Microbrewery Machines
In the world of craft beer, the rise of microbreweries has been a game-changer. These small-scale brewing operations have revolutionized the industry, offering beer enthusiasts a wide range of unique and flavorful brews. At the heart of every successful microbrewery lies a sophisticated piece of equipment known as the microbrewery machine.
This specialized brewing system is designed to cater to the needs of small-batch production, allowing brewers to experiment with different ingredients and techniques while maintaining exceptional quality control. Whether you’re a seasoned brewer or an aspiring entrepreneur looking to venture into the exciting world of craft beer, understanding the intricacies of microbrewery machines is essential.
Microbrewery Machine Overview
A microbrewery machine is a compact and versatile brewing system that combines various components to facilitate the entire beer-making process. From mashing and lautering to boiling, cooling, and fermentation, these all-in-one units streamline the brewing experience. Typically, microbrewery machines are designed to produce batches ranging from a few gallons to several barrels, catering to the needs of small-scale operations.
Unlike traditional large-scale brewery setups, microbrewery machines offer a high degree of flexibility and control, allowing brewers to fine-tune every aspect of the brewing process. This level of precision is crucial in crafting unique and distinctive beer styles that set microbreweries apart from their larger counterparts.
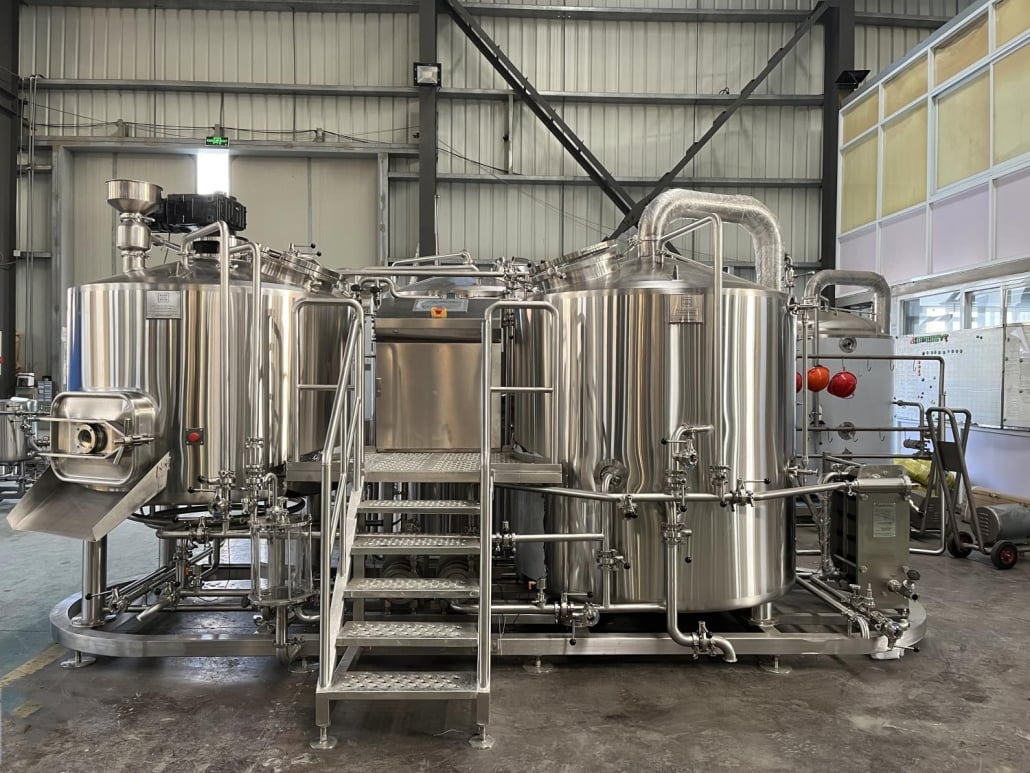
Types of Microbrewery Machines
Machine Type | Description |
---|---|
All-Grain Systems | These systems are designed for brewers who want complete control over the mashing process, using whole grains as the primary fermentable source. All-grain systems typically include a mash tun, lauter tun, and a brew kettle. |
Brew-in-a-Bag (BIAB) Systems | BIAB systems simplify the all-grain brewing process by combining the mashing and lautering steps into a single vessel, typically a large brew kettle. This setup is ideal for small-scale operations with limited space. |
Extract Brewing Systems | For those new to brewing or seeking a more straightforward approach, extract brewing systems use pre-processed malt extract as the fermentable source, eliminating the need for a dedicated mash tun. These systems are often more compact and easier to operate. |
The Microbrewery Brewing Process
The brewing process is a complex and fascinating journey that transforms simple ingredients into a delectable craft beer. While the specific steps may vary slightly depending on the brewery’s equipment and preferences, the general process follows a well-established sequence.
- Milling: The first step involves crushing the malted grains to expose their starches and enzymes for the mashing process.
- Mashing: During mashing, the crushed grains are mixed with hot water in a mash tun, allowing the enzymes to convert the starches into fermentable sugars.
- Lautering: After mashing, the liquid wort is separated from the spent grains in a process called lautering, which can be achieved through a lauter tun or a brew-in-a-bag setup.
- Boiling: The collected wort is then transferred to a brew kettle for boiling, where hops are added to impart bitterness, aroma, and flavor. This step also sterilizes the wort.
- Cooling: After boiling, the wort must be rapidly cooled to prepare it for fermentation. This is typically done using a wort chiller or heat exchanger.
- Fermentation: Once cooled, the wort is transferred to a fermentation vessel, where yeast is added to convert the fermentable sugars into alcohol and carbon dioxide, producing the desired beer.
- Conditioning and Packaging: Finally, the beer is conditioned, carbonated, and packaged for consumption or distribution.
Microbrewery Machine Capacity and Spaces
Capacity Range | Typical Batch Size | Required Space |
---|---|---|
Small-Scale | 5 – 10 gallons | Compact home brewery or small commercial space |
Medium-Scale | 10 – 30 gallons | Dedicated brewery room or small industrial unit |
Large-Scale | 30 – 100+ gallons | Large industrial facility or microbrewery |
Design and Layout Considerations
When it comes to microbrewery machines, design and layout play a crucial role in maximizing efficiency and ensuring a smooth brewing process. Here are some key considerations:
- Ergonomics: The machine’s components should be arranged in a logical and user-friendly manner, minimizing unnecessary movement and strain during operation.
- Workflow: The layout should facilitate a seamless workflow, with each step of the brewing process flowing naturally into the next.
- Accessibility: Easy access to essential components, such as the mash tun, brew kettle, and fermentation vessels, is crucial for maintenance and cleaning.
- Automation: Many modern microbrewery machines offer varying degrees of automation, from semi-automatic to fully automated systems, reducing manual labor and ensuring consistent results.
Customization and Scalability
One of the significant advantages of microbrewery machines is their ability to be customized and scaled according to the brewer’s specific needs and growth plans. Reputable manufacturers offer a range of modular systems that can be easily expanded or modified as production demands increase.
For instance, a brewer may start with a compact all-grain system and gradually upgrade to larger vessels, add automation features, or incorporate specialized components such as a dedicated yeast propagation system or a centrifuge for clarification.
Microbrewery Machine Suppliers and Price Range
When it comes to sourcing a microbrewery machine, brewers have a variety of options, ranging from turnkey solutions from established manufacturers to custom-built systems from specialized fabricators. Here’s an overview of some notable suppliers and their typical price ranges:
Supplier | Price Range (USD) | Description |
---|---|---|
Ss Brewtech | $5,000 – $50,000+ | Offers a wide range of brewing systems, from small-scale homebrewing setups to commercial-grade equipment. Known for their high-quality stainless steel components and modular designs. |
Brewmation | $10,000 – $100,000+ | Specializes in automated and semi-automated brewing systems, with a focus on user-friendly controls and advanced features like remote monitoring and data logging. |
JVNW | $3,000 – $30,000+ | A popular choice for homebrewers and small commercial operations, offering affordable and customizable brewing systems with a range of accessories and add-ons. |
Psycho Brew | $10,000 – $80,000+ | Known for their innovative designs and high-end brewing equipment, catering to both commercial and hobbyist brewers. |
Portland Kettle Works | $5,000 – $60,000+ | A trusted name in the industry, offering high-quality brewing systems made from premium materials, with a focus on durability and precision. |
It’s important to note that the final cost of a microbrewery machine can vary significantly based on factors such as system capacity, level of automation, customization options, and additional components or accessories.
Installation, Operation, and Maintenance
Aspect | Considerations |
---|---|
Installation | – Proper site preparation, including adequate space and utilities (water, electricity, drainage) <br> – Professional installation and commissioning by qualified technicians <br> – Adherence to local building codes and regulations |
Operation | – Comprehensive training for brewers on system operation and safety protocols <br> – Detailed standard operating procedures (SOPs) for consistent brewing practices <br> – Proper record-keeping and batch tracking for quality control |
Maintenance | – Regular cleaning and sanitization of all components <br> – Preventive maintenance schedules for equipment inspection and servicing <br> – Availability of spare parts and technical support from the supplier |
Proper installation, operation, and maintenance are crucial for ensuring the longevity and optimal performance of a microbrewery machine. Many suppliers offer comprehensive support services, including on-site installation, training, and maintenance contracts, to ensure a seamless experience for their customers.
Choosing the Right Microbrewery Machine Supplier
With numerous suppliers in the market, selecting the right partner for your microbrewery machine can be a daunting task. Here are some key factors to consider:
Factor | Description |
---|---|
Reputation and Experience | Look for well-established suppliers with a proven track record in the brewing industry. Read customer reviews, seek recommendations, and research their experience in designing and manufacturing microbrewery machines. |
Product Quality and Innovation | Evaluate the supplier’s commitment to using high-quality materials, implementing advanced manufacturing techniques, and staying up-to-date with the latest brewing technologies and innovations. |
Customization and Scalability | Assess the supplier’s ability to offer customized solutions that can adapt to your specific requirements and growth plans, allowing for future expansion or modifications. |
Customer Support and Service | Consider the supplier’s level of customer support, including installation assistance, training programs, maintenance services, and access to spare parts and technical expertise. |
Pricing and Value | While cost should not be the sole determining factor, it’s essential to compare pricing across different suppliers and evaluate the overall value proposition, taking into account the quality, features, and long-term support offered. |
By carefully evaluating these factors, you can increase the likelihood of finding a reliable and trustworthy supplier who can provide a microbrewery machine that meets your brewing needs and contributes to the success of your operation.
Pros and Cons of Microbrewery Machines
Like any brewing equipment, microbrewery machines come with their own set of advantages and limitations. Here’s a breakdown of the pros and cons to help you make an informed decision:
Pros | Cons |
---|---|
Small Batch Flexibility: Microbrewery machines allow for small-batch production, enabling brewers to experiment with various recipes and styles without committing to large volumes. | Capacity Limitations: While suitable for small-scale operations, microbrewery machines may have limited capacity, making it challenging to meet high-volume demand without investing in additional equipment. |
Cost-Effective: Compared to large-scale brewing systems, microbrewery machines often have a lower upfront cost, making them an attractive option for startups and hobbyists. | Space Requirements: Although compact, microbrewery machines still require dedicated space and proper layout planning, which may be a challenge in smaller facilities. |
Control and Precision: Many microbrewery machines offer advanced features and control systems, allowing brewers to precisely monitor and adjust various parameters for consistent quality. | Maintenance and Cleaning: Thorough cleaning and maintenance are essential for microbrewery machines, which can be time-consuming and labor-intensive, especially for smaller operations. |
Scalability: Modular designs and the ability to upgrade components make it possible to scale up microbrewery machines as production demands increase. | Limited Automation: While some microbrewery machines offer automation features, smaller systems may require more manual intervention, increasing the workload for brewers. |
Hands-On Experience: Microbrewery machines provide a hands-on brewing experience, allowing brewers to develop a deep understanding of the entire process. | Supplier Dependence: Reliance on a single supplier for parts, service, and support can be a potential risk if the supplier experiences issues or discontinues operations. |
By weighing these pros and cons against your specific brewing goals, budget, and operational requirements, you can determine whether a microbrewery machine is the right choice for your brewing endeavor.
Advantages of Microbrewery Machines
- Small-Batch Flexibility: One of the primary advantages of microbrewery machines is their ability to produce small batches of beer. This flexibility allows brewers to experiment with different recipes, ingredients, and techniques without committing to large volumes, reducing waste and minimizing financial risk.
- Cost-Effectiveness: Compared to large-scale brewing systems, microbrewery machines often have a lower upfront cost, making them an attractive option for startups, homebrewers, and small commercial operations with limited budgets.
- Control and Precision: Many modern microbrewery machines are equipped with advanced features and control systems, enabling brewers to precisely monitor and adjust various parameters throughout the brewing process. This level of control ensures consistent quality and allows for fine-tuning of recipes.
- Scalability: Most microbrewery machines are designed with scalability in mind, offering modular components that can be easily upgraded or expanded as production demands increase. This scalability allows businesses to grow without the need for a complete system overhaul.
- Hands-On Experience: Microbrewery machines provide a hands-on brewing experience, allowing brewers to develop a deep understanding of the entire process from start to finish. This knowledge can be invaluable in refining recipes and troubleshooting issues.
- Compact Footprint: Despite their advanced capabilities, microbrewery machines have a relatively compact footprint, making them suitable for small brewery spaces, garages, or even residential settings for homebrewing enthusiasts.
Limitations of Microbrewery Machines
- Capacity Limitations: While microbrewery machines are ideal for small-batch production, they may have limited capacity, making it challenging to meet high-volume demand without investing in additional equipment or expanding the system.
- Space Requirements: Although designed to be compact, microbrewery machines still require dedicated space and proper layout planning. Ensuring adequate space for efficient workflow and maintenance can be a challenge in smaller facilities.
- Maintenance and Cleaning: Thorough cleaning and maintenance are crucial for microbrewery machines to ensure consistent quality and prevent contamination. This process can be time-consuming and labor-intensive, especially for smaller operations with limited staff.
- Limited Automation: While some microbrewery machines offer automation features, smaller systems may require more manual intervention, increasing the workload for brewers and potentially introducing human error.
- Supplier Dependence: When investing in a microbrewery machine, brewers often become reliant on a single supplier for parts, service, and support. This dependence can be a potential risk if the supplier experiences issues or discontinues operations.
- Upgrade Costs: As production demands increase, upgrading a microbrewery machine or expanding the system can involve significant costs, potentially offsetting the initial cost-effectiveness advantage.
It’s important to carefully evaluate these limitations and consider your long-term brewing goals and growth plans to determine if a microbrewery machine is the right fit for your operation.
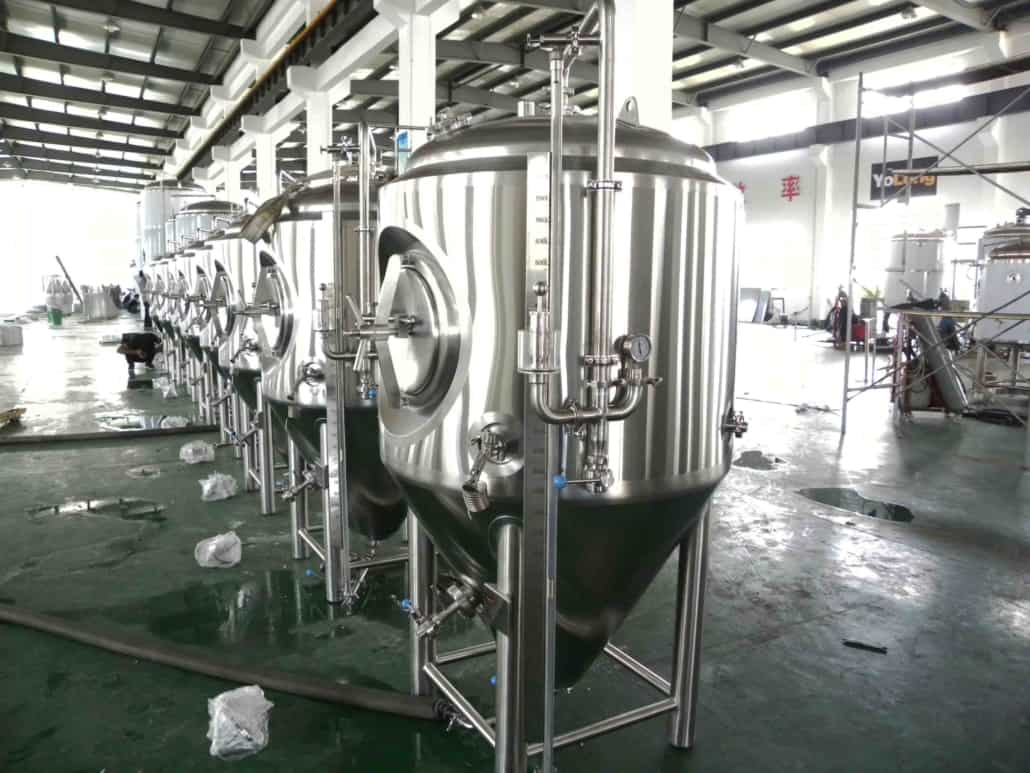
FAQ
Question | Answer |
---|---|
What is the typical batch size for a microbrewery machine? | Microbrewery machines are designed to produce small batches, typically ranging from 5 to 30 gallons or more, depending on the specific system and brewery’s needs. |
Can microbrewery machines be scaled up for larger production? | Yes, many microbrewery machines are designed with scalability in mind, allowing brewers to upgrade or expand the system as their production demands increase. This can involve adding larger vessels, additional fermentation tanks, or incorporating automated features. |
How much space is required for a microbrewery machine? | The space requirements vary depending on the system’s size and configuration, but most microbrewery machines are designed to be compact. A dedicated brewery room or small industrial unit is typically sufficient for medium-scale operations. |
What are the common materials used in microbrewery machines? | High-quality stainless steel is the most commonly used material for microbrewery machines due to its durability, resistance to corrosion, and ease of cleaning. Other materials like copper or aluminum may be used for specific components. |
How easy is it to customize a microbrewery machine? | Many reputable suppliers offer customization options, allowing brewers to tailor the system to their specific needs. This can include adding specialized components, adjusting vessel sizes, or incorporating automation features. |
How often do microbrewery machines require maintenance? | Regular maintenance is crucial for microbrewery machines. Thorough cleaning and sanitization should be performed after each brew, while preventive maintenance schedules for equipment inspection and servicing may vary depending on usage and the manufacturer’s recommendations. |
Can microbrewery machines be used for commercial production? | Absolutely. While some microbrewery machines are designed for homebrewing, many suppliers offer commercial-grade systems suitable for small to medium-scale commercial operations, such as microbreweries, brewpubs, and taprooms. |
What kind of training is typically provided with a microbrewery machine? | Reputable suppliers often provide comprehensive training on system operation, safety protocols, and brewing best practices. This may include on-site training sessions, detailed manuals, and ongoing support from technical experts. |
Share this entry
Interested in learning more about Brewing Systems including additional details and pricing information? Please use the form below to contact us!
YOLONG BREWERY EQUIPMENT FAQS
- Commercial Brewery / Craft Brewery / Microbrewery / Nanobrewery
- What is The Difference Between Craft Beer and Industrial Beer?
- The Bespoke Differences In Custom Brewing Systems
- Everything You Need to Know About Kettle Souring
- How to Choose Brewing Equipment for Your business?
- How To Choose The-Best Partner To Build Your Commercial Microbrewing System?
- Two Detection Sensors That You Need To Use In Your Brewhouse System
- Remote Control Applications in Brewing Equipment/How does it work?
- How To Clean Your Brand New Brewery Tanks?