Stainless Steel Brewing Tanks
Stainless steel brewing tanks are an essential component of any modern brewery, whether it’s a large-scale commercial operation or a small microbrewery. These tanks are designed to hold and ferment the wort (the liquid extracted from the mashing process) during the brewing process. Stainless steel is the material of choice for brewing tanks due to its superior durability, corrosion resistance, and ease of cleaning.
Imagine you’re a craft brewer, pouring your heart and soul into creating the perfect batch of beer. The quality of your brew depends heavily on the equipment you use, and that’s where stainless steel brewing tanks come into play. These sleek, shiny tanks are the workhorses of any brewery, ensuring that your beer is fermented and conditioned to perfection.
Brewing Equipment Guide: Stainless Steel Tanks
Before we dive into the nitty-gritty details of stainless steel brewing tanks, let’s take a step back and understand the overall brewing process. The journey of beer starts with the mashing process, where malted grains are mixed with hot water to extract the sugary liquid known as wort. This wort is then transferred to a brew kettle, where it is boiled and hops are added for flavor and aroma.
Once the boiling process is complete, the wort is rapidly cooled and transferred to a fermentation vessel – and that’s where our stainless steel brewing tanks come into play. These tanks provide an ideal environment for the yeast to convert the sugars in the wort into alcohol and carbon dioxide, effectively turning the wort into beer.
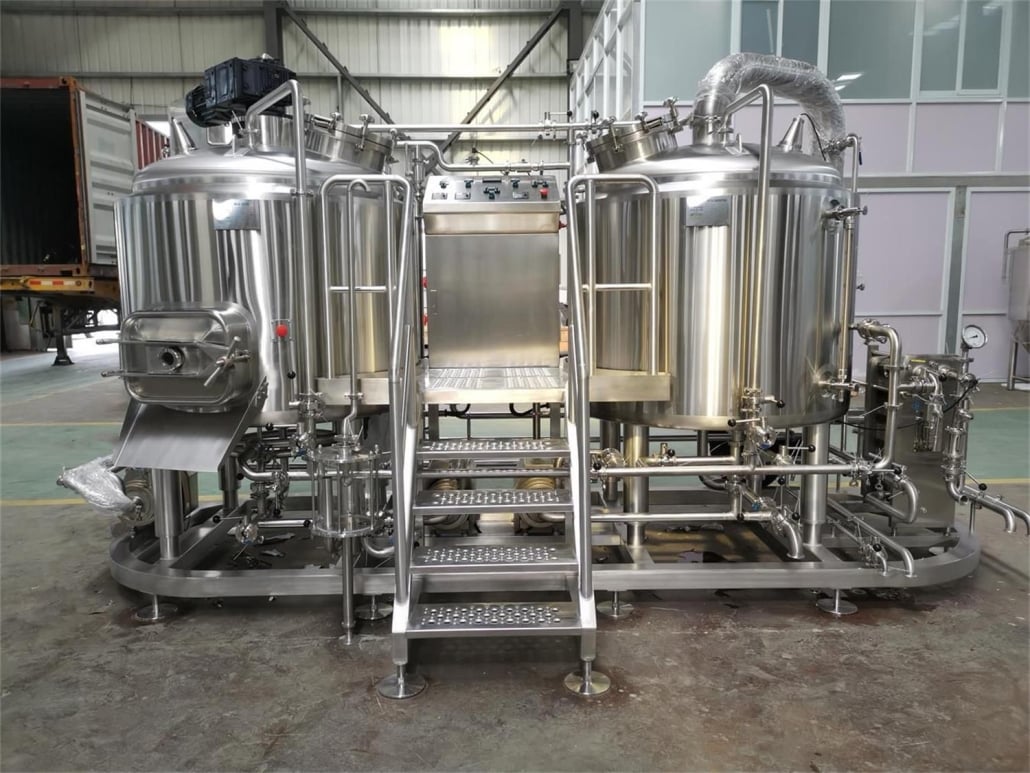
Types of Stainless Steel Brewing Tanks
Tank Type | Description |
---|---|
Unitank/Uni-tank | A single vessel used for both fermentation and conditioning/aging. Eliminates the need for separate tanks. |
Conical Fermenters | Cylindrical tanks with a conical bottom, designed for efficient yeast collection and removal. |
Cylindrical Fermenters | Straight-sided cylindrical tanks, often used for primary fermentation. |
Bright Beer Tanks | Used for conditioning and carbonating the beer after fermentation. |
Brite Tanks | Insulated tanks for storing and serving the finished beer. |
The Brewing Process with Stainless Steel Tanks
The journey from humble grains to a satisfying sip of beer is a complex dance of ingredients, temperatures, and meticulous care. While the recipe and brewing style play a starring role, the supporting act – the vessels themselves – plays a crucial role in shaping the final masterpiece. In the modern brewery, stainless steel tanks have become the go-to conductor, orchestrating the brewing process with efficiency, hygiene, and unwavering quality.
Unlike their wooden or ceramic predecessors, stainless steel tanks offer a symphony of advantages. Their smooth, non-porous surfaces resist the growth of bacteria and other contaminants, ensuring the purity of the brew. Unlike wood, which can impart unwanted flavors, stainless steel remains neutral, allowing the brewer’s creativity to shine through. Additionally, their durability withstands the rigors of the brewing process, from the high temperatures of mashing to the vigorous fermentation dance.
The different stages of brewing find their perfect partners in a variety of stainless steel tanks. The journey begins in the mash tun, where crushed grains mingle with hot water, releasing their sugars. These tanks feature specialized rakes or lautering plates to efficiently separate the sweet wort from the spent grains. The wort then travels to the kettle, where it boils with hops, infusing the distinctive bitterness and aroma. Modern kettles often boast whirlpool features, creating a gentle vortex that clarifies the wort and optimizes hop utilization.
The heart of the brewing process lies in the fermentation tanks. Here, the magic of yeast transforms the sugary wort into beer, generating alcohol, carbon dioxide, and the beer’s characteristic flavors and aromas. These tanks come in various shapes and sizes, each playing a specific role. Cylindroconical tanks (CCTs), with their distinctive cone-shaped bottoms, facilitate easy yeast separation and sediment removal. Brite tanks, on the other hand, serve as the final polishing act, where the beer clarifies, carbonates, and matures to perfection.
Beyond their functional prowess, stainless steel tanks offer brewers the flexibility to experiment and innovate. Precise temperature control systems allow for manipulation of fermentation profiles, creating beers with diverse flavor profiles. Some breweries even utilize pressure-rated tanks for unique styles like lagers or sour beers.
Tank Capacity, Spaces, Design, and Layout
Capacity Range | Floor Space Required | Design Features |
---|---|---|
1 – 10 BBL (31 – 310 gallons) | 100 – 300 sq ft | Compact footprint, jacketed tanks for temperature control, easy access for cleaning. |
10 – 30 BBL (310 – 930 gallons) | 300 – 800 sq ft | Larger tanks, often with elevated platforms or catwalks for access, dedicated fermentation and conditioning areas. |
30+ BBL (930+ gallons) | 800+ sq ft | Large-scale production facilities, automated systems, dedicated tank farms, and more complex piping and process control. |
Customization and Personalization
In today’s world, mass production and one-size-fits-all solutions are increasingly giving way to individualized approaches. We crave experiences curated to our preferences, products engineered for our specific needs, and information filtered through our unique lens. This shift towards customized and personalized offerings has become a defining characteristic of modern life, reshaping industries and captivating consumers.
Customization empowers us to take the reins. Imagine designing your dream car, choosing every detail from the exterior paint to the engine specifications. Or picture crafting a personalized fitness plan tailored to your goals and fitness level. Customization grants us agency, allowing us to express ourselves and create solutions that perfectly match our desires.
Personalization, on the other hand, takes a more passive approach. Algorithms and data analysis work behind the scenes to anticipate our needs and deliver experiences seamlessly. Think about music streaming services suggesting songs you’ll love based on your listening history, or news platforms filtering articles specific to your interests. Personalization leverages technology to anticipate and fulfill our potential desires, often before we even voice them.
The distinction between customization and personalization might seem subtle, but their nuances have significant implications. Customization thrives on user control, offering a sense of ownership and empowerment. Personalization prioritizes convenience and relevance, delivering tailor-made experiences without requiring explicit user effort. Both approaches, however, share a common goal: deepening engagement and fostering loyalty by catering to individual preferences and needs.
The success of these strategies hinges on striking the right balance. Excessive customization can lead to decision fatigue, overwhelming users with endless options. Overaggressive personalization, on the other hand, can raise privacy concerns and create an unsettling feeling of being surveilled. Finding the sweet spot requires careful consideration of user preferences, ethical data practices, and a clear understanding of the desired outcome.
Looking ahead, the future of customization and personalization lies in a dynamic interplay between user agency and intelligent anticipation. Imagine AI-powered tools that recommend options within customizable frameworks, empowering users to make informed choices while benefiting from intelligent suggestions. We may also see advancements in privacy-preserving personalization, ensuring tailored experiences without compromising user data security.
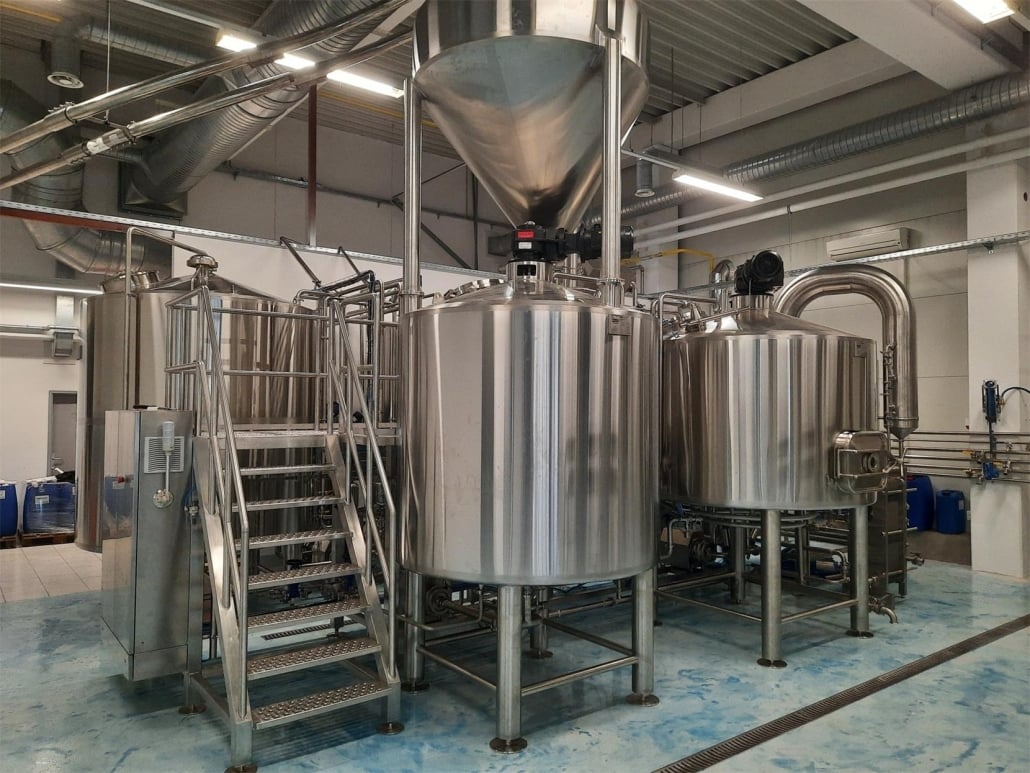
Sourcing and Pricing for Stainless Steel Brewing Tanks
Supplier | Price Range (New) | Used Options |
---|---|---|
Ss Brewtech | $2,000 – $20,000 | Yes |
Perl Fermenters | $3,000 – $50,000 | Yes |
Psycho Brew | $1,500 – $15,000 | Limited |
Brewhaus | $5,000 – $100,000 | Yes |
Blichmann Engineering | $1,000 – $10,000 | Limited |
Installation, Operation, and Maintenance
Installation | Operation | Maintenance |
---|---|---|
Proper site preparation, leveling, and utility connections | Temperature control, yeast pitching, fermentation monitoring | Regular cleaning, passivation, gasket replacements |
Rigging and placement of tanks | Transferring beer, carbonation, conditioning | Inspections for leaks or damage |
Piping and process control setup | Sanitation and sterilization procedures | Preventative maintenance schedules |
Choosing the Right Stainless Steel Brewing Tank Supplier
When it comes to selecting the perfect stainless steel brewing tank for your brewery, there are several factors to consider. Here’s a handy table to help you navigate the decision-making process:
Factor | Considerations |
---|---|
Quality | Look for reputable manufacturers with a track record of producing high-quality tanks. Check for certifications and quality control processes. |
Customization | Evaluate your specific brewing needs and determine if custom tank sizes, fittings, or designs are required. |
Lead Time | Consider the lead time for manufacturing and delivery, especially for custom orders or during peak seasons. |
Service and Support | Assess the level of technical support, installation assistance, and after-sales service provided by the supplier. |
Pricing | Compare pricing from multiple suppliers, factoring in the tank quality, customization options, and shipping costs. |
Warranties | Review the manufacturer’s warranty coverage and terms, ensuring your investment is protected. |
Pros and Cons of Stainless Steel Brewing Tanks
Like any brewing equipment, stainless steel tanks come with their own set of advantages and limitations. Let’s take a look at some of the key pros and cons:
Pros | Cons |
---|---|
Durability and longevity | Higher initial investment cost |
Corrosion resistance | Potential for scratches or dents |
Easy to clean and sanitize | Skilled labor required for installation and maintenance |
Versatility in tank sizes and designs | Potential for off-flavors if not properly passivated |
Maintains consistent temperatures | Bulky and heavy, requiring proper floor support |
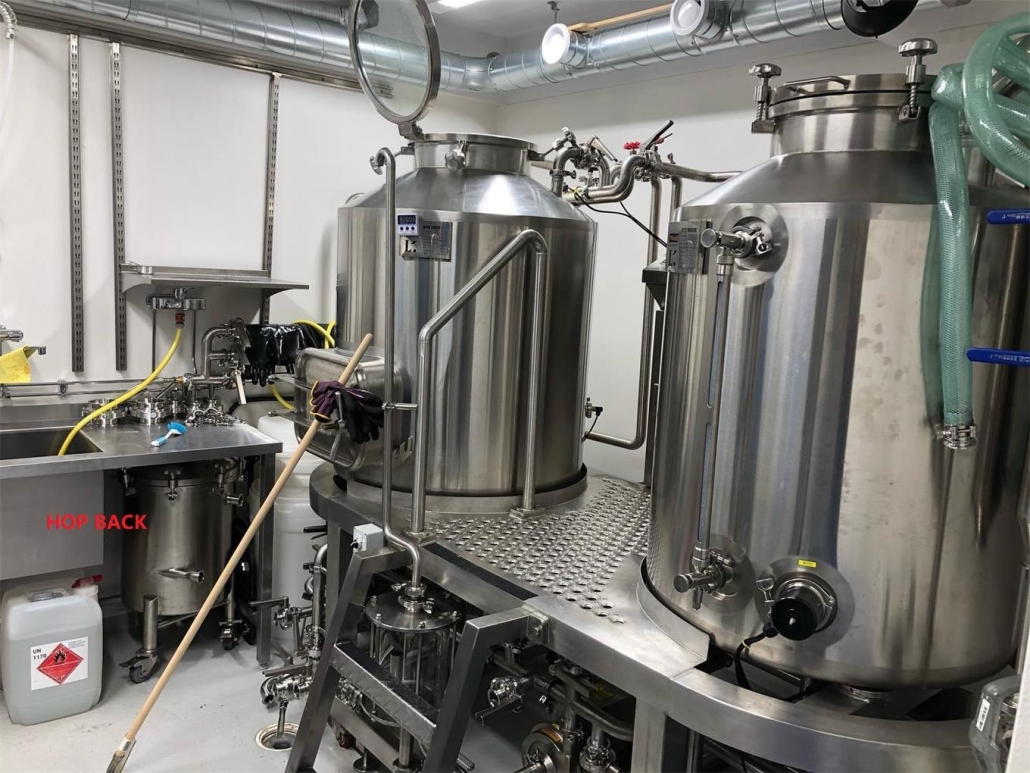
Advantages and Limitations
Stainless steel brewing tanks offer several advantages over other materials, such as their resistance to corrosion, ease of cleaning, and durability. However, they also come with limitations, such as a higher initial investment cost and the potential for scratches or dents if not handled properly.
One of the key advantages of stainless steel tanks is their ability to maintain consistent temperatures during the fermentation process. This is crucial for producing high-quality, consistent beer batches. Additionally, their versatility in terms of tank sizes and designs allows breweries to tailor their equipment to their specific needs.
On the other hand, stainless steel tanks can be heavy and bulky, requiring proper floor support and skilled labor for installation and maintenance. Off-flavors can also occur if the tanks are not properly passivated, a process that creates a protective oxide layer on the stainless steel surface.
FAQ
Q: What is the difference between a unitank and a conical fermenter? A: A unitank is a single vessel used for both fermentation and conditioning/aging, while a conical fermenter is specifically designed for efficient yeast collection and removal during fermentation, with a conical bottom shape.
Q: How often do stainless steel brewing tanks need to be cleaned? A: Tanks should be cleaned after every use to prevent contamination and maintain proper sanitation. The frequency can vary depending on the brewery’s production schedule and cleaning protocols.
Q: Can stainless steel tanks be insulated for temperature control? A: Yes, many manufacturers offer insulation jackets or glycol cooling systems for temperature control during fermentation and conditioning.
Q: How long do stainless steel brewing tanks typically last? A: With proper care and maintenance, high-quality stainless steel tanks can last for decades, making them a worthwhile investment for breweries.
Q: Can stainless steel tanks be customized with specific fittings or designs? A: Yes, many manufacturers offer customization options for fittings, tank sizes, finishes, and even personalized branding or logos etched onto the tanks.
Q: What is the process for passivating stainless steel tanks? A: Passivation involves treating the stainless steel surface with an acid solution to remove any contaminants and create a protective oxide layer, preventing off-flavors and maintaining the tank’s sanitary condition.
Share this entry
Interested in learning more about Brewing Systems including additional details and pricing information? Please use the form below to contact us!
YOLONG BREWERY EQUIPMENT FAQS
- Commercial Brewery / Craft Brewery / Microbrewery / Nanobrewery
- What is The Difference Between Craft Beer and Industrial Beer?
- The Bespoke Differences In Custom Brewing Systems
- Everything You Need to Know About Kettle Souring
- How to Choose Brewing Equipment for Your business?
- How To Choose The-Best Partner To Build Your Commercial Microbrewing System?
- Two Detection Sensors That You Need To Use In Your Brewhouse System
- Remote Control Applications in Brewing Equipment/How does it work?
- How To Clean Your Brand New Brewery Tanks?