1 BBL Brewing System: Equipment, Process, and More
Overview: What is a 1 BBL Brewing System?
If you’re passionate about brewing your own craft beer or starting a microbrewery, understanding the right brewing system is crucial. The 1 BBL (Barrel) brewing system is a popular choice for those who want to dive into small-scale brewing. But what exactly does this system entail? A 1 BBL brewing system typically refers to a brewing setup with a capacity to brew 1 barrel of beer, equivalent to 31 gallons or about 117 liters. This size is ideal for small breweries, startups, or serious homebrewers aiming to produce craft beer at a larger scale than typical homebrew kits.
The system’s compact size allows for easier management of resources, making it a great entry point for those stepping into the commercial brewing world. But it’s not just about size; it’s about the precision, control, and consistency this system offers, which is why many brewers consider it the perfect balance between homebrewing and commercial brewing.
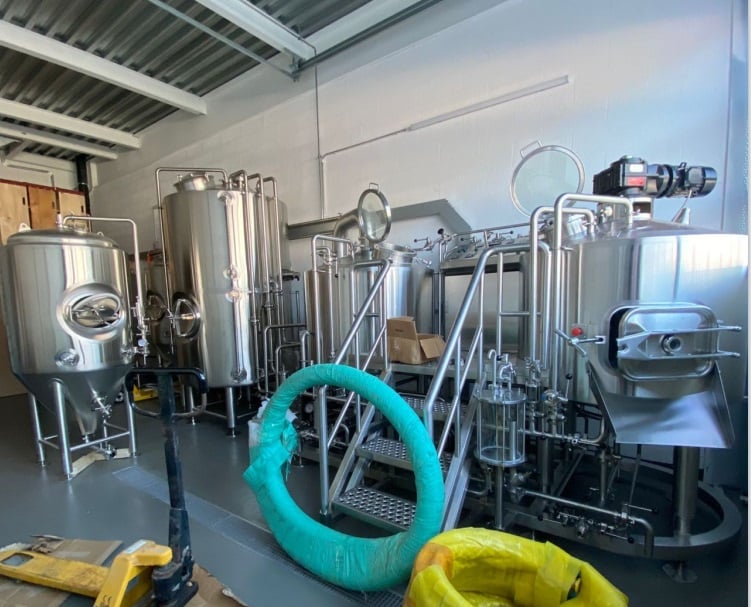
A Comprehensive Guide to 1 BBL Brewing Equipment
To get started with a 1 BBL brewing system, you need to understand the components involved. Each piece of equipment plays a critical role in the brewing process, and knowing how they all fit together can help you make informed decisions.
Key Components of a 1 BBL Brewing System:
- Brewhouse: The heart of the brewing operation where mash, boil, and wort production happen. It includes the mash tun, lauter tun, and brew kettle.
- Fermentation Tanks: These tanks hold the wort after brewing for fermentation. Their design allows for temperature control, crucial for consistent results.
- Hot Liquor Tank (HLT): Used to heat and store hot water necessary for mashing and sparging processes.
- Cold Liquor Tank (CLT): Stores chilled water, used in cooling the wort post-boil before fermentation begins.
- Heat Exchanger: An essential tool for cooling the hot wort rapidly, preventing unwanted bacteria growth.
- Pump: Helps in transferring liquids between different brewing stages, ensuring efficient and safe movement.
- Controls: Includes digital or analog control systems to manage temperatures, flow rates, and other brewing parameters.
- Cleaning in Place (CIP) System: An integrated cleaning system designed for sanitizing tanks and lines without disassembly.
Types of 1 BBL Brewing Equipment
Equipment Type | Description | Core Functionality | Design Considerations |
---|---|---|---|
Brewhouse | Includes mash tun, lauter tun, and brew kettle. | Main area for mashing, boiling, and wort production. | Should be made of high-quality stainless steel for durability. |
Fermentation Tanks | Cylindrical or conical tanks designed to hold wort during fermentation. | Facilitates the fermentation process with controlled temperature. | Requires precise temperature control mechanisms. |
Hot Liquor Tank (HLT) | Tank used to heat and store hot water. | Provides hot water for mashing and sparging. | Must have effective insulation to maintain temperature. |
Cold Liquor Tank (CLT) | Used for storing and chilling water. | Cools the wort after boiling. | Should have efficient cooling capabilities. |
Heat Exchanger | Device for quickly cooling the wort before fermentation. | Ensures rapid cooling to safe fermentation temperatures. | Requires easy cleaning access to prevent contamination. |
Pump | Facilitates the movement of liquids between different stages of brewing. | Transfers wort and water between different brewing stages. | Must be food-grade and capable of handling high temperatures. |
Control Systems | Digital or analog systems for monitoring and controlling the brewing process. | Manages temperature, flow rates, and other critical parameters. | Should offer precise and user-friendly control options. |
Cleaning in Place (CIP) | Integrated cleaning mechanism designed to clean tanks and lines without needing disassembly. | Ensures hygiene and prevents contamination between batches. | Must be thorough and easy to operate for regular maintenance. |
The Brewing Process: Step-by-Step with a 1 BBL System
Brewing with a 1 BBL system is more than just following a recipe; it’s about mastering a process that turns raw ingredients into a delicious final product. Here’s a detailed breakdown of how the brewing process unfolds using a 1 BBL system.
1. Mashing
The brewing process starts with mashing, where the milled grains (usually malt) are mixed with hot water in the mash tun. This mixture, known as the mash, is maintained at a specific temperature to activate enzymes that convert the starches in the grains into fermentable sugars. This step is crucial as it determines the alcohol content and body of the beer.
2. Lautering
Once the mashing is complete, the mash is transferred to the lauter tun. Here, the liquid wort is separated from the solid grain husks. This process is vital to ensure that the wort is clear, as cloudy wort can affect the flavor and stability of the beer. Sparging, the process of rinsing the grains with hot water, helps extract more fermentable sugars.
3. Boiling
After lautering, the wort is moved to the brew kettle where it is boiled. Boiling is essential to sterilize the wort, extract flavors from hops, and eliminate unwanted compounds. This step also allows brewers to adjust the bitterness and aroma of the beer by adding hops at different times.
4. Cooling
Post-boil, the wort needs to be cooled quickly to a temperature suitable for fermentation. This is where the heat exchanger comes into play, rapidly cooling the wort while minimizing the risk of contamination. The cooled wort is then transferred to the fermentation tank.
5. Fermentation
In the fermentation tank, yeast is added to the cooled wort, initiating the fermentation process. The yeast consumes the fermentable sugars, producing alcohol and carbon dioxide in return. Depending on the beer style, fermentation can take anywhere from a few days to several weeks.
6. Conditioning
After fermentation, the beer may undergo conditioning. This stage allows flavors to mature and develop, leading to a smoother and more refined final product. Conditioning can occur in the same fermentation tank or in a separate conditioning tank.
7. Packaging
Finally, once the beer has reached its desired flavor profile, it’s ready for packaging. Whether it’s bottled, canned, or kegged, careful attention is given to maintaining the beer’s freshness and quality during this step.
Design, Capacity, and Layout Considerations for a 1 BBL Brewing System
Feature | Details | Design & Layout |
---|---|---|
Capacity | 1 BBL (31 gallons or 117 liters). Ideal for small-scale brewing. | Compact size, suitable for small spaces and startups. |
Space Requirements | Requires a moderate space, typically around 100-150 square feet, depending on additional equipment. | Layout should allow for easy movement and access to all components, with consideration for future expansion. |
System Design | Modular design, typically made from stainless steel. | Customizable designs are available, allowing for specific brewing needs or space constraints. |
Layout Considerations | Requires space for brewhouse, fermentation tanks, and utility systems like water and power supply. | Considerations include workflow efficiency, sanitation, and easy access to control panels and CIP systems. |
Customization Options | Ability to upgrade or add features like automated controls, extra fermentation tanks, or enhanced CIP systems. | Customization allows tailoring the system to specific brewing processes or recipes, making it versatile for various beer styles. |
Selecting the Right Supplier for a 1 BBL Brewing System
Choosing a supplier for your 1 BBL brewing system is a critical decision. The right supplier not only provides high-quality equipment but also offers valuable support and expertise. Here’s how to navigate this important choice.
1. Reputation and Experience
Look for suppliers with a solid reputation and years of experience in the brewing industry. A well-established supplier is likely to offer more reliable equipment and better customer service. Check reviews, ask for references, and see if the supplier has worked with other breweries of your size.
2. Range of Equipment
Ensure the supplier offers a comprehensive range of brewing equipment. This includes not just the brewhouse but also fermentation tanks, heat exchangers, pumps, and control systems. Having a single source for all your equipment can simplify installation and maintenance.
3. Customization Options
Every brewery has unique needs, so it’s essential to choose a supplier that offers customization. Whether you need specific tank sizes, additional features, or bespoke system layouts, a supplier who can tailor the equipment to your needs is invaluable.
4. Technical Support and Training
Brewing is as much about knowledge as it is about equipment. A good supplier should offer training on how to operate and maintain your system. Additionally, they should provide ongoing technical support to troubleshoot any issues that arise.
5. Pricing and Warranty
Finally, consider the price and warranty. While it’s tempting to go for the cheapest option, remember that quality is key. Look for a supplier that offers competitive pricing without compromising on quality. A strong warranty is also crucial, as it protects your investment in the long
term.
Suppliers and Price Range for 1 BBL Brewing Systems
Supplier Name | Price Range | Key Features | Reputation | Customization |
---|---|---|---|---|
ABC Brewing Systems | $10,000 – $15,000 | High-quality stainless steel, comprehensive setup. | Well-known for reliability. | Extensive customization options available. |
Brewers’ Choice | $12,000 – $18,000 | Includes all core components, strong warranty, technical support. | Excellent customer service. | Custom designs for different brewing styles. |
CraftMaster Pro | $9,000 – $14,000 | Affordable, durable, user-friendly control systems. | Good value for money. | Limited customization. |
ProBrew | $15,000 – $20,000 | Advanced technology, automation options, extensive training programs. | Premium brand, highly rated. | Highly customizable, with automated options. |
Microbrew Solutions | $11,000 – $16,000 | Compact design, energy-efficient, great for startups. | Strong in small-scale systems. | Moderate customization available. |
Installation, Operation, and Maintenance of a 1 BBL Brewing System
Once you’ve selected your equipment, the next steps involve installation, operation, and maintenance. Each of these stages is crucial to ensure that your brewing system runs efficiently and produces high-quality beer.
Installation
Installing a 1 BBL brewing system requires careful planning and execution. The system needs to be set up in a space that can accommodate the equipment and allow for smooth workflow. Professional installation is recommended to ensure that all components are connected correctly and safely, particularly when it comes to electrical systems, plumbing, and ventilation.
Operation
Operating a 1 BBL brewing system involves understanding each stage of the brewing process and how to manage the equipment. This includes controlling temperatures, managing fluid transfers, and monitoring fermentation. Proper training is essential to master the system’s controls and processes. Many suppliers offer training sessions to help new brewers get started.
Maintenance
Regular maintenance is key to ensuring the longevity and efficiency of your brewing system. This includes routine cleaning using the CIP system, checking and replacing seals and gaskets, inspecting pumps and heat exchangers, and recalibrating control systems. Preventive maintenance helps avoid costly downtime and ensures that your beer maintains consistent quality.
Installation, Operation, and Maintenance of a 1 BBL Brewing System
Aspect | Details | Best Practices |
---|---|---|
Installation | Involves setting up brewhouse, tanks, and utility connections. | Hire professionals for installation to ensure all systems are connected safely and efficiently. |
Operation | Day-to-day management of the brewing process, from mashing to packaging. | Receive proper training from your supplier or an experienced brewer. Use detailed logs to track brewing parameters. |
Maintenance | Regular upkeep including cleaning, part replacements, and system checks. | Implement a routine maintenance schedule. Use CIP systems regularly, and conduct inspections after every brewing cycle. |
Comparing Pros and Cons of a 1 BBL Brewing System
Investing in a 1 BBL brewing system is a significant decision, so it’s important to weigh the advantages and limitations. Here’s a detailed comparison to help you make an informed choice.
Advantages
- Scalability: The 1 BBL system is perfect for small breweries or brewpubs. Its manageable size allows you to produce enough beer to meet demand without overwhelming your resources. It’s also a great starting point with potential for expansion.
- Quality Control: Smaller batches mean you have more control over the brewing process, allowing for higher consistency and quality in your brews. This is particularly beneficial for craft brewers who want to maintain the unique character of their beers.
- Cost-Effective: Compared to larger systems, a 1 BBL system is more affordable both in terms of initial investment and operational costs. It uses less energy and fewer raw materials, making it a cost-effective option for startups.
- Versatility: This system allows for experimentation with different beer styles and recipes. You can easily adjust the brewing process or ingredients to create a wide variety of beers without committing to large quantities.
Limitations
- Limited Production Capacity: The primary drawback is the limited production capacity. While perfect for small-scale operations, a 1 BBL system may not meet the needs of a rapidly growing brewery or one with high demand.
- Labor-Intensive: Managing a small system often requires more hands-on involvement compared to automated larger systems. This can be time-consuming and labor-intensive, particularly if you’re brewing multiple batches a week.
- Space Constraints: While compact, a 1 BBL system still requires a dedicated space with proper utilities. For some, finding or modifying a suitable space can be challenging.
- Expansion Limitations: Scaling up from a 1 BBL system to a larger setup can require significant investment. If you plan to expand rapidly, starting with a larger system might be more economical in the long run.
Pros and Cons of a 1 BBL Brewing System
Advantages | Limitations |
---|---|
Scalability for small operations | Limited production capacity for larger demands |
High-quality control over small batches | Requires more hands-on management, leading to higher labor input |
Cost-effective, low initial investment | May require significant space or modifications |
Versatility for experimenting with recipes | Expansion from 1 BBL can be costly, might necessitate starting with a larger system for long-term growth |
Choosing the Best 1 BBL Brewing System Supplier
Selecting a supplier can be daunting with so many options available. To help you make the best choice, here’s a guide on what to consider:
1. Equipment Quality
Ensure the supplier uses high-grade materials, particularly stainless steel, which is standard for brewing equipment. The quality of the materials will affect the durability, hygiene, and performance of your brewing system.
2. Technical Support and After-Sales Service
Consider the level of support the supplier offers after purchase. This includes installation help, training, and ongoing technical support. A supplier who is committed to your success will offer robust after-sales service.
3. Customization and Flexibility
Choose a supplier who can customize the system according to your specific needs. Whether it’s modifying tank sizes, adding automation features, or designing a system layout that fits your space, flexibility is key.
4. Price vs. Value
While price is important, it shouldn’t be the only factor. Consider the overall value – what you get for your money. Sometimes paying a bit more for a reliable system with excellent support is worth the investment.
5. Reputation and Reviews
Do some research on the supplier’s reputation. Read reviews, ask for references, and check their track record with other brewers. A supplier with a strong reputation is more likely to provide quality products and services.
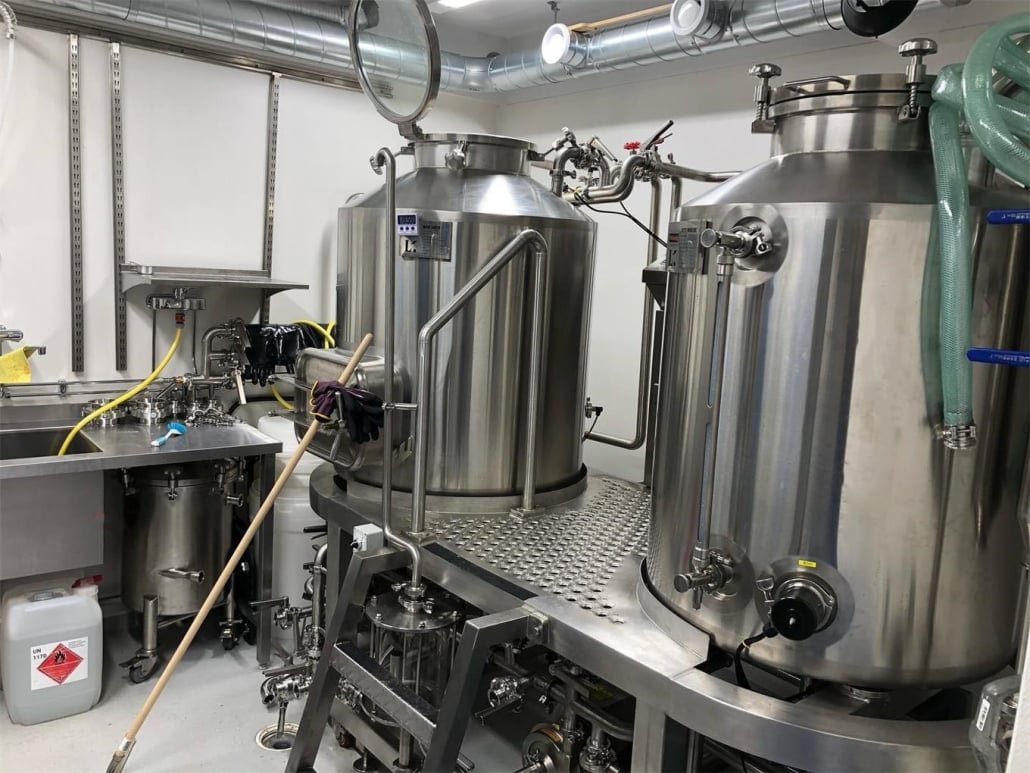
How to Choose a 1 BBL Brewing System Supplier
Consideration | Details | Key Questions to Ask |
---|---|---|
Equipment Quality | High-grade stainless steel, durable construction. | What materials are used? Are the tanks and fittings durable and easy to clean? |
Technical Support & After-Sales | Installation assistance, training, ongoing support. | What support is available after purchase? Is training included? |
Customization | Ability to modify equipment size, design, and features. | Can the system be tailored to my specific brewing needs? What are the customization options? |
Price vs. Value | Competitive pricing with good overall value. | Is the price reasonable for the quality and features offered? What’s included in the total cost? |
Reputation & Reviews | Positive feedback from other brewers, strong industry presence. | What do other brewers say about this supplier? Can they provide references or testimonials? |
FAQ
What does 1 BBL mean in brewing?
1 BBL stands for one barrel, which is equivalent to 31 gallons or about 117 liters. In brewing, it refers to the system’s capacity to brew that volume in a single batch.
Is a 1 BBL system suitable for homebrewing?
Yes, a 1 BBL system can be suitable for serious homebrewers or those looking to scale up from smaller homebrew setups. It’s particularly ideal for those who want to produce larger quantities or experiment with more complex brewing processes.
How much space is required for a 1 BBL brewing system?
A 1 BBL brewing system typically requires about 100-150 square feet, depending on the layout and any additional equipment like fermentation tanks or storage. Adequate space for workflow and utilities is crucial.
Can a 1 BBL system be upgraded?
Yes, many 1 BBL systems can be customized and expanded. You can add more fermentation tanks, upgrade control systems, or integrate automated processes as your brewing operation grows.
Share this entry
Interested in learning more about Brewing Systems including additional details and pricing information? Please use the form below to contact us!
YOLONG BREWERY EQUIPMENT FAQS
- Commercial Brewery / Craft Brewery / Microbrewery / Nanobrewery
- What is The Difference Between Craft Beer and Industrial Beer?
- The Bespoke Differences In Custom Brewing Systems
- Everything You Need to Know About Kettle Souring
- How to Choose Brewing Equipment for Your business?
- How To Choose The-Best Partner To Build Your Commercial Microbrewing System?
- Two Detection Sensors That You Need To Use In Your Brewhouse System
- Remote Control Applications in Brewing Equipment/How does it work?
- How To Clean Your Brand New Brewery Tanks?