The Ultimate Guide to a 10 BBL Brewery
Overview of a 10 BBL Brewery
A 10 BBL brewery is a brewing system with a capacity of 10 barrels, where one barrel equals 31 gallons. This system is ideal for small to medium-sized craft breweries looking to scale up production while maintaining control over quality. A 10 BBL system allows brewers to produce around 310 gallons of beer per batch, making it a popular choice for those aiming to serve a local market or expand distribution without investing in an industrial-scale operation.
The 10 BBL brewery strikes a perfect balance between volume and manageability, offering the flexibility to experiment with new recipes while meeting consumer demand. It’s a versatile setup that supports different brewing styles, batch sizes, and fermentation techniques. Whether you’re brewing a hoppy IPA or a rich stout, the 10 BBL system provides ample room for creativity.
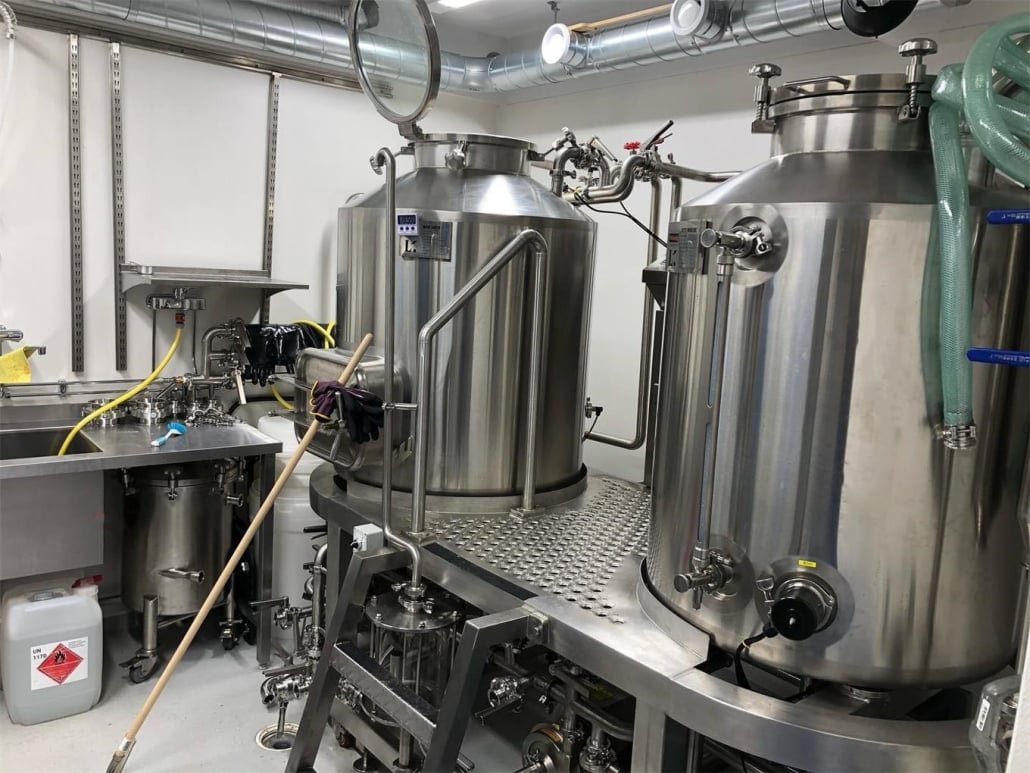
The Essential Guide to 10 BBL Brewery Equipment
Investing in a 10 BBL brewery involves understanding the various components that make up the brewing system. Each piece of equipment plays a crucial role in ensuring the efficiency, quality, and consistency of the brewing process.
Key Components of a 10 BBL Brewery
- Mash Tun: The vessel where the mashing process occurs, converting the starches in malt into fermentable sugars.
- Lauter Tun: Used to separate the wort (liquid) from the grain husks after the mashing process.
- Brew Kettle/Whirlpool: Where the wort is boiled, and hops are added to achieve the desired bitterness and aroma.
- Hot Liquor Tank: Heats and stores hot water used in various stages of the brewing process.
- Fermenters: Vessels where the wort is fermented into beer after the addition of yeast.
- Bright Tanks: Used for beer conditioning, carbonation, and storage before packaging.
- Heat Exchanger: Cools down the wort quickly before it is transferred to fermenters, preventing contamination and unwanted flavors.
Overview of 10 BBL Brewery Equipment
Equipment | Function | Key Features | Considerations |
---|---|---|---|
Mash Tun | Converts starches into fermentable sugars | Insulation, agitator, false bottom | Material quality, insulation efficiency |
Lauter Tun | Separates wort from grain husks | Rakes, adjustable knives, large wort outlet | Separation efficiency, ease of cleaning |
Brew Kettle/Whirlpool | Boils wort and adds hops | Vortex breaker, steam jacket, insulation | Heating efficiency, ease of operation |
Hot Liquor Tank | Heats and stores water for brewing | Insulation, sight glass, heating elements | Heating capacity, insulation |
Fermenters | Ferments wort into beer | Conical bottom, cooling jackets, CIP system | Cooling efficiency, volume capacity |
Bright Tanks | Conditions, carbonates, and stores beer | Pressure rated, carbonation stone, insulation | Pressure handling, cooling efficiency |
Heat Exchanger | Cools wort rapidly before fermentation | Plate or tubular design, stainless steel | Cooling rate, ease of cleaning |
Brewing Process in a 10 BBL Brewery
The brewing process in a 10 BBL brewery follows a series of steps, each critical to the final product’s quality. From mashing to fermentation and packaging, every stage must be executed with precision to ensure the beer’s flavor, clarity, and stability.
Step 1: Mashing
Mashing is the process where milled grains (usually malted barley) are mixed with hot water in the mash tun. This mixture, called the mash, undergoes a biochemical reaction where enzymes break down the starches in the grain into fermentable sugars. The temperature, pH, and time are carefully controlled to optimize enzyme activity and ensure a consistent conversion rate.
Step 2: Lautering
After mashing, the mash is transferred to the lauter tun, where the liquid wort is separated from the spent grains. The lauter tun features a false bottom and rakes to assist in the separation process. The wort is then drained and sparged (rinsed with hot water) to extract as much sugar as possible.
Step 3: Boiling
The wort is then transferred to the brew kettle, where it is boiled for 60 to 90 minutes. During this stage, hops are added at different intervals to impart bitterness, flavor, and aroma. Boiling also sterilizes the wort and precipitates unwanted proteins, which are removed through a whirlpool process after boiling.
Step 4: Cooling
After boiling, the wort must be cooled rapidly to a temperature suitable for yeast pitching. This is done using a heat exchanger, which passes the hot wort through a series of plates or tubes where it exchanges heat with cold water or glycol. Rapid cooling is crucial to avoid bacterial contamination and preserve the beer’s flavor.
Step 5: Fermentation
Once cooled, the wort is transferred to fermenters, where yeast is added to begin the fermentation process. The yeast converts the fermentable sugars in the wort into alcohol and carbon dioxide. Fermentation can take anywhere from a few days to several weeks, depending on the beer style and desired characteristics.
Step 6: Conditioning
After fermentation, the beer is conditioned in bright tanks. During this stage, the beer is carbonated and allowed to mature, which improves its flavor and clarity. Bright tanks are also where any final adjustments, such as dry hopping or adding flavorings, are made.
Step 7: Packaging
Finally, the beer is ready for packaging. Depending on the brewery’s setup, the beer can be packaged in kegs, bottles, or cans. Each packaging method has its advantages and requires specific equipment to ensure the beer’s quality and shelf life.
Customization and Design Considerations for a 10 BBL Brewery
When setting up a 10 BBL brewery, customization and design are key factors that can influence the efficiency, workflow, and overall success of the brewery. Whether you’re working with a compact space or planning for future expansion, careful planning and design can make a significant difference.
Space and Layout
The layout of a 10 BBL brewery should be designed to optimize the flow of ingredients, equipment, and staff. This includes the placement of mash tuns, fermenters, and bright tanks to minimize movement and maximize efficiency. Adequate space must also be allocated for storage, utilities, and packaging areas.
Capacity and Scalability
While a 10 BBL brewery offers a specific production capacity, it’s essential to consider scalability if you plan to increase production in the future. This could involve investing in larger fermenters or additional tanks, as well as ensuring that your heating, cooling, and utilities can handle increased demand.
Customization Options
Customization options for a 10 BBL brewery include specialized brewing systems tailored to your brewing style, such as incorporating additional vessels for step mashing or a more complex CIP (Clean-In-Place) system for easier maintenance. You can also choose from various materials, finishes, and automation levels based on your budget and operational needs.
Design and Customization Options for 10 BBL Breweries
Aspect | Considerations | Customization Options |
---|---|---|
Space Layout | Workflow optimization, equipment placement | Compact designs, modular setups, open layouts |
Capacity | Current vs. future production needs | Larger fermenters, additional tanks, expansion |
Materials | Durability, ease of cleaning | Stainless steel, copper, custom finishes |
Automation | Ease of operation, consistency | Semi-automated, fully automated systems |
Special Features | Brewing style, efficiency improvements | Step mashing vessels, enhanced CIP systems |
Choosing the Right 10 BBL Brewery Supplier
Selecting a reliable supplier for your 10 BBL brewery is crucial for ensuring that you get high-quality equipment, excellent customer service, and ongoing support. There are many factors to consider when choosing a supplier, from their reputation in the industry to the warranties and after-sales services they offer.
Factors to Consider When Choosing a Supplier
- Reputation and Reviews: Look for suppliers with a strong reputation in the industry and positive reviews from other brewers. This is often a good indicator of their reliability and the quality of their equipment.
- Pricing and Value: Compare pricing from multiple suppliers to ensure you’re getting the best value for your investment. Remember, the cheapest option isn’t always the best, as lower prices can sometimes mean lower quality.
- Warranty and Support: Ensure that the supplier offers a comprehensive warranty and reliable after-sales support. This will give you peace of mind and help you address any issues that may arise during installation or operation.
Comparison of 10 BBL Brewery Suppliers
Supplier | Reputation | Price Range | Warranty | Support Services |
Supplier A | High | $50,000 – $75,000 | 5-year warranty | 24/7 support, installation assistance |
Supplier B | Medium | $45,000 – $70,000 | 3-year warranty | Installation support, training |
Supplier C | High | $55,000 – $80,000 | 5-year warranty | Comprehensive after-sales service |
Supplier D | Low | $40,000 – $60,000 | 2-year warranty | Basic support, limited hours |
Installation, Operation, and Maintenance of a 10 BBL Brewery
Operating a 10 BBL brewery involves more than just brewing beer. Proper installation, operation, and maintenance are key to ensuring the longevity of your equipment and the quality of your beer. Below, we delve into these aspects in more detail.
Installation
Installing a 10 BBL brewery requires careful planning and coordination. This involves everything from site preparation and utility hookups to ensuring that all equipment is installed according to the manufacturer’s specifications. Professional installation services are recommended to avoid potential issues that could affect your brewery’s operation.
Operation
Operating a 10 BBL brewery involves understanding each piece of equipment and how it functions within the brewing process. Training is essential for both the head brewer and any staff members to ensure that the brewery runs smoothly and efficiently. Additionally, maintaining proper records of each brew can help in identifying any operational issues and improving processes.
Maintenance
Regular maintenance is crucial for preventing downtime and ensuring that your equipment performs optimally. This includes routine cleaning, inspection, and replacement of worn parts. A well-maintained brewery not only produces better beer but also extends the life of the equipment, providing a better return on investment.
Installation, Operation, and Maintenance Guide
Aspect | Key Points | Best Practices |
---|---|---|
Installation | Site preparation, utility setup, professional help | Hire professionals, follow manufacturer guidelines |
Operation | Equipment training, process control | Regular staff training, detailed brewing logs |
Maintenance | Cleaning, inspection, part replacement | Routine schedule, use of quality replacement parts |
How to Choose the Best 10 BBL Brewery for Your Needs
Selecting the right 10 BBL brewery depends on various factors, including your production goals, budget, and available space. Here, we compare the key considerations you should take into account to make the best choice for your brewery.
Capacity and Production Goals
Your production goals are perhaps the most critical factor when choosing a 10 BBL brewery. If you plan to produce large volumes of beer regularly, you’ll need a system that can handle the increased demand. Conversely, if you aim to brew smaller, more experimental batches, a system with flexibility and scalability may be more suitable.
Budget Constraints
Budget is always a major consideration. While it might be tempting to go for the cheapest option, it’s essential to think long-term. Investing in a higher-quality system can save money in the long run by reducing maintenance costs and improving efficiency.
Space Availability
The space you have available will dictate the size and configuration of your brewery. A compact space may require a more vertical setup or modular equipment, while a larger space could allow for a more traditional horizontal layout.
Customization Needs
If you have specific brewing styles or processes in mind, customization options can make a significant difference. Whether it’s additional vessels for complex mashing techniques or enhanced automation for consistency, customization can help you tailor the brewery to your needs.
Factors in Choosing a 10 BBL Brewery
Factor | Considerations | Recommended Option |
---|---|---|
Capacity | Regular large batches vs. experimental small batches | Larger fermenters for high volume, flexible setups for small batches |
Budget | Initial cost vs. long-term savings | Invest in quality equipment to reduce long-term costs |
Space | Compact vs. large brewing space | Modular systems for small spaces, traditional setups for large spaces |
Customization | Specific brewing techniques and styles | Tailored vessels, automation options |
Advantages and Disadvantages of a 10 BBL Brewery
Like any brewing system, a 10 BBL brewery comes with its own set of pros and cons. Understanding these can help you determine whether this is the right system for your brewing goals.
Advantages
- Scalability: A 10 BBL system is scalable, making it ideal for breweries looking to grow.
- Flexibility: The system allows for a wide range of brewing styles and batch sizes, providing creative freedom.
- Cost-Effective: Compared to larger systems, a 10 BBL brewery offers a good balance between cost and production capacity.
- Manageable Size: It’s large enough to meet significant demand but small enough to be manageable by a small team.
Disadvantages
- Space Requirements: A 10 BBL brewery requires a significant amount of space, which may not be feasible for all locations.
- Initial Investment: The upfront cost can be high, particularly when considering high-quality equipment and customization.
- Maintenance Needs: With more complex systems come higher maintenance demands, which can add to the overall cost and time investment.
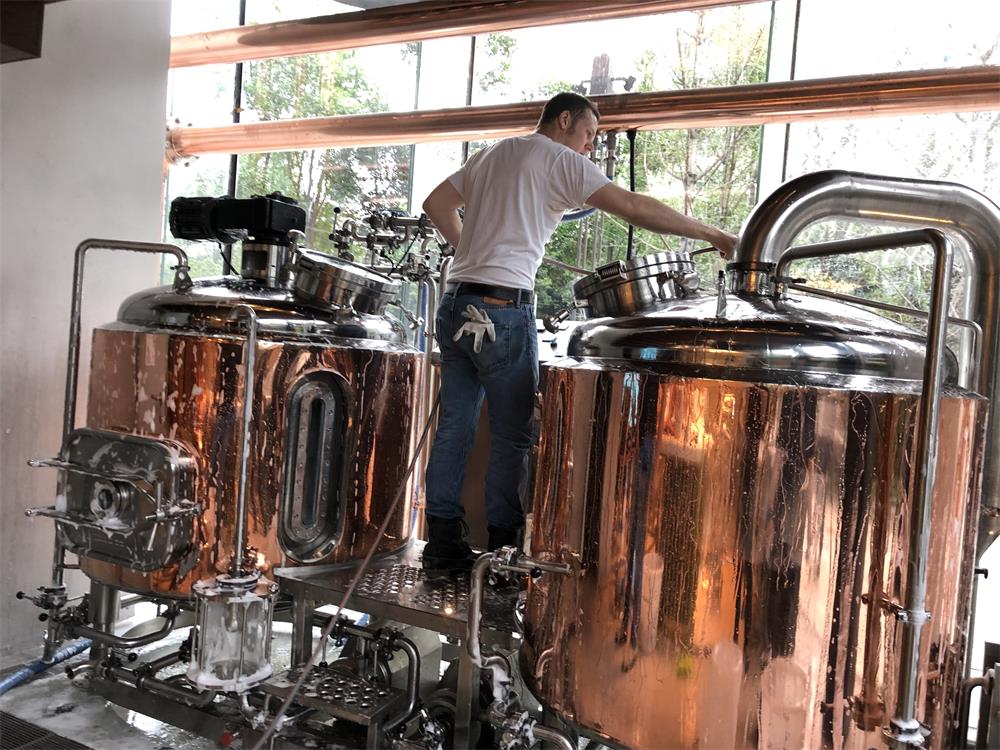
Pros and Cons of a 10 BBL Brewery
Aspect | Advantages | Disadvantages |
---|---|---|
Scalability | Ideal for growing breweries | May require additional investment as you scale |
Flexibility | Supports a wide range of brewing styles | Requires more complex equipment and knowledge |
Cost-Effectiveness | Good balance of cost and capacity | Higher upfront costs compared to smaller systems |
Manageability | Can be operated by a small team | Requires significant space and maintenance |
FAQs
What is a 10 BBL brewery?
A 10 BBL brewery is a brewing system that produces 10 barrels (310 gallons) of beer per batch, making it suitable for small to medium-sized craft breweries.
How much space do I need for a 10 BBL brewery?
The space required for a 10 BBL brewery can vary, but you typically need at least 1,500 to 2,500 square feet to accommodate the equipment, storage, and workspace.
What is the cost of setting up a 10 BBL brewery?
The cost can range from $50,000 to $100,000 or more, depending on the equipment quality, customization, and installation requirements.
How long does it take to brew a batch in a 10 BBL system?
Brewing a batch in a 10 BBL system typically takes 4 to 8 hours, depending on the complexity of the recipe and the efficiency of the system.
Can a 10 BBL brewery be expanded in the future?
Yes, a 10 BBL brewery is scalable. You can add more fermenters, upgrade tanks, or even increase the system’s capacity as your production needs grow.
Share this entry
Interested in learning more about Brewing Systems including additional details and pricing information? Please use the form below to contact us!
YOLONG BREWERY EQUIPMENT FAQS
- Commercial Brewery / Craft Brewery / Microbrewery / Nanobrewery
- What is The Difference Between Craft Beer and Industrial Beer?
- The Bespoke Differences In Custom Brewing Systems
- Everything You Need to Know About Kettle Souring
- How to Choose Brewing Equipment for Your business?
- How To Choose The-Best Partner To Build Your Commercial Microbrewing System?
- Two Detection Sensors That You Need To Use In Your Brewhouse System
- Remote Control Applications in Brewing Equipment/How does it work?
- How To Clean Your Brand New Brewery Tanks?