Electric Brewing System
Overview
Electric brewing systems have revolutionized the home and small-scale commercial brewing industry. Gone are the days of clunky, gas-powered setups; the modern brewer now enjoys the precision, convenience, and safety of electric systems. Whether you’re a seasoned brewer looking to upgrade or a beginner eager to dive into the craft, understanding the intricacies of electric brewing systems is crucial. In this guide, we’ll explore everything you need to know about electric brewing systems, from equipment choices and brewing processes to installation, operation, and maintenance.
Understanding Electric Brewing Systems
Electric brewing systems are advanced setups that utilize electricity to heat water, mash grains, and boil wort in the beer-making process. Unlike traditional brewing methods that rely on gas burners, electric systems offer greater control over temperature and are typically more energy-efficient. These systems can be tailored for home brewers or scaled up for microbreweries.
Benefits of Electric Brewing Systems
Electric brewing systems provide several advantages over traditional gas-powered systems:
- Precision and Control: Electric systems allow for precise temperature control, essential for consistent brewing results.
- Energy Efficiency: Compared to gas burners, electric systems are often more energy-efficient, reducing the overall cost of brewing.
- Safety: Electric brewing eliminates the need for open flames, reducing the risk of accidents in the brewing area.
- Space-Saving: Electric systems are often more compact, making them ideal for small brewing spaces.
Electric Brewing Equipment Guide
Choosing the right equipment is crucial for successful brewing. The market is flooded with various options, each with unique features and specifications. Here’s a detailed look at the core components of an electric brewing system.
Key Components
- Brew Kettle: The heart of the brewing process, where wort is boiled and hops are added.
- Mash Tun: A vessel used to steep and mash grains, converting starches to sugars.
- Hot Liquor Tank (HLT): Holds and heats water used in the brewing process, particularly for mashing and sparging.
- Electric Heating Elements: Replace traditional burners and provide consistent, controllable heat.
- Pump: Circulates wort between vessels during brewing.
- Control Panel: Centralized unit to monitor and adjust temperatures, timers, and pump operations.
Choosing the Right Equipment
When selecting an electric brewing system, consider the following factors:
- Batch Size: Determine how much beer you intend to brew at one time. Home brewers might need a smaller system, whereas microbreweries require larger setups.
- Material Quality: Stainless steel is the preferred material for brewing equipment due to its durability and resistance to corrosion.
- Automation Level: Some systems are fully automated, while others offer manual control. Your choice depends on your brewing experience and desired involvement in the brewing process.
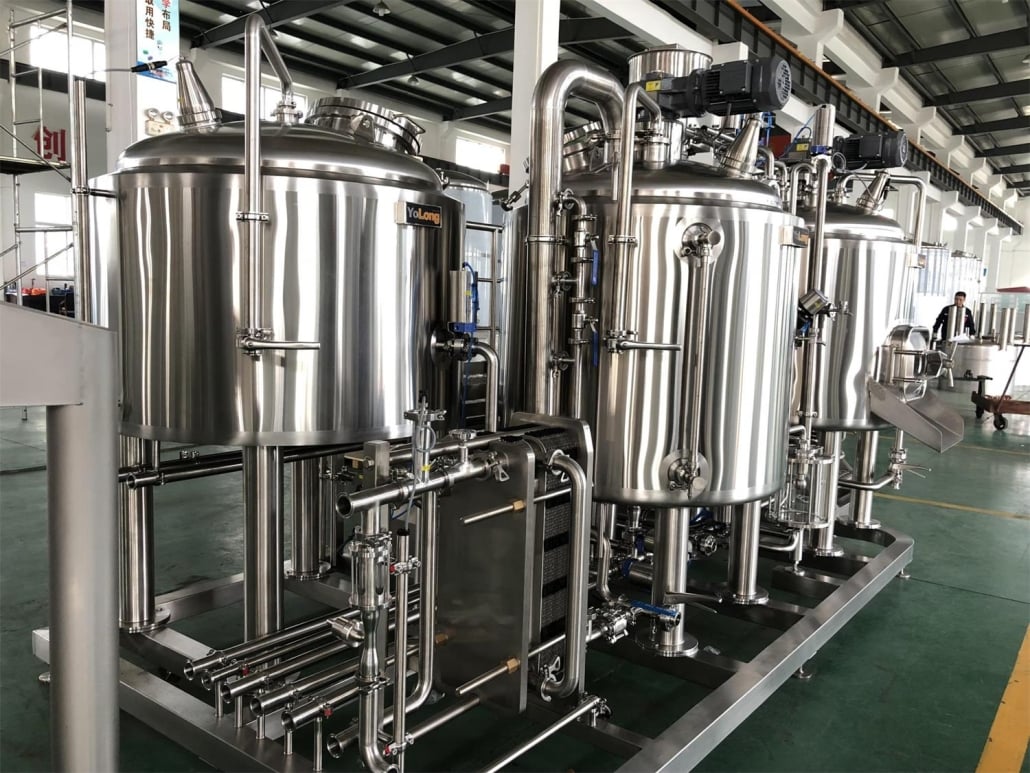
Types of Electric Brewing Systems
System Type | Features | Best For |
---|---|---|
All-In-One Systems | Combines mash tun, brew kettle, and sometimes the HLT into a single unit. | Home brewers, beginners |
Three-Vessel Systems | Separate vessels for mash tun, brew kettle, and HLT. Offers more control and capacity. | Advanced home brewers, microbreweries |
BIAB (Brew in a Bag) | Simplified system where mashing and boiling occur in the same vessel, using a mesh bag for grains. | Budget-conscious brewers, small spaces |
Custom-Built Systems | Tailored to specific needs, offering full control over each aspect of the brewing process. | Professional brewers, enthusiasts |
Electric Brewing Process Explained
Brewing beer with an electric system follows the same basic principles as traditional brewing, with added benefits of automation and control. Let’s walk through the process step by step.
1. Heating the Water
The brewing process begins by heating water in the Hot Liquor Tank (HLT). The control panel allows for precise temperature settings, crucial for the consistency of the brewing process.
2. Mashing the Grains
Once the water reaches the desired temperature, it is transferred to the mash tun, where it mixes with crushed grains. This process converts the starches in the grains into fermentable sugars, creating a sweet liquid known as wort.
3. Recirculating the Wort
In some electric systems, a pump recirculates the wort, ensuring even temperature distribution and improving the efficiency of sugar extraction from the grains.
4. Sparging
After mashing, the grains are rinsed with hot water in a process called sparging. This step extracts the remaining sugars from the grains, increasing the wort’s sugar content.
5. Boiling the Wort
The wort is then transferred to the brew kettle, where it is boiled. During this stage, hops are added to impart bitterness, flavor, and aroma to the beer. The precise control offered by electric systems ensures a consistent boil, crucial for hop utilization and wort sterilization.
6. Cooling the Wort
After boiling, the wort needs to be quickly cooled to a temperature suitable for fermentation. Electric systems often include a wort chiller, which rapidly reduces the temperature, minimizing the risk of contamination.
7. Fermentation
The cooled wort is transferred to a fermenter, where yeast is added. The yeast consumes the sugars in the wort, producing alcohol and carbon dioxide. Temperature control is critical during this stage, and electric systems may include temperature-controlled fermenters.
8. Bottling and Conditioning
Once fermentation is complete, the beer is bottled and allowed to condition, where it develops carbonation and matures in flavor.
Electric Brewing System Design and Layout
Designing the layout of your brewing system is crucial for efficient operation. Whether you’re setting up in a small home space or a larger microbrewery, planning the design carefully can save time and effort during brewing.
Considerations for Layout
Factor | Details |
---|---|
Space Availability | Ensure that your setup fits comfortably in your brewing space. Consider vertical setups for small areas. |
Workflow Efficiency | Arrange equipment in a logical sequence to minimize movement during brewing. |
Ventilation | Electric systems generate heat and steam; ensure adequate ventilation in your brewing space. |
Power Supply | Verify that your electrical setup can handle the power requirements of your system. |
Sanitation | Design the layout to facilitate easy cleaning and maintenance. |
Customization Options for Electric Brewing Systems
Customization is a significant advantage of electric brewing systems. Whether you want to automate more of the process, increase capacity, or add specific features, many manufacturers offer tailored solutions.
Popular Customization Options
- Automated Control Panels: Incorporate advanced controllers for precise management of temperatures, timers, and pumps.
- Increased Capacity: Upgrade vessels to larger sizes to accommodate bigger batches.
- Integrated Chillers: Add built-in wort chillers for rapid cooling post-boil.
- Advanced Filtration Systems: Ensure clearer beer with built-in filtration solutions.
- Aesthetic Modifications: Customize the appearance of your system with different finishes, branding, or decorative elements.
Electric Brewing System Price Range
The cost of an electric brewing system can vary widely based on factors like capacity, level of automation, material quality, and brand reputation. Below is a general guide to price ranges.
System Type | Price Range (USD) | Notes |
---|---|---|
Entry-Level Systems | $500 – $1,500 | Suitable for hobbyists and small-scale home brewers. Often includes basic all-in-one systems. |
Mid-Range Systems | $1,500 – $4,000 | Offers more capacity, automation, and customization. Ideal for serious home brewers. |
High-End Systems | $4,000 – $10,000+ | Professional-grade systems with advanced features, suitable for microbreweries or large-scale production. |
Custom-Built Systems | Varies widely | Prices depend on specific customizations, with costs potentially exceeding standard high-end systems. |
How to Choose an Electric Brewing System Supplier
Choosing the right supplier is as important as selecting the right system. A reliable supplier will offer quality products, good customer support, and comprehensive warranties.
Factors to Consider
Criteria | Details |
---|---|
Reputation | Look for suppliers with positive reviews and a strong track record in the industry. |
Customer Support | Ensure that the supplier offers robust after-sales support and technical assistance. |
Warranty | Check for warranty terms that cover key components like control panels, heating elements, and pumps. |
Customization Options | Choose a supplier that can accommodate your specific needs and offers flexibility in system design. |
Price Transparency | The supplier should provide clear, detailed quotes without hidden costs. |
Installation, Operation, and Maintenance of Electric Brewing Systems
Proper installation, operation, and maintenance are crucial for the longevity and performance of your electric brewing system.
Installation Tips
- Electrical Setup: Ensure that the brewing area has a dedicated circuit that can handle the system’s power requirements. Hire a licensed electrician if necessary.
- Ventilation: Install appropriate ventilation to manage steam and heat output, preventing condensation and potential mold issues.
- Space Planning: Leave sufficient space around equipment for maintenance access and ensure easy reach to control panels and pumps.
Operation Guidelines
- Safety First: Always follow the manufacturer’s instructions for operating the system, particularly regarding electrical components.
- Temperature Monitoring: Keep a close eye on temperature settings during brewing to avoid overheating or under-heating.
- Cleaning and Sanitizing: Regularly clean all components, especially those that come in direct contact with wort and beer, to prevent contamination.
Maintenance Essentials
Component | Maintenance Task | Frequency |
---|---|---|
Heating Elements | Inspect and clean to prevent scale buildup. | After every brewing session |
Control Panel | Check for software updates and ensure buttons/switches function properly. | Monthly |
Pumps and Valves | Lubricate and check for leaks. | Quarterly |
Vessels | Clean thoroughly, checking for signs of wear or corrosion. | After every brewing session |
Comparing Electric Brewing Systems: Pros and Cons
To make an informed decision, it’s essential to weigh the pros and cons of electric brewing systems against traditional methods.
Advantages of Electric Brewing Systems
- Precision: Electric systems offer exact temperature control, essential for consistent brewing.
- Energy Efficiency: Generally more energy-efficient compared to gas systems, reducing operational costs.
- Safety: Eliminates the risk associated with open flames, making the brewing environment safer.
- Space-Saving: Compact designs make them ideal for small brewing spaces.
- Environmentally Friendly: Electric systems produce fewer emissions compared to gas-powered alternatives.
Limitations of Electric Brewing Systems
- Initial Cost: Electric systems can be more expensive upfront, especially for high-end or custom-built models.
- Power Dependency: They rely on a stable electrical supply, which can be a disadvantage in areas prone to power outages.
- Learning Curve: Advanced systems, especially those with full automation, may require a steeper learning curve for beginners.
Electric vs. Gas Brewing Systems
Feature | Electric Brewing Systems | Gas Brewing Systems |
---|---|---|
Temperature Control | Precise and consistent | Can be harder to control, especially in outdoor settings. |
Energy Efficiency | Generally more energy-efficient | Typically less efficient, with more heat loss. |
Safety | Safer, with no open flames | Higher risk due to open flames and potential gas leaks. |
Cost | Higher initial cost, but lower operational costs | Lower initial cost, but potentially higher operational costs. |
Portability | Less portable, requires stable electricity | More portable, especially for outdoor brewing. |
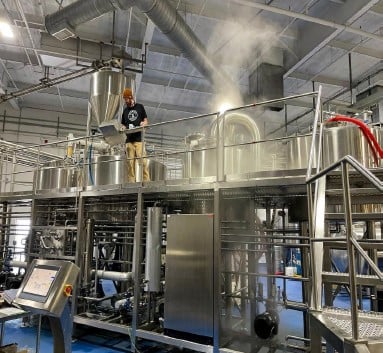
FAQs
What is an Electric Brewing System?
An electric brewing system is a setup that uses electric heating elements to control the temperature during the beer brewing process. It replaces traditional gas burners with electric components, providing more precise control over the brewing process.
How Much Does an Electric Brewing System Cost?
The cost varies widely based on the system’s size, automation level, and customization. Entry-level systems may cost between $500 and $1,500, while high-end or custom-built systems can exceed $10,000.
Are Electric Brewing Systems Safe?
Yes, electric brewing systems are generally safer than gas-powered systems. They eliminate the risk of open flames and gas leaks, although it’s crucial to ensure proper electrical setup and ventilation.
Can I Customize My Electric Brewing System?
Absolutely! Many manufacturers offer customization options, from automated control panels to larger vessel capacities and integrated chillers.
What Are the Maintenance Requirements?
Regular maintenance includes cleaning the vessels and heating elements after each use, checking and lubricating pumps and valves quarterly, and ensuring that the control panel is functioning correctly.
How Do I Choose the Right System?
Consider your brewing needs, including batch size, available space, and budget. Evaluate different systems based on their features, customization options, and the reputation of the supplier.
Conclusion
Electric brewing systems represent the future of brewing for both home enthusiasts and small-scale commercial operations. Their precision, safety, and efficiency make them an attractive option for anyone serious about crafting high-quality beer. By understanding the components, processes, and customization options available, you can select the perfect system to meet your brewing needs. Whether you’re just starting or looking to upgrade, an electric brewing system is an investment in better beer and a more enjoyable brewing experience.
Share this entry
Interested in learning more about Brewing Systems including additional details and pricing information? Please use the form below to contact us!
YOLONG BREWERY EQUIPMENT FAQS
- Commercial Brewery / Craft Brewery / Microbrewery / Nanobrewery
- What is The Difference Between Craft Beer and Industrial Beer?
- The Bespoke Differences In Custom Brewing Systems
- Everything You Need to Know About Kettle Souring
- How to Choose Brewing Equipment for Your business?
- How To Choose The-Best Partner To Build Your Commercial Microbrewing System?
- Two Detection Sensors That You Need To Use In Your Brewhouse System
- Remote Control Applications in Brewing Equipment/How does it work?
- How To Clean Your Brand New Brewery Tanks?