Professional Brewing Equipment
The Brewing Process and Equipment Used
Step 1: Milling the Grains
Milling is where the brewing journey begins. The grains are crushed to expose their starches, which are later converted into fermentable sugars. Consistency in milling ensures efficient sugar extraction and prevents clogging during the brewing process.
Key Equipment: Grain mills with adjustable rollers for uniform milling.
Step 2: Mashing
Mashing involves mixing the crushed grains with hot water to form a mash. This activates enzymes that break down starches into fermentable sugars.
Key Equipment: Mash tuns. Choose models with precise temperature controls and efficient insulation.
Step 3: Lautering
In lautering, the mash is separated into liquid wort and spent grains. The process requires careful handling to ensure maximum wort extraction without introducing unwanted flavors.
Key Equipment: Lauter tuns with slotted plates or false bottoms for efficient filtration.
Step 4: Boiling
The wort is boiled to sterilize it and to integrate hops, which add bitterness, flavor, and aroma.
Key Equipment: Brew kettles with whirlpool systems and temperature control.
Step 5: Fermentation
Fermentation is where the wort transforms into beer. Yeast converts the sugars into alcohol and carbon dioxide.
Key Equipment: Conical fermenters for easy yeast harvesting and sediment removal.
Step 6: Conditioning
Conditioning refines the beer, improving clarity and flavor.
Key Equipment: Bright tanks or secondary fermenters.
Step 7: Packaging
Packaging the finished beer into kegs, bottles, or cans is the final step. Efficiency here ensures minimal waste and consistent carbonation.
Key Equipment: Semi-automated or fully automated packaging lines.
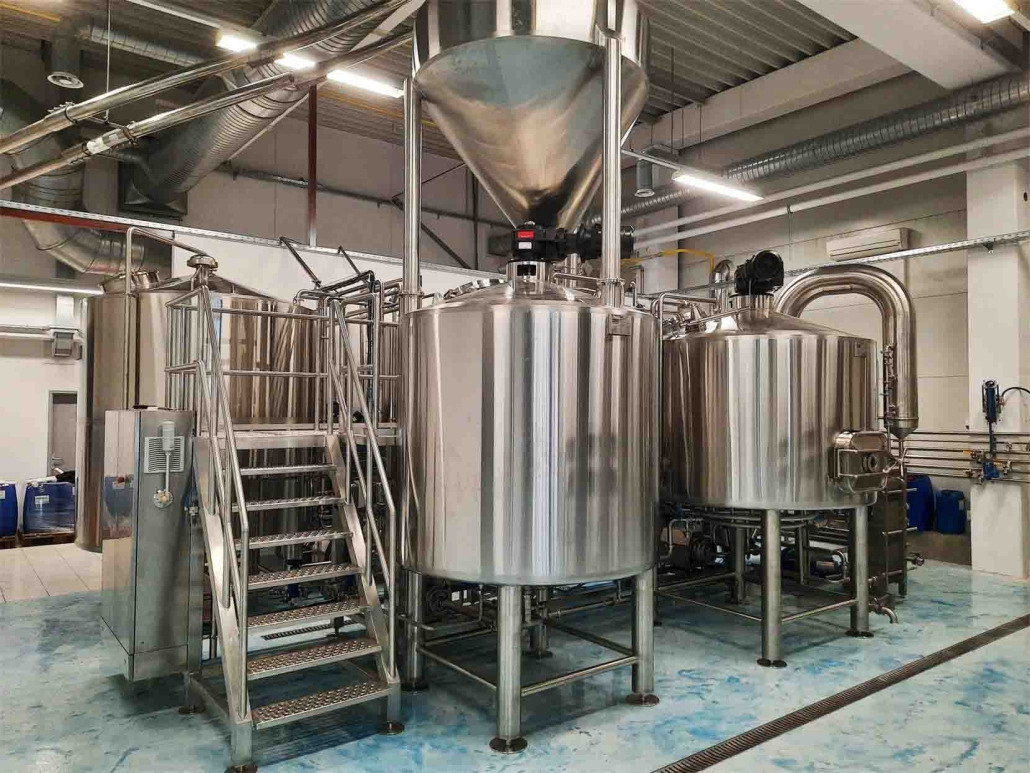
Troubleshooting Common Issues with Beer Fermenters
Fermentation Stalls
- Cause: Low temperatures, insufficient yeast pitching, or poor aeration.
- Solution: Maintain optimal temperature control and pitch the right amount of yeast.
Off-Flavors
- Cause: Contamination, temperature fluctuations, or poor cleaning practices.
- Solution: Regularly sanitize equipment and monitor temperature stability.
Excess Sediment
- Cause: Poor yeast flocculation or inadequate conditioning time.
- Solution: Use fining agents or extend the conditioning period.
Comparison of Equipment by Capacity, Space, and Design
Feature | Small-Scale Equipment | Medium-Scale Equipment | Large-Scale Equipment |
---|---|---|---|
Capacity | 5-50 gallons | 50-500 gallons | 500+ gallons |
Space Required | Compact, fits in small areas | Requires dedicated brewing room | Large brewing facilities needed |
Design | Simple, often manual controls | Semi-automated | Fully automated |
Customization | Limited | Moderate | High, tailored for specific needs |
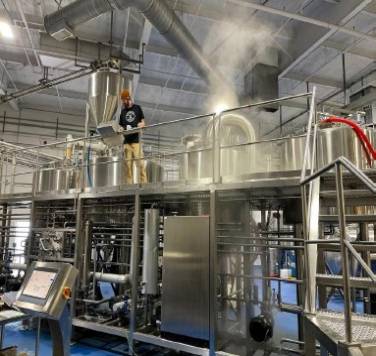
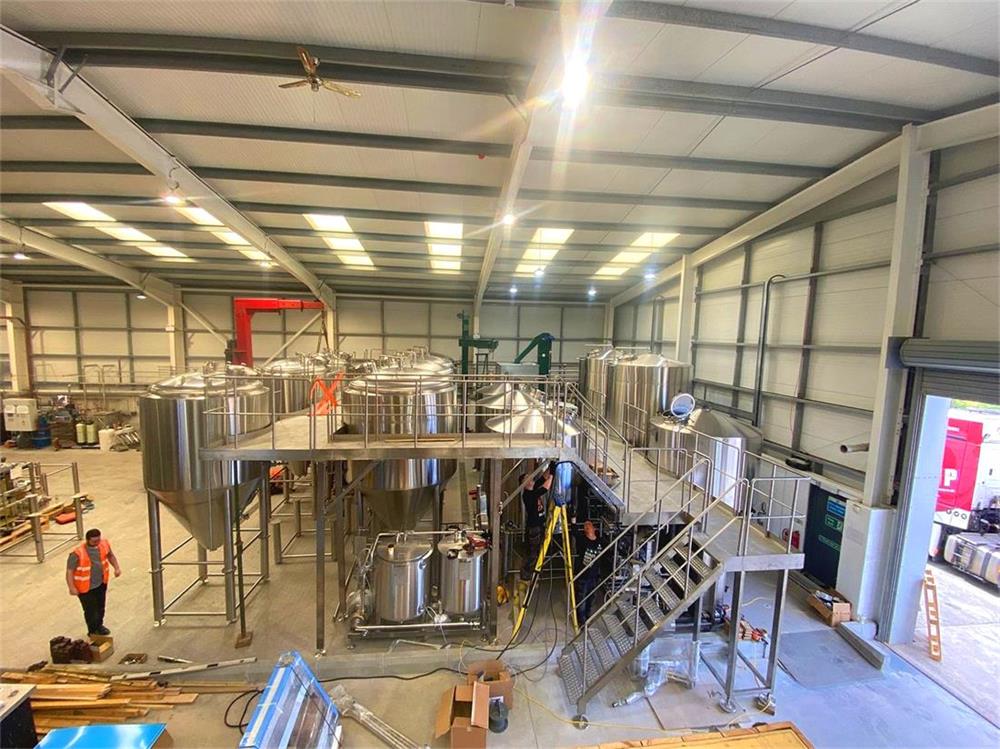
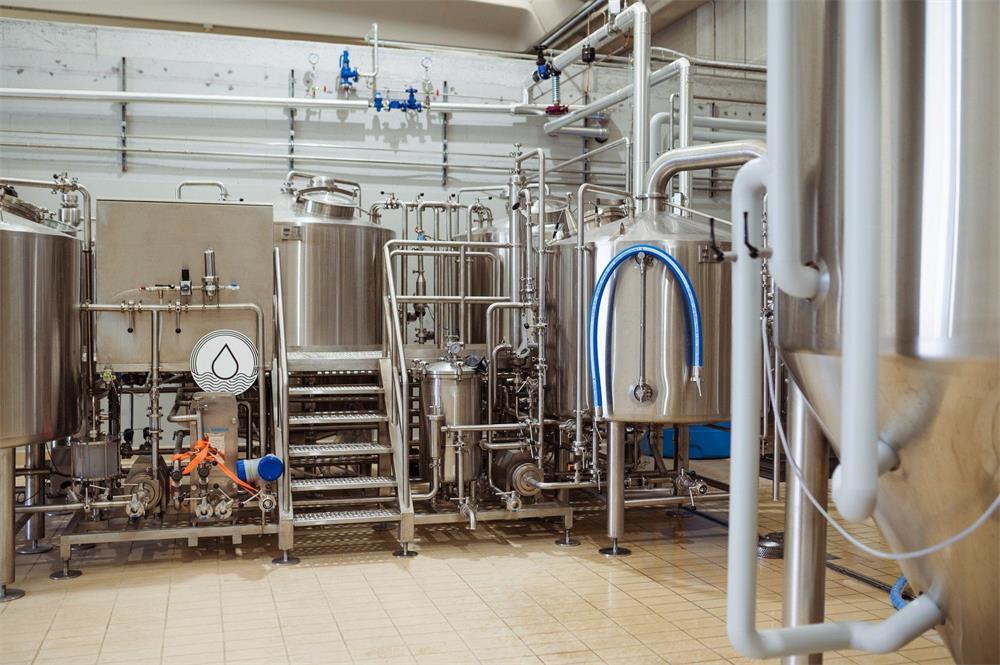
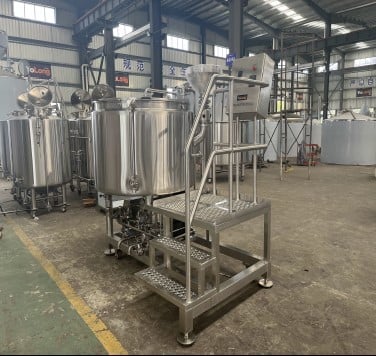
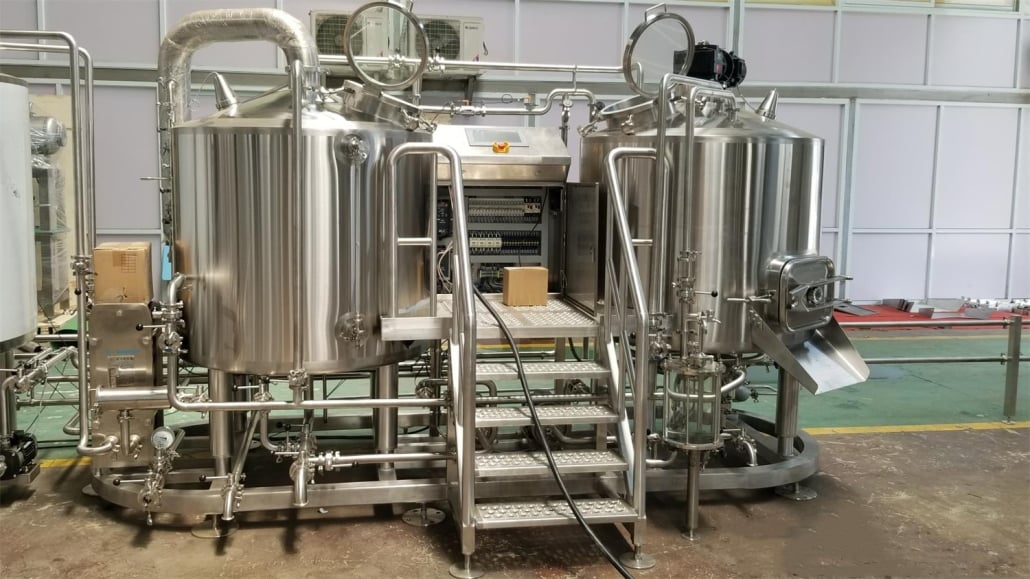
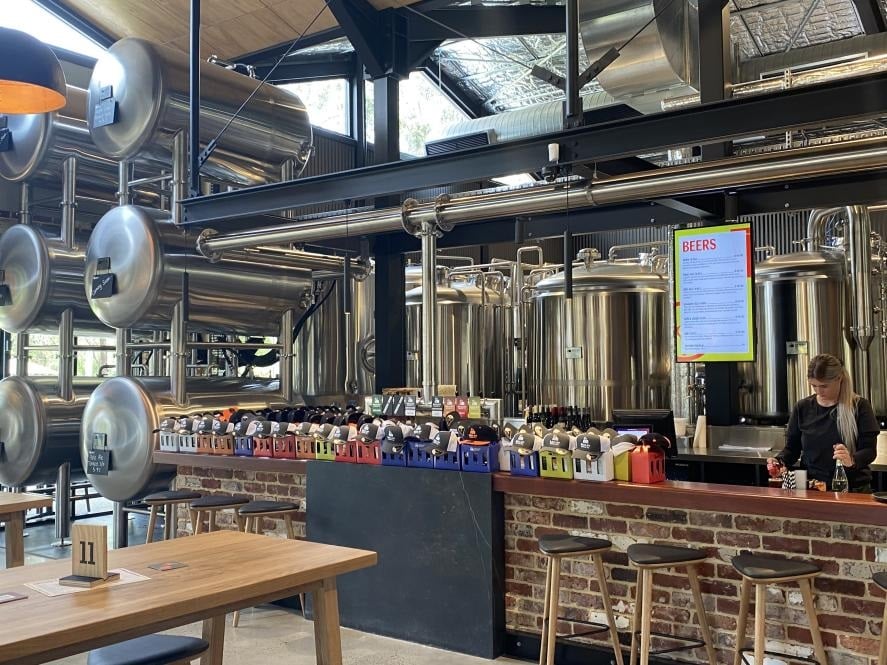
Suppliers and Price Ranges
Supplier | Equipment Offered | Price Range |
---|---|---|
BrewTech Solutions | Entry-level brewing systems | $1,000 – $10,000 |
ProBrew Systems | Medium-scale brewery setups | $10,000 – $100,000 |
MegaBrew Co. | Large-scale brewing equipment | $100,000 – $1,000,000+ |
Installation, Operation, and Maintenance
Aspect | Details |
---|---|
Installation | Professional installation ensures proper setup of plumbing, electrical, and ventilation systems. |
Operation | Adhere to manufacturer guidelines; monitor critical parameters like temperature and pressure. |
Maintenance | Regular cleaning, calibration, and inspections are essential for longevity and performance. |
How to Choose the Best Supplier
Factor | Details |
---|---|
Reputation | Check reviews, testimonials, and industry standing. |
Customization Options | Ensure the supplier offers tailored solutions to meet your needs. |
After-Sales Support | Look for comprehensive support, including warranties and maintenance services. |
Price Transparency | Request detailed quotes to avoid hidden costs. |
Delivery and Installation | Confirm shipping timelines and whether installation support is included. |
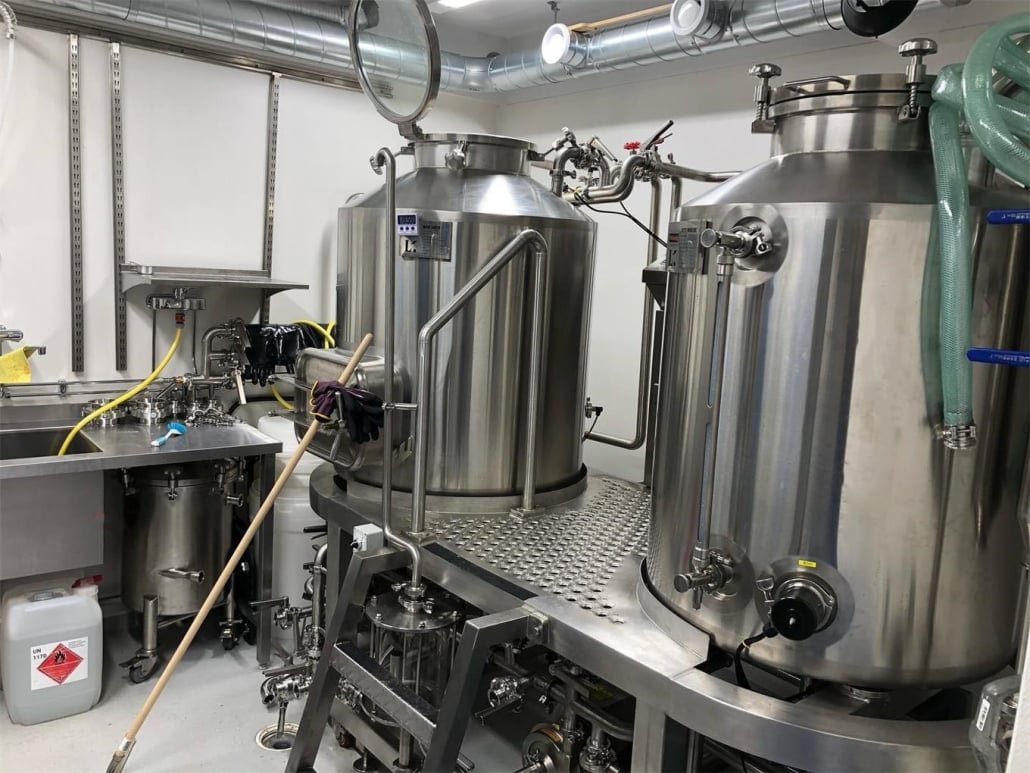
Advantages and Limitations of Professional Brewing Equipment
Aspect | Advantages | Limitations |
---|---|---|
Small Systems | Affordable, compact, great for pilot brewing | Limited production capacity |
Medium Systems | Ideal for growing breweries, balances cost and output | Requires more space and investment |
Large Systems | High capacity, automated, scalable | Expensive upfront costs, requires skilled operators |
FAQs
Question | Answer |
---|---|
What is the best material for brewing tanks? | Stainless steel is the industry standard for its durability and cleanliness. |
How do I clean professional brewing equipment? | Use brewery-grade cleaning agents like PBW and no-rinse sanitizers. |
What size system should I start with? | It depends on your production goals; small systems are ideal for startups. |
Can brewing equipment be customized? | Yes, many suppliers offer bespoke designs tailored to specific needs. |
How long does it take to install a system? | Installation times vary but generally range from a few days to several weeks. |