bright brewery tank
Bright Brewery Tank Overview
A bright brewery tank, also known as a bright beer tank (BBT), is a specialized vessel used in the brewing industry for storing and conditioning beer after fermentation. It plays a crucial role in the final stages of the brewing process, ensuring the beer is properly carbonated, clarified, and ready for packaging. These tanks are designed to maintain the beer in a controlled environment, free from exposure to oxygen, light, and other contaminants that could compromise the flavor and quality of the beer.
The primary function of a bright brewery tank is to provide a suitable environment for the beer to undergo a natural conditioning process, often referred to as “bright beer tank conditioning.” During this process, the beer is allowed to mature, develop its desired flavor profile, and achieve the desired level of carbonation. The tanks are equipped with specialized features that facilitate this conditioning process, such as temperature control, pressure regulation, and racking capabilities.
Brewing Process and the Role of Bright Brewery Tanks
The brewing process involves several stages, each contributing to the final product’s taste, aroma, and quality. Once the fermentation process is complete, the beer is transferred from the fermentation tank to the bright brewery tank. This transition marks the beginning of the conditioning phase, where the beer underges several transformations before it is ready for packaging and distribution.
During the bright beer tank conditioning phase, the following processes occur:
- Clarification: The beer is allowed to rest and clarify, allowing any remaining yeast and other particulates to settle at the bottom of the tank. This process results in a clear, brilliant beer.
- Carbonation: Precise levels of carbon dioxide are introduced into the beer, either through natural carbonation (by allowing the remaining yeast to produce CO2) or through forced carbonation (by injecting CO2 directly into the tank).
- Maturation: The beer is held in the bright brewery tank for a specific period, allowing its flavors to develop and mature. This aging process can range from a few days to several weeks, depending on the beer style and desired characteristics.
- Stabilization: Certain additives, such as silica gel or polyvinylpolypyrrolidone (PVPP), may be introduced to help stabilize the beer and improve its shelf life.
- Filtration: In some cases, the beer may undergo a final filtration process to remove any remaining particulates, ensuring a crystal-clear final product.
Once the conditioning process is complete, the beer is ready for packaging, whether in kegs, bottles, or cans, and distribution to the market.
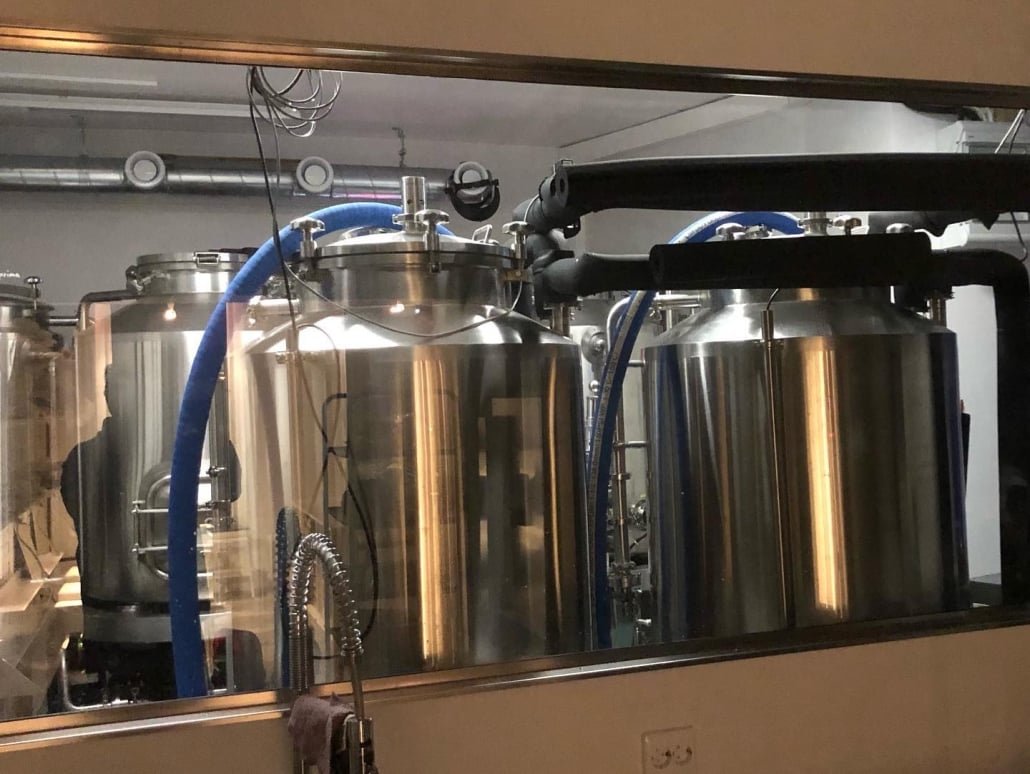
Types of Bright Brewery Tanks
Bright brewery tanks come in various types, each designed to cater to specific brewing needs and beer styles. The following table outlines some common types of bright brewery tanks:
Tank Type | Description |
---|---|
Unitank/Cylindroconical Tank | A popular choice for smaller breweries, these tanks combine fermentation and bright beer conditioning in a single vessel, offering a space-saving solution. |
Horizontal Bright Tank | Cylindrical tanks designed for larger breweries, with a horizontal orientation that maximizes floor space utilization. |
Vertical Bright Tank | Upright cylindrical tanks, often preferred for their smaller footprint and ease of cleaning. |
Jacketed Bright Tank | Tanks with an outer jacket that allows for precise temperature control during conditioning. |
Pressure Bright Tank | Tanks designed to withstand higher pressures, suitable for forced carbonation and counter-pressure filling processes. |
Features of Bright Brewery Tanks
Bright brewery tanks are engineered to meet the specific requirements of the brewing industry, incorporating various features to ensure optimal beer conditioning and quality control. Here are some common features found in these tanks:
- Temperature Control: Precise temperature regulation is essential for proper conditioning and flavor development. Bright brewery tanks often feature jacketed walls or internal cooling/heating coils to maintain the desired temperature range.
- Pressure Regulation: Controlling the pressure inside the tank is crucial for carbonation and preventing oxidation. Tanks are equipped with pressure relief valves, pressure gauges, and gas injection/purging systems.
- Racking Capabilities: Bright brewery tanks typically have racking arms or racking ports that allow for the transfer of beer into or out of the tank without introducing oxygen or contaminants.
- Sight Glass: A sight glass or level indicator provides visual monitoring of the beer level within the tank.
- Sampling Ports: Ports or valves allow for sampling the beer during the conditioning process, enabling quality control checks and adjustments as needed.
- Cleaning and Sanitation Systems: Proper cleaning and sanitation are essential in the brewing industry. Many bright brewery tanks feature integrated clean-in-place (CIP) systems or are designed for easy manual cleaning.
- Insulation: Insulated tank walls help maintain consistent temperatures and minimize energy loss during the conditioning process.
- Agitation Systems: Some tanks incorporate agitation systems, such as rocking mechanisms or internal rousers, to aid in clarification and carbonation.
- Automation and Control Systems: Modern bright brewery tanks often integrate with automated control systems, allowing for precise monitoring and adjustment of various parameters, such as temperature, pressure, and timing.
By incorporating these features, bright brewery tanks provide brewers with the necessary tools to ensure consistent beer quality, efficient conditioning, and adherence to industry standards.
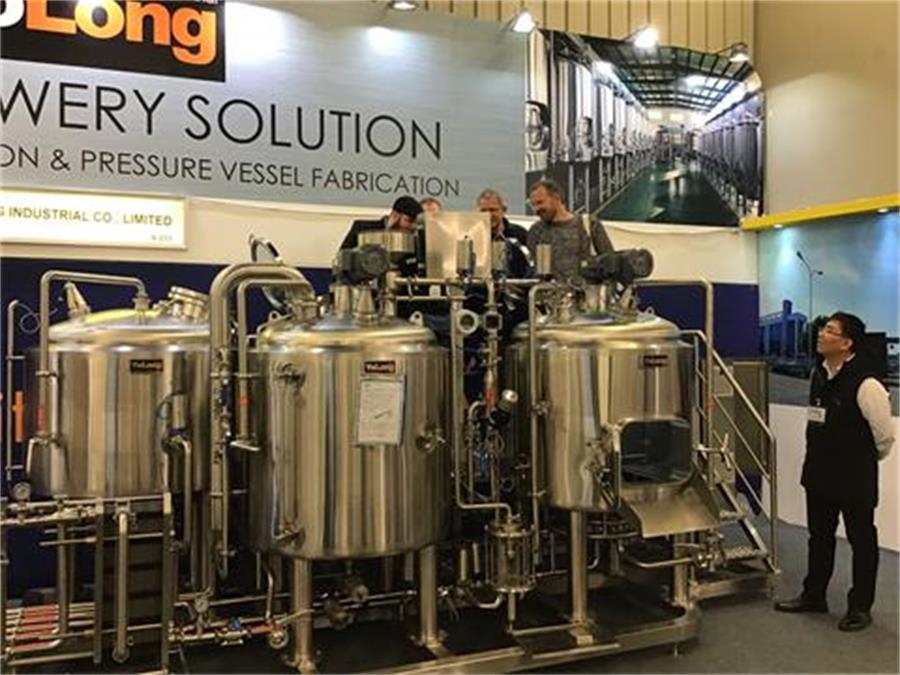
Capacity, Spaces, Design, and Layout Considerations
When selecting and installing bright brewery tanks, several factors must be considered to ensure optimal performance and efficiency. The capacity, available space, design, and layout of the tanks play a crucial role in the overall brewing operation.
Capacity
The capacity of a bright brewery tank is a critical consideration, as it directly impacts the brewery’s production volume and ability to meet demand. Tanks are available in a range of sizes, from small-scale tanks for microbreweries to massive tanks for large-scale commercial operations. The capacity is typically measured in liters, gallons, or hectoliters, and it’s essential to choose a tank size that aligns with the brewery’s current and projected production needs.
Spaces and Layout
The available space in the brewery is a significant factor in determining the type and layout of bright brewery tanks. Horizontal tanks generally require more floor space, while vertical tanks have a smaller footprint but may require additional ceiling height. Careful planning is necessary to ensure proper tank placement, access for maintenance and cleaning, and efficient workflow.
Considerations for tank layout include:
- Adequate clearance for tank installation, maintenance, and cleaning
- Proper spacing between tanks for access and ventilation
- Efficient workflow for beer transfer and packaging
- Integration with other brewery equipment and systems
- Compliance with local building codes and regulations
Design and Customization
Bright brewery tanks can be customized to meet specific brewing requirements and preferences. Manufacturers often offer various design options, such as material selection (e.g., stainless steel, copper, or other food-grade materials), insulation types, and specialized features like dedicated sampling ports or custom racking systems.
Some common design considerations include:
- Tank shape (cylindrical, cylindroconical, or conical)
- Tank orientation (horizontal or vertical)
- Insulation thickness and material
- Integrated cooling or heating systems
- Racking system design (arms, ports, or integrated piping)
- Automation and control system integration
- Aesthetic finishes and branding elements
Customization allows breweries to optimize their bright brewery tanks for specific beer styles, production volumes, and operational requirements, ensuring efficient and streamlined conditioning processes.
Bright Brewery Tank Suppliers and Price Ranges
The brewing equipment market offers a wide range of bright brewery tank suppliers, catering to breweries of various sizes and budgets. When selecting a supplier, it’s essential to consider factors such as reputation, quality, customer support, and pricing.
Here’s a table showcasing some of the prominent bright brewery tank suppliers and their approximate price ranges:
Supplier | Price Range (USD) | Notes |
---|---|---|
Alfa Laval | $10,000 – $100,000+ | Renowned global supplier of brewing equipment, offering high-quality stainless steel tanks. |
Criveller | $5,000 – $50,000+ | Italian manufacturer with a focus on customized brewing solutions. |
Della Toffola | $8,000 – $80,000+ | Reputable Italian supplier with a wide range of tank sizes and configurations. |
GEA | $15,000 – $150,000+ | Global leader in brewing technology, offering advanced automation and control systems. |
Hypro | $4,000 – $40,000+ | Affordable options for small to medium-sized breweries. |
Meura | $8,000 – $70,000+ | Belgian manufacturer known for quality and innovative designs. |
Newlands Systems | $6,000 – $60,000+ | Specializes in compact and efficient brewery equipment. |
Pentair Haffmans | $12,000 – $120,000+ | Premium supplier with expertise in carbonation and clarification systems. |
Psycho Brew | $3,000 – $30,000+ | Cost-effective solutions for small breweries and homebrewing enthusiasts. |
Ss Brewtech | $5,000 – $50,000+ | Focused on high-quality stainless steel tanks and brewing equipment. |
Please note that these price ranges are approximate and can vary depending on factors such as tank size, features, customization, and geographic location. It’s advisable to request quotes from multiple suppliers and compare offerings to find the best fit for your brewery’s needs and budget.
Installation, Operation, and Maintenance
Proper installation, operation, and maintenance are crucial for ensuring the longevity and optimal performance of bright brewery tanks. These aspects require careful planning and execution to maintain the tanks’ integrity and ensure consistent beer quality.
Installation
The installation process for bright brewery tanks involves several critical steps:
- Site Preparation: Ensuring the brewery has adequate space, proper flooring, utilities (water, electricity, and gas if needed), and access for tank installation.
- Tank Positioning: Carefully positioning the tank in the designated area, considering factors such as clearance, access for maintenance, and integration with other brewery equipment.
- Piping and Connections: Connecting the tank to the necessary piping systems for liquid transfer, gas lines, and cleaning/sanitation systems.
- Electrical and Control Systems: Installing and integrating any electrical components, control systems, and automation equipment.
- Testing and Commissioning: Conducting thorough testing and commissioning to ensure proper operation, leak detection, and compliance with safety regulations.
Proper installation is crucial for the tank’s functionality, safety, and adherence to local building codes and regulations.
Operation
Operating a bright brewery tank requires trained personnel and adherence to established procedures. Key aspects of tank operation include:
- Temperature Control: Maintaining the appropriate temperature range for the specific beer style and conditioning process.
- Pressure Regulation: Controlling the tank’s internal pressure for carbonation, transfer, and packaging processes.
- Monitoring and Adjustments: Regularly monitoring tank parameters (temperature, pressure, carbonation levels, etc.) and making necessary adjustments to ensure optimal conditioning.
- Sampling and Quality Control: Conducting regular sampling and quality control checks to monitor the beer’s progress and make any necessary adjustments.
- Cleaning and Sanitation: Implementing rigorous cleaning and sanitation procedures to maintain the tank’s hygiene and prevent contamination.
Proper operation is essential for producing high-quality beer consistently and ensuring the tank’s longevity.
Maintenance
Regular maintenance is vital for ensuring the bright brewery tank’s continued performance and extending its service life. Maintenance activities may include:
- Inspections: Conducting regular inspections to check for signs of wear, corrosion, or damage to the tank and its components.
- Preventive Maintenance: Performing scheduled maintenance tasks, such as lubricating moving parts, replacing gaskets or seals, and checking for proper operation of valves and controls.
- Cleaning and Sanitation: Implementing thorough cleaning and sanitation protocols, including chemical cleaning and sterilization procedures, to maintain the tank’s hygiene.
- Repair and Replacement: Addressing any identified issues promptly by repairing or replacing worn or damaged components.
- Record Keeping: Maintaining detailed records of maintenance activities, inspections, and any issues encountered for future reference and troubleshooting.
By adhering to proper installation, operation, and maintenance procedures, breweries can ensure the longevity and optimal performance of their bright brewery tanks, contributing to consistent beer quality and operational efficiency.
Choosing the Right Bright Brewery Tank Supplier
Selecting the right bright brewery tank supplier is crucial for ensuring the success of your brewing operation. With a wide range of suppliers available in the market, it’s essential to consider several key factors to make an informed decision.
Here are some important considerations when choosing a bright brewery tank supplier:
Consideration | Description |
---|---|
Reputation and Experience | Look for suppliers with a proven track record in the brewing industry. Reputable suppliers with extensive experience are more likely to offer high-quality products and reliable after-sales support. |
Product Quality and Durability | Evaluate the materials used, construction methods, and overall quality of the tanks offered by the supplier. High-quality tanks ensure longevity and minimize the risk of contamination or equipment failure. |
Customization Options | Assess the supplier’s ability to provide customized solutions tailored to your brewery’s specific needs, such as unique tank configurations, specialized features, or integrated control systems. |
Technical Support and Service | Consider the level of technical support and service offered by the supplier, including installation assistance, training, maintenance support, and prompt response times for any issues that may arise. |
Delivery and Lead Times | Evaluate the supplier’s delivery capabilities and lead times to ensure timely delivery of your tanks, minimizing potential production delays or disruptions. |
Warranty and Guarantees | Review the warranty and guarantee terms offered by the supplier, providing assurance of product quality and protection against manufacturing defects. |
Pricing and Value | Compare pricing across different suppliers, considering not only the upfront costs but also the long-term value and potential savings from factors like energy efficiency, low maintenance requirements, and extended service life. |
Local or Regional Presence | Working with a supplier with a local or regional presence can be advantageous, as they may have a better understanding of local regulations, customs, and logistical considerations. |
Certifications and Compliance | Ensure the supplier adheres to relevant industry standards, certifications, and regulatory compliance requirements, such as food-grade material certification and adherence to sanitation guidelines. |
By carefully evaluating these factors, you can choose a bright brewery tank supplier that aligns with your brewery’s requirements, budget, and overall business objectives, ensuring a successful and efficient brewing operation.
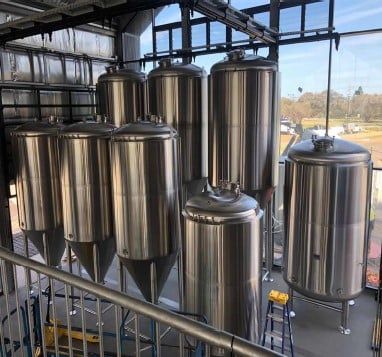
Pros and Cons of Bright Brewery Tanks
While bright brewery tanks are essential for the conditioning and packaging of beer, it’s important to understand their advantages and limitations to make informed decisions about their use and maintenance.
Pros of Bright Brewery Tanks
- Controlled Environment: Bright brewery tanks provide a controlled environment for beer conditioning, protecting the beer from exposure to oxygen, light, and other contaminants that could adversely affect its flavor and quality.
- Efficient Conditioning: The specialized features of bright brewery tanks, such as temperature control, pressure regulation, and racking capabilities, facilitate efficient and consistent conditioning processes, ensuring optimal beer quality.
- Extended Shelf Life: Proper conditioning in bright brewery tanks can extend the shelf life of beer, allowing for longer storage and distribution periods without compromising quality.
- Versatility: Different types of bright brewery tanks are available to accommodate various beer styles, production volumes, and brewery sizes, providing versatility in brewing operations.
- Automation and Control: Many modern bright brewery tanks are equipped with advanced automation and control systems, enabling precise monitoring and adjustment of critical parameters, improving consistency and reducing the risk of human error.
- Scalability: As breweries grow and expand their operations, bright brewery tanks can be easily scaled up or added to accommodate increased production volumes.
Cons of Bright Brewery Tanks
- Initial Investment Cost: Bright brewery tanks can represent a significant capital investment, particularly for larger or more advanced systems, which may be a barrier for some smaller breweries or startups.
- Maintenance and Cleaning Requirements: Proper maintenance and cleaning of bright brewery tanks are essential to ensure their longevity and prevent contamination. These processes can be time-consuming and labor-intensive, adding to operational costs.
- Space Requirements: Depending on their size and configuration, bright brewery tanks can occupy substantial floor space, which may be a challenge in breweries with limited area availability.
- Energy Consumption: Temperature control and other features of bright brewery tanks can contribute to increased energy consumption, potentially impacting operational costs and environmental footprint.
- Potential for Equipment Failures: Like any complex equipment, bright brewery tanks are susceptible to potential failures, such as leaks, malfunctions, or damage, which can disrupt production and require costly repairs or replacements.
- Training and Expertise: Operating and maintaining bright brewery tanks effectively requires specialized training and expertise, which may necessitate additional staff or training expenses for breweries.
By carefully weighing these pros and cons, breweries can make informed decisions about the implementation and management of bright brewery tanks, balancing the benefits of consistent beer quality and efficient conditioning against the associated costs and operational considerations.
FAQ
Q: What is the typical capacity range for bright brewery tanks? A: Bright brewery tanks are available in a wide range of capacities, from small tanks for microbreweries (e.g., 100-500 liters) to large-scale tanks for commercial operations (e.g., 50,000+ liters or more).
Q: Can bright brewery tanks be used for fermentation? A: While some unitank or cylindroconical tanks can be used for both fermentation and conditioning, dedicated bright brewery tanks are primarily designed for the conditioning stage after fermentation is complete.
Q: What materials are commonly used for bright brewery tanks? A: Stainless steel is the most common material used for bright brewery tanks due to its durability, corrosion resistance, and ease of cleaning. Some tanks may also incorporate other food-grade materials like copper or specialized coatings.
Q: How often do bright brewery tanks need to be cleaned and sanitized? A: The frequency of cleaning and sanitizing bright brewery tanks can vary depending on usage and brewery protocols, but it’s generally recommended to clean and sanitize tanks after every use or batch to prevent contamination and maintain beer quality.
Q: Can bright brewery tanks be customized to specific brewery needs? A: Yes, many manufacturers offer customization options for bright brewery tanks, such as unique tank configurations, specialized features (e.g., dedicated sampling ports, custom racking systems), and integration with automation and control systems.
Q: What are the typical maintenance requirements for bright brewery tanks? A: Regular maintenance for bright brewery tanks includes inspections for wear and corrosion, preventive maintenance (e.g., lubricating moving parts, replacing gaskets/seals), cleaning and sanitation protocols, and prompt repair or replacement of any worn or damaged components.
Share this entry
Interested in learning more about Brewing Systems including additional details and pricing information? Please use the form below to contact us!
YOLONG BREWERY EQUIPMENT FAQS
- Commercial Brewery / Craft Brewery / Microbrewery / Nanobrewery
- What is The Difference Between Craft Beer and Industrial Beer?
- The Bespoke Differences In Custom Brewing Systems
- Everything You Need to Know About Kettle Souring
- How to Choose Brewing Equipment for Your business?
- How To Choose The-Best Partner To Build Your Commercial Microbrewing System?
- Two Detection Sensors That You Need To Use In Your Brewhouse System
- Remote Control Applications in Brewing Equipment/How does it work?
- How To Clean Your Brand New Brewery Tanks?