Industrial Beer Making Equipment
Overview of industrial beer making equipment
Beer brewing has evolved from small-scale craft operations to large-scale industrial production. Today, breweries use state-of-the-art industrial beer-making equipment to streamline the brewing process, ensuring consistency, efficiency, and high-quality beer. This guide explores the essential components of industrial brewing systems, how to choose the right equipment, costs, top manufacturers, maintenance tips, and future trends in beer brewing technology.
The Importance of industrial beer making equipment in Modern Beer Production
The beer industry has seen massive growth, with consumers demanding more variety and higher quality. Industrial beer-making equipment plays a crucial role in meeting this demand by automating processes, enhancing precision, and ensuring large-scale production without compromising flavor. The right brewing equipment helps breweries maintain consistency, optimize ingredient usage, and reduce waste, making it a key factor in the success of any beer production facility.
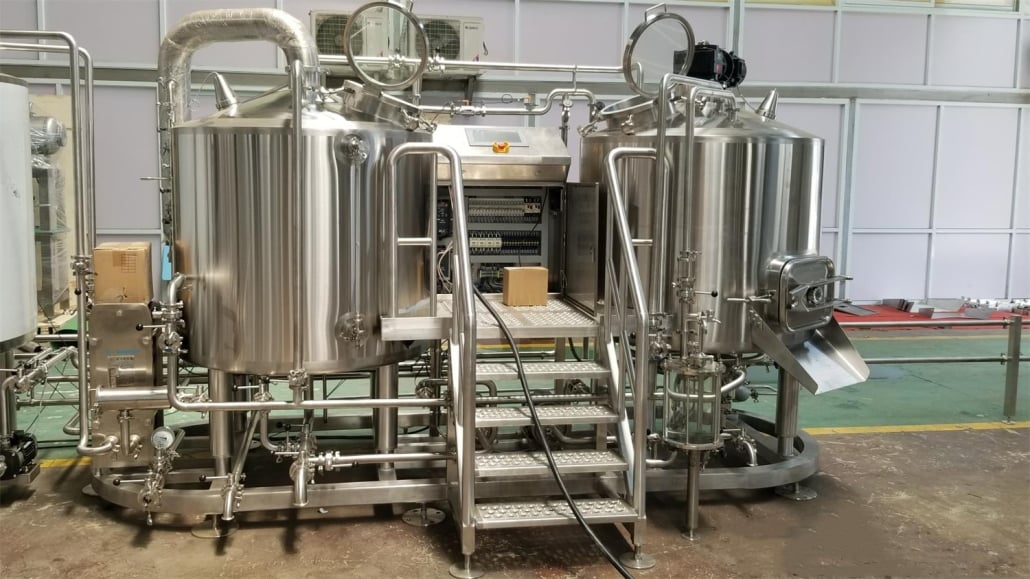
What Is industrial beer making equipment?
Industrial beer-making equipment refers to the machinery used in large-scale beer production. This equipment covers everything from raw material processing to fermentation, filtration, packaging, and distribution. Unlike homebrewing or craft brewing systems, industrial brewing setups can handle thousands of liters per batch, allowing breweries to meet market demands efficiently.
Key Components of Industrial Beer Brewing Equipment
Industrial brewing equipment consists of various components that work together to produce high-quality beer efficiently. Below are the essential elements:
Milling System
Malted barley is crushed in a milling system to break down starches and expose fermentable sugars, ensuring efficient mashing.
Mashing System
The milled grains are mixed with hot water in the mash tun, allowing enzymes to break down starches into fermentable sugars.
Lautering System
The mash is transferred to a lauter tun, where the wort is separated from the spent grain.
Boiling Kettle
The wort is boiled with hops to extract bitterness, flavor, and aroma. This process sterilizes the wort and helps in protein coagulation.
Whirlpool System
After boiling, the wort is spun in a whirlpool tank to separate solid particles before cooling.
Cooling and Fermentation System
The cooled wort is transferred to fermentation tanks, where yeast is added. The yeast converts sugars into alcohol and carbon dioxide.
Filtration and Clarification Equipment
Filtration removes solids and ensures beer clarity. Advanced systems include centrifuges and diatomaceous earth filters.
Carbonation and Conditioning Tanks
Beer is carbonated and conditioned to develop its final flavor and texture.
Packaging Line
The beer is packaged in kegs, cans, or bottles using automated packaging lines.
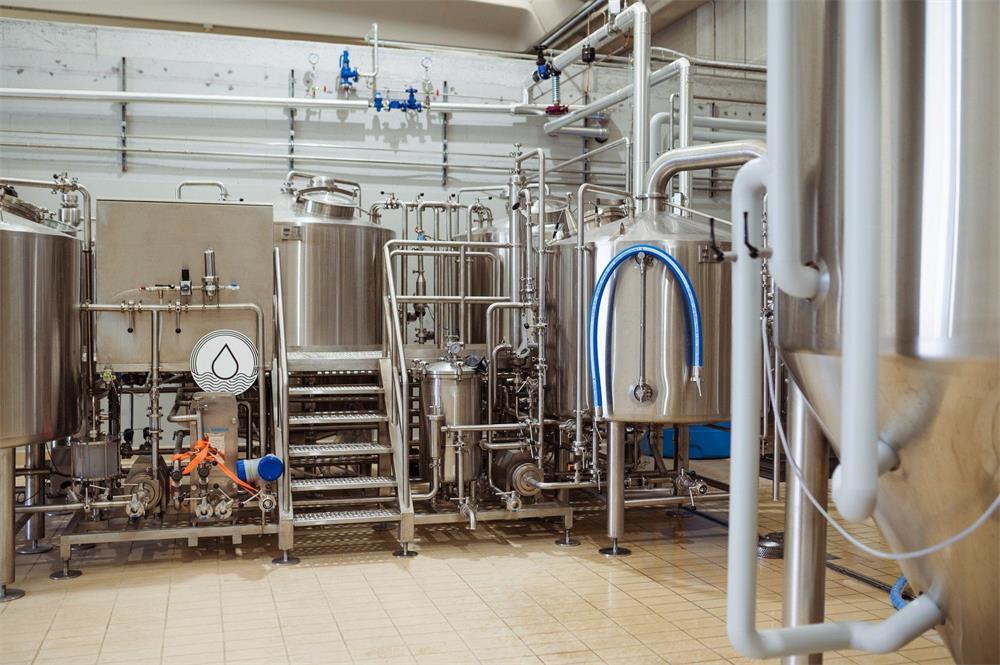
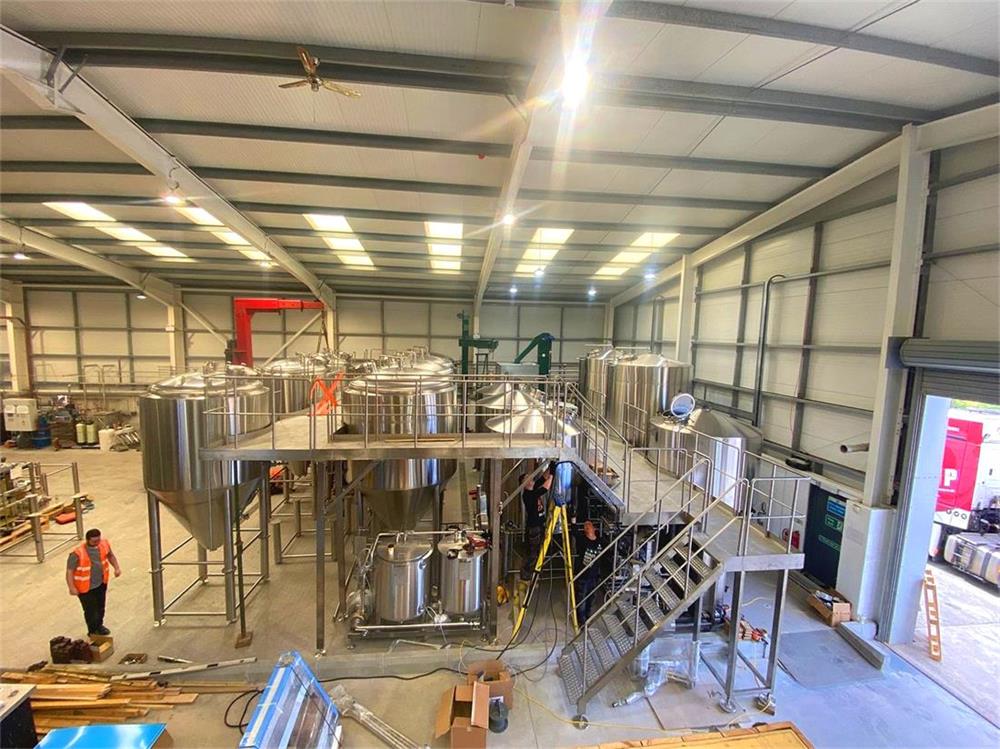
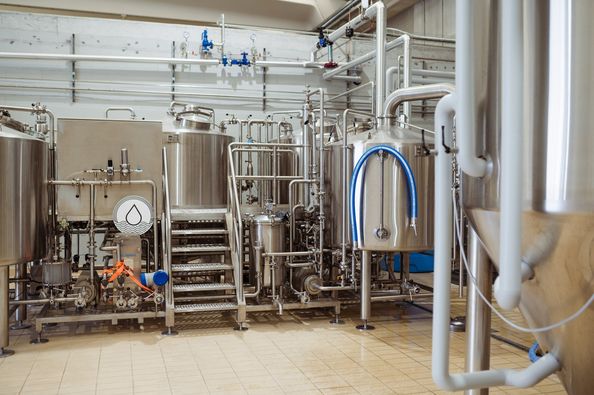
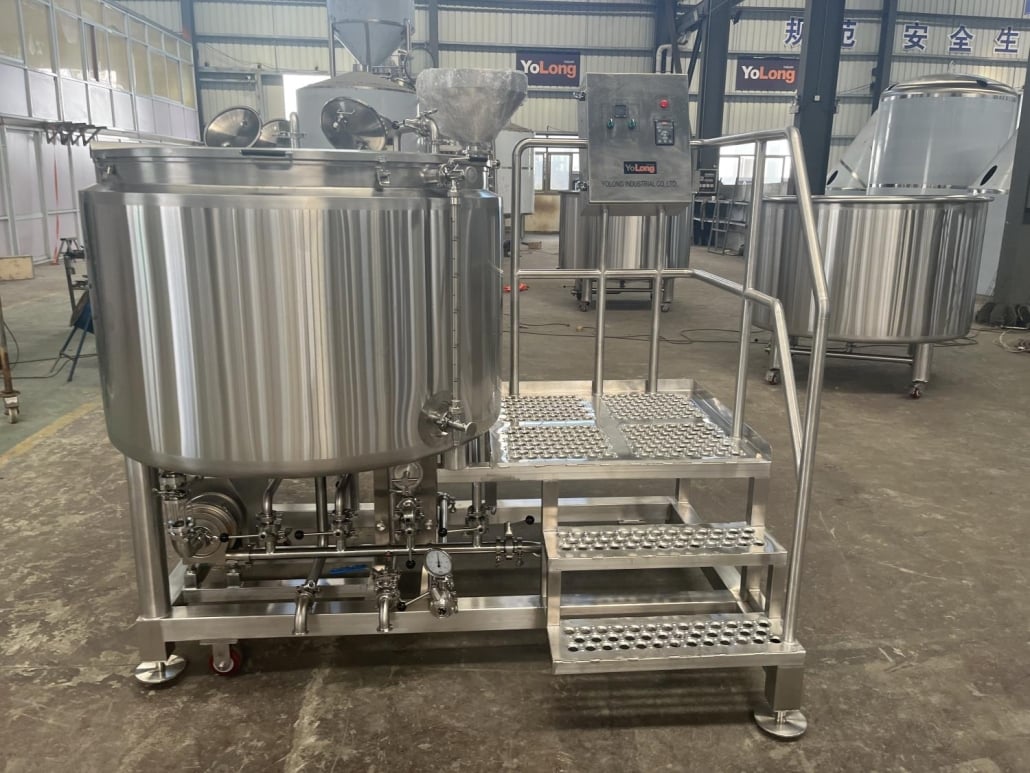
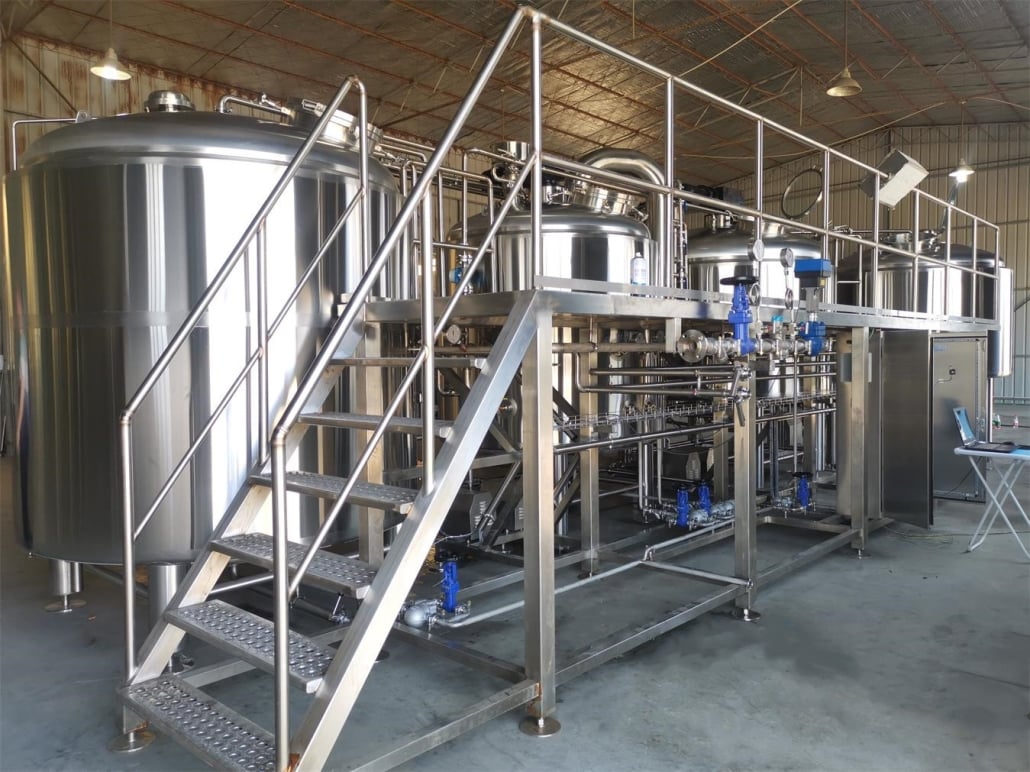
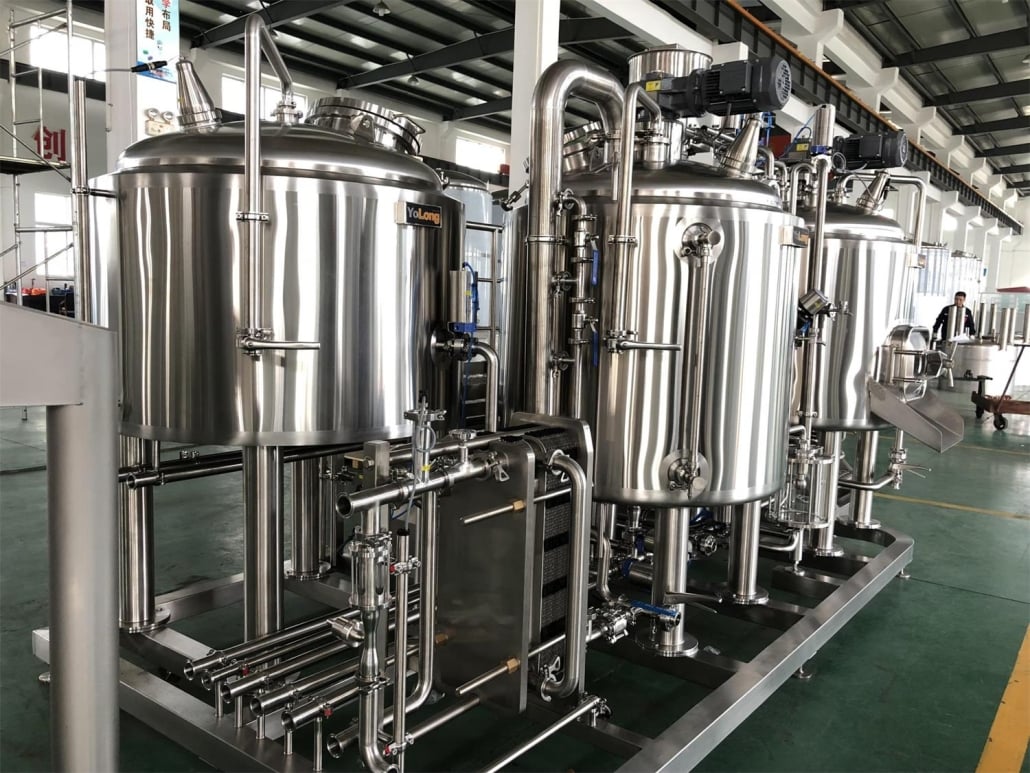
How to Choose the Right Beer Making Equipment?
Selecting the right industrial brewing equipment depends on several factors. The table below outlines key considerations:
Factor | Details |
---|---|
Production Capacity | Consider batch size and annual output. |
Automation Level | Choose between semi-automatic and fully automated systems. |
Space Requirements | Ensure equipment fits within your brewery layout. |
Budget | Balance between initial investment and long-term cost savings. |
Scalability | Opt for equipment that can scale as demand increases. |
Energy Efficiency | Look for energy-saving features to reduce operational costs. |
Cost Analysis: How Much Does Industrial Brewery Equipment Cost?
The cost of industrial brewing equipment varies based on capacity, automation, and brand. Here’s a general breakdown:
Equipment Type | Price Range |
---|---|
Small Brewery (5-10 BBL) | $50,000 – $200,000 |
Medium Brewery (10-50 BBL) | $200,000 – $1,000,000 |
Large Brewery (50+ BBL) | $1,000,000+ |
Full Automated System | $500,000 – $5,000,000 |
Best Industrial Beer Equipment Brands and Manufacturers
Several manufacturers dominate the industrial brewing equipment market. Some of the most reputable brands include:
- Krones AG – Known for high-end automation and packaging solutions.
- GEA Group – Specializes in brewing technology and filtration systems.
- Brewery Mechanization Systems (BMS) – Offers customized brewing solutions.
- Ss Brewtech – Provides advanced fermentation and brewing systems.
- Ziemann Holvrieka – Renowned for large-scale brewery solutions.
Maintenance and Cleaning Tips for Brewery Equipment
Proper maintenance ensures the longevity and efficiency of brewing equipment. Here are some essential maintenance tips:
- Regular Cleaning – Use CIP (Clean-In-Place) systems to sanitize tanks and pipes.
- Routine Inspections – Check for leaks, wear, and tear regularly.
- Lubrication – Keep moving parts lubricated to prevent breakdowns.
- Filter Replacement – Change filters periodically to maintain efficiency.
- Calibration – Ensure sensors and temperature controls are accurate.
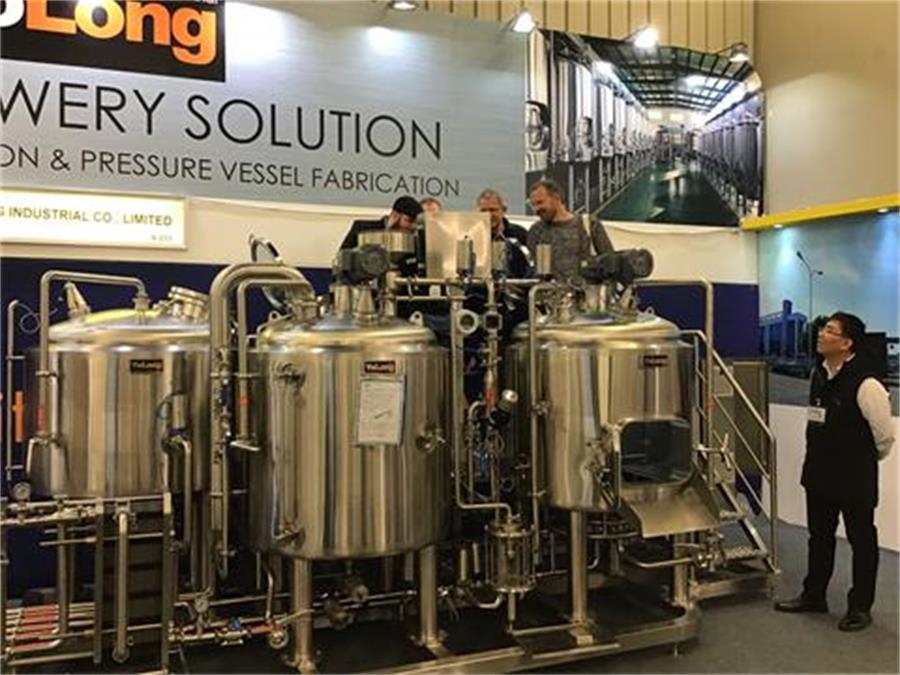
Future Trends in Beer Brewing Equipment
Technology continues to shape the brewing industry. Emerging trends include:
- Automation & AI – Smart brewing systems optimize efficiency and consistency.
- Sustainability – Energy-efficient and eco-friendly brewing solutions.
- Small-Batch Industrial Brewing – Large breweries adopting craft-style production.
- Enhanced Quality Control – Advanced analytics and sensors for precision brewing.
FAQs
Question | Answer |
---|---|
What is the lifespan of brewing equipment? | Typically 10-20 years with proper maintenance. |
Can industrial equipment be customized? | Yes, many manufacturers offer tailored brewing solutions. |
How long does beer fermentation take? | It varies from 5 days to several weeks, depending on the beer style. |
What is the best material for brewing tanks? | Stainless steel is preferred for durability and hygiene. |
How do breweries manage waste? | Waste is processed through filtration and repurposed for animal feed or biogas. |
Share this entry
Interested in learning more about Brewing Systems including additional details and pricing information? Please use the form below to contact us!
YOLONG BREWERY EQUIPMENT FAQS
- Commercial Brewery / Craft Brewery / Microbrewery / Nanobrewery
- What is The Difference Between Craft Beer and Industrial Beer?
- The Bespoke Differences In Custom Brewing Systems
- Everything You Need to Know About Kettle Souring
- How to Choose Brewing Equipment for Your business?
- How To Choose The-Best Partner To Build Your Commercial Microbrewing System?
- Two Detection Sensors That You Need To Use In Your Brewhouse System
- Remote Control Applications in Brewing Equipment/How does it work?
- How To Clean Your Brand New Brewery Tanks?