Complete Beer Brewing System
Overview of a Complete Beer Brewing System
Brewing beer at home or in a small-scale commercial setup can be an immensely rewarding hobby or business venture. A complete beer brewing system encompasses all the equipment, tools, and knowledge necessary to transform grains, hops, water, and yeast into delicious craft beer. This guide aims to provide an in-depth look at everything you need to know about setting up and operating a beer brewing system, from the essential equipment to the detailed brewing process. We’ll also explore the different types of systems available, their capacities, space requirements, design and layout considerations, customization options, and more.
Essential Brewing Equipment
- Mash Tun: Used for mashing the grains and extracting fermentable sugars.
- Boil Kettle: Where the wort is boiled and hops are added for bitterness and aroma.
- Fermenter: A vessel where the wort is fermented by yeast to produce alcohol.
- Heat Source: Can be electric, propane, or natural gas, used to heat the mash tun and boil kettle.
- Cooling System: Usually a wort chiller to cool the wort quickly after boiling.
- Pumps and Tubing: For transferring liquids between vessels.
- Grain Mill: For crushing the grains before mashing.
- Cleaning and Sanitizing Equipment: Ensures all equipment is free from contaminants.
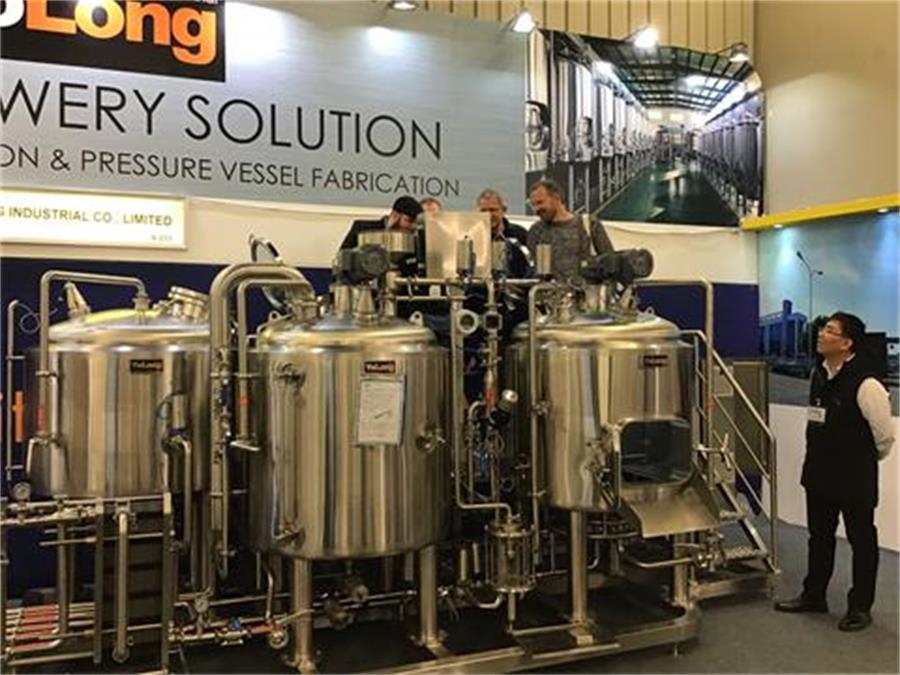
Types of Brewing Systems
Different brewing systems cater to varying levels of expertise, batch sizes, and budgets. Here’s a comparison of the main types of brewing systems available.
System Type | Description | Ideal For | Price Range |
---|---|---|---|
All-Grain Systems | Uses raw grains, providing full control over the brewing process. | Experienced brewers | $1,000 – $5,000+ |
Extract Systems | Utilizes malt extract, simplifying the brewing process. | Beginners and intermediate brewers | $100 – $1,000 |
Brew-in-a-Bag (BIAB) | A simplified all-grain method using a single vessel. | Homebrewers with limited space | $50 – $500 |
Electric Systems | Electric heating elements provide precise temperature control. | Homebrewers and small-scale commercial setups | $500 – $3,000+ |
Professional Systems | Large, automated systems designed for commercial brewing. | Microbreweries and brewpubs | $10,000 – $100,000+ |
The Brewing Process
Brewing beer involves several steps, each requiring specific equipment and techniques. Here’s a detailed look at the brewing process from start to finish.
Mashing
Mashing involves mixing crushed grains with hot water to create a mash. This activates enzymes that convert starches into fermentable sugars. The mash tun is typically used for this step.
Boiling
After mashing, the liquid, now called wort, is transferred to the boil kettle. The wort is boiled and hops are added at various stages to impart bitterness, flavor, and aroma.
Cooling
Post-boil, the wort must be cooled quickly to a temperature suitable for fermentation. This is often done using a wort chiller, which can be an immersion chiller, plate chiller, or counterflow chiller.
Fermentation
The cooled wort is transferred to a fermenter, where yeast is added. The yeast consumes the sugars, producing alcohol and carbon dioxide. This process can take from a few days to several weeks, depending on the beer style and fermentation temperature.
Conditioning and Packaging
After fermentation, the beer is conditioned to develop its final flavors and carbonation. It can be conditioned in the fermenter, in bottles, or in kegs. Once conditioned, the beer is packaged for consumption.
Capacity, Space, and Design Considerations
When choosing a brewing system, consider the following factors to ensure it fits your needs and space.
Parameter | Details |
---|---|
Capacity | Systems range from 1-gallon setups for hobbyists to 10+ barrel systems for commercial brewers. |
Space Requirements | Home systems can fit in a garage or basement, while commercial systems need dedicated brewing areas. |
Design and Layout | Modular designs allow for expansion; consider flow of ingredients and ease of cleaning. |
Customization Options | Systems can be customized with additional tanks, advanced controls, and automation features. |
Suppliers and Price Range
The price of a brewing system can vary widely based on its size, complexity, and features. Here’s an overview of some suppliers and the price range of their systems.
Supplier | System Type | Price Range |
---|---|---|
MoreBeer! | Homebrew and small commercial | $100 – $10,000 |
Ss Brewtech | Homebrew and commercial | $200 – $20,000 |
Spike Brewing | Homebrew and small commercial | $300 – $15,000 |
Blichmann Engineering | Homebrew and commercial | $200 – $25,000 |
Anvil Brewing | Homebrew | $100 – $5,000 |
Braukon | Commercial | $20,000 – $100,000+ |
Installation, Operation, and Maintenance
Setting up a brewing system requires careful planning and execution. Proper installation, operation, and maintenance are crucial to ensure smooth and efficient brewing.
Aspect | Details |
---|---|
Installation | Professional installation recommended for complex systems; ensure proper plumbing, electrical, and ventilation. |
Operation | Follow manufacturer guidelines; training may be required for advanced systems. |
Maintenance | Regular cleaning and sanitizing; periodic checks for wear and tear; follow a maintenance schedule. |
Choosing a Supplier
Selecting the right supplier is critical to getting a brewing system that meets your needs and budget. Here are some factors to consider.
Consideration | Details |
---|---|
Reputation | Look for reviews and testimonials; consider the supplier’s experience and reliability. |
Support and Service | Ensure the supplier offers good customer support, training, and after-sales service. |
Customization Options | Check if the supplier can customize the system to your specifications. |
Warranty and Guarantees | Look for warranties and guarantees that provide peace of mind. |
Advantages and Limitations of Different Brewing Systems
Different brewing systems have their own advantages and limitations. Here’s a comparison to help you decide which system is right for you.
System Type | Advantages | Limitations |
---|---|---|
All-Grain Systems | Full control over brewing process; better flavor potential. | More complex and time-consuming; requires more equipment. |
Extract Systems | Easier and quicker; less equipment needed. | Less control over final product; potentially less flavor complexity. |
Brew-in-a-Bag (BIAB) | Simplified all-grain method; less equipment needed. | Limited batch size; can be harder to maintain consistent temperatures. |
Electric Systems | Precise temperature control; can be used indoors. | Higher upfront cost; may require special electrical setup. |
Professional Systems | High efficiency; automation reduces labor. | Very expensive; requires significant space and infrastructure. |
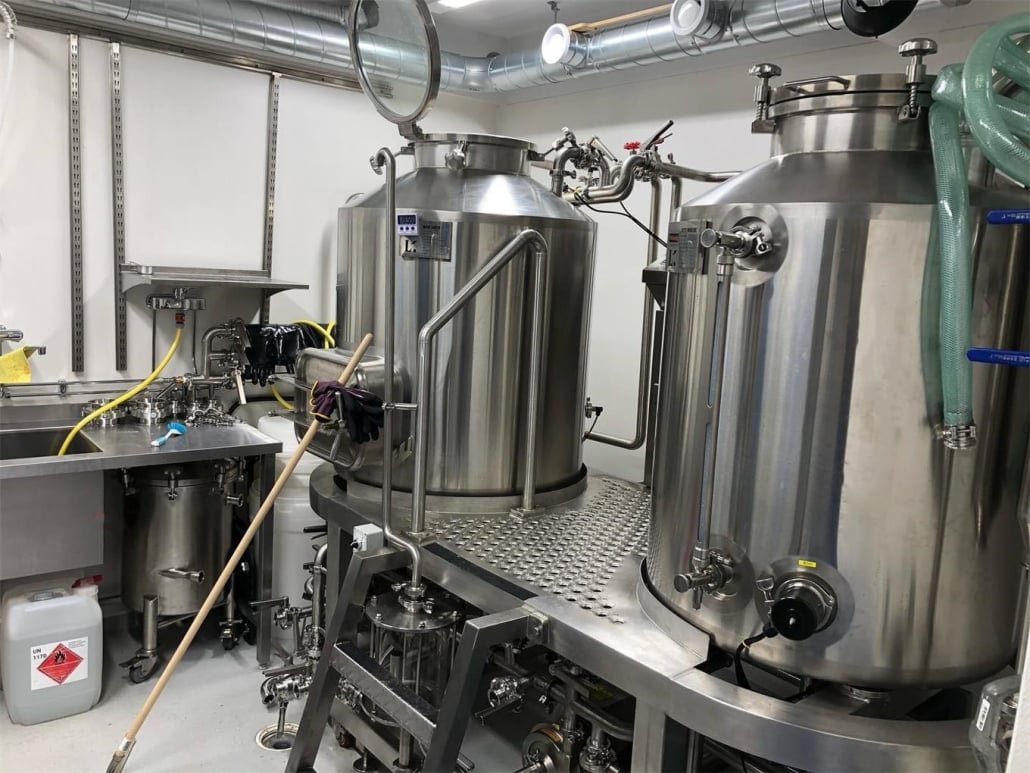
FAQs
Q: What is the best type of brewing system for a beginner?
A: For beginners, an extract brewing system is often the best choice. It simplifies the brewing process by using malt extract, which reduces the complexity and time required. Brew-in-a-Bag (BIAB) systems are also a good option for those wanting to try all-grain brewing without a large investment in equipment.
Q: How much space do I need for a home brewing system?
A: The space required depends on the size of the system. A small homebrew system can fit in a garage or basement, while larger setups may need a dedicated room. Ensure you have enough space for all equipment, ingredients, and a clean, dry area for storage.
Q: Can I customize my brewing system?
A: Yes, many suppliers offer customization options. You can add extra fermenters, advanced controls, and automation features to suit your brewing needs. Discuss your requirements with suppliers to find the best options.
Q: How much does a professional brewing system cost?
A: Professional brewing systems can range from $10,000 to over $100,000 depending on the capacity, level of automation, and additional features. It’s a significant investment, so it’s essential to choose a system that meets your production needs and budget.
Q: What maintenance does a brewing system require?
A: Regular cleaning and sanitizing are crucial to prevent contamination. Additionally, periodic checks for wear and tear, calibration of equipment, and following a maintenance schedule will help ensure your system operates smoothly and efficiently.
Share this entry
Interested in learning more about Brewing Systems including additional details and pricing information? Please use the form below to contact us!
YOLONG BREWERY EQUIPMENT FAQS
- Commercial Brewery / Craft Brewery / Microbrewery / Nanobrewery
- What is The Difference Between Craft Beer and Industrial Beer?
- The Bespoke Differences In Custom Brewing Systems
- Everything You Need to Know About Kettle Souring
- How to Choose Brewing Equipment for Your business?
- How To Choose The-Best Partner To Build Your Commercial Microbrewing System?
- Two Detection Sensors That You Need To Use In Your Brewhouse System
- Remote Control Applications in Brewing Equipment/How does it work?
- How To Clean Your Brand New Brewery Tanks?