Commercial Brewing System
Overview
A commercial brewing system is an essential piece of equipment for any brewery, whether it’s a small-scale craft operation or a large-scale industrial facility. These systems are designed to handle the entire brewing process, from mashing and lautering to boiling and fermenting. They come in various sizes and configurations to suit different production capacities and brewing styles. In this article, we’ll delve into the world of commercial brewing systems, exploring their components, types, brewing processes, and factors to consider when selecting and operating one.
Commercial Brewing System Components
Before we dive into the different types of commercial brewing systems, let’s understand the key components that make up these systems:
Component | Description |
---|---|
Mash Tun | A vessel where the milled grains are mixed with hot water, allowing the enzymes to convert the starches into fermentable sugars. |
Lauter Tun | A vessel where the mash is separated into the sweet wort (liquid) and the spent grains. |
Brew Kettle | A large kettle where the wort is boiled, and hops are added to provide bitterness, flavor, and aroma. |
Whirlpool | A vessel where the wort is separated from the trub (hop residue) after boiling. |
Fermentation Tanks | Vessels where the cooled wort is fermented by adding yeast, converting sugars into alcohol and CO2. |
Bright Beer Tanks | Tanks used for conditioning and carbonating the beer before packaging. |
These components work together in a well-orchestrated system to produce high-quality beer consistently.
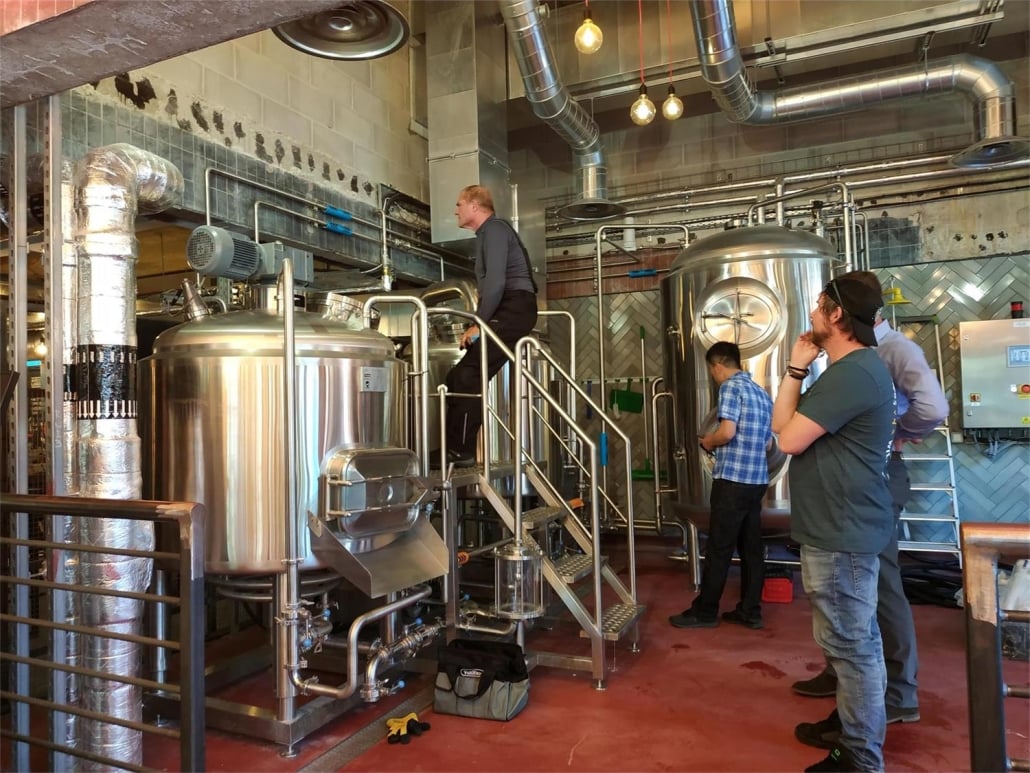
Types of Commercial Brewing Systems
Commercial brewing systems come in various configurations to cater to different production scales and brewing styles. Here are some of the most common types:
System Type | Description |
---|---|
Brewhouse | A complete system that includes the mash tun, lauter tun, brew kettle, and whirlpool. |
Craft Brewing System | Compact systems designed for small to medium-sized craft breweries, often with semi-automatic or fully automatic control systems. |
Micro Brewing System | Smaller systems ideal for nano or microbreweries, homebrewers scaling up, or pilot brewing operations. |
Pub Brewing System | Systems designed for on-site brewing at pubs or brewpubs, usually with a smaller footprint and lower capacity. |
Brewing Process with a Commercial System
The brewing process with a commercial system typically follows these steps:
- Milling: The malted grains are milled to crack the husks and expose the endosperm, preparing them for mashing.
- Mashing: The milled grains are mixed with hot water in the mash tun, allowing the enzymes to convert the starches into fermentable sugars.
- Lautering: The mash is transferred to the lauter tun, where the sweet wort is separated from the spent grains.
- Boiling: The wort is transferred to the brew kettle, where it is boiled, and hops are added at specific intervals to achieve the desired bitterness, flavor, and aroma.
- Whirlpooling: The wort is transferred to the whirlpool, where the trub (hop residue) is separated from the clear wort.
- Cooling: The wort is cooled rapidly to the desired fermentation temperature using a wort chiller or heat exchanger.
- Fermentation: The cooled wort is transferred to the fermentation tanks, where yeast is added to convert the sugars into alcohol and CO2.
- Conditioning and Packaging: After fermentation, the beer is transferred to bright beer tanks for conditioning and carbonation before being packaged into kegs, bottles, or cans.
Capacity, Spaces, Design, and Layout
Commercial brewing systems are available in various capacities to accommodate different production scales. Here’s a table that outlines some common capacity ranges and the corresponding brewery sizes:
Capacity Range (BBL/Batch) | Brewery Size |
---|---|
1-10 BBL | Nano/Microbrewery |
10-30 BBL | Small Craft Brewery |
30-100 BBL | Medium Craft Brewery |
100+ BBL | Large Craft/Regional Brewery |
When it comes to design and layout, several factors must be considered, such as the available space, production volume, and workflow efficiency. Many commercial brewing systems are modular, allowing for customization and future expansion. The layout should promote a smooth flow of materials and personnel, with proper access for cleaning, maintenance, and operations.
Customization and Automation
Breweries often require customized solutions to meet their specific needs and brewing styles. Many commercial brewing system manufacturers offer customization options, such as:
- Material selection (stainless steel, copper, etc.)
- Automation levels (manual, semi-automatic, or fully automatic)
- Insulation and jacketing options
- Unique vessel shapes or sizes
- Integration with existing equipment or infrastructure
Automation is becoming increasingly popular, as it can improve consistency, efficiency, and process control. Automated systems can handle tasks like mashing, lautering, wort transfer, and temperature control, reducing the need for manual intervention.
Commercial Brewing System Suppliers and Price Range
There are numerous suppliers of commercial brewing systems, ranging from small-scale manufacturers to large, established companies. Here’s a table that lists some popular suppliers and their approximate price ranges for different system sizes:
Supplier | Nano/Micro Systems | Small Craft Systems | Medium+ Craft Systems |
---|---|---|---|
Specific Mechanical Systems | $50,000 – $150,000 | $150,000 – $500,000 | $500,000+ |
Prospero | $50,000 – $150,000 | $150,000 – $500,000 | $500,000+ |
Brewmation | $50,000 – $150,000 | $150,000 – $500,000 | $500,000+ |
Psycho Brew | $50,000 – $150,000 | $150,000 – $500,000 | $500,000+ |
Quality Tank Solutions | $50,000 – $150,000 | $150,000 – $500,000 | $500,000+ |
It’s important to note that these prices are rough estimates and can vary significantly based on the specific configuration, automation level, and customization options.
Installation, Operation, and Maintenance
Installing a commercial brewing system is a complex process that often requires the assistance of professional installers and contractors. Here’s a table that outlines some key considerations for installation, operation, and maintenance:
Aspect | Considerations |
---|---|
Installation | – Site preparation (floor reinforcement, utilities, drainage, etc.) – Proper ventilation and access for maintenance – Integration with existing infrastructure (if applicable) – Compliance with local regulations and building codes |
Operation | – Comprehensive training for brewery personnel – Adherence to standard operating procedures – Proper cleaning and sanitation protocols – Process monitoring and quality control measures – Record-keeping and batch tracking |
Maintenance | – Regular cleaning and inspection schedules – Preventive maintenance programs – Spare parts inventory and availability – Service contracts or on-call technical support – Compliance with safety regulations |
Proper installation, operation, and maintenance are crucial for ensuring consistent beer quality, maximizing efficiency, and prolonging the lifespan of the brewing system.
Choosing the Right Supplier
Selecting the right supplier for your commercial brewing system is a critical decision that can impact the success of your brewery. Here are some key factors to consider when choosing a supplier:
Factor | Description |
---|---|
Reputation and Experience | Look for suppliers with a proven track record in the brewing industry and a strong reputation for quality and reliability. |
Product Range and Customization | Evaluate the supplier’s product range to ensure they can meet your specific requirements, including customization options if needed. |
Technical Support and Service | Consider the supplier’s technical support offerings, such as on-site service, remote support, and maintenance contracts. |
Lead Times and Delivery | Inquire about lead times and delivery schedules to ensure they align with your project timeline and production needs. |
Warranty and Guarantees | Review the supplier’s warranty and guarantees to understand the level of protection and support provided. |
Customer Reviews and References | Seek customer reviews and references to gauge the supplier’s performance and customer satisfaction levels. |
Pricing and Payment Terms | Evaluate the pricing structure and payment terms to ensure they fit within your budget and financial constraints. |
By carefully considering these factors, you can increase the chances of finding a reliable and trustworthy supplier that meets your brewery’s specific needs.
Pros and Cons of Commercial Brewing Systems
Like any investment, commercial brewing systems come with their own set of advantages and limitations. Here’s a table that outlines some of the key pros and cons:
Pros | Cons |
---|---|
Consistent beer quality and reproducibility | High initial investment cost |
Increased production capacity and efficiency | Significant space and utility requirements |
Automation and process control capabilities | Complexity in operation and maintenance |
Scalability for future growth | Potential need for specialized training and expertise |
Compliance with regulatory standards | Downtime and production disruptions during maintenance or repairs |
Improved safety and sanitation measures | Potential environmental impact (water usage, energy consumption, waste) |
It’s important to carefully weigh these pros and cons in the context of your brewery’s specific goals, resources, and operational requirements.
Advantages and Limitations of Different System Types
Each type of commercial brewing system comes with its own set of advantages and limitations. Here’s a table that compares the key advantages and limitations of the most common system types:
System Type | Advantages | Limitations |
---|---|---|
Brewhouse | – Complete brewing solution – High production capacity – Automation and process control options – Scalability for future growth | – High initial investment cost – Larger footprint and space requirements – Increased complexity and maintenance needs |
Craft Brewing System | – Compact and efficient design – Suitable for small to medium-sized breweries – Automation and semi-automatic options – Relatively lower investment cost | – Limited production capacity compared to larger systems – Potential scalability limitations for rapid growth – May require manual intervention in some processes |
Micro Brewing System | – Ideal for nano or microbreweries – Lower investment cost – Smaller footprint and space requirements – Suitable for pilot brewing or homebrew scaling | – Limited production capacity – Fewer automation and process control options – Potential scalability limitations for future growth |
Pub Brewing System | – On-site brewing for pubs or brewpubs – Smaller footprint and space requirements – Lower investment cost – Potential for increased customer engagement | – Limited production capacity – Fewer automation and process control options – Potential scalability limitations for future growth |
When selecting a commercial brewing system, it’s crucial to consider your brewery’s current and future production needs, available space, budget, and growth plans to find the system type that best aligns with your requirements.
FAQ
Question | Answer |
---|---|
What is the typical lifespan of a commercial brewing system? | With proper maintenance and care, a well-built commercial brewing system can last for 10-20 years or more. However, some components may need replacement over time. |
Can a commercial brewing system be expanded or upgraded? | Many commercial brewing systems are designed with modularity and scalability in mind, allowing for future expansion or upgrades to accommodate increased production demands. |
What are the typical utility requirements for a commercial brewing system? | Commercial brewing systems typically require access to utilities such as water, electricity, natural gas or steam, and proper drainage. The specific requirements will depend on the system size and configuration. |
How much space is needed for a commercial brewing system? | The required space depends on the system size and layout. As a general guide, a small craft brewing system may require 1,000-2,000 square feet, while a larger system could need 5,000 square feet or more. |
Can a commercial brewing system be relocated or moved? | While it’s possible to relocate or move a commercial brewing system, it’s a complex and often costly process that may require disassembly, transportation, and reinstallation by professionals. |
What are the typical maintenance requirements for a commercial brewing system? | Regular cleaning, inspection, and preventive maintenance are essential. This may include tasks like cleaning tanks, replacing gaskets and seals, lubricating moving parts, and calibrating instruments. |
Can a commercial brewing system be automated or controlled remotely? | Yes, many modern commercial brewing systems offer various levels of automation and remote control capabilities, allowing for improved efficiency, consistency, and process monitoring. |
How long does it take to install a commercial brewing system? | Installation times can vary greatly depending on the system size, complexity, and site preparation requirements. Typical installations may take several weeks to several months. |
What are the main factors that affect the cost of a commercial brewing system? | Key cost factors include system size and capacity, level of automation, customization options, brand reputation, materials used, and any additional equipment or infrastructure required. |
Can a commercial brewing system be leased or financed? | Yes, many suppliers offer leasing or financing options for commercial brewing systems, which can help spread out the initial investment cost over a longer period. |