Best Fermentation Tanks for Breweries
Types of Brewery Tank: Understanding the Brewing Workhorses
Let’s start at the heart of brewing: the tanks. If you think all brewery tanks are the same, think again. There are multiple types of tanks in a beer brewing system, each with its own job and personality. It’s like a team sport where everyone has a position and specific skills.
First up, we have Mash Tuns. These are where the milled malted barley gets mixed with hot water. Think of it as a giant teapot where the goal is to turn grain starches into fermentable sugars.
Then we move to Lauter Tuns, which look a lot like mash tuns but are all about filtering. They have a false bottom to let the sweet wort pass through while holding the grain husks back.
Next in line is the Boil Kettle, also known as a Brew Kettle. This is where the wort is boiled and hops are added for bitterness, aroma, and flavor. If brewing were cooking, this is where the magic seasoning happens.
After the boil, the wort is sent to a Whirlpool Tank, where it spins to remove unwanted solids. Then it gets chilled rapidly.
Finally, the most famous one: Fermentation Tanks. These come in all shapes and sizes. This is where yeast takes over and converts sugars into alcohol and CO2. Without this, you just have sweet grain juice, not beer.
There’s also the Brite Tank (Bright Beer Tank). It polishes the beer—clarifies and carbonates it before packaging. You might think of it as the beer’s dressing room before it hits the big stage (your mouth).
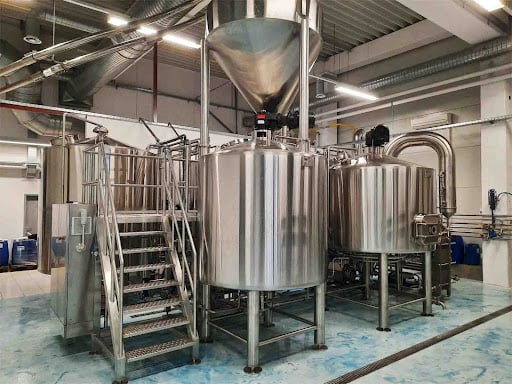
Materials and Construction of Brewery Tank: What’s Inside the Steel?
Brewery tanks may look like space-age pods, but what they’re made of matters as much as what’s inside them. Most tanks are crafted from 304 or 316 stainless steel. Why? Because stainless steel is durable, easy to clean, and doesn’t rust or react with beer’s acidic contents. 316 stainless is a bit more corrosion-resistant, especially against chlorides, making it pricier but more suitable in salty or coastal environments.
The interior of these tanks is usually polished to a sanitary finish, typically between 0.4 to 0.8 µm Ra (roughness average). This smoothness helps prevent bacterial contamination and ensures easy cleaning. Welds are seamless and polished for the same reason.
Tanks are often jacketed (double-walled) to allow for glycol cooling. Temperature control is essential in fermentation and conditioning. These jackets are like climate control for your beer’s environment.
Insulation is also added to tanks, particularly hot liquor tanks and fermentation vessels, to keep heat in or out as needed. Think of them like the thermal mugs of the brewing world.
How to Choose the Right Brewery Tank: Making the Smart Brew Investment
Picking the right tank isn’t just about budget—though let’s be real, budget always matters. It’s about brewing goals, space, scale, and beer style. So how do you make the right choice?
First, define your production volume. A nano-brewery producing 1 BBL (barrel) at a time won’t need the same tank size as a 30-BBL microbrewery.
Consider space constraints. Tall tanks might work in warehouses, but not in a garage setup. Width versus height is a practical factor, not just a design choice.
Then there’s process flow. Do you need a separate whirlpool tank? Are you brewing lagers (which require longer fermentation) or quick-turnaround ales? The style you brew can determine whether you need multiple fermenters or more brite tanks.
Factor in temperature control systems, automation, and even future expansion. Some tanks come with ports and valves ready for extra sensors or sidecar units like yeast propagation systems.
And don’t ignore compliance and standards. Look for tanks that meet ASME, FDA, and 3A Sanitary Standards where applicable.
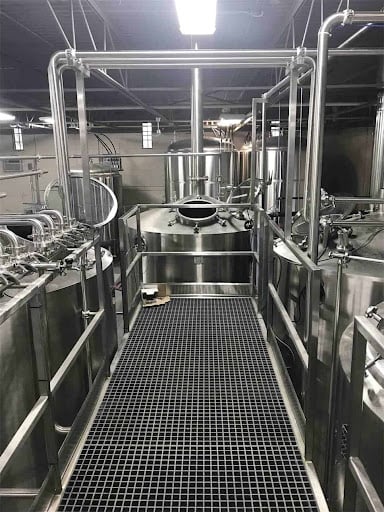
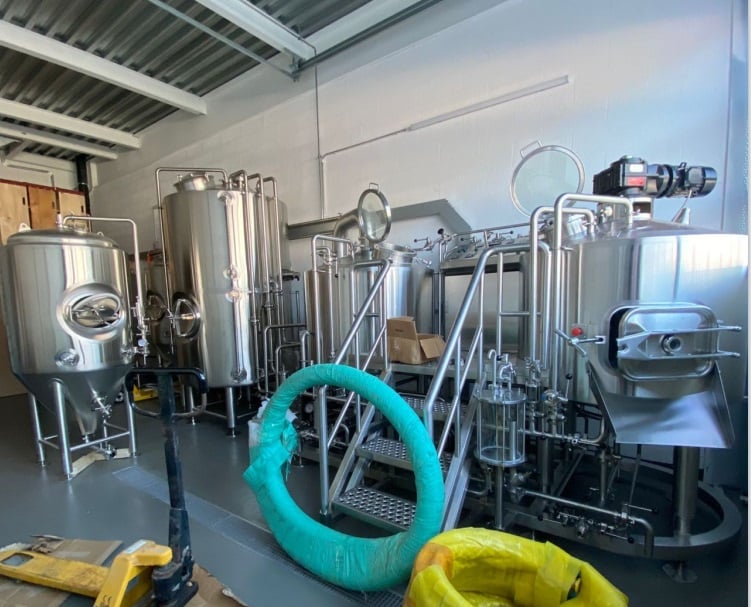
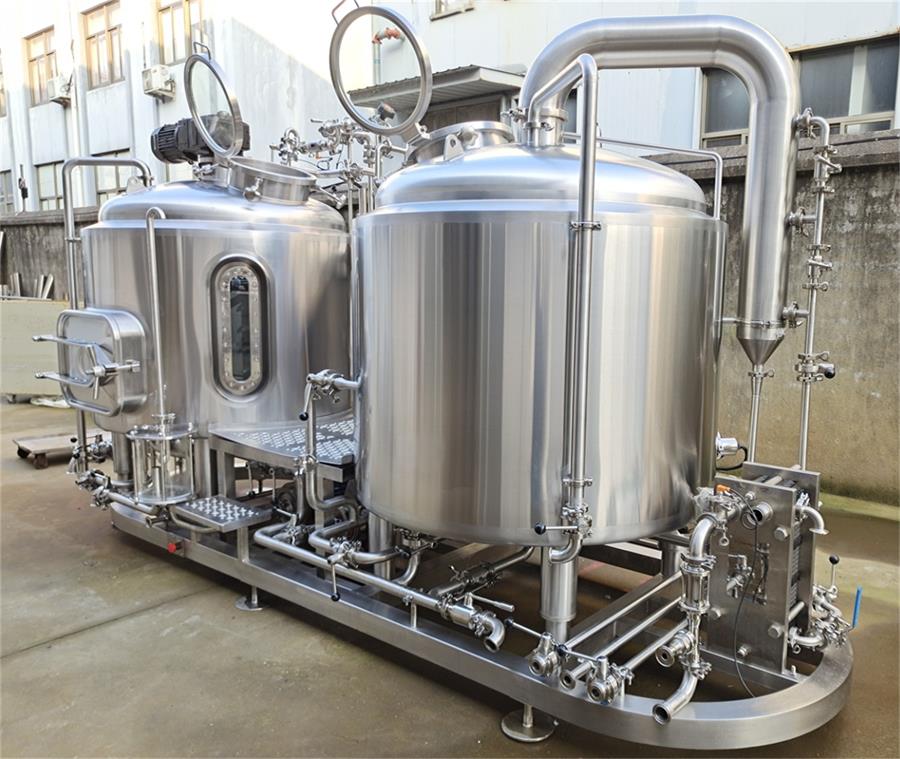
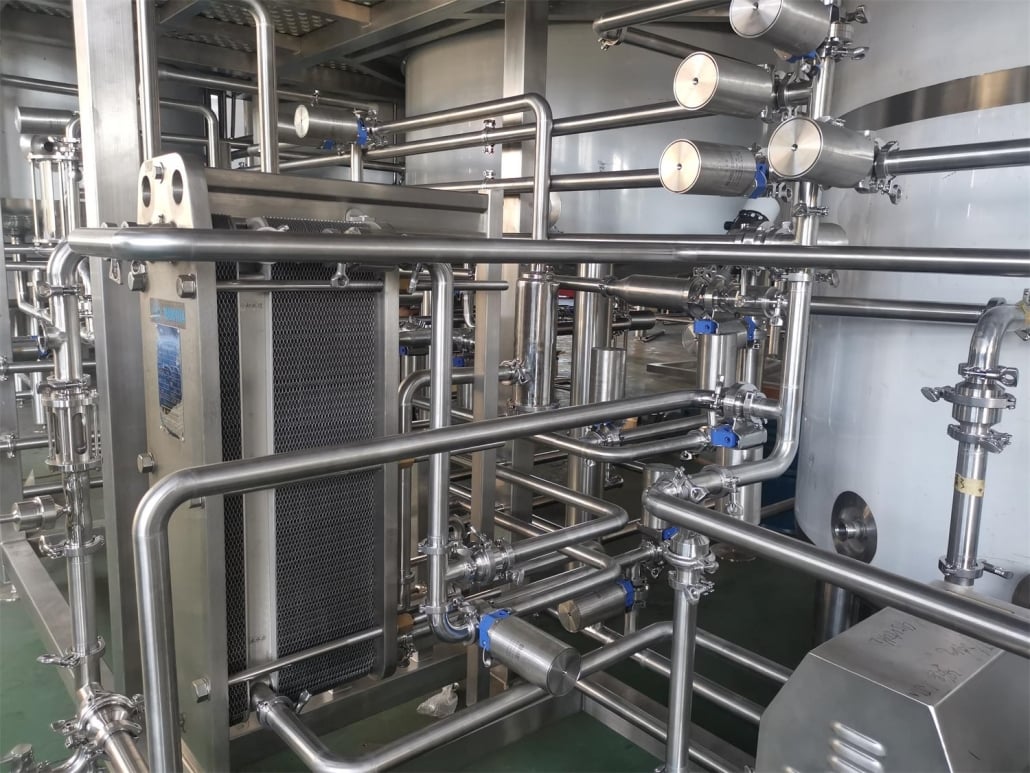
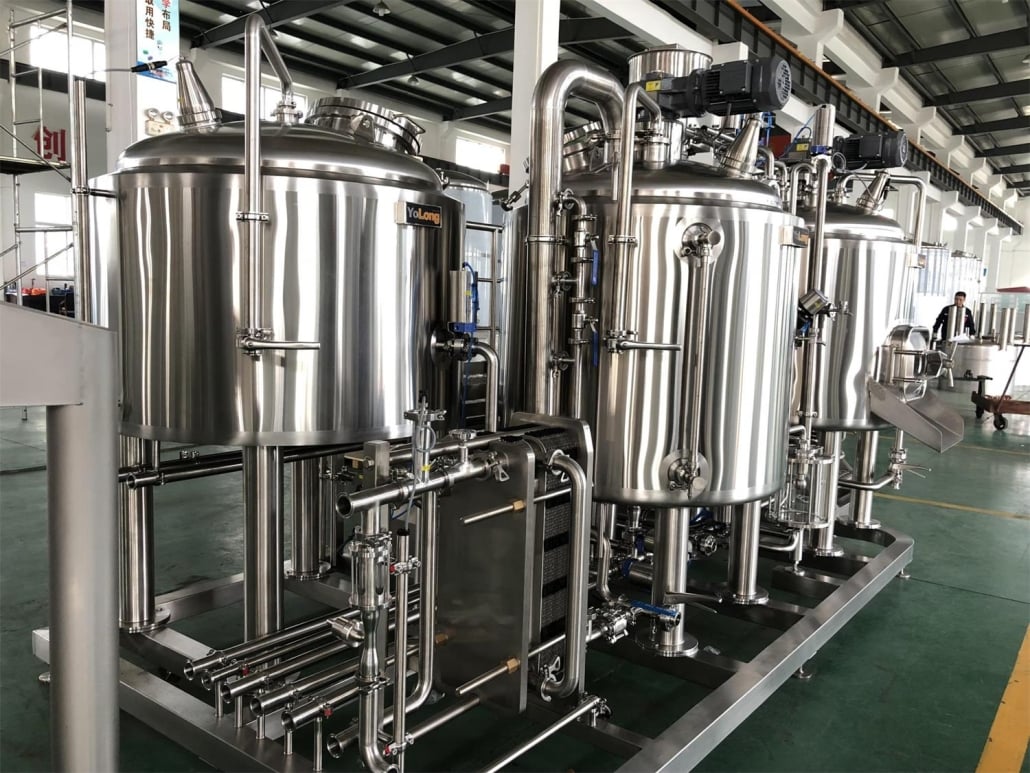
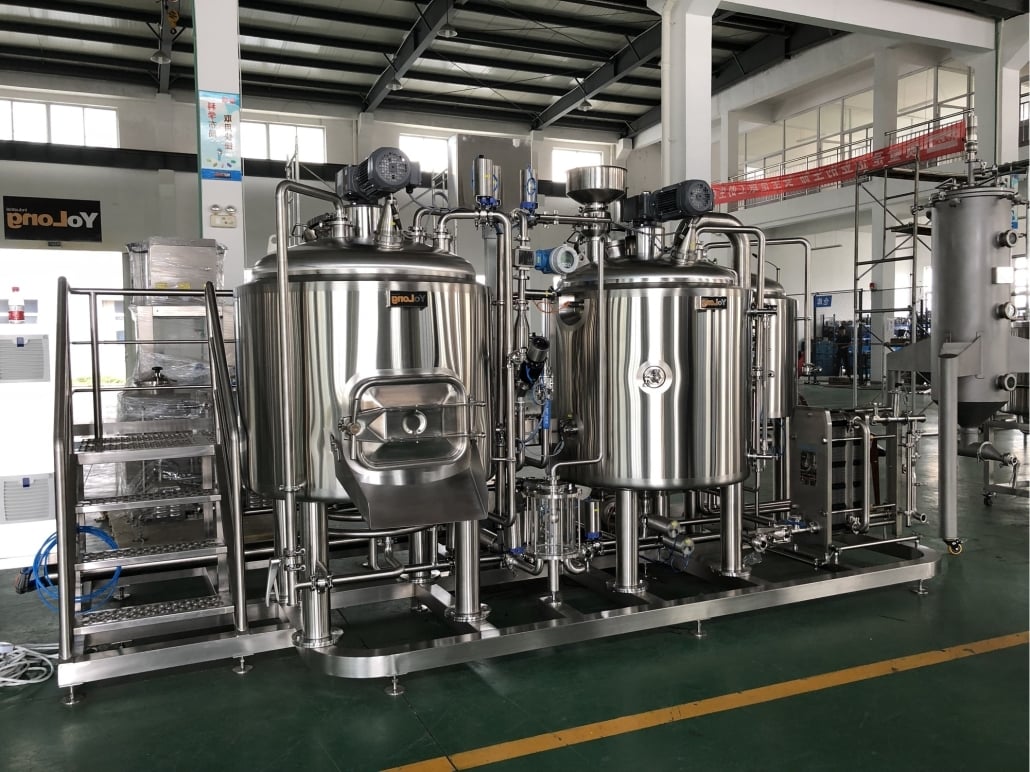
Brewery Tank Maintenance Tips: Love Your Tanks, and They’ll Love You Back
You can’t brew clean beer in dirty tanks—simple as that. Maintenance isn’t just about sanitation; it’s about longevity, safety, and quality.
Regular cleaning using CIP (Clean-In-Place) systems keeps biofilms and residues at bay. Fermentation tanks especially need routine attention due to yeast, proteins, and hop resins.
Check and replace gaskets, seals, and valves periodically. These parts degrade faster than the tank walls and can be hotspots for contamination.
Inspect pressure relief valves and temperature sensors. They need to be working perfectly to ensure safe operations. Nobody wants a geyser of beer from a pressure mishap.
Polish your tanks once in a while (yes, seriously). It helps maintain the smooth sanitary surface.
Track everything. Maintenance logs help catch recurring issues and support compliance with health and safety audits.
Top Brewery Tank Manufacturers or Suppliers: Who Builds the Best Brew Gear?
Looking for a tank builder? There are many global and local players, but a few names stand out based on quality, innovation, and customer feedback.
Ss Brewtech (USA) – Famous for their pro-quality homebrew tanks and commercial systems. Known for thoughtful design, and killer customer support.
BrewBilt Manufacturing (USA) – California-based, offering both standard and custom tanks. Built to ASME standards, these are workhorses.
JVNW (USA) – A long-standing player in commercial brewing systems. Heavy-duty construction and reliable temperature control systems.
Psycho Brew (USA) – Ideal for nano to microbreweries. These guys offer a nice balance between affordability and quality.
DME Process Systems (Canada) – Known for top-tier large-scale solutions. Excellent reputation in the global market.
Tiantai Brewing Equipment (China) – Competitive pricing with solid quality. Their systems are often seen in startups worldwide.
Specific Mechanical Systems (Canada) – Premium tanks with beautiful design and excellent polish work. These are the Ferraris of brewery tanks.
Comparison Table: Brewery Tank Manufacturers
Manufacturer | Country | Target Market | Strengths | Pricing Range |
---|---|---|---|---|
Ss Brewtech | USA | Homebrew to Pro | Innovation, Support, Quality | $$ |
BrewBilt Manufacturing | USA | Micro to Macro | Customization, Durability | $$$$ |
JVNW | USA | Commercial | Proven Reliability, Temp Control | $$$$ |
Psycho Brew | USA | Nano to Micro | Cost-effective, Practical Design | $$ |
DME Process Systems | Canada | Commercial | Engineering Excellence | $$$$ |
Tiantai Brewing Equipment | China | Startups, Export | Budget Friendly, Versatile | $ |
Specific Mechanical | Canada | High-end Craft Breweries | Finish Quality, Aesthetics | $$$$ |
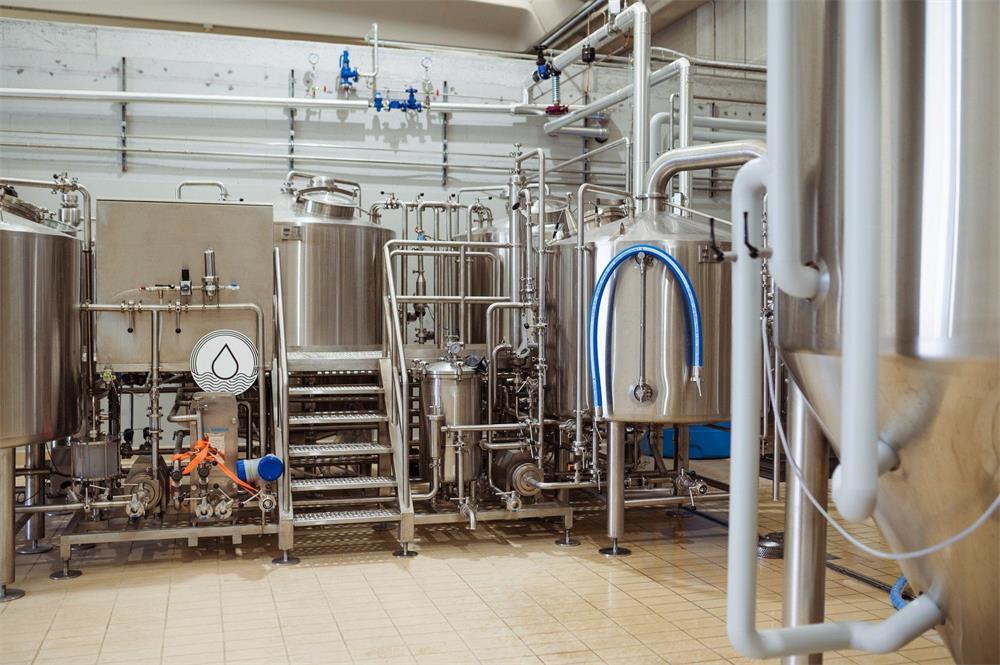
FAQ
Question | Answer |
---|---|
What size brewery tank do I need? | Depends on your batch size. Common sizes range from 1 BBL to 30+ BBL for microbreweries. |
How do I clean a brewery tank? | Use a Clean-In-Place (CIP) system with caustic cleaners, acid rinse, and a final sanitization step. |
What’s the difference between fermenters and brite tanks? | Fermenters are for fermenting; brite tanks are for clarifying, carbonating, and storing beer. |
Can I use one tank for multiple stages? | Technically yes, but it’s not efficient or ideal for quality control. |
How long do brewery tanks last? | With proper care, over 20 years. Stainless steel is incredibly durable. |
What’s the price of a brewery tank? | Anywhere from $2,000 for small fermenters to $50,000+ for large, fully jacketed tanks. |