Micro Brewing Equipment
Overview: Why Micro Brewing Equipment Matters
Microbrewing equipment is the backbone of any brewery setup, playing a critical role in both the brewing process and final product quality. The right equipment will affect efficiency, flavor consistency, and even help you scale your business as demand grows. But what exactly should you look for in micro brewing equipment?
In this guide, we’ll walk through the main types of brewing equipment, discuss factors like capacity, design, and customization, and give you a roadmap to setting up a brewing operation that fits your vision and budget.
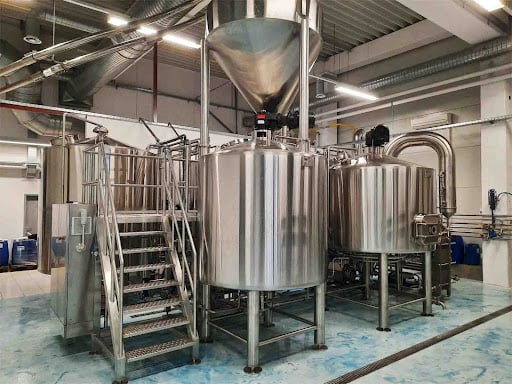
Essential Micro Brewing Equipment Guide
To make high-quality beer, it’s essential to understand the various types of brewing equipment available. Let’s explore each component, what it does, and how it fits into the overall brewing process.
Brewing Equipment Types and Functions
Equipment Type | Description |
---|---|
Mash Tun | A vessel for mashing grains with water to produce wort. The mash tun is essential for converting starches to sugars. |
Lauter Tun | Separates wort from the grain after mashing. Lauter tuns have slotted plates to allow wort flow while holding back the grain. |
Boiling Kettle | Heats wort to a rolling boil, which sterilizes the liquid and extracts bitter compounds from hops. |
Fermentation Tanks | Vessels where wort is inoculated with yeast to ferment and produce alcohol. Options range from stainless steel tanks to conical fermenters. |
Bright Tank | Used for carbonating and conditioning beer before packaging, ensuring a consistent taste and clarity. |
Heat Exchanger | Rapidly cools down wort after boiling to the right temperature for yeast addition, preventing unwanted bacterial growth. |
Kegging & Bottling Equipment | Includes kegs, bottles, filling lines, and capping machines essential for packaging beer after brewing. |
Cleaning and Sanitizing Equipment | Specialized pumps and chemical systems for cleaning tanks, pipes, and surfaces to maintain hygiene and prevent contamination. |
Each piece of equipment contributes to a specific stage of brewing, from the initial mashing of grains to the final packaging of the product.
Micro Brewing Process Explained
Microbrewing is an intricate process that combines science, technique, and artistry. Here’s a closer look at the main stages:
1. Mashing
Mashing involves steeping crushed grains in hot water, activating enzymes that convert starches to fermentable sugars. The choice of grain, water temperature, and time all influence the wort’s flavor profile.
2. Lautering
The wort is separated from the grain bed in the lauter tun. Lautering involves sparging (rinsing) the grain with additional water to extract as much sugar as possible, optimizing yield.
3. Boiling
Boiling sterilizes the wort and extracts bitter flavors from hops. The length of the boil and choice of hops influence bitterness, flavor, and aroma in the final beer.
4. Cooling and Fermentation
After boiling, the wort is cooled quickly in a heat exchanger to a temperature suitable for yeast. Yeast is then added in fermentation tanks, transforming sugars into alcohol and CO₂.
5. Conditioning and Carbonation
After fermentation, beer undergoes conditioning, often in a bright tank. Here, carbonation is added, and the beer matures, gaining clarity and balance.
6. Packaging
Finally, the beer is packaged in bottles, cans, or kegs for distribution.
Each of these steps is crucial, as even a slight variation can lead to vastly different outcomes in taste, aroma, and texture.
Choosing Micro Brewing Equipment by Capacity and Layout
Selecting the right brewing equipment goes beyond just knowing the types—you also need to consider capacity, design, layout, and customization based on your brewing goals.
Feature | Description |
---|---|
Capacity | Typical microbrewing systems range from small 5-barrel systems for small-scale operations to 30+ barrels for larger microbreweries. |
Design & Layout | Consider vertical space for stacked tanks or a spread-out horizontal layout for easier access. |
Customization | Many suppliers offer customization, such as modular tanks or advanced automation, to tailor systems to specific recipes or batch sizes. |
Customization is especially valuable if you plan to create unique, experimental brews or frequently adjust recipes.
Comparing Micro Brewing Equipment Suppliers and Price Ranges
The market is filled with equipment suppliers, each with its pros, cons, and pricing structure. Below are some popular options, along with their general price ranges for a typical microbrewery setup.
Supplier | Price Range | Strengths | Considerations |
---|---|---|---|
ABC Brewing Co. | $50,000 – $300,000 | High-quality materials, good durability | Higher initial cost |
BrewTech Solutions | $40,000 – $250,000 | Customizable setups, reliable support | Mid-range cost, moderate installation complexity |
EcoBrew Systems | $30,000 – $200,000 | Environmentally friendly options | Limited capacity options for large-scale breweries |
Selecting a supplier depends on factors like budget, required batch sizes, and available features. Consider speaking with multiple vendors to assess support and flexibility for future upgrades.
Installation, Operation, and Maintenance of Micro Brewing Equipment
Operating brewing equipment requires both expertise and ongoing maintenance to ensure efficiency and longevity.
Aspect | Details |
---|---|
Installation | Typically performed by professional technicians provided by the supplier. Installation costs may vary based on equipment complexity. |
Operation | Operators should be trained in using controls and safety protocols, especially for pressurized tanks and heat exchangers. |
Maintenance | Routine cleaning, checking seals and valves, and calibrating sensors help maintain product quality and extend equipment life. |
Preventative maintenance is crucial to avoid contamination risks and costly downtime.
How to Choose the Best Micro Brewing Equipment Supplier
Choosing the right supplier goes beyond price; you need to consider factors like quality, support, and long-term relationship potential.
Criterion | Explanation |
---|---|
Reputation | Look for suppliers with a track record of reliability and positive reviews from other breweries. |
Support | Consider the level of customer support, including installation, training, and troubleshooting assistance. |
Warranty | Ensure the supplier offers a robust warranty covering repairs, replacements, and routine maintenance for a set period. |
Customization Options | Some suppliers offer flexibility to modify equipment to meet specific brewing requirements. |
Talking to other brewers about their experiences can also provide valuable insights.
Advantages and Disadvantages of Micro Brewing Equipment
Every brewing system comes with its pros and cons, which depend largely on the type of brewing, scale, and budget.
Advantages | Disadvantages |
---|---|
High control over brewing parameters | Higher upfront and maintenance costs |
Scalability allows for business growth | Requires significant space and utility requirements |
Quality consistency across batches | Complex setup and longer installation periods |
Customization to create unique brews | Technical expertise needed for operation and repair |
For small-scale operations, high-quality but smaller equipment can balance budget and functionality.
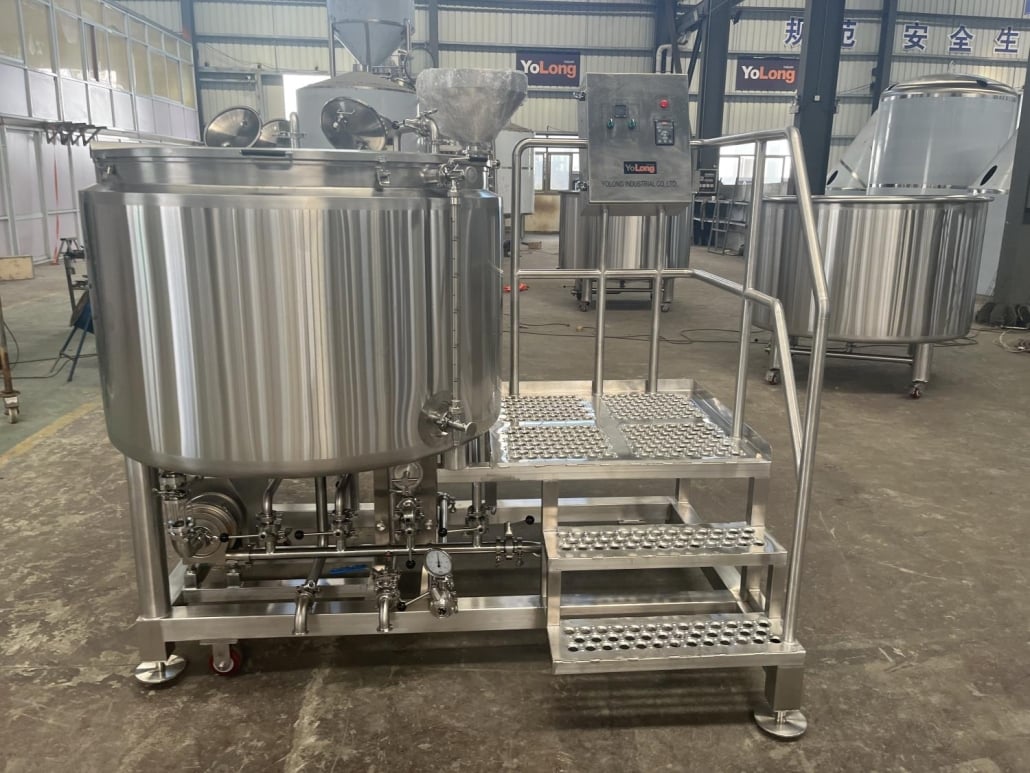
FAQ
Question | Answer |
---|---|
What is the average cost of setting up a microbrewery? | Costs range from $50,000 to $500,000 depending on the scale, customization, and equipment quality. |
Can I start a microbrewery at home? | Yes, though zoning laws and equipment space will limit scale; home-brewing kits are a good start for practice. |
How much space does micro brewing equipment require? | Small systems need around 500 sq. ft., while larger setups may require 2,000 sq. ft. or more. |
What maintenance is required for brewing equipment? | Routine cleaning, lubrication, and inspection of seals, sensors, and valves are essential for consistent quality. |
Share this entry
Interested in learning more about Brewing Systems including additional details and pricing information? Please use the form below to contact us!
YOLONG BREWERY EQUIPMENT FAQS
- Commercial Brewery / Craft Brewery / Microbrewery / Nanobrewery
- What is The Difference Between Craft Beer and Industrial Beer?
- The Bespoke Differences In Custom Brewing Systems
- Everything You Need to Know About Kettle Souring
- How to Choose Brewing Equipment for Your business?
- How To Choose The-Best Partner To Build Your Commercial Microbrewing System?
- Two Detection Sensors That You Need To Use In Your Brewhouse System
- Remote Control Applications in Brewing Equipment/How does it work?
- How To Clean Your Brand New Brewery Tanks?