Vessel Brewhouse
Brewing beer is an art, and at the heart of this craft lies the vessel brewhouse, a fundamental piece of equipment that can make or break your brewing experience. Whether you’re a homebrewer dreaming big or a commercial brewery aiming to scale up, understanding the intricacies of a vessel brewhouse is crucial. In this guide, we’ll take you through every aspect of vessel brewhouses, from their purpose and equipment to brewing processes, customization, installation, and maintenance. So, grab your favorite pint, and let’s dive in!
What Is a Vessel Brewhouse?
A vessel brewhouse is the central component of any brewery, responsible for transforming raw ingredients into wort—the liquid that eventually becomes beer. It consists of a series of interconnected tanks and vessels, each performing a unique role in the brewing process. The term “vessel brewhouse” often refers to the collective equipment, which can include mash tuns, lauter tuns, brew kettles, and whirlpool tanks.
But why does this equipment matter? Imagine trying to bake bread without a proper oven—it just wouldn’t work. Similarly, the quality, design, and efficiency of your brewhouse dictate the consistency, flavor, and scalability of your beer production.
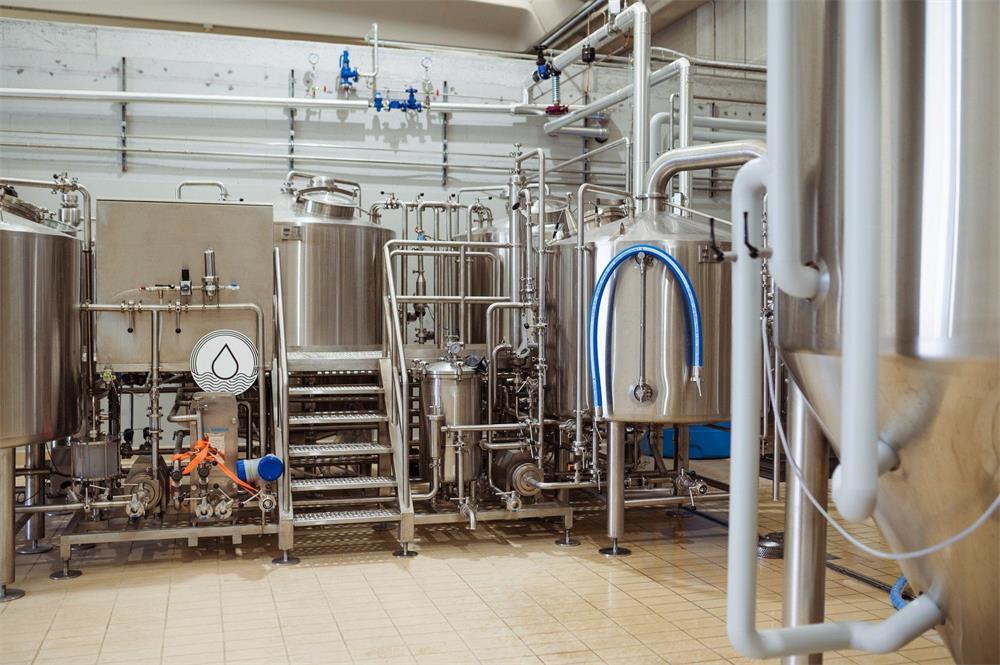
Key Equipment in a Vessel Brewhouse
Every vessel brewhouse shares a common set of equipment, though the specific configuration may vary based on the size and type of brewing operation. Here’s a breakdown of what you’ll typically find:
Equipment | Purpose | Common Features |
---|---|---|
Mash Tun | Where malted grains are mixed with water to convert starches into sugars (mashing). | Insulated tanks with precise temperature controls. |
Lauter Tun | Separates the liquid wort from the spent grains. | Features a false bottom or slotted plates for filtration. |
Brew Kettle | Boils the wort, sterilizing it and adding hops for bitterness, flavor, and aroma. | Often equipped with heating systems (direct fire, steam, or electric). |
Whirlpool Tank | Helps separate hop particles and trub from the wort before fermentation. | Designed with tangential inlets for efficient whirlpooling. |
Hot Liquor Tank | Stores and heats water used during the brewing process. | Ensures water is readily available at the desired temperature. |
Cold Liquor Tank | Provides chilled water for cooling wort post-boil. | Paired with heat exchangers for rapid cooling. |
Brewing Process in a Vessel Brewhouse
The brewing process in a vessel brewhouse can be likened to a symphony, with each instrument playing a vital role. Let’s walk through the steps:
1. Mashing
In the mash tun, crushed malt is combined with hot water. This step activates enzymes that convert starches into fermentable sugars. The result? A sugary liquid called wort.
2. Lautering
Next, the wort is separated from the spent grains in the lauter tun. This step ensures clarity and maximizes sugar extraction.
3. Boiling
The wort moves to the brew kettle, where it’s boiled to sterilize the liquid. Hops are added during this stage, contributing bitterness, flavor, and aroma.
4. Whirlpooling
In the whirlpool tank, the wort is spun rapidly, forcing unwanted solids to collect at the center, leaving a clean liquid ready for fermentation.
5. Cooling
The wort is cooled using a heat exchanger and cold liquor, bringing it to the optimal temperature for yeast pitching.
6. Fermentation
While not part of the brewhouse itself, fermentation tanks are where yeast converts sugars into alcohol and CO2, completing the transformation into beer.
Design, Layout, and Customization of Vessel Brewhouses
Choosing the right brewhouse depends on factors like available space, production volume, and your specific brewing goals. Here’s an overview of the customization options:
Parameter | Details |
---|---|
Capacity | Ranges from small-scale systems (1-10 barrels) for craft brewers to industrial setups (100+ barrels). |
Layout | Modular designs for compact spaces or sprawling configurations for larger facilities. |
Material | Typically stainless steel for durability, hygiene, and temperature control. |
Heating Method | Direct fire (cost-effective), electric (energy-efficient), or steam (ideal for scalability). |
Automation | Manual systems for hands-on brewers versus automated setups with precise controls and monitoring. |
Aesthetic Options | Polished stainless steel or custom finishes for a branded, professional look. |
Suppliers and Price Range for Vessel Brewhouses
Finding the right supplier can be as daunting as choosing the brewhouse itself. Here’s a snapshot of key suppliers and price ranges:
Supplier | Price Range | Specialization |
---|---|---|
ABC Brewing Systems | $20,000 – $200,000 | Small to mid-sized craft breweries. |
BrewTech Inc. | $50,000 – $500,000 | Industrial-scale systems with full automation. |
ProBrew Equipment | $25,000 – $250,000 | Customizable options for boutique breweries. |
China Brewhouse Co. | $10,000 – $150,000 | Affordable systems with competitive quality. |
Installation, Operation, and Maintenance of Vessel Brewhouses
A brewhouse is a significant investment, so proper installation, operation, and maintenance are non-negotiable.
Installation
- Ensure proper placement to optimize workflow and meet safety standards.
- Partner with professionals for piping, electrical, and heating setups.
Operation
- Familiarize yourself with the system’s control panels and standard operating procedures.
- Regularly monitor temperature, pressure, and flow rates to ensure consistency.
Maintenance
- Clean vessels thoroughly after each brew to prevent contamination.
- Perform regular inspections for wear and tear, especially on valves and seals.
- Schedule annual servicing with your supplier for long-term reliability.
How to Choose the Right Vessel Brewhouse Supplier
When selecting a supplier, consider these factors:
Criteria | Why It Matters |
---|---|
Reputation | Trusted suppliers with positive reviews ensure quality and support. |
Customization | A supplier who offers tailored solutions can better meet your unique brewing needs. |
After-Sales Service | Reliable support for installation, troubleshooting, and maintenance. |
Cost vs. Value | Balance affordability with features, durability, and scalability. |
Lead Time | Choose a supplier with reasonable delivery timelines to match your project schedule. |
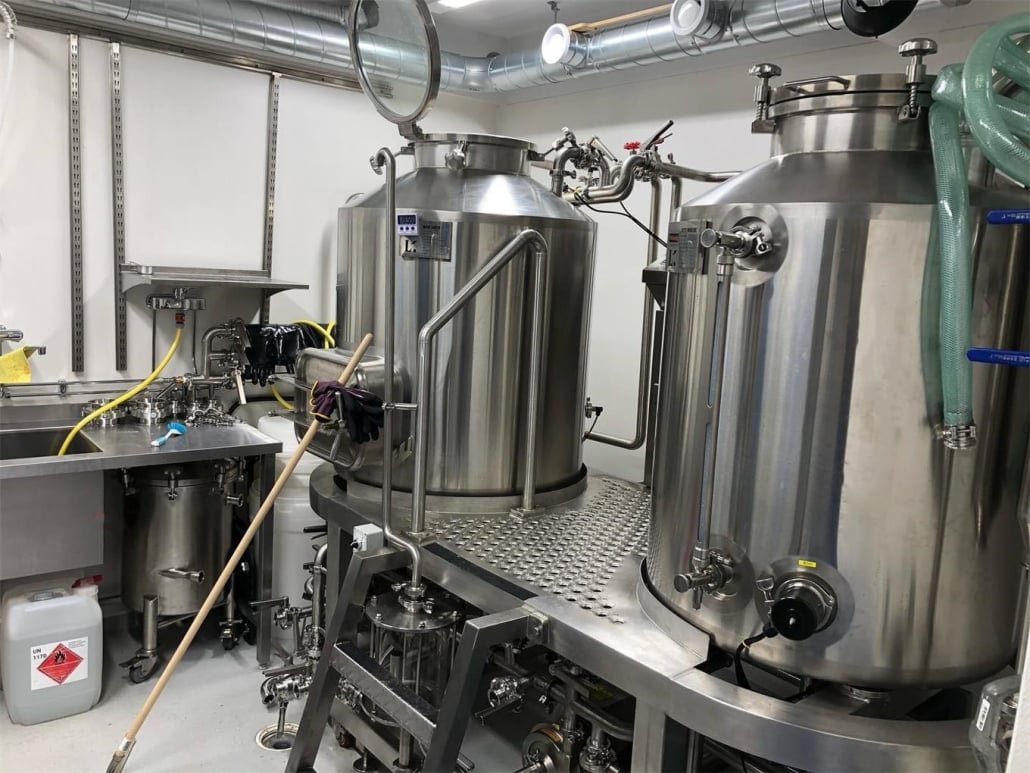
Advantages and Disadvantages of Vessel Brewhouses
To help you weigh your options, here’s a detailed comparison:
Aspect | Advantages | Disadvantages |
---|---|---|
Efficiency | Faster brewing cycles and consistent results. | Higher upfront costs for advanced systems. |
Customization | Tailored to specific production needs. | May require longer lead times for delivery. |
Scalability | Supports future expansion with modular designs. | Complex systems may require skilled operators. |
FAQs
Question | Answer |
---|---|
What is the typical lifespan of a brewhouse? | With proper maintenance, a quality vessel brewhouse can last 20-30 years or more. |
How much space do I need for a brewhouse? | Space requirements vary but plan for at least 150 sq. ft. for small setups and more for larger systems. |
Can I start with a small brewhouse and scale up? | Yes, modular designs allow for expansion as your production grows. |
What’s the best heating method for small breweries? | Electric heating is energy-efficient and cost-effective for small-scale operations. |
How do I clean a brewhouse? | Use a Clean-In-Place (CIP) system with caustic solutions and rinse thoroughly after every brew. |