How to Set Up a Beer Brewing Plant
What Is a Beer Brewing Plant?
Ever wondered how your favorite beer goes from a few simple ingredients to that golden, fizzy perfection in your glass? That magic happens in a beer brewing plant. Think of it as a high-tech kitchen mixed with a bit of chemistry lab, where grain, hops, yeast, and water come together in a carefully controlled process.
A beer brewing plant is a facility designed to brew beer on a commercial or large-scale level. It can be anything from a small craft operation tucked into a warehouse to a massive industrial complex churning out millions of liters each year. These plants are equipped with specialized systems to handle every stage of the brewing process—from mashing and fermentation to conditioning and packaging.
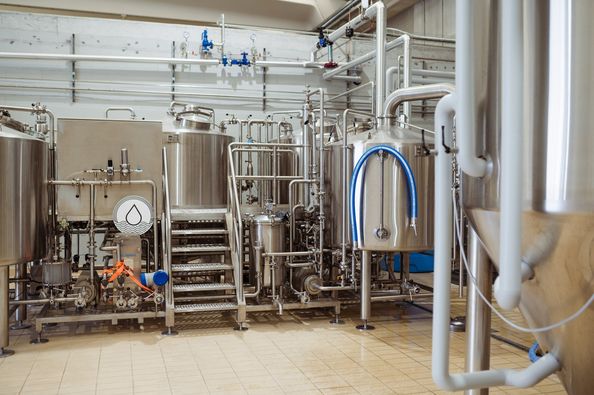
Types of Beer Brewing Plants
Now, not all brewing plants are created equal. Depending on your goals, space, and budget, you’ll need to choose a setup that fits.
Microbreweries are on the smaller side, typically producing less than 15,000 barrels per year. They’re often local favorites and focus on unique, experimental beers. Then we have brewpubs, which are hybrids—part restaurant, part brewery—letting customers sip fresh beer right where it’s made. These places are all about the experience.
Craft breweries operate at a slightly larger scale than microbreweries but still maintain that indie vibe. They usually prioritize quality, flavor, and brewing artistry over mass production. At the top of the pyramid are industrial breweries. These giants, like Anheuser-Busch or Heineken, produce at an international scale. They have massive facilities, global distribution, and automated systems that prioritize consistency and efficiency.
Essential Equipment for a Beer Brewing Plant
Whether you’re brewing 10 gallons or 10,000 barrels, the core equipment remains surprisingly consistent—just scaled up. Let’s walk through the essentials:
You start with a mash tun, where milled grains and hot water mix to convert starches into fermentable sugars. Next up is the lauter tun, which separates the liquid wort from the spent grains. This sweet wort heads to the brew kettle for boiling, where hops are added to give the beer its bitterness and aroma.
Once boiled, the wort goes into a whirlpool tank or heat exchanger to cool down. It’s then transferred into fermenters—often conical vessels—where yeast is pitched to begin fermentation. This stage can last from a few days to several weeks, depending on the beer type.
After fermentation, the beer moves into conditioning tanks where flavors mature. Finally, there’s filtration, carbonation, and packaging in bottles, cans, or kegs. On top of this, you’ll need pumps, hoses, valves, chillers, cleaning systems, and a lot of sensors to keep the brew just right.
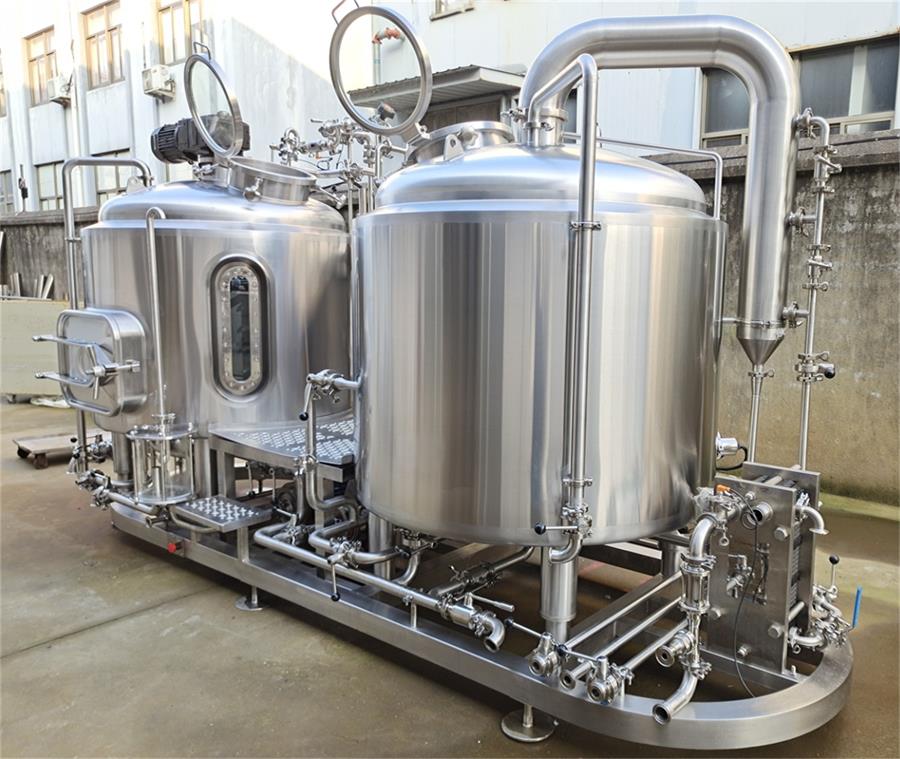
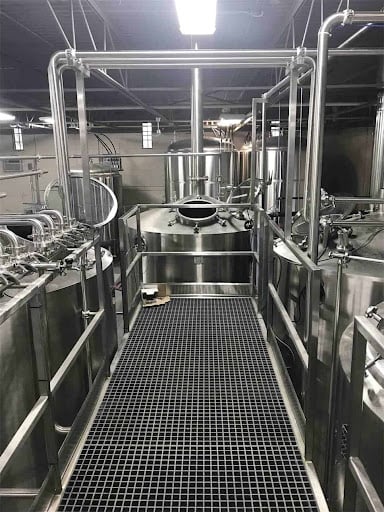
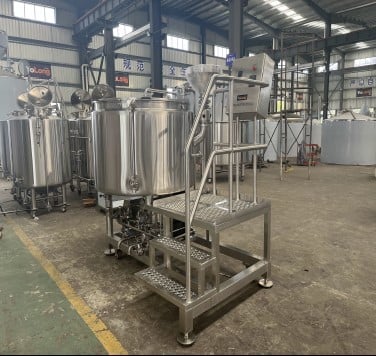
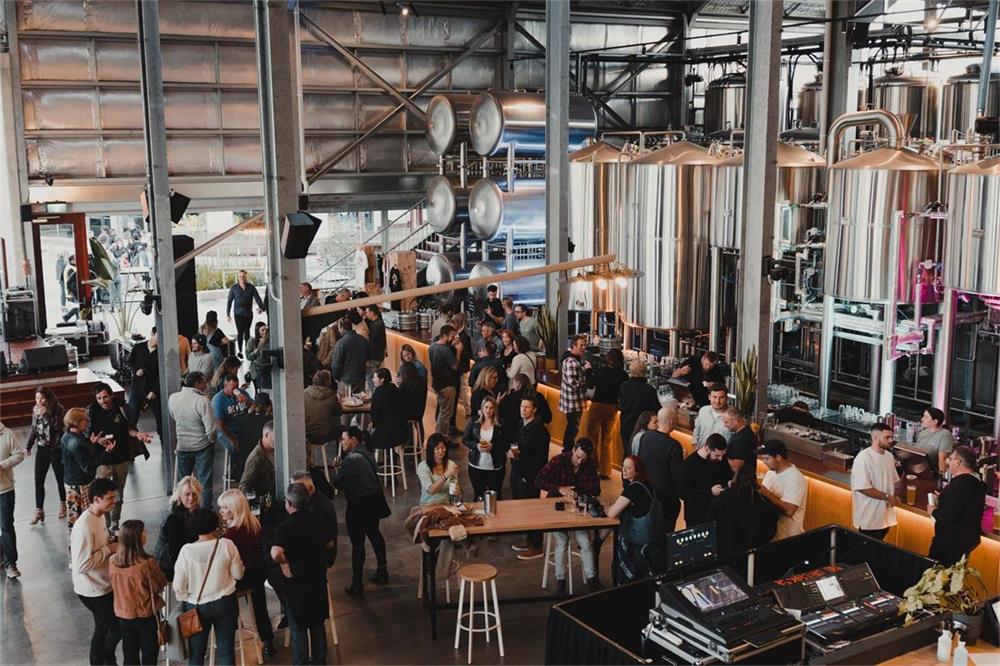
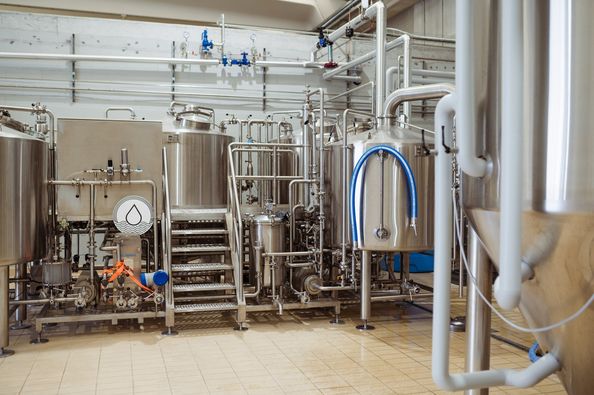
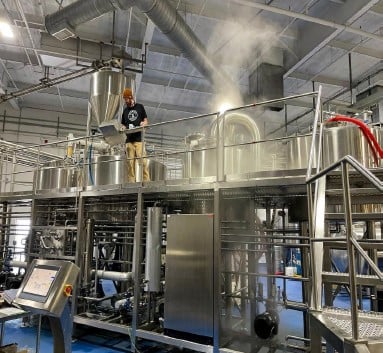
Step-by-Step: How to Start Your Own Beer Brewing Plant
Step | Details |
---|---|
1. Research and Planning | Understand your target market, beer styles, legal regulations, and funding options. Write a comprehensive business plan. |
2. Choose a Location | Look for a space with proper utilities (water, power, drainage), zoning for manufacturing, and potential foot traffic if you plan a taproom. |
3. Select the Equipment | Choose between turnkey systems or custom setups. Consider your production capacity and room for expansion. |
4. Get Licenses and Permits | Register your business, apply for state/federal brewing licenses, food handling permits, and environmental clearances. |
5. Build the Facility | Design the layout for efficient workflow—brewhouse, fermentation area, cold storage, packaging zone. Install plumbing, electricals, HVAC. |
6. Hire and Train Staff | Brewmasters, technicians, quality control, sales, and customer service—you’ll need a team passionate about beer and precision. |
7. Start Brewing and Testing | Pilot test batches to fine-tune recipes, calibrate equipment, and develop your flagship beers. |
8. Launch and Market Your Brand | Use digital marketing, tasting events, and partnerships with local pubs. Build a brand story that resonates. |
Cost to Set Up a Beer Brewing Plant
Let’s talk money. Setting up a beer brewing plant isn’t exactly cheap, but costs can vary wildly based on scale and ambition. A nano-brewery might cost as little as $50,000, while a mid-sized craft operation could push past $500,000. Industrial breweries? We’re talking millions.
Here’s a breakdown of major cost categories:
- Equipment: From $30,000 for a small setup to $1M+ for industrial systems.
- Facility Costs: Renovations, utility upgrades, flooring—can range from $10,000 to several hundred thousand.
- Licensing and Legal: Depends on country/state, but budget $10,000–$50,000.
- Labor and Training: Payroll will be your biggest recurring cost—plan for $100,000+/year for a small team.
- Ingredients and Packaging: Startup supply of malt, hops, bottles/cans—around $10,000 to get rolling.
Tips for Running a Successful Beer Brewing Plant
So, you’ve got your plant set up. How do you keep things running smoothly and grow your brand? First off, quality is king. No amount of marketing can make up for inconsistent or bland beer. Invest in lab testing and sensory panels.
Second, innovate. People love trying new styles and flavors, so keep your brewmaster’s creative juices flowing. But balance that with reliable flagship beers that customers come back for.
Third, nail your logistics. Fresh beer has a shelf life. Keep your cold chain tight and your distribution streamlined. That means refrigerated transport, good inventory software, and strong retail relationships.
Fourth, build community. Host events, collaborate with local businesses, and be active on social media. Your brewery should feel like a living, breathing part of your local scene.
Lastly, stay compliant. Regulations in alcohol manufacturing are strict. Stay up-to-date with tax filings, health inspections, and safety protocols. Better safe than fined—or shut down.
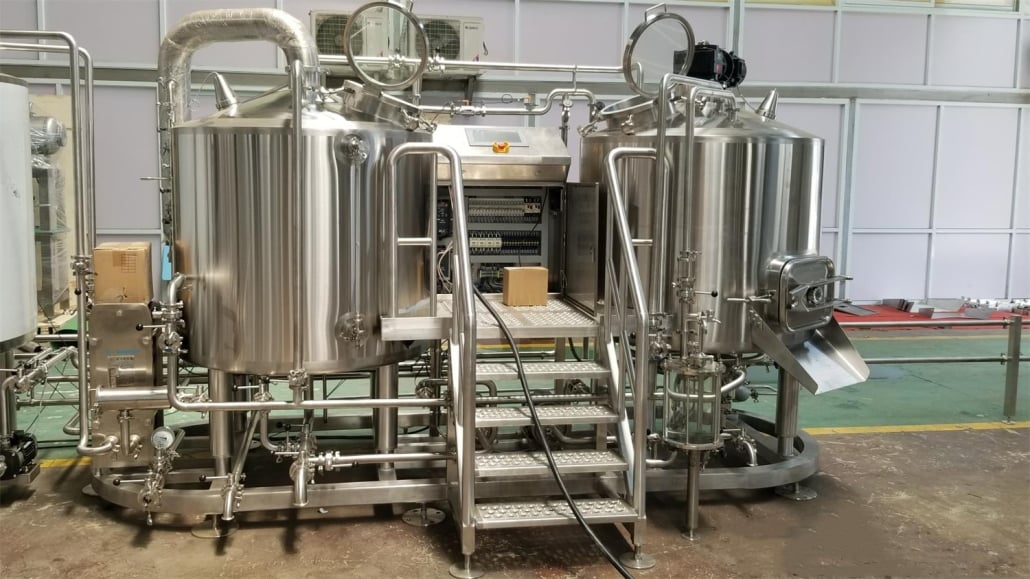
FAQ
Question | Answer |
---|---|
What size brewery should I start with? | It depends on your goals. For local markets, a 5-10 BBL system might suffice. For wider distribution, consider 30 BBL or more. |
How long does it take to brew a batch of beer? | From grain to glass, typically 2–6 weeks depending on the beer style. Lagers take longer than ales. |
Can I automate my beer brewing plant? | Yes, automation is common in larger plants. You can automate mashing, temperature controls, fermentation monitoring, and even packaging. |
Is brewing beer profitable? | It can be—if you manage costs, maintain quality, and build a strong brand. Margins are tight in competitive markets. |
Do I need a brewmaster to start? | Not necessarily, but having a trained brewmaster ensures consistent quality and recipe development. You can also hire consultants. |
Share this entry
Interested in learning more about Brewing Systems including additional details and pricing information? Please use the form below to contact us!
YOLONG BREWERY EQUIPMENT FAQS
- Commercial Brewery / Craft Brewery / Microbrewery / Nanobrewery
- What is The Difference Between Craft Beer and Industrial Beer?
- The Bespoke Differences In Custom Brewing Systems
- Everything You Need to Know About Kettle Souring
- How to Choose Brewing Equipment for Your business?
- How To Choose The-Best Partner To Build Your Commercial Microbrewing System?
- Two Detection Sensors That You Need To Use In Your Brewhouse System
- Remote Control Applications in Brewing Equipment/How does it work?
- How To Clean Your Brand New Brewery Tanks?