Choosing the Best Micro Brewing Equipment
Overview
Micro brewing has evolved into a passion project for many beer enthusiasts and small business owners. As craft beer continues to gain popularity worldwide, micro brewing equipment plays a pivotal role in turning unique ideas into delectable brews. But what exactly does it take to set up a microbrewery? From understanding the essential tools to maintaining your equipment, this comprehensive guide covers everything you need to know.
What is Micro Brewing Equipment?
Micro brewing equipment consists of the tools and machinery used to produce craft beer on a smaller scale than traditional large breweries. It’s tailored for small-scale production, often catering to local markets, brewpubs, or experimental batches. Unlike home brewing kits, micro brewing equipment is more sophisticated and capable of producing higher quantities without sacrificing quality.
Think of it as the bridge between hobby brewing and industrial beer production. From malt mills to fermenters, every piece of equipment plays a critical role in the brewing process. Whether you’re brewing 5 gallons or 5 barrels, the right tools ensure consistency, flavor, and efficiency.
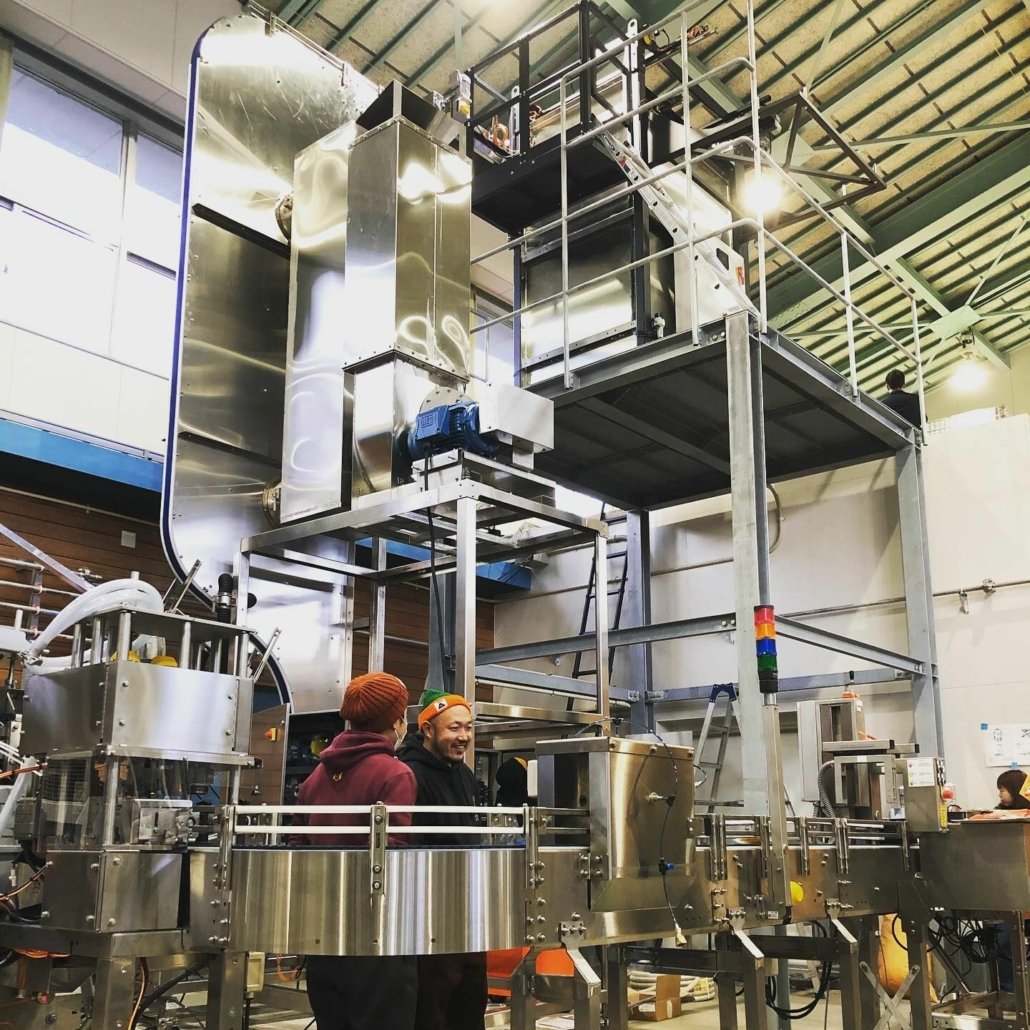
Types of Micro Brewing Equipment
Micro brewing requires several key pieces of equipment, each with a specific purpose. Let’s explore them in detail:
1. Malt Mills
Malt mills crush malted grains into smaller particles, allowing water to extract fermentable sugars during the mashing process. They’re essential for breaking down grains without pulverizing them, ensuring optimal efficiency.
2. Mash Tuns
Mash tuns are vessels where milled grains are mixed with hot water to extract sugars. Insulation and temperature control are critical features for ensuring consistent results.
3. Boiling Kettles
Boiling kettles, or brew kettles, are used to boil the wort (unfermented beer) with hops. This process sterilizes the wort and infuses it with flavor and bitterness.
4. Fermenters
Fermenters are sealed vessels where yeast converts sugars into alcohol and carbon dioxide. They come in various shapes and sizes, often equipped with temperature controls for precise fermentation.
5. Conditioning Tanks
These tanks allow beer to mature, clarify, and carbonate before packaging. Proper conditioning ensures the final product meets desired quality standards.
6. Cleaning Systems
Automated or manual cleaning systems (CIP systems) are used to sanitize brewing equipment. Cleanliness is non-negotiable in brewing, as contamination can ruin entire batches.
7. Packaging Equipment
From bottle fillers to kegging systems, packaging equipment ensures your beer reaches customers in a presentable and safe form.
How to Choose the Right Micro Brewing Equipment
Choosing the right micro brewing equipment can be daunting, especially with so many options. Here are some factors to consider:
1. Production Capacity
Determine how much beer you plan to produce. Small-scale operations may require 1-barrel systems, while larger microbreweries might opt for 10-barrel systems.
2. Space Availability
Measure your available space. Brewing equipment can be bulky, and you’ll need room for storage, operations, and future expansion.
3. Budget
Equipment costs vary widely. Start with a budget and prioritize essential items. Remember, quality equipment often pays for itself in efficiency and durability.
4. Material Quality
Stainless steel is the gold standard for brewing equipment due to its durability, corrosion resistance, and ease of cleaning.
5. Automation Level
Decide whether you prefer manual systems for hands-on control or automated systems for streamlined operations.
6. Manufacturer Reputation
Research manufacturers and read reviews. Trusted brands often provide better support, warranties, and quality assurance.
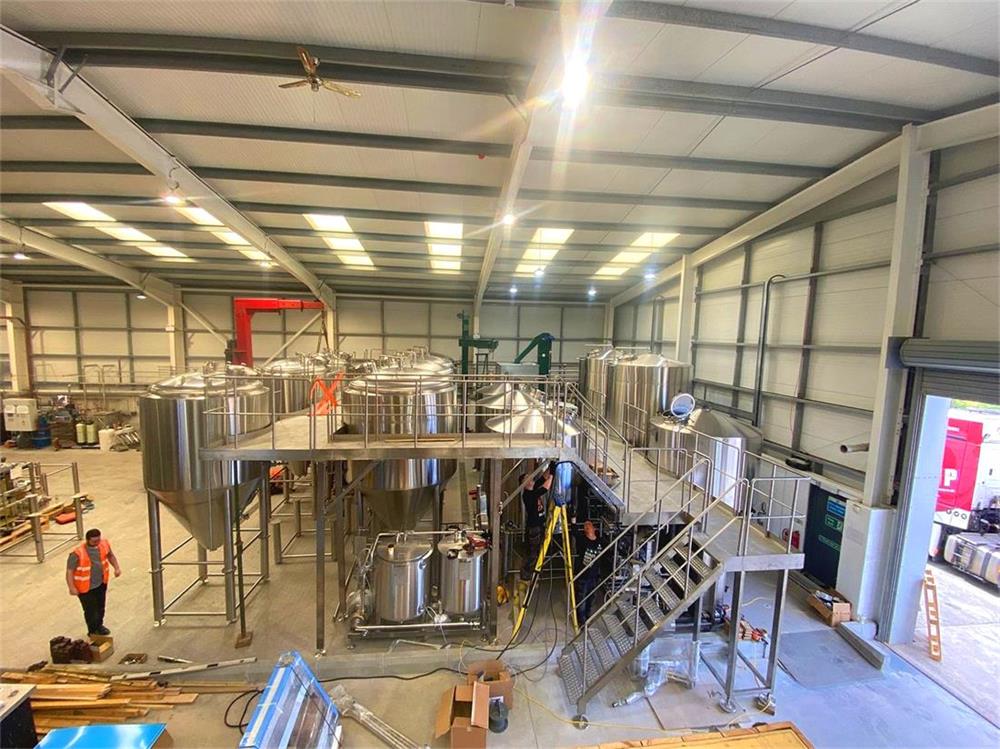
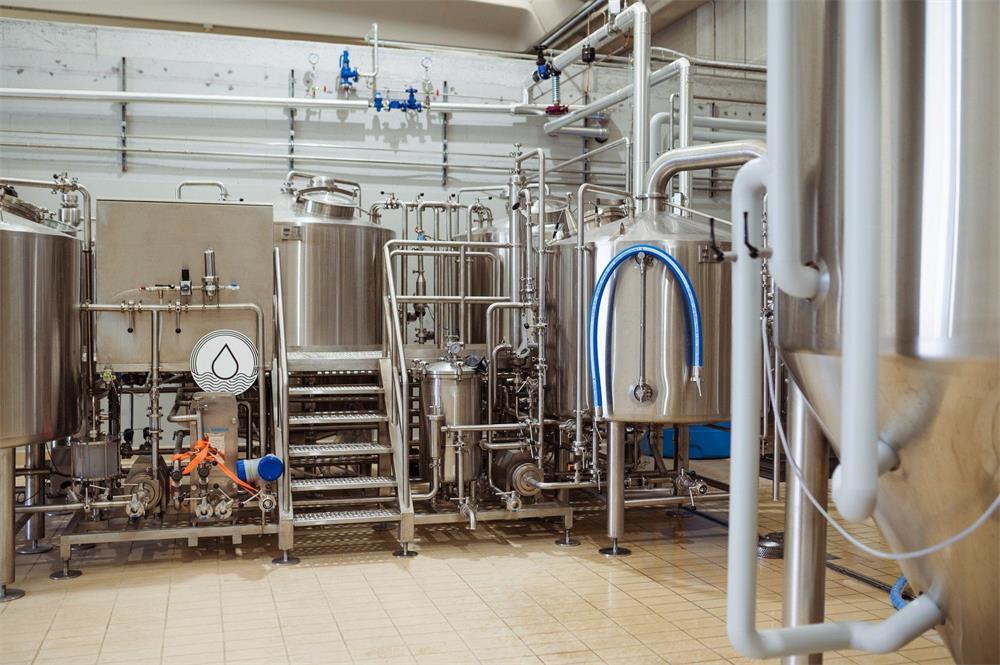
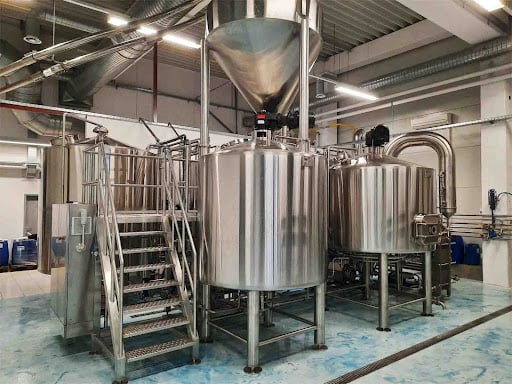
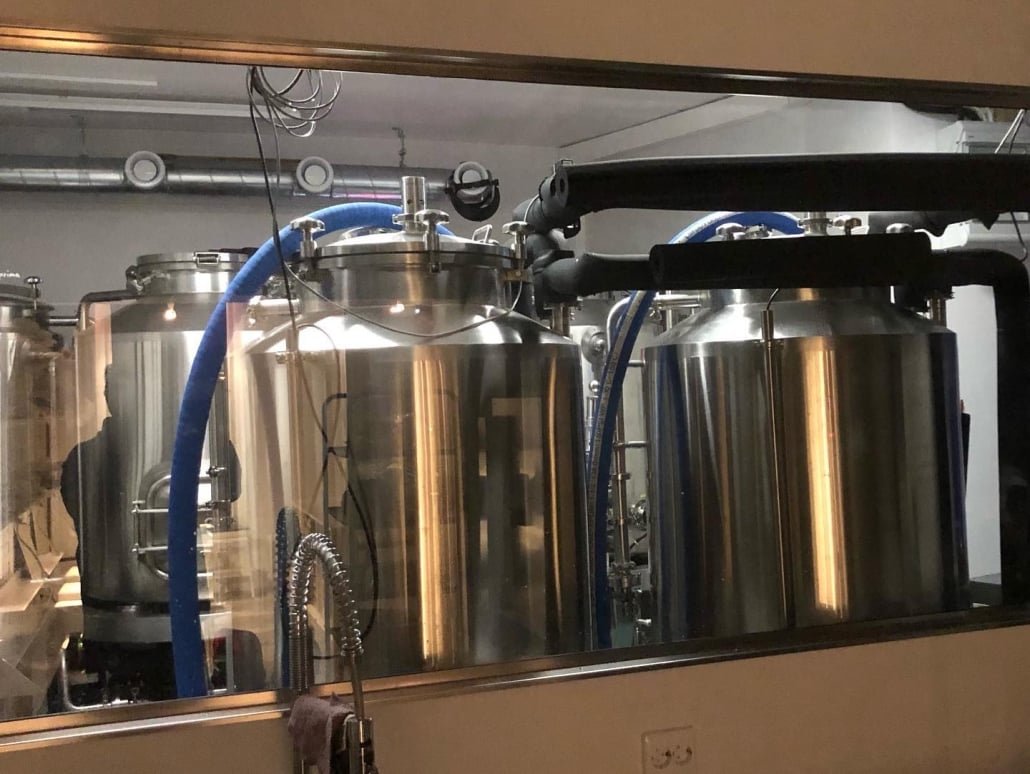
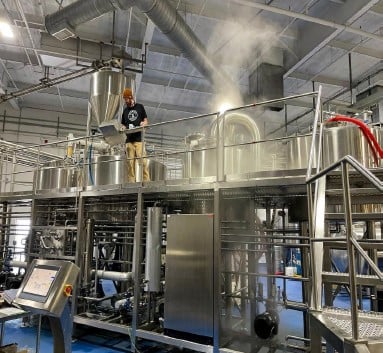
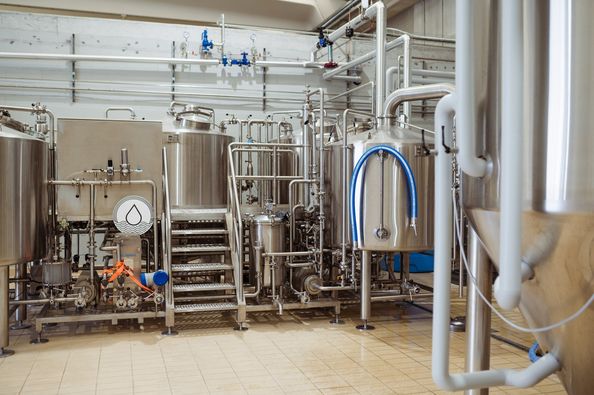
Top 5 Micro Brewing Equipment Brands in 2025
Here’s a comparison of leading micro brewing equipment brands to help you make an informed decision:
Brand | Specialty | Production Range | Price Range | Customer Support |
---|---|---|---|---|
Blichmann Engineering | Innovative home-to-pro systems | 1-10 barrels | $5,000 – $50,000 | Excellent, responsive |
Ss Brewtech | Affordable, scalable equipment | 1-5 barrels | $3,000 – $30,000 | Strong, community-focused |
Spike Brewing | High-quality stainless steel gear | 1-15 barrels | $7,000 – $60,000 | Personalized, professional |
BrauKon | Customizable brewing solutions | 5-50 barrels | $50,000 – $300,000+ | Premium, comprehensive |
Anvil Brewing | Budget-friendly beginner systems | 1-3 barrels | $1,000 – $10,000 | Reliable, beginner-friendly |
Tips for Maintaining Your Brewing Equipment
Maintenance is key to extending the lifespan of your brewing equipment and ensuring consistent beer quality. Follow these tips:
Tip | Details |
---|---|
Clean Regularly | After each use, thoroughly clean all equipment to prevent residue buildup. |
Inspect for Wear and Tear | Regularly check for cracks, leaks, or corrosion in your equipment. |
Use Proper Cleaning Agents | Avoid harsh chemicals that could damage stainless steel or other materials. |
Lubricate Moving Parts | Keep mechanical components well-lubricated to prevent breakdowns. |
Calibrate Sensors and Gauges | Ensure accurate readings by periodically calibrating temperature and pressure sensors. |
Store Equipment Properly | Protect equipment from extreme temperatures and humidity when not in use. |
How Much Does Micro Brewing Equipment Cost?
The cost of micro brewing equipment depends on scale, quality, and automation levels. Here’s a rough breakdown:
- Entry-Level Systems: $5,000 – $20,000 for small-scale or pilot systems.
- Mid-Range Systems: $25,000 – $100,000 for larger, semi-automated setups.
- High-End Systems: $150,000+ for fully automated, high-capacity systems.
Keep in mind, additional costs include installation, utilities, and ongoing maintenance. It’s wise to budget for unexpected expenses.
Advantages and Disadvantages of Various Types of Micro Brewing Equipment
Every type of brewing equipment has its pros and cons. Let’s take a closer look:
Stainless Steel Equipment
- Advantages: Durable, easy to clean, corrosion-resistant.
- Disadvantages: Higher upfront cost.
Plastic Equipment
- Advantages: Affordable, lightweight.
- Disadvantages: Less durable, prone to scratches.
Glass Fermenters
- Advantages: Non-reactive, easy to monitor fermentation.
- Disadvantages: Fragile, heavy.
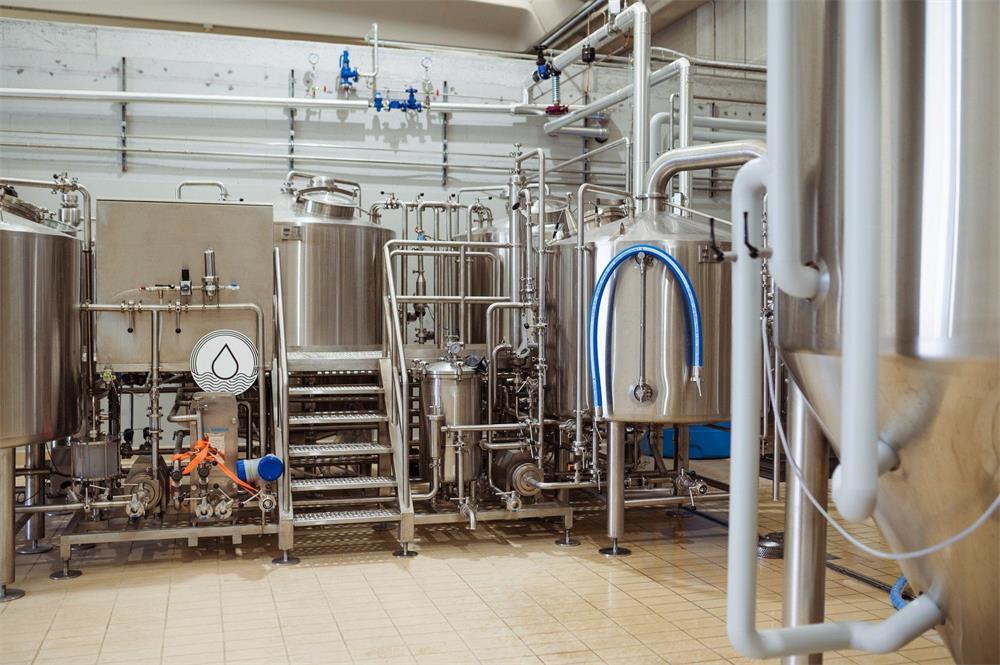
How Can Beer Manufacturing Plants Promote New Brands?
Promoting new beer brands requires creativity and strategy. Here are a few ideas:
- Host Tasting Events: Engage local communities by offering free tastings.
- Collaborate with Restaurants: Pair your beers with food to create memorable experiences.
- Leverage Social Media: Showcase your brewing process and share customer testimonials.
- Offer Seasonal Brews: Limited-edition releases create buzz and urgency.
- Participate in Beer Festivals: Network with enthusiasts and industry professionals.
FAQ
Question | Answer |
---|---|
What size system is best for a startup? | A 1-3 barrel system is ideal for most startups aiming for local markets. |
How often should I clean my equipment? | Clean after every batch to maintain hygiene and prevent contamination. |
Can I upgrade my system later? | Yes, many systems are modular and can be expanded as your business grows. |
What certifications should I look for? | Look for FDA-approved materials and ISO certifications for quality. |
Is automation necessary for microbreweries? | Not mandatory, but it improves efficiency and consistency. |