How to Set Up a Beer Manufacturing Plant
Beer is one of the oldest and most beloved beverages in the world, with a rich history dating back thousands of years. Today, beer production has evolved into a massive industry, ranging from small craft breweries to large-scale commercial plants. Setting up a beer manufacturing plant requires a thorough understanding of brewing processes, equipment, investment requirements, legal compliance, and distribution strategies.
Large Commercial Breweries vs. Craft Breweries
Beer manufacturing broadly falls into two categories: large commercial breweries and craft breweries.
Large Commercial Breweries
These breweries produce beer on a massive scale, often exceeding millions of barrels annually. They prioritize efficiency, consistency, and cost-effectiveness. Large commercial breweries often have state-of-the-art equipment and rely on automated systems for brewing, bottling, and packaging. Major brands such as Budweiser, Heineken, and Coors operate on this scale.
Craft Breweries
Craft breweries, on the other hand, focus on small-batch production with unique flavors and traditional brewing techniques. They emphasize quality and creativity over mass production. Craft breweries typically produce less than 6 million barrels per year and tend to have a strong local or niche market appeal. Examples include Sierra Nevada, Stone Brewing, and Dogfish Head.
Each model has its pros and cons. Large breweries benefit from economies of scale but lack the flexibility of craft brewers, who can quickly adapt to consumer trends and experiment with new flavors.
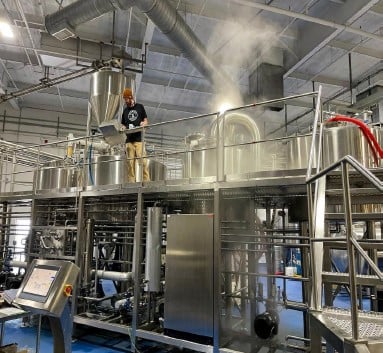
The Beer Production Process
Beer manufacturing follows a systematic process that transforms raw ingredients into the final product. The key steps include:
- Malting – Barley grains are soaked, germinated, and dried to develop fermentable sugars.
- Mashing – The malted barley is mixed with hot water to extract sugars, creating a sweet liquid known as wort.
- Boiling – The wort is boiled, and hops are added for bitterness and aroma.
- Fermentation – Yeast is introduced to convert sugars into alcohol, a process that can take several days to weeks.
- Conditioning – The beer is aged to enhance flavor and carbonation.
- Filtration & Packaging – The final product is filtered, carbonated (if necessary), and packaged in bottles, cans, or kegs.
Each stage requires precise control to maintain quality and consistency.
Essential Equipment for a Beer Manufacturing Plant
Setting up a brewery requires a variety of specialized equipment. Here are the most essential components:
- Milling System – Crushes malted barley to extract sugars.
- Mash Tun – Mixes malt with hot water for sugar extraction.
- Lauter Tun – Separates solid grains from the liquid wort.
- Brew Kettle – Boils the wort and integrates hops.
- Fermentation Tanks – House the fermentation process where yeast converts sugars into alcohol.
- Conditioning Tanks – Used for aging and refining the beer’s taste.
- Filtration System – Removes unwanted particles and ensures clarity.
- Cooling System – Regulates temperature during brewing and fermentation.
- Packaging Line – Includes bottling, canning, and kegging machines.
Costs & Investment: How Much Does It Take to Start?
The cost of setting up a beer manufacturing plant varies based on size, location, and scale of production. Here’s a breakdown:
Expense Category | Small-Scale Craft Brewery ($) | Mid-Size Brewery ($) | Large Commercial Brewery ($) |
---|---|---|---|
Equipment | 100,000 – 500,000 | 500,000 – 2M | 5M – 20M |
Facility & Setup | 50,000 – 300,000 | 300,000 – 1M | 2M – 10M |
Licensing & Permits | 10,000 – 50,000 | 50,000 – 200,000 | 500,000 – 1M |
Raw Materials | 10,000 – 50,000 | 50,000 – 200,000 | 500,000 – 2M |
Marketing & Distribution | 20,000 – 100,000 | 100,000 – 500,000 | 1M – 5M |
Total Estimated Cost | 200,000 – 1M | 1M – 5M | 10M – 50M |
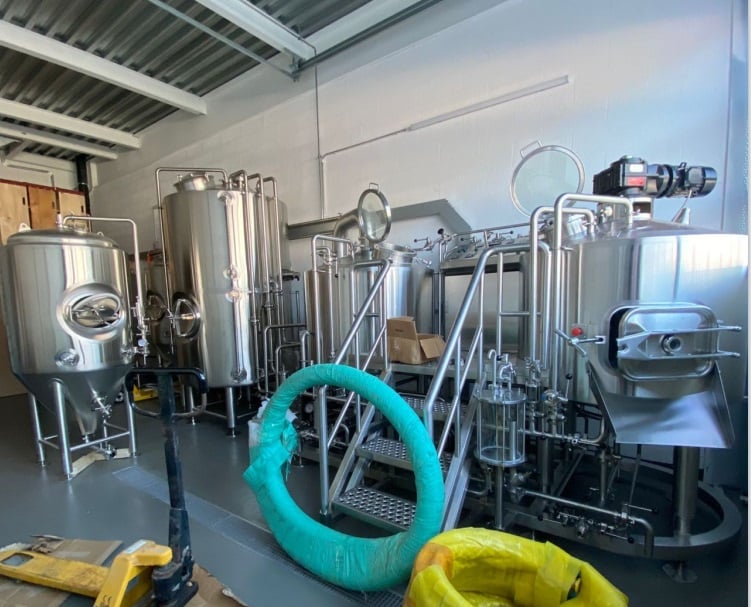
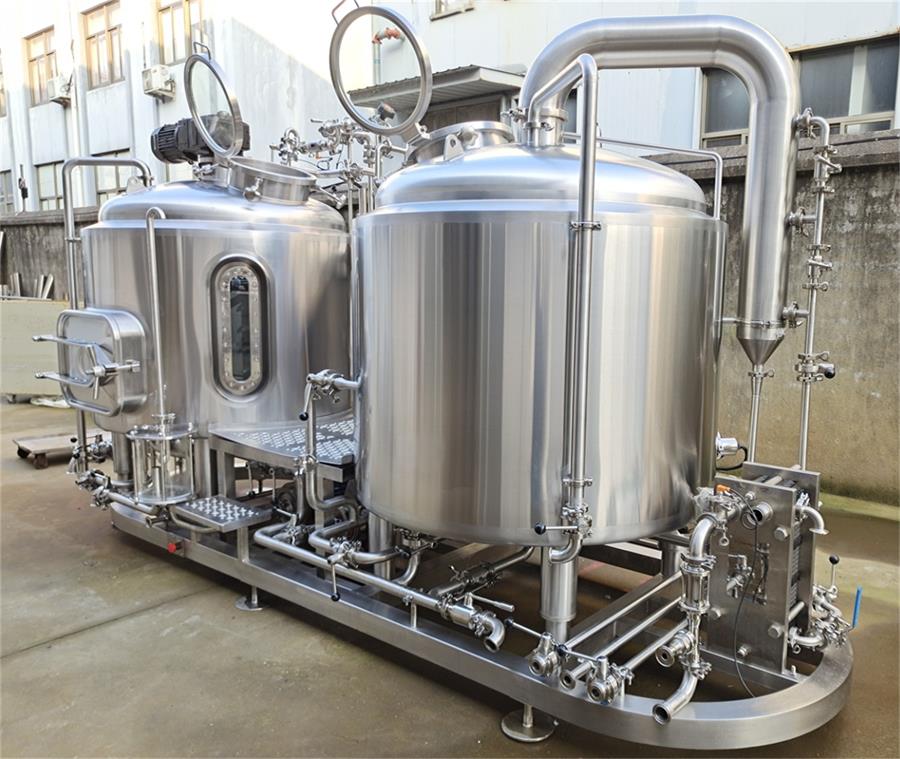
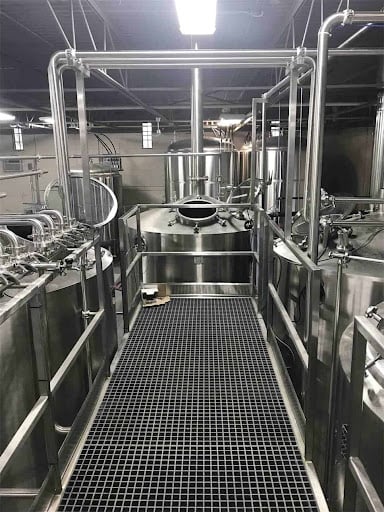
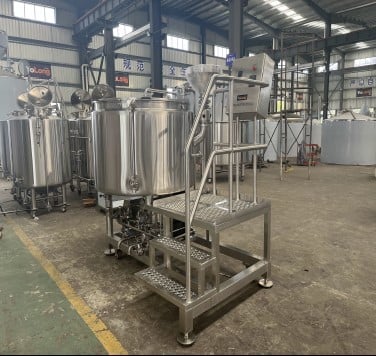
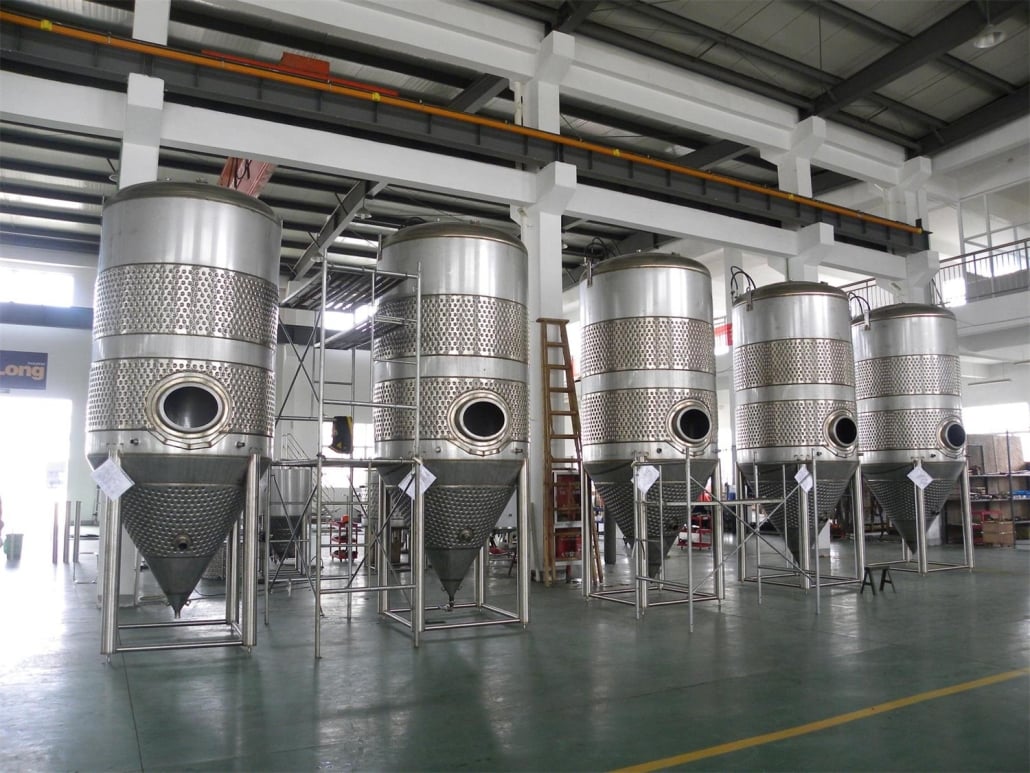
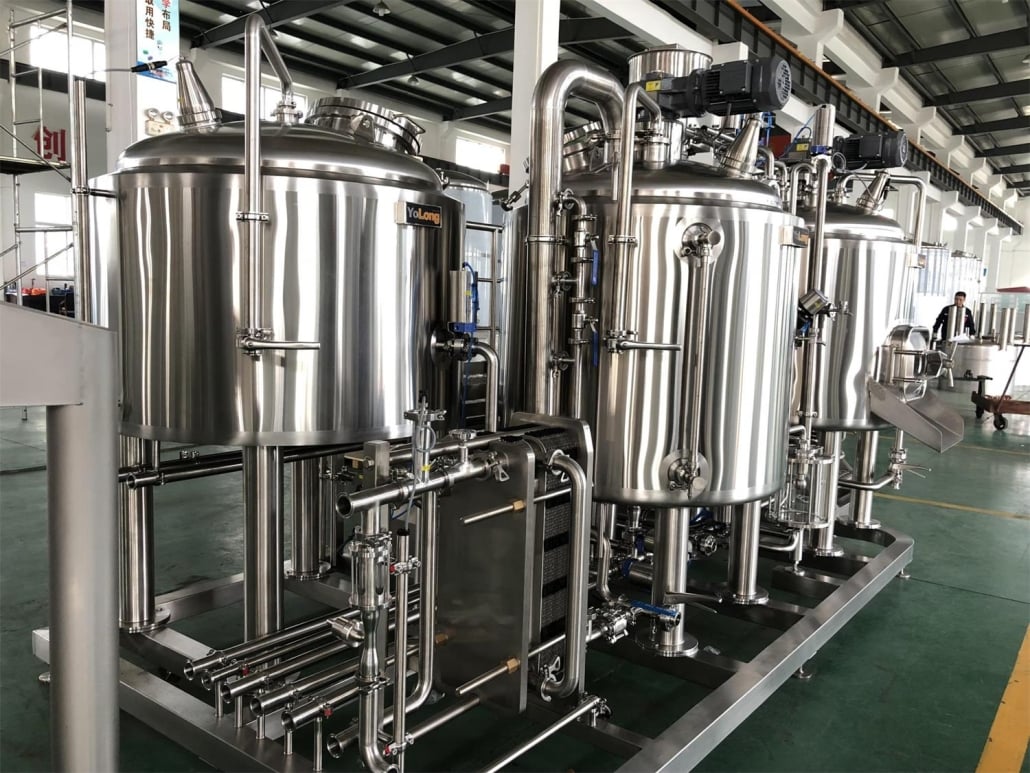
Legal & Licensing Requirements
To operate a beer manufacturing plant, you must comply with local, state, and federal regulations. Key legal requirements include:
- Brewery License – Required for production and sales.
- Alcohol Tax and Trade Bureau (TTB) Permit – Mandatory in the U.S.
- State Alcohol License – Varies by state and region.
- Environmental Regulations – Compliance with waste disposal and water usage policies.
- Health and Safety Standards – Includes hygiene, fire safety, and labor laws.
Marketing & Distribution
Strategy | Details |
---|---|
Local Taprooms | Selling directly from the brewery boosts profit margins. |
Retail Sales | Partnering with liquor stores expands reach. |
Online Sales | E-commerce sales, where legal, enhance accessibility. |
Bars & Restaurants | Draft sales increase brand visibility. |
Festivals & Events | Beer festivals introduce products to new consumers. |
Future Trends in Beer Manufacturing
The beer industry is continuously evolving. Key trends shaping the future include:
- Sustainable Brewing – Breweries are adopting eco-friendly practices like water conservation and solar energy.
- Non-Alcoholic Beers – Rising health consciousness is driving demand for alcohol-free options.
- Innovative Flavors – Experimental ingredients such as exotic fruits, spices, and CBD-infused beers are gaining traction.
- Smart Brewing Technology – Automation and AI-driven analytics enhance efficiency and quality control.
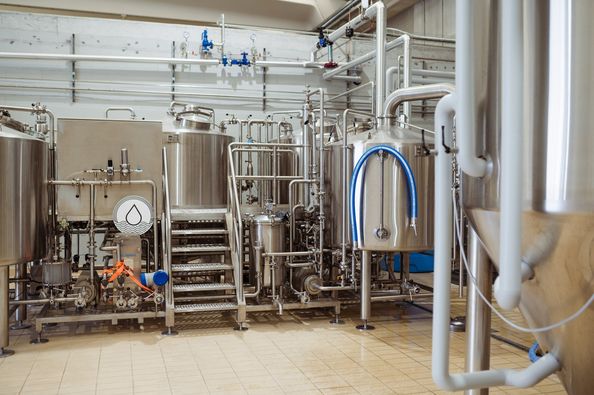
FAQ
Question | Answer |
---|---|
How much does it cost to start a brewery? | Costs range from $200,000 for small craft breweries to $50M for large commercial plants. |
What licenses do I need? | A brewery license, TTB permit, and state alcohol license are required. |
How long does it take to brew beer? | The brewing process typically takes 2-6 weeks. |
What’s the profit margin on beer? | Margins vary but are usually 30-50% depending on scale and distribution. |
Can I sell beer online? | Online sales depend on local laws and shipping regulations. |