How much does brewery equipment cost
Overview of Brewery Equipment Costs
Starting a brewery is an exciting venture, but one of the biggest challenges is understanding the cost of brewery equipment. Whether you are setting up a small craft brewery or a large commercial operation, the investment can range significantly based on size, scale, and customization. From brewhouses to fermentation tanks, cooling systems to packaging lines, every piece of equipment contributes to the final price tag.
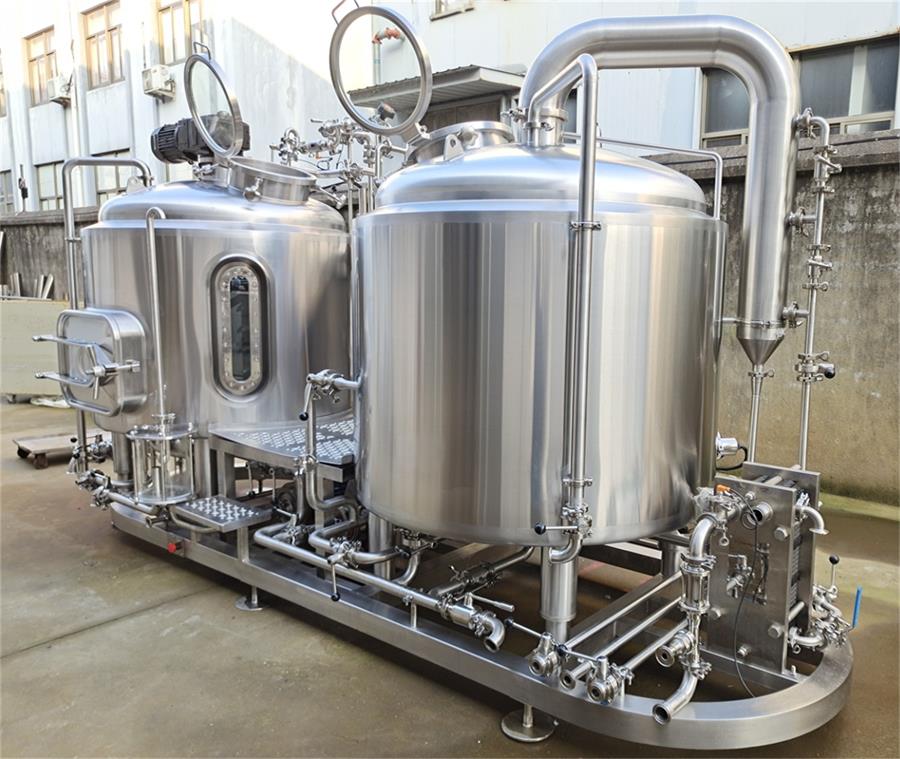
Factors Affecting the Cost of Brewing Equipment
Several key factors influence the price of brewing equipment. Understanding these factors can help you make an informed decision and manage your budget effectively.
- Brewery Scale and Production Volume – Larger breweries require bigger and more complex equipment, driving up costs.
- Material and Build Quality – Stainless steel is the industry standard due to its durability and hygiene, but higher grades and thicker materials increase the price.
- Automation Level – Fully automated brewing systems cost significantly more than semi-automatic or manual setups.
- Brand and Manufacturer – Well-known brands often charge a premium due to reputation and reliability.
- Customization Requirements – Custom-built systems tailored to unique brewing styles and batch sizes cost more than standard models.
- Import and Shipping Costs – Sourcing equipment from international manufacturers may involve high freight charges, import taxes, and customs fees.
- Additional Accessories – Pumps, hoses, temperature controllers, and filtration systems add to the total cost.
Costs of Brewing Equipment for Different Scales
Brewery equipment costs vary widely depending on the size and scope of the brewing operation. Here’s an estimated breakdown:
Nano and Microbreweries (1-10 BBL)
- Estimated Cost: $50,000 – $250,000
- Ideal for: Startups, homebrewers going commercial, small taprooms
- Equipment Includes: Small brewhouse, fermenters, basic filtration, manual kegging
- Pros: Low startup costs, easier to manage, good for experimenting with recipes
- Cons: Limited production capacity, higher cost per unit of beer
Mid-Sized Craft Breweries (10-50 BBL)
- Estimated Cost: $250,000 – $1,000,000
- Ideal for: Established microbreweries expanding production
- Equipment Includes: Larger brewhouse, glycol chilling system, automated kegging/bottling, better filtration
- Pros: Increased efficiency, scalable production
- Cons: Higher initial investment, requires more space
Large Commercial Breweries (50+ BBL)
- Estimated Cost: $1,000,000 – $10,000,000+
- Ideal for: High-volume production and distribution
- Equipment Includes: High-capacity brewhouse, extensive storage tanks, advanced automation, sophisticated packaging
- Pros: Lower cost per unit of beer, mass production capabilities
- Cons: Significant upfront cost, requires large facilities and skilled labor
Installation and Transportation of Brewing Equipment
The cost of setting up brewing equipment is not just about purchasing; installation and transportation are major expenses too.
- Nano and Microbreweries: Simple installation, may only require a local electrician and plumber. Costs range from $5,000 – $20,000.
- Mid-Sized Breweries: Needs professional setup, glycol cooling installation, and precise calibration. Expect $20,000 – $100,000.
- Large Breweries: Requires full-scale industrial installation, including floor reinforcement and specialized labor. Costs exceed $100,000.
Shipping fees depend on the equipment’s weight, size, and distance. Domestic purchases may cost a few thousand dollars, while international shipping can add tens of thousands in customs and freight charges.
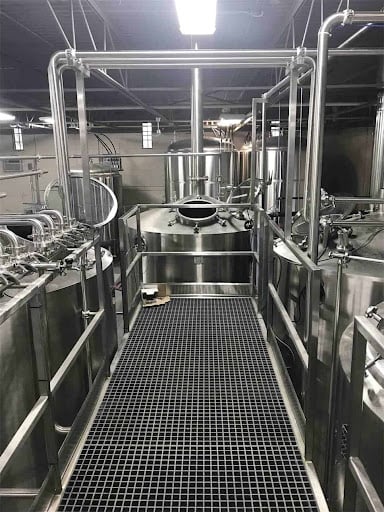
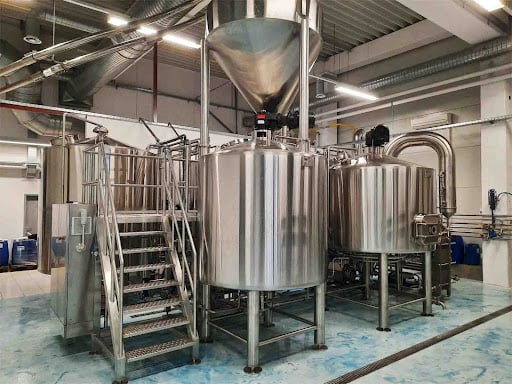
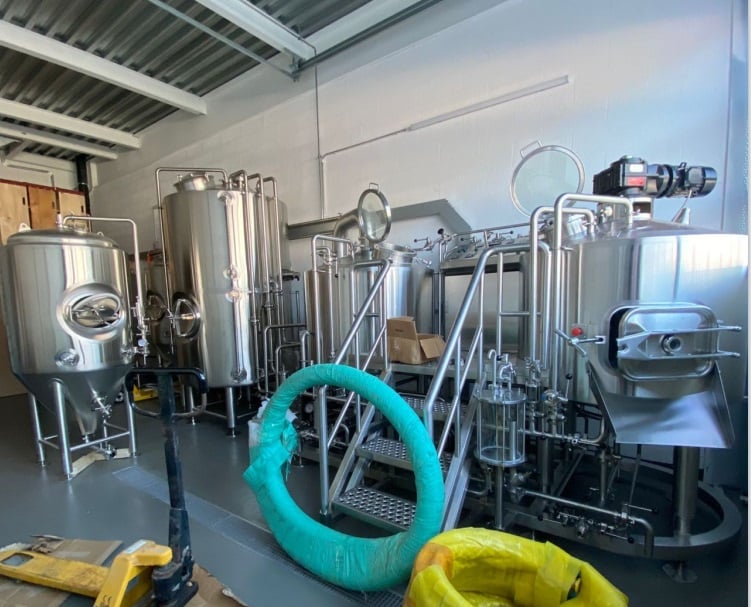
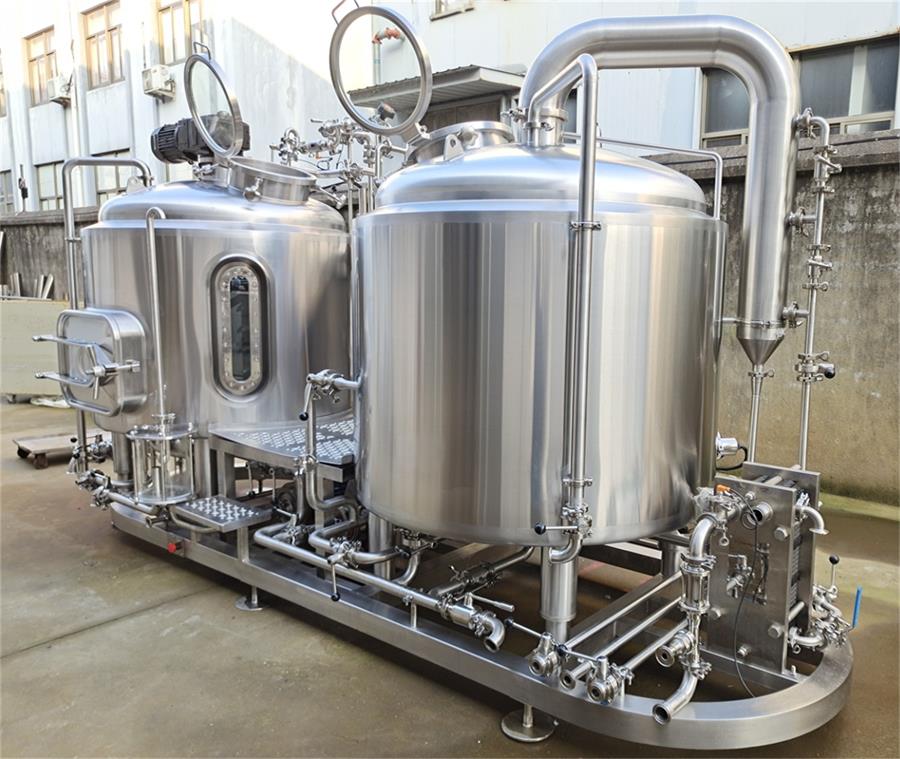
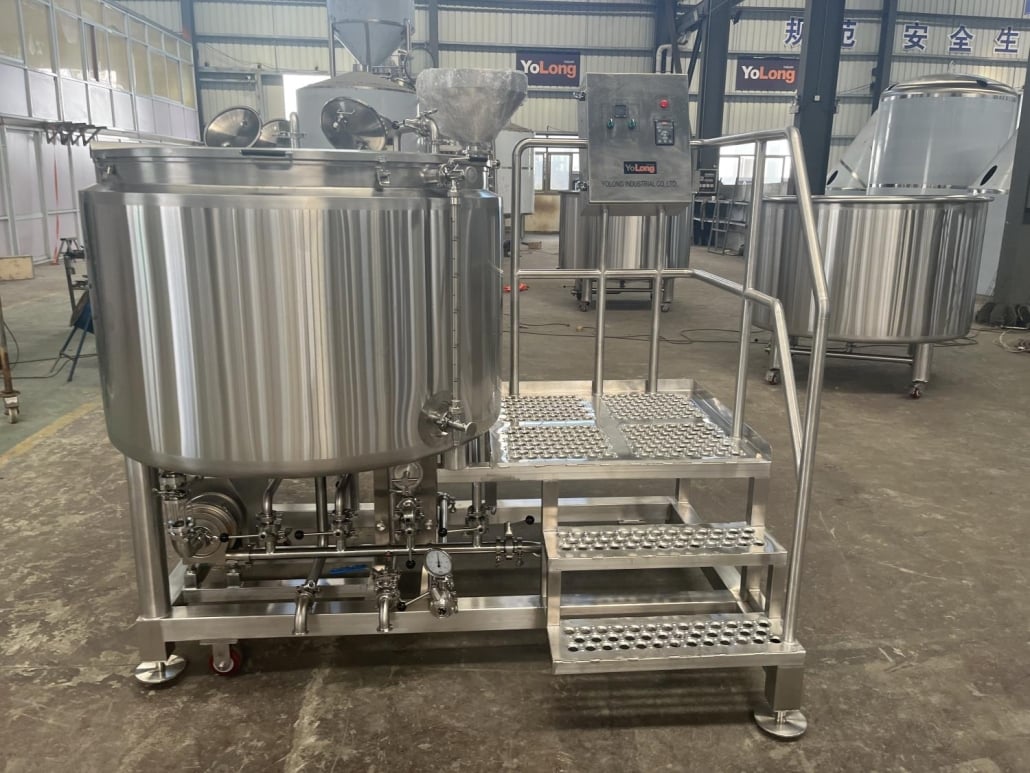
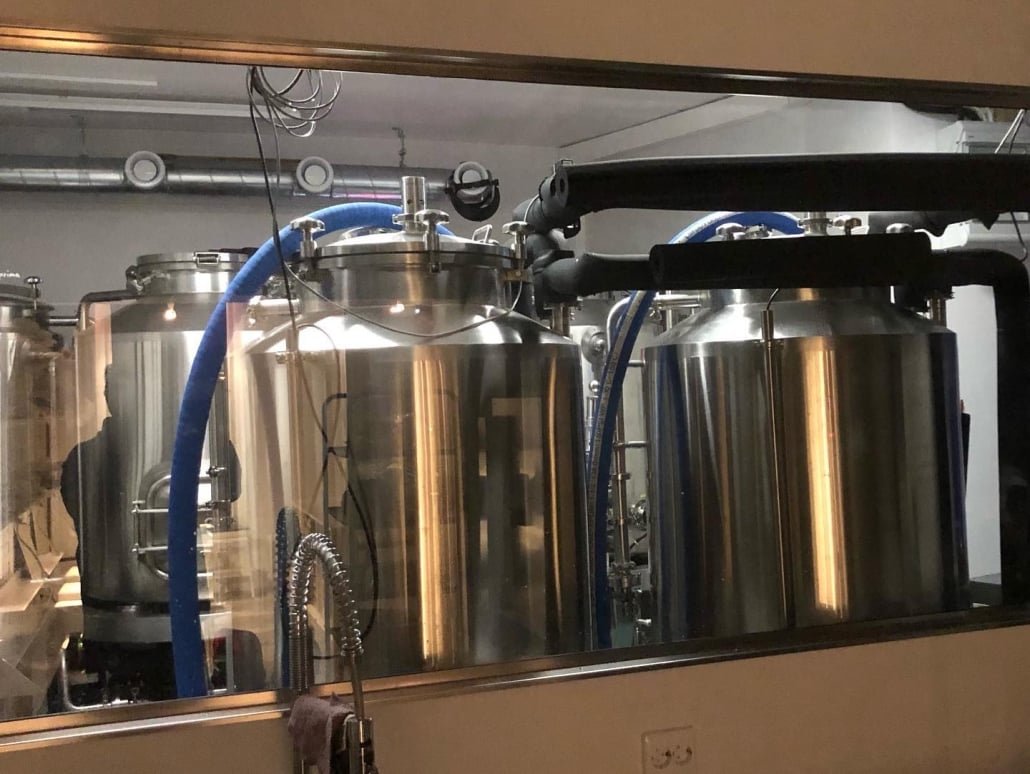
Maintenance and Repair of Brewing Equipment
Equipment Type | Common Maintenance Tasks | Estimated Annual Cost |
---|---|---|
Brewhouse | Cleaning, pump servicing, checking heating elements | $2,000 – $10,000 |
Fermentation Tanks | Sanitization, valve replacement, cooling system check | $1,500 – $7,000 |
Cooling System | Glycol maintenance, compressor servicing | $3,000 – $15,000 |
Packaging Line | Conveyor lubrication, seal replacement, machine calibration | $5,000 – $25,000 |
How to Choose Suitable Brewing Equipment
Consideration | Explanation |
---|---|
Production Goals | Define how much beer you plan to produce per year. |
Budget | Set realistic financial limits including installation and maintenance. |
Space Availability | Ensure your facility can accommodate the required tanks and utilities. |
Automation Level | Decide between manual, semi-automatic, and fully automated systems. |
Expansion Plans | Choose equipment that allows for future growth without excessive replacement costs. |
How to Save on Brewery Equipment Costs
- Buy Used Equipment: Many breweries sell high-quality used tanks and brewhouses at a fraction of the original price.
- Negotiate with Suppliers: Always ask for discounts, especially when purchasing in bulk.
- Consider Modular Systems: Some manufacturers offer modular equipment that can expand as your business grows.
- Optimize Energy Efficiency: Invest in energy-efficient boilers and cooling systems to save on operational costs.
- Lease Instead of Buying: Equipment leasing can reduce initial capital investment and provide flexibility.
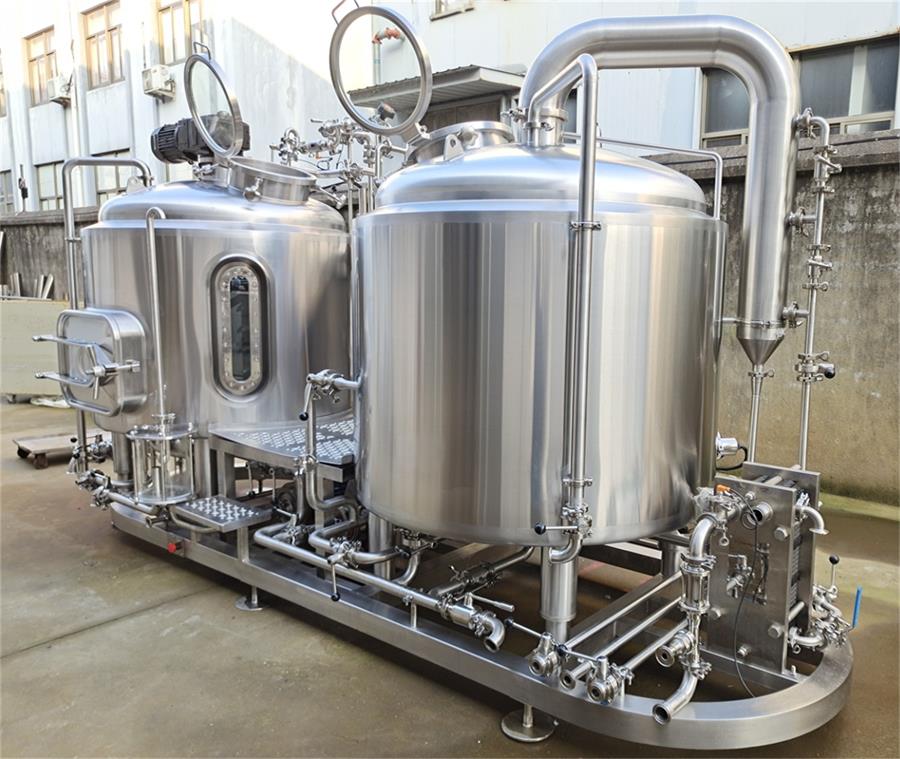
FAQ
Question | Answer |
---|---|
How much does it cost to start a brewery? | Costs vary widely from $50,000 for a nano-brewery to over $10 million for a commercial facility. |
What is the most expensive brewing equipment? | The brewhouse and fermentation tanks typically represent the largest investment. |
Can I buy used brewery equipment? | Yes! Many breweries sell quality used equipment at lower prices, helping reduce startup costs. |
How much space do I need for a brewery? | A nano-brewery may need 500-1,000 sq. ft., while a large commercial brewery could require 10,000+ sq. ft. |
How can I reduce equipment costs? | Buy used, negotiate deals, lease equipment, and opt for energy-efficient solutions. |