Comprehensive Guide to Beer Equipment Suppliers
Overview: Understanding the World of Beer Equipment Suppliers
When it comes to brewing beer, the importance of selecting the right equipment cannot be overstated. Whether you’re a homebrewer scaling up your operations or an entrepreneur setting up a commercial brewery, the equipment you choose will profoundly impact the quality, efficiency, and profitability of your brewing process. This comprehensive guide will take you through everything you need to know about beer equipment suppliers. We will explore different types of brewing systems, present a detailed overview of the brewing process, discuss equipment capacities, and provide insights into supplier options and price ranges. We’ll also touch on critical aspects such as installation, operation, and maintenance, and offer tips on how to choose the best supplier for your needs.
Guide to Beer Brewing Equipment
The equipment used in beer brewing varies widely depending on the scale and type of brewing. From simple homebrewing setups to large-scale commercial systems, understanding the different types of equipment and their functions is essential for making an informed decision.
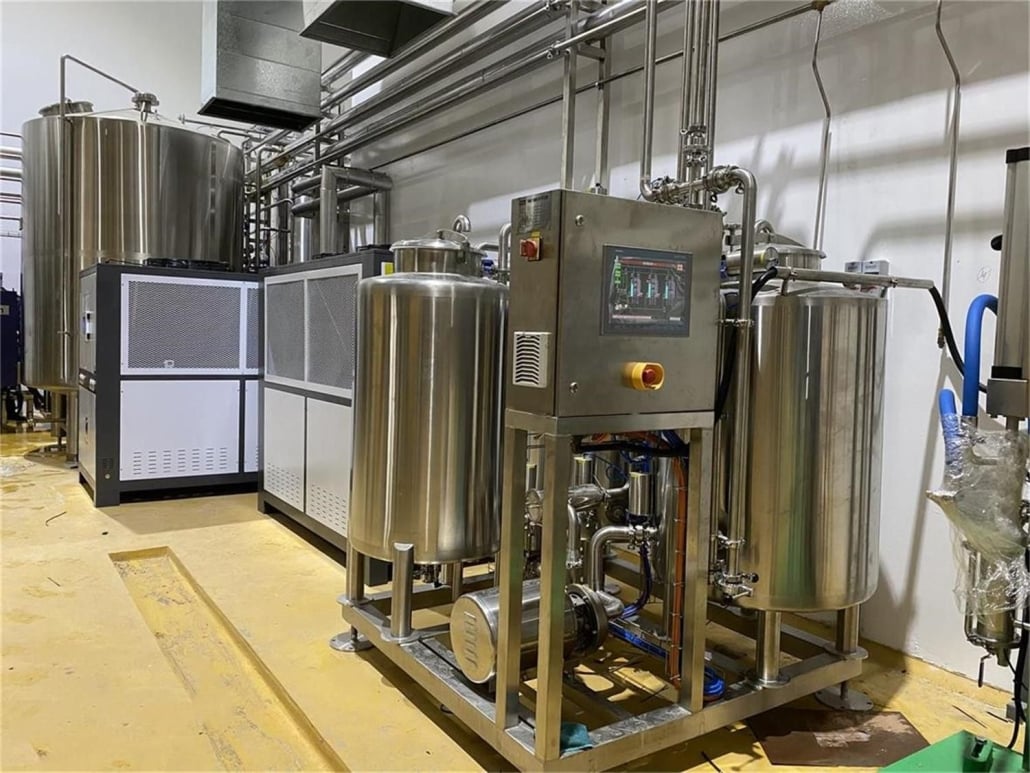
Beer Brewing Equipment Types
In the brewing process, each piece of equipment plays a crucial role in transforming raw ingredients into a finished product. Here’s a closer look at the types of equipment you’ll need:
Equipment Type | Description |
---|---|
Mash Tun | A vessel where the malt is mixed with water and heated to convert starches to sugars. |
Lauter Tun | Used for separating the wort (the liquid extract) from the spent grains. |
Boil Kettle | Where the wort is boiled and hops are added for flavor and aroma. |
Fermentation Tanks | Vessels where yeast is added to the wort to start the fermentation process. |
Bright Beer Tanks | These tanks are used for maturing, clarifying, and carbonating the beer before packaging. |
Heat Exchanger | A device used to rapidly cool the wort after boiling, preventing contamination and preparing it for fermentation. |
Kegging and Bottling Equipment | Systems used to package the beer after fermentation. Includes kegs, bottles, cappers, and labeling machines. |
Cleaning and Sanitizing Equipment | Essential for maintaining hygiene in the brewery, this includes CIP (Clean-In-Place) systems, hoses, brushes, and chemical sanitizers. |
Beer Brewing Process Explained
The beer brewing process is a fascinating journey from raw materials to a refreshing glass of beer. It involves several stages, each requiring specific equipment and precise control over conditions like temperature, time, and cleanliness.
- Mashing: This is the first step, where crushed grains are mixed with water in the mash tun. The heat activates enzymes that convert starches into fermentable sugars.
- Lautering: After mashing, the mixture (now called mash) is transferred to the lauter tun. Here, the liquid wort is separated from the solid grains.
- Boiling: The wort is then boiled in a kettle, and hops are added at different stages to impart bitterness, flavor, and aroma.
- Cooling: After boiling, the wort must be quickly cooled to a temperature suitable for fermentation. This is typically done using a heat exchanger.
- Fermentation: The cooled wort is transferred to fermentation tanks, where yeast is added. Yeast consumes the sugars in the wort, producing alcohol and carbon dioxide.
- Maturation: Once fermentation is complete, the beer is moved to bright beer tanks for maturation. This process can last from a few days to several weeks, depending on the beer style.
- Packaging: Finally, the beer is packaged using kegging or bottling equipment, ready for distribution and consumption.
Comparing Beer Brewing Equipment by Capacity, Space Requirements, and Customization Options
Selecting the right equipment involves understanding your production needs and available space. Here’s a comparison to help you choose:
Factor | Small-Scale Equipment | Medium-Scale Equipment | Large-Scale Equipment |
---|---|---|---|
Capacity | Ideal for producing 5-30 gallons per batch. | Suitable for 50-300 gallons per batch. | Designed for 500-10,000 gallons per batch. |
Space Requirements | Can fit in small spaces like a garage or basement. | Requires a dedicated room or small commercial space. | Needs significant space, often an entire warehouse. |
Customization Options | Limited, mostly standardized setups. | Offers moderate customization options (e.g., add-ons). | Highly customizable, tailored to specific brewing needs. |
Installation Complexity | Easy, often DIY-friendly. | Moderate, may require professional installation. | Complex, requiring professional installation and setup. |
Beer Equipment Suppliers and Price Range
Finding the right supplier is crucial for ensuring quality and getting the best deal. Below is a table that categorizes suppliers based on price range and service offerings:
Supplier | Price Range | Specialization | Region | Customer Support |
---|---|---|---|---|
BrewTech | $5,000 – $50,000 | Custom commercial brewing systems | North America | Extensive support with on-site assistance. |
Alpha Brewing Operations | $10,000 – $100,000 | Mid to large-scale brewing systems | Global | 24/7 support with remote monitoring. |
Ss Brewtech | $500 – $10,000 | Homebrewing and small-scale commercial | Worldwide | Online support with DIY resources. |
Premier Stainless Systems | $20,000 – $150,000 | High-end commercial systems | North America, Europe | Full-service support including installation and training. |
Psycho Brew | $1,000 – $20,000 | Small to medium-scale systems | USA | Comprehensive support with customization options. |
Installation, Operation, and Maintenance of Beer Brewing Equipment
To ensure the longevity and efficiency of your brewing equipment, it’s essential to understand the nuances of installation, operation, and maintenance.
Aspect | Details |
---|---|
Installation | Most suppliers offer installation services. For large systems, professional installation is crucial to avoid operational issues. |
Operation | Requires a thorough understanding of brewing processes. Suppliers often provide training for new systems. |
Maintenance | Regular cleaning and inspection are necessary. Many systems include CIP (Clean-In-Place) features for easier upkeep. |
Troubleshooting | Most suppliers offer troubleshooting guides and customer support. Keeping spare parts on hand can minimize downtime. |
How to Choose the Right Beer Equipment Supplier
Selecting the right supplier involves more than just comparing prices. Here’s a guide on what to consider:
Consideration | Importance | Tips |
---|---|---|
Budget | High | Determine your budget before shopping. Remember to factor in shipping, installation, and maintenance costs. |
Quality of Equipment | Very High | Research the materials and construction quality. Stainless steel is a standard for most equipment. |
Customer Reviews | High | Look for suppliers with positive feedback, especially regarding customer service and product reliability. |
Supplier Experience | Moderate to High | More experienced suppliers may offer better support and more reliable products. |
Customization Options | Depends on needs | If you require specific features, ensure the supplier can customize the equipment to your specifications. |
After-Sales Support | Very High | Check if the supplier offers ongoing support, including maintenance and parts availability. |
Advantages and Disadvantages of Different Brewing Equipment
Understanding the pros and cons of each equipment type can help you make a better decision:
Equipment Type | Advantages | Disadvantages |
---|---|---|
Small-Scale Systems | Affordable, easy to use, and ideal for beginners. | Limited production capacity, fewer customization options. |
Medium-Scale Systems | Balanced capacity and customization, suitable for small breweries. | Requires more space and higher upfront costs. |
Large-Scale Systems | High production capacity, fully customizable, suitable for commercial breweries. | High cost, complex installation, and maintenance. |
Automated Systems | Increases efficiency, reduces labor costs, and ensures consistency. | Expensive, may require technical expertise to operate and maintain. |
Manual Systems | Allows for hands-on control, often less expensive. | Labor-intensive, higher risk of human error, requires more time. |
Installation, Operation, and Maintenance
The long-term success of your brewery heavily depends on proper installation, operation, and maintenance of your equipment. Each stage of this process is vital to ensure the system runs smoothly and delivers consistent results.
Installation
Proper installation is the first step to ensuring that your brewing equipment functions as intended. While smaller systems can often be installed with minimal assistance, larger, more complex setups typically require professional installation. This not only ensures that all components are correctly assembled but also that the system is optimized for your specific brewing needs.
Operation
Operating brewing equipment requires a blend of technical knowledge and practical experience. Suppliers often provide training to help you get started, which is especially important for more complex systems. Understanding the operation manual, regular monitoring of the brewing process, and maintaining consistent records are key practices that can significantly impact the quality of your beer.
Maintenance
Maintenance is where many brewers falter, leading to unexpected downtimes and costly repairs. Regular cleaning, particularly of components like fermentation tanks and heat exchangers, is critical. Implementing a maintenance schedule and adhering to it can prolong the lifespan of your equipment and maintain the quality of your beer.
Tips for Choosing a Reliable Beer Equipment Supplier
Choosing the right supplier is a strategic decision that can influence your brewing success. Here’s how to make an informed choice:
- Evaluate the Supplier’s Reputation: Look for reviews, testimonials, and case studies. A supplier with a strong reputation is likely to deliver high-quality products and reliable customer service.
- Consider Their Experience in the Industry: Experienced suppliers often have better insights into the challenges brewers face and can offer tailored solutions.
- Assess the Range of Equipment: Ensure the supplier offers a wide range of equipment options that suit your current needs and future growth.
- Check for Customization Capabilities: If your brewing process requires specific features or capabilities, ensure the supplier can customize the equipment to meet those needs.
- Review After-Sales Support: Robust after-sales support is critical, especially if you encounter issues post-installation. This includes availability of spare parts, troubleshooting assistance, and maintenance services.
- Compare Prices and Value for Money: While it’s important to stay within budget, don’t compromise on quality. Consider the long-term value of the equipment rather than just the upfront cost.
Pros and Cons: Comparing Beer Brewing Equipment Types
When deciding on the right brewing equipment, weighing the pros and cons is essential. Here’s a comparison:
Type of System | Pros | Cons |
---|---|---|
Manual Brewing Systems | Lower cost, full control over brewing process. | Labor-intensive, requires more skill and time. |
Automated Brewing Systems | Consistent results, efficient, reduces manual labor. | Higher upfront cost, requires technical knowledge to operate. |
Semi-Automated Systems | Balance between control and automation, more affordable than fully automated systems. | Can be complex to operate, still requires some manual labor. |
Modular Systems | Flexible, can be expanded as your brewery grows. | Initial cost can be high, may require professional installation and setup. |
Turnkey Systems | Ready to use, includes all necessary equipment and components. | Less flexibility in customization, typically more expensive upfront. |
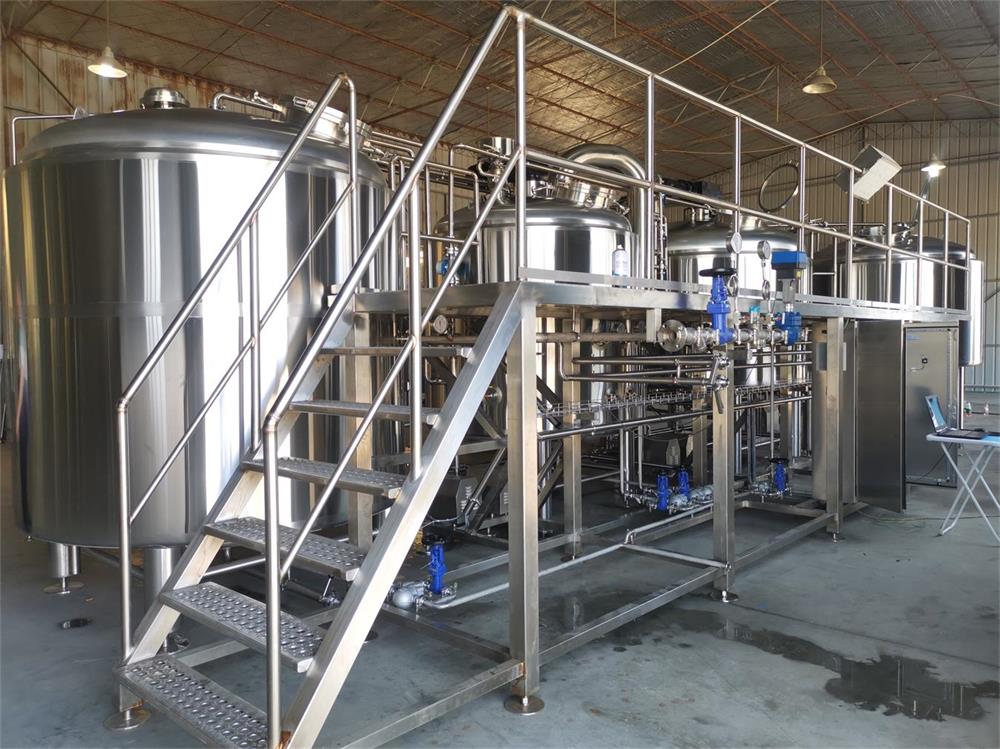
FAQ
Question | Answer |
---|---|
What should I consider when choosing a beer equipment supplier? | Consider factors such as budget, equipment quality, customer reviews, supplier experience, customization options, and after-sales support. |
How do I know if a supplier is reputable? | Research online reviews, ask for references, and consider the supplier’s experience and presence in the industry. |
Is it better to buy a complete brewing system or individual components? | It depends on your needs and budget. A complete system ensures compatibility and ease of installation, while individual components allow for customization. |
How often should I perform maintenance on my brewing equipment? | Regular maintenance is essential. Some tasks, like cleaning, should be done after every brew, while others, like inspections, can be scheduled monthly or quarterly. |
Can I customize my brewing equipment? | Yes, many suppliers offer customization options to tailor the equipment to your specific brewing process and needs. |
What is the typical lifespan of brewing equipment? | With proper maintenance, brewing equipment can last 10-20 years or more, depending on usage and build quality. |
Conclusion
Choosing the right beer equipment supplier is a critical step in setting up a successful brewery. By understanding the different types of equipment, the brewing process, and the factors that influence your purchase, you can make an informed decision that supports your business goals. Remember, while cost is an important consideration, the quality, reliability, and support offered by the supplier are equally crucial in ensuring that your brewing operations run smoothly for years to come.
With this guide, you’re well-equipped to navigate the complexities of the beer equipment market and make choices that will help your brewery thrive. Whether you’re starting small or planning a large-scale operation, the right equipment and supplier partnership will be the foundation of your brewing success.
Share this entry
Interested in learning more about Brewing Systems including additional details and pricing information? Please use the form below to contact us!
YOLONG BREWERY EQUIPMENT FAQS
- Commercial Brewery / Craft Brewery / Microbrewery / Nanobrewery
- What is The Difference Between Craft Beer and Industrial Beer?
- The Bespoke Differences In Custom Brewing Systems
- Everything You Need to Know About Kettle Souring
- How to Choose Brewing Equipment for Your business?
- How To Choose The-Best Partner To Build Your Commercial Microbrewing System?
- Two Detection Sensors That You Need To Use In Your Brewhouse System
- Remote Control Applications in Brewing Equipment/How does it work?
- How To Clean Your Brand New Brewery Tanks?