The size of the mash tun ensures that a 10 bbl system can handle larger quantities of grain, which translates to a bigger output of wort.
- Lautering: After mashing, the mixture is transferred to the lauter tun, where the liquid wort is separated from the grain husks. A well-designed lauter tun ensures that wort separation happens efficiently, even at a larger capacity.
- Boiling: The wort is then boiled in the brew kettle. This is when hops are added for bitterness, flavor, and aroma. A 10 bbl system usually has a brew kettle large enough to allow for vigorous boiling, which helps evaporate unwanted compounds like DMS (dimethyl sulfide).
- Whirlpooling: After the boil, the wort is transferred to a whirlpool vessel where hop particles and other solids are removed. This step ensures clarity and purity of the wort before fermentation.
- Fermentation: The cooled wort is transferred to a fermenter, where yeast is added to begin the fermentation process. The fermentation tanks in a 10 bbl brewery are designed to maintain the correct pressure and temperature for optimal yeast activity.
- Conditioning: Once fermentation is complete, the beer can be conditioned or aged depending on the style. This can be done in the same tanks or transferred to bright tanks for additional clarity and carbonation.
- Packaging: After conditioning, the beer is either kegged, bottled, or canned for distribution.
Customizing Your 10 bbl Brewery: Capacity, Space, Design, and Layout
Designing a brewery is like designing a kitchen—you need a layout that supports efficiency and comfort, especially with a 10 bbl system. Here’s how to think about these factors.
Capacity and Space Requirements
A 10 bbl brewery system occupies a significant amount of space, so understanding spatial requirements is crucial to avoid operational bottlenecks.
Factor | Details |
---|---|
Capacity per batch | 310 gallons (1,170 liters) of beer per brew cycle. |
Space Requirements | At least 500 to 1,000 square feet of dedicated brewing space, depending on additional storage and operational needs. |
Height Clearance | Ceiling height of 12-16 feet is ideal for tanks and equipment, especially for fermenters and brewhouses. |
Ventilation | Proper ventilation is essential due to heat and steam generated during the brewing process. |
Tank Layout | Fermenters, mash tuns, and kettles should be arranged for efficient movement of liquids between vessels. |
Storage | Space for grain storage, keg storage, and packaging materials is vital, ideally adjacent to the brewing area. |
Utilities | Ensure access to power, water, and gas connections, especially for larger tanks and heating elements. |
Designing a Brewery Layout
In designing your 10 bbl brewery, consider the flow of the brewing process from mashing to packaging. An effective layout minimizes the distance between equipment, making the brewing process more efficient. Group your hot side (mash tun, lauter tun, brew kettle) together, and keep the cold side (fermenters, brite tanks) nearby but separate for optimal temperature control.
Customization Options:
- Automated Control Panels: These can streamline the brewing process by automating temperature regulation, pump operations, and other tasks.
- Modular Tanks: Depending on your production needs, you can add extra fermentation tanks or brite tanks to increase production without overhauling your entire system.
- Heating Methods: Options include direct fire, steam, or electric heating. Steam is the most efficient for larger systems, but direct fire can be cheaper to set up.
Suppliers and Price Range of 10 bbl Breweries
There’s a wide range of suppliers for 10 bbl systems, each offering different levels of customization and price points. Prices can vary greatly based on the features, materials, and country of manufacture.
Supplier | Price Range | Customization Options | Origin |
---|---|---|---|
ABC Brewing Systems | $70,000 – $100,000 | Full customization | USA |
Premier Stainless Systems | $90,000 – $120,000 | Modular, expandable | USA |
Stout Tanks and Kettles | $75,000 – $110,000 | Customizable tanks | USA |
SS Brewtech | $80,000 – $150,000 | Full automated systems | USA/China |
DEGONG Brewery Equipment | $60,000 – $90,000 | Modular systems | China |
Factors Impacting Price:
- Material: Stainless steel is the most common material, known for durability and easy cleaning. The grade of stainless steel (304 vs. 316) can affect price and corrosion resistance.
- Automation: Fully automated systems cost significantly more than manual or semi-automated setups.
- Country of Manufacture: US-made systems generally cost more due to higher labor and material costs, but they may come with better warranties and customer service.
Installation, Operation, and Maintenance of a 10 bbl Brewery
Getting a 10 bbl brewery up and running requires careful planning, particularly regarding installation, operation, and ongoing maintenance.
Stage | Details |
---|---|
Installation | Installing a 10 bbl system requires a professional team, often provided by the supplier. Utilities like water, gas, and electricity need to be configured. |
Operation | Operating the system involves managing the brewing process from start to finish, including monitoring temperatures, controlling pumps, and managing yeast health. |
Downtime | Regular maintenance checks help prevent downtime, which can be costly for a production-based business. |
Maintenance | Regular cleaning of tanks, lines, and heat exchangers is essential. A CIP (Clean-In-Place) system can simplify this process and prolong the life of the equipment. |
How to Choose a Supplier for a 10 bbl Brewery
Selecting the right supplier can make or break your brewery’s success. Here’s what to look for:
Criteria | Details |
---|---|
Experience and Reputation | Look for suppliers with extensive experience and positive reviews. Ask for references from other breweries. |
Customization Options | Ensure the supplier can tailor the system to your space, brewing style, and operational preferences. |
Technical Support | Choose suppliers that offer ongoing technical support and training, especially if you’re opting for an automated system. |
Warranty and Service | A good supplier should offer warranties on equipment and have a responsive service team for repairs and maintenance issues. |
Delivery and Installation | Check if the supplier provides delivery and installation services, as this can save you time and reduce the risk of installation issues. |
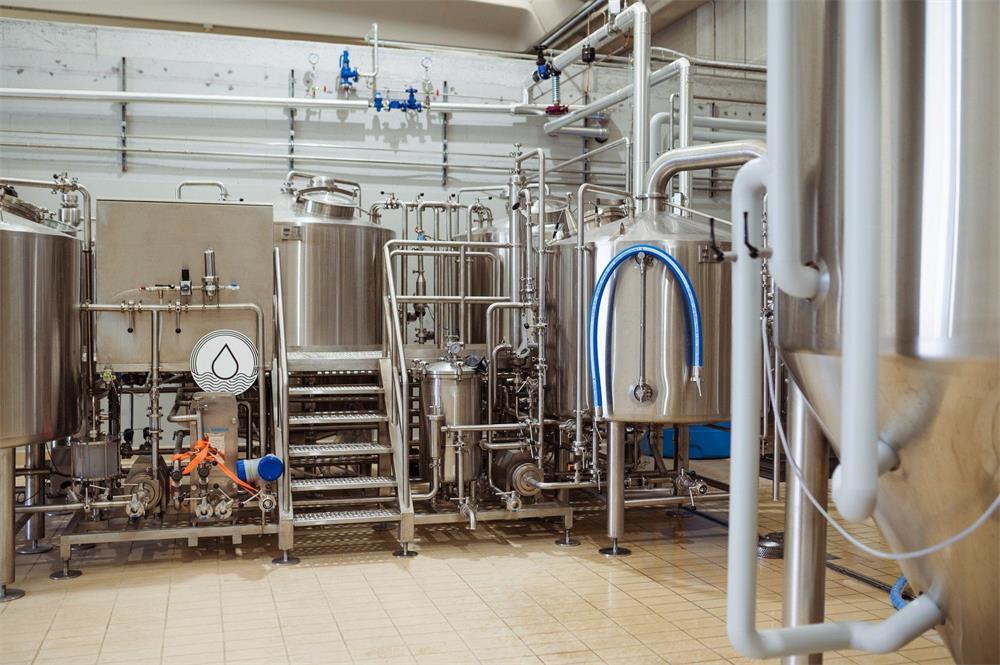
Comparing Advantages and Limitations of a 10 bbl Brewery
Choosing a 10 bbl brewery system offers unique benefits but also comes with a few limitations compared to smaller or larger systems.
Advantages | Limitations |
---|---|
Scalability: Ideal size for microbreweries that want to grow production. | Cost: Initial investment can be significant, especially with automation. |
Flexibility: Can handle a wide variety of beer styles and experimental batches. | Space: Requires significant space, making it unsuitable for smaller breweries. |
Production Volume: Large enough to meet regional or local demand while maintaining craft quality. | Complexity: May require more skilled labor and technical knowledge compared to smaller systems. |
FAQs
Question | Answer |
---|---|
What is the typical output of a 10 bbl brewery? | A 10 bbl system produces around 310 gallons of beer per batch, which can translate to around 1,000-1,300 pints of beer, depending on the beer style and yield. |
Can a 10 bbl system be operated by a small team? | Yes, many 10 bbl systems can be operated by 2-4 people, depending on the level of automation and batch complexity. |
What is the average time for brewing on a 10 bbl? | From start to finish, including fermentation, it can take anywhere from 2 to 6 weeks, depending on the beer style and the fermentation time required. |
How often should a 10 bbl system be cleaned? | A CIP (Clean-In-Place) system can be used after every brew to clean tanks and piping. Thorough cleaning of all components should be done every few months. |
How much does a 10 bbl brewery cost? | Prices range from $60,000 to $150,000 depending on features, customization, and the country of manufacture. |
Share this entry
Interested in learning more about Brewing Systems including additional details and pricing information? Please use the form below to contact us!
YOLONG BREWERY EQUIPMENT FAQS
- Commercial Brewery / Craft Brewery / Microbrewery / Nanobrewery
- What is The Difference Between Craft Beer and Industrial Beer?
- The Bespoke Differences In Custom Brewing Systems
- Everything You Need to Know About Kettle Souring
- How to Choose Brewing Equipment for Your business?
- How To Choose The-Best Partner To Build Your Commercial Microbrewing System?
- Two Detection Sensors That You Need To Use In Your Brewhouse System
- Remote Control Applications in Brewing Equipment/How does it work?
- How To Clean Your Brand New Brewery Tanks?