Automated Brewery System
Overview of Automated Brewery Systems
Imagine brewing beer without the guesswork, stress, and manual labor. That’s what automated brewery systems bring to the table—a seamless fusion of technology and tradition to deliver consistent, high-quality beer. These systems are gaining traction in the brewing industry, from large-scale breweries to small craft operations, thanks to their efficiency, scalability, and precision.
At their core, automated brewery systems are designed to streamline the brewing process by automating tasks like mashing, boiling, fermenting, and packaging. But what sets them apart? Let’s dive into the details.
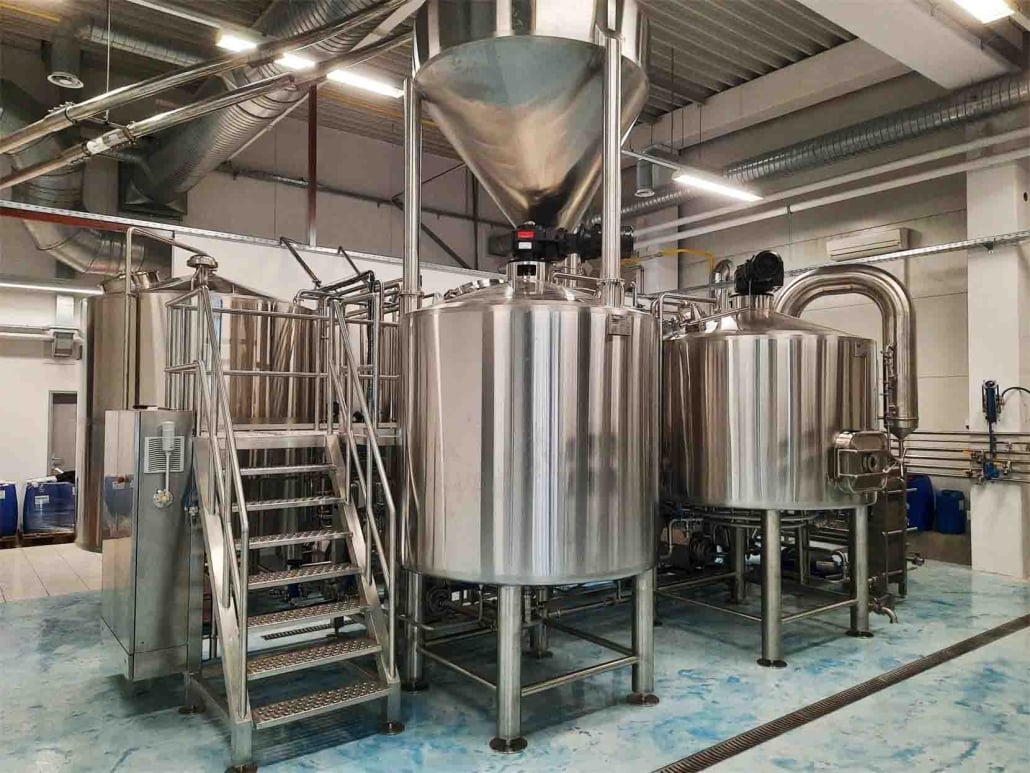
The Core Functions of Automated Brewery Systems
An automated brewery system is like having a personal assistant for your brewing operations. Here’s how they work:
1. Precision in Brewing
Automation ensures every step—from heating to fermentation—is precisely controlled. Want consistent flavor in every batch? Automated systems make it happen by regulating temperature, pH levels, and ingredient ratios.
2. Enhanced Scalability
Whether you’re producing 50 liters or 5,000 liters, these systems scale seamlessly. It’s like upgrading your kitchen to a Michelin-starred setup.
3. Efficiency Boost
Manual brewing can be labor-intensive, but automated systems cut down brewing times significantly while improving output quality. Faster processes mean happier customers!
Troubleshooting Common Issues with Automated Brewery Equipment
Even the best systems can face hiccups. Here’s how to tackle common challenges:
1. Temperature Fluctuations
Does your brew taste off? Temperature control issues are a common culprit. Automated systems often have built-in alarms to alert brewers when temperatures deviate from set parameters.
2. Sensor Malfunctions
Modern systems rely heavily on sensors. A faulty sensor might disrupt the brewing cycle. Regular calibration and maintenance keep your system running smoothly.
3. Software Glitches
Occasional software crashes or bugs can pause production. Backups and regular updates are essential to minimize disruptions.
Present Brewing Process with Automated Systems
An automated brewery system follows these key stages, combining the artistry of brewing with cutting-edge technology:
1. Mashing
In this stage, grains are mixed with hot water. Automation ensures precise temperature control to extract sugars efficiently.
2. Lautering
The system separates the liquid wort from the grain solids. Advanced systems use pumps and valves for optimal efficiency.
3. Boiling
The wort is boiled, and hops are added. Automated timers and temperature settings ensure consistency.
4. Fermentation
The magic happens here—yeast converts sugars into alcohol. Automation keeps the fermentation environment ideal.
5. Packaging
Whether bottling, canning, or kegging, automated systems streamline this process, ensuring quality and speed.
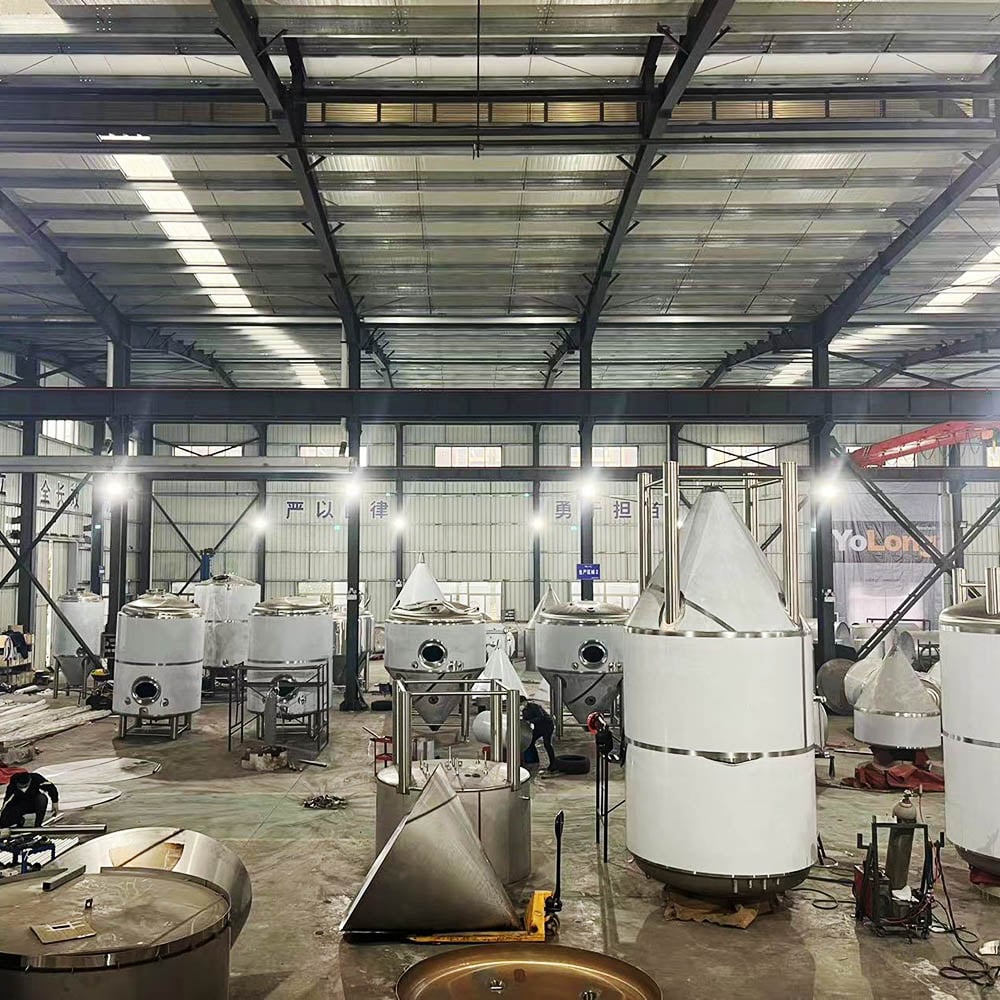
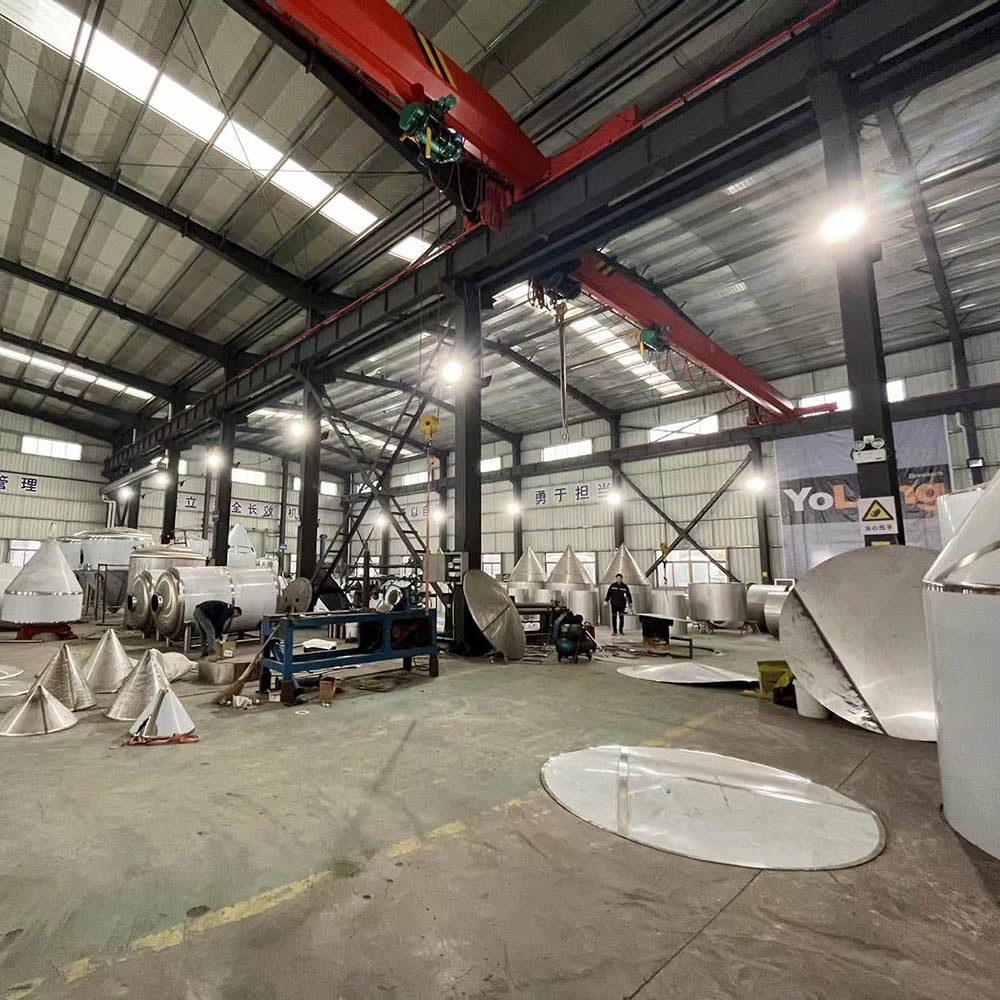
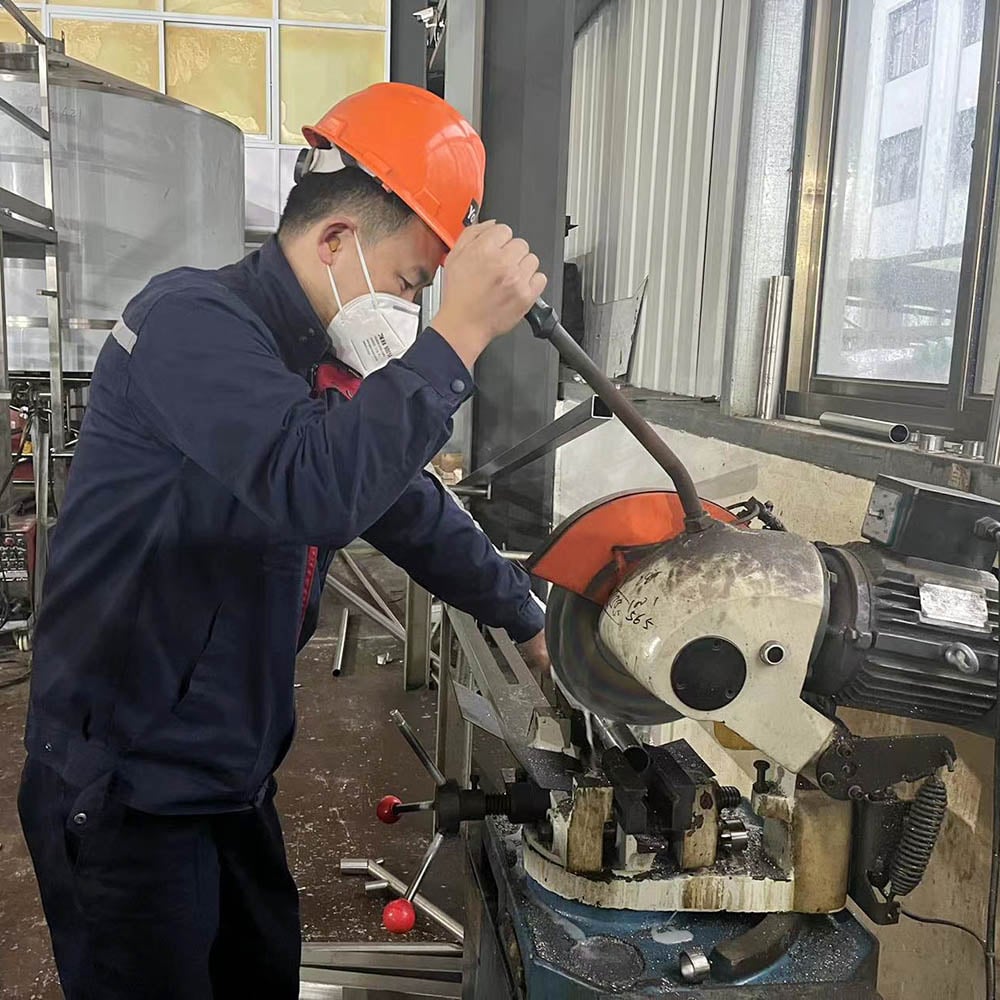
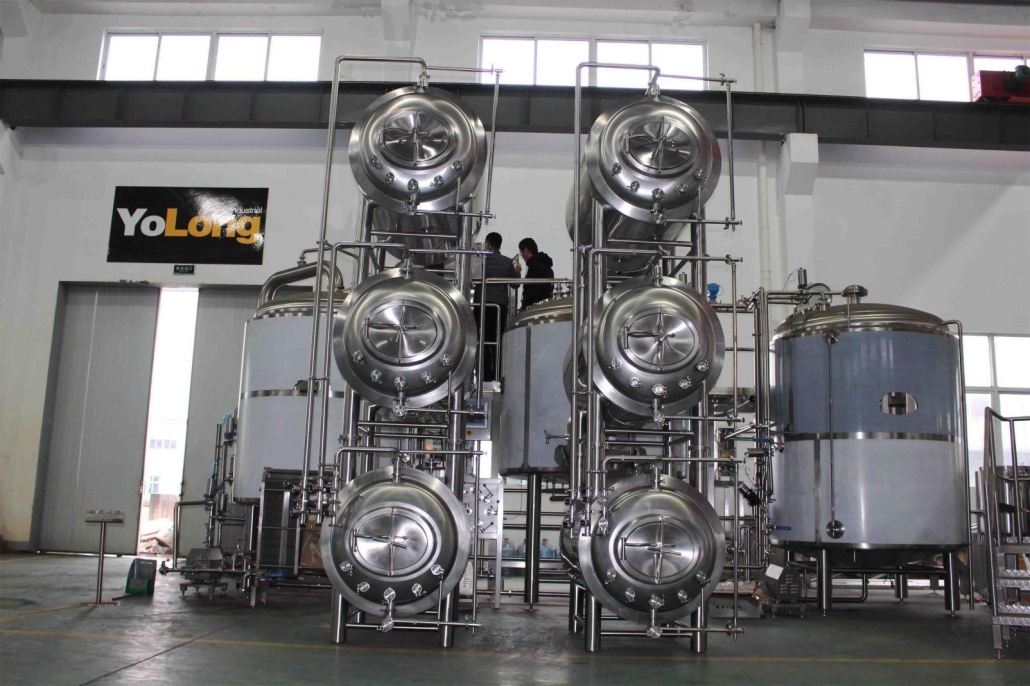
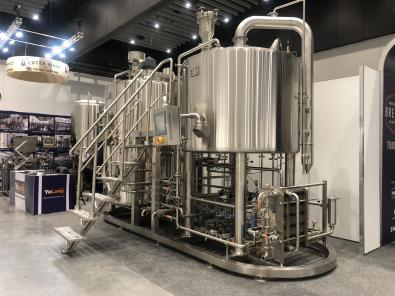
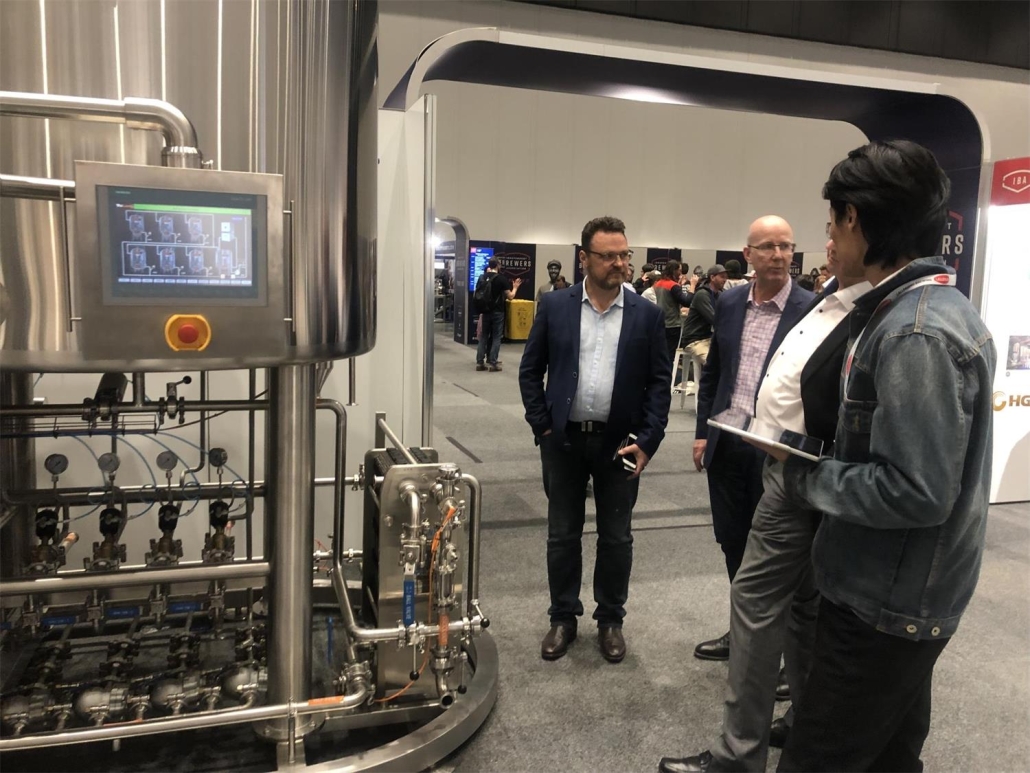
Comparison of Features: Capacity, Space, Design, Layout, and Customization
Feature | Small Breweries | Medium Breweries | Large Breweries |
---|---|---|---|
Capacity | 50-500 liters | 500-5,000 liters | 5,000+ liters |
Space Requirements | Compact, fits small spaces | Moderate, requires dedicated areas | Large, warehouse-style setup |
Design | Minimalist, user-friendly interfaces | Modular, scalable | Comprehensive, fully integrated |
Layout | Compact and portable designs | Flexible modular layouts | Large, fixed layouts |
Customization | Limited options | Moderate customization | High-level customization |
Suppliers and Price Ranges of Automated Brewery Systems
Supplier | Price Range (USD) | Special Features |
---|---|---|
BrewTech Systems | $20,000 – $100,000 | Compact designs, IoT-enabled |
SmartBrew Automation | $50,000 – $200,000 | Modular systems, AI-powered analytics |
BrewMaster Pro | $100,000 – $500,000 | Large-scale systems, high precision |
Installation, Operation, and Maintenance Guidelines
Aspect | Details |
---|---|
Installation | Involves electrical setup, piping, and software integration. |
Operation | User-friendly interfaces with real-time monitoring of brewing processes. |
Maintenance | Regular cleaning, sensor calibration, and software updates. |
How to Choose the Right Supplier
Criteria | Details |
---|---|
Reputation | Look for suppliers with strong reviews and industry experience. |
Customization | Ensure the system can adapt to your specific brewing needs. |
Price vs. Value | Compare upfront costs with long-term efficiency and savings. |
Support & Service | Opt for suppliers offering excellent customer support and training programs. |
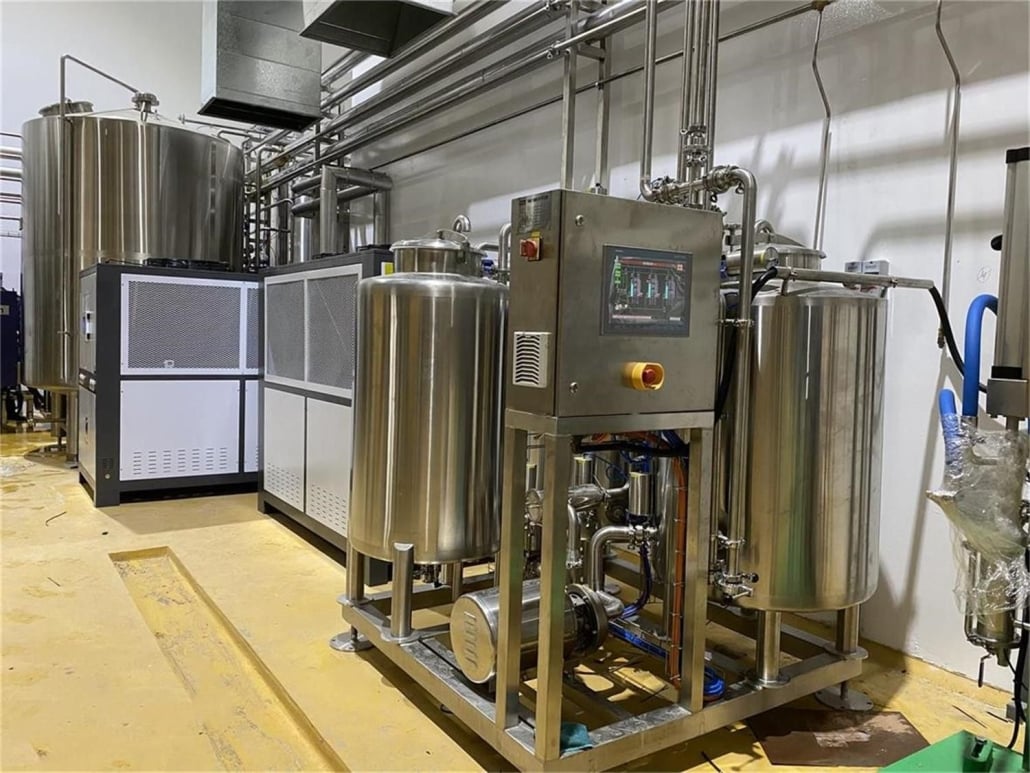
Advantages and Limitations of Automated Brewery Systems
Advantages | Limitations |
---|---|
Consistency in quality across batches | High initial investment |
Time and labor savings | Requires technical expertise for operation |
Improved scalability | Potential software or hardware malfunctions |
Better data analysis for process optimization | May not suit very small-scale operations |
The Benefits of an Automated Brewery System for the Brewing Industry
Automated systems are a game-changer for brewers. They offer unparalleled control, reduce waste, and make scaling operations a breeze. Small craft brewers can maintain artisanal quality while expanding their reach, and large-scale breweries benefit from operational efficiency.
FAQs
Question | Answer |
---|---|
What is an automated brewery system? | A technology-driven system that automates the brewing process from start to finish. |
How much does it cost? | Prices range from $20,000 to $500,000 depending on capacity and features. |
Are they suitable for small breweries? | Yes, especially modular systems designed for compact spaces. |
What are the key maintenance tasks? | Cleaning, sensor calibration, and regular software updates are essential. |
Can I customize an automated system? | Most suppliers offer customization to meet specific brewing needs. |
Share this entry
Interested in learning more about Brewing Systems including additional details and pricing information? Please use the form below to contact us!
YOLONG BREWERY EQUIPMENT FAQS
- Commercial Brewery / Craft Brewery / Microbrewery / Nanobrewery
- What is The Difference Between Craft Beer and Industrial Beer?
- The Bespoke Differences In Custom Brewing Systems
- Everything You Need to Know About Kettle Souring
- How to Choose Brewing Equipment for Your business?
- How To Choose The-Best Partner To Build Your Commercial Microbrewing System?
- Two Detection Sensors That You Need To Use In Your Brewhouse System
- Remote Control Applications in Brewing Equipment/How does it work?
- How To Clean Your Brand New Brewery Tanks?