Industrial Brewing Equipment
Overview of Industrial Brewing Equipment
Industrial brewing equipment refers to the machinery and tools used in the large-scale production of beer. Unlike homebrewing setups, industrial systems handle significant volumes and require sophisticated designs for precision, efficiency, and consistency. The brewing process, from mashing to fermentation, demands equipment tailored to meet the high standards of taste, quality, and production capacity.
Key Features of Industrial Brewing Equipment
- Scalability: Designed for high production volumes.
- Automation: Advanced systems ensure consistency and reduce manual intervention.
- Durability: Built with stainless steel and corrosion-resistant materials.
- Customizability: Equipment can be tailored to specific recipes and production needs.
- Efficiency: Optimized for energy savings and resource management.
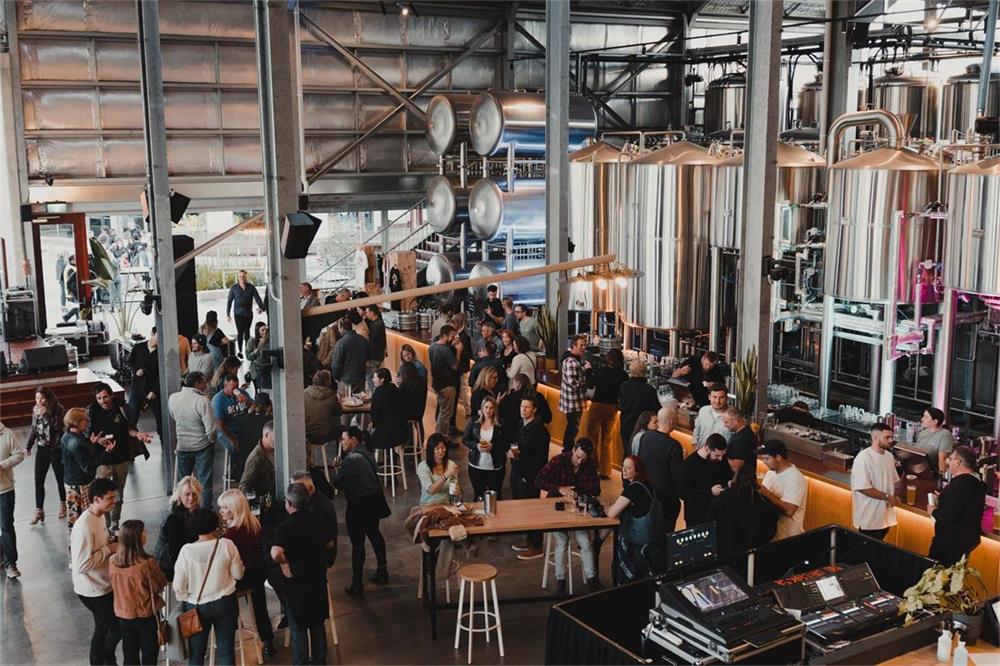
Troubleshooting Common Issues with Microbrewing Equipment
Even the best equipment isn’t immune to hiccups. Here’s a closer look at common challenges and how to tackle them:
1. Uneven Heating During Mashing
Uneven heating can lead to inconsistent sugar extraction, affecting the beer’s flavor. Often, this issue arises from malfunctioning heating elements or poor circulation in the mash tun.
- Solution: Regularly inspect heating elements for wear and clean them to ensure proper function. Use stirring mechanisms or recirculation pumps to maintain even temperature distribution.
2. Clogged Fermenters
Fermenters can get clogged with yeast or trub, disrupting fermentation and cleaning processes.
- Solution: Use conical fermenters that allow easy removal of sediment. Regularly clean fermenters and sanitize fittings to prevent blockages.
3. Pump Failures
Pumps are the lifeblood of industrial brewing systems, moving liquids between stages. Overuse or improper maintenance can lead to failures.
- Solution: Check for worn-out seals or impellers. Schedule routine maintenance and keep spare parts handy.
4. Inefficient Cooling Systems
Cooling systems that fail to drop the wort temperature fast enough can lead to poor fermentation or contamination.
- Solution: Inspect glycol systems for leaks and ensure proper insulation. Use heat exchangers for efficient cooling.
5. Automation Glitches
Software-driven automation systems occasionally malfunction, leading to errors in timing or temperature control.
- Solution: Keep software updated and have a technician on call for troubleshooting.
The Brewing Process: Step-by-Step
Industrial brewing is a finely tuned process, where each step builds on the last to create the perfect beer. Let’s break it down:
1. Milling
The process begins with milling malted barley to break open the grain and expose the starches. This is critical for efficient sugar extraction.
- Equipment Used: Roller mills, hammer mills.
- Key Considerations: Consistency in grain size ensures optimal mashing.
2. Mashing
Milled grains are mixed with hot water in the mash tun to convert starches into fermentable sugars.
- Equipment Used: Mash tuns with heating and stirring mechanisms.
- Key Considerations: Precise temperature control is crucial for enzyme activity.
3. Lautering
The mash is transferred to the lauter tun, where the liquid wort is separated from the solid grain husks.
- Equipment Used: Lauter tuns with false bottoms and rakes.
- Key Considerations: Ensure proper drainage to avoid stuck mashes.
4. Boiling
The wort is boiled in a kettle, hops are added, and unwanted compounds are removed.
- Equipment Used: Boiling kettles, hop dosing systems.
- Key Considerations: Uniform heating and controlled boil-off rates.
5. Cooling
The hot wort is rapidly cooled to a temperature suitable for yeast fermentation.
- Equipment Used: Plate heat exchangers, glycol systems.
- Key Considerations: Rapid cooling minimizes contamination risk.
6. Fermentation
Yeast is added to the cooled wort, converting sugars into alcohol and CO2.
- Equipment Used: Conical fermenters, temperature control systems.
- Key Considerations: Monitor temperature and pressure closely.
7. Filtration and Packaging
The beer is filtered to remove any remaining particulates and then packaged for distribution.
- Equipment Used: Filtration systems, bottling or kegging lines.
- Key Considerations: Maintain sterility to avoid contamination.
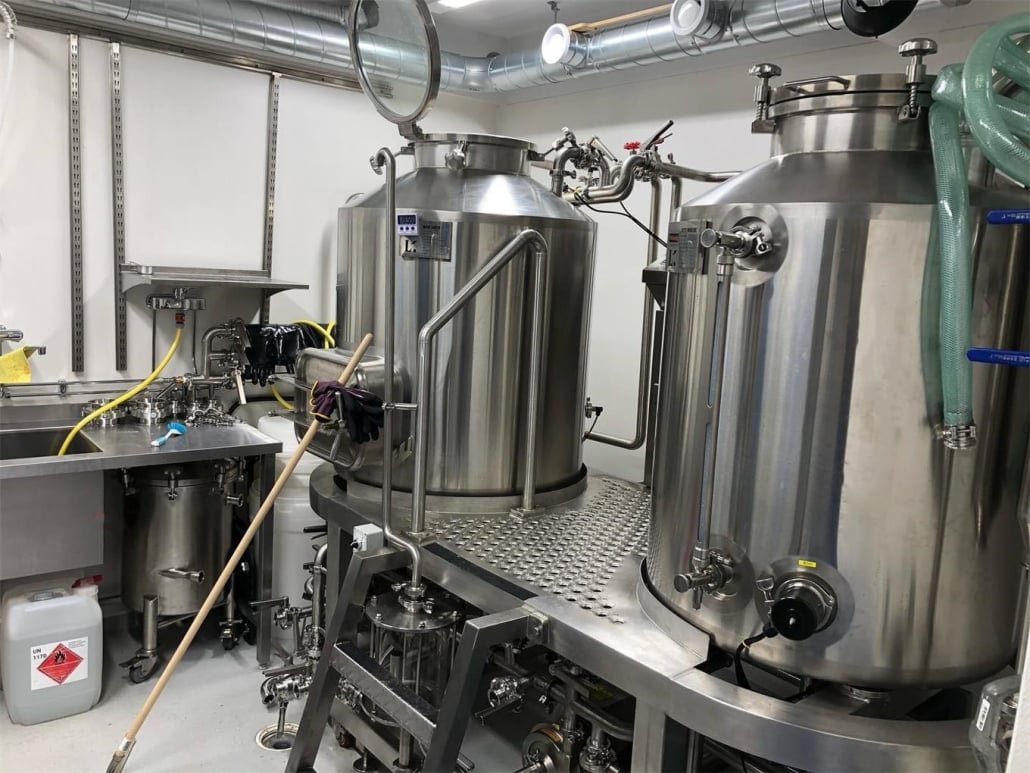
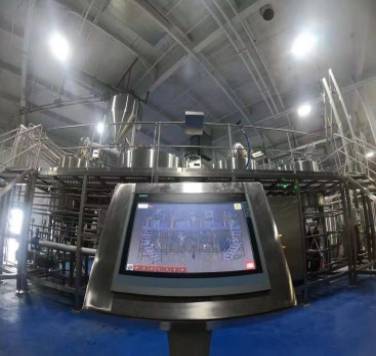
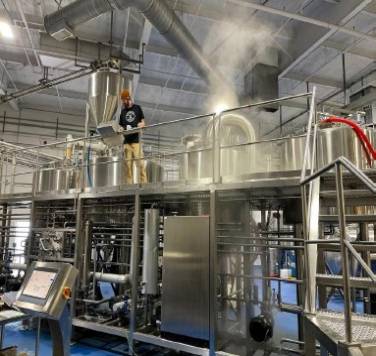
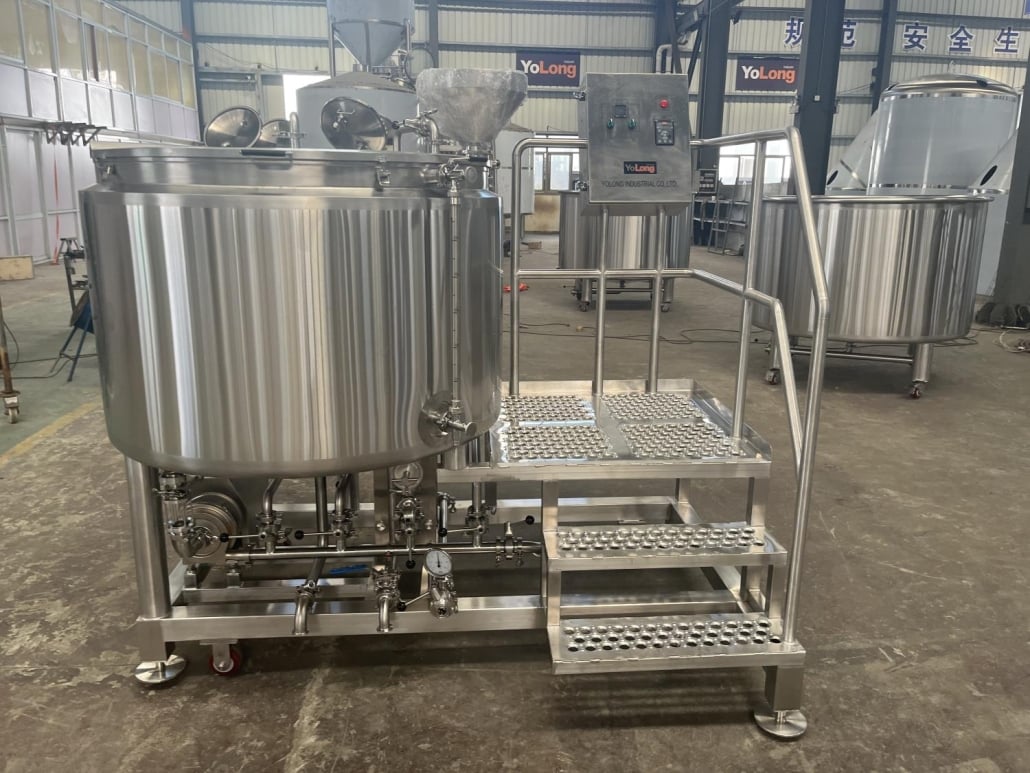
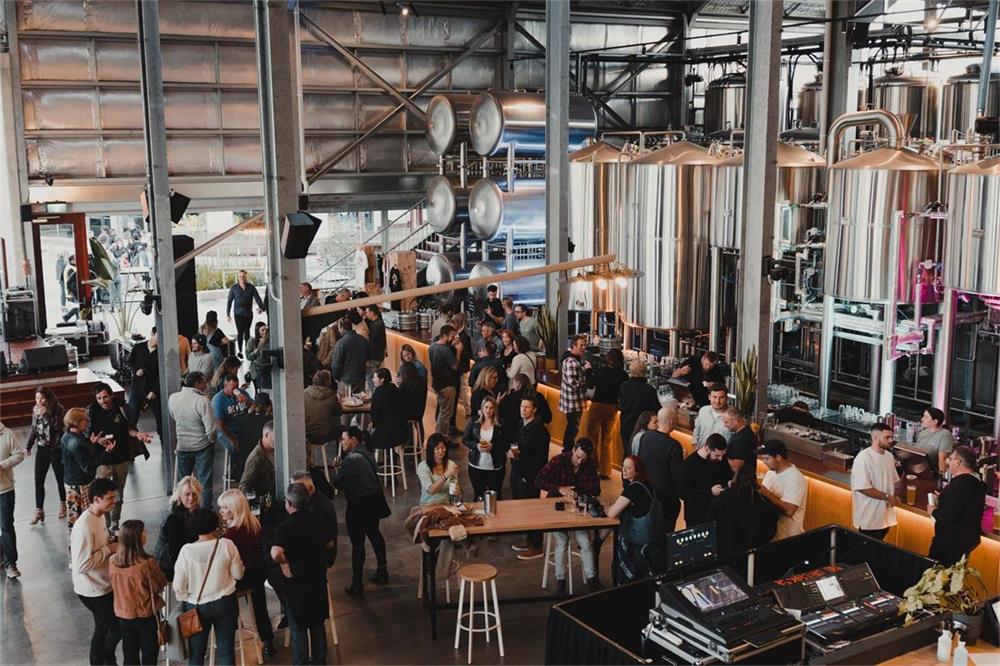
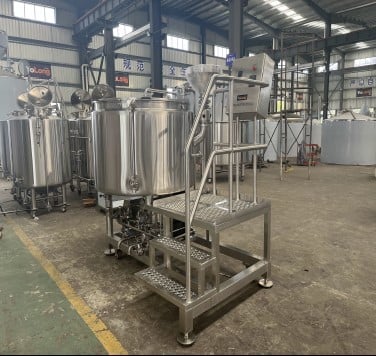
Industrial Brewing Equipment: Capacities, Spaces, Design, and Layout
Feature | Details |
---|---|
Capacity | Ranges from 5 HL to 300 HL, depending on production scale. |
Space Requirements | Compact systems for small breweries; large-scale systems need dedicated facilities. |
Design | Stainless steel construction, CIP (Clean-In-Place) systems for hygiene. |
Layout | Modular designs allow flexible configurations to fit available space. |
Customization | Tailored setups for specific brewing styles and recipes. |
Suppliers and Price Range
Supplier | Price Range (USD) | Key Features |
---|---|---|
BrewTech | $50,000 – $500,000 | Modular systems, advanced automation. |
Alpha Brewing Ops | $75,000 – $750,000 | Customizable setups, turnkey solutions. |
Ss BrewTech | $30,000 – $250,000 | Compact designs for microbreweries. |
Lehui | $100,000 – $1,000,000+ | Large-scale solutions, global presence. |
Installation, Operation, and Maintenance
Aspect | Details |
---|---|
Installation | Requires professional setup, alignment, and calibration by experienced technicians. |
Operation | User-friendly interfaces with training provided for operators. |
Maintenance | Includes regular cleaning, lubrication of moving parts, and software updates. |
Key Challenges | Availability of spare parts, skilled maintenance personnel. |
How to Choose the Right Industrial Brewing Equipment
Factor | Details |
---|---|
Production Volume | Determine current and future capacity needs to avoid under- or over-investing. |
Budget | Assess total costs, including installation and maintenance. |
Customization Options | Ensure the equipment supports your brewing style and recipes. |
Supplier Reputation | Research reviews, customer feedback, and after-sales support. |
Energy Efficiency | Look for systems designed to minimize power and water consumption. |
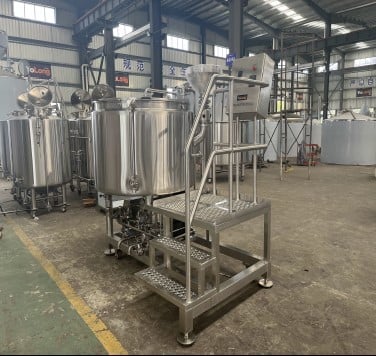
Pros and Cons of Industrial Brewing Equipment
Aspect | Advantages | Limitations |
---|---|---|
Scalability | Supports large-scale production. | High initial investment cost. |
Automation | Ensures consistency and efficiency. | Requires skilled operators for troubleshooting. |
Durability | Long lifespan with proper maintenance. | Regular maintenance can be expensive. |
Customization | Tailored for specific needs. | Lead times for custom setups can be lengthy. |
FAQ
Question | Answer |
---|---|
What is the lifespan of industrial brewing equipment? | Typically 10-20 years with proper maintenance. |
How much does industrial brewing equipment cost? | Ranges from $30,000 to over $1,000,000, depending on size and features. |
Can I use industrial equipment for craft brewing? | Yes, many systems are scalable and customizable for craft breweries. |
What maintenance is required? | Regular cleaning, inspections, lubrication, and software updates. |
How do I choose the right supplier? | Look for reputation, reviews, customization options, and after-sales support. |
Share this entry
Interested in learning more about Brewing Systems including additional details and pricing information? Please use the form below to contact us!
YOLONG BREWERY EQUIPMENT FAQS
- Commercial Brewery / Craft Brewery / Microbrewery / Nanobrewery
- What is The Difference Between Craft Beer and Industrial Beer?
- The Bespoke Differences In Custom Brewing Systems
- Everything You Need to Know About Kettle Souring
- How to Choose Brewing Equipment for Your business?
- How To Choose The-Best Partner To Build Your Commercial Microbrewing System?
- Two Detection Sensors That You Need To Use In Your Brewhouse System
- Remote Control Applications in Brewing Equipment/How does it work?
- How To Clean Your Brand New Brewery Tanks?