3 BBL Brite Tank Beer Fermentation and Serving Tanks
A 3 BBL Brite Tank is a stainless steel vessel used for fermenting, filtering, carbonating, and serving beer in commercial breweries. With a capacity of 93 gallons or 352 liters, 3 BBL tanks are a popular size for small to mid-sized craft breweries producing ales and lagers on a 3-15 barrel brew system.
This guide covers everything needed to understand 3BBL brite tanks including design, layout, installation, suppliers, pricing, pros and cons, and typical brewery applications. It aims to help brewers compare options and make informed decisions when selecting 3BBL tank systems.
3 BBL Brite Tank Equipment Guide
Brite tanks, also called serving tanks or uni-tanks, perform multiple functions in the brewing process. The main equipment components of a 3BBL brite tank system are:
Equipment Type | Description |
---|---|
Tank Vessel | The primary stainless steel tank that holds beer during fermentation, clarification, carbonation and serving. Includes fittings for cleaning, transfers, monitoring. |
Glycol Cooling | Glycol chiller unit and coil/jacket to control fermentation temperature. |
CO2 Injection | CO2 regulator, stone, tubing for carbonation. |
Serving Components | Faucets, flow control, lines, couplers for direct draw dispensing to bar. |
Automation | Level sensors, pressure/flow meters, temperature probes, and controls. |
Filtration | Pump, filter housing, membranes, hoses for clarifying beer. |
CIP Components | Spray balls, piping, pumps, valves, tanks, chemicals for cleaning in place (CIP). |
Fermenter Stands | Custom floor stands, ladders, railings for safe access to tank manways and ports. |
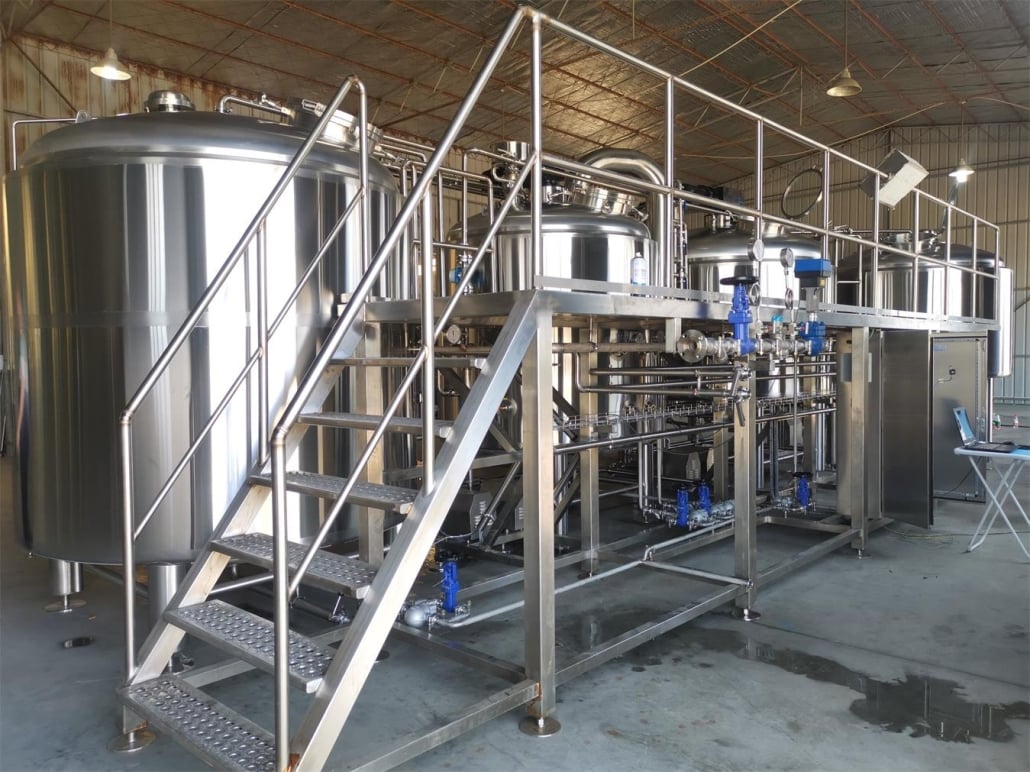
Typical 3 BBL Brite Tank Design and Layout
3BBL brite tanks come in horizontal and vertical stainless tank configurations. They may be fully custom built or ordered as complete engineered systems with integrated features and automation.
Parameter | Details |
---|---|
Orientation | Horizontal or Vertical stainless tank |
Shape | Cylindrical with elliptical, sloped, or cone bottom heads |
Material | Stainless steel – grade 304 or 316L |
Surface Finish | Interior polish: 150 grit or better (120 grit floor);<br>Exterior 2B Mill or better |
Manway | 12″-16″ diameter opening at top with camlock, sanitary clamp or bolted entrance |
Ports | 1.5″-2″ Tri-clamp fittings for temperature probes, CO2 injection, transfers |
Legs | Adjustable stainless steel legs – 6″ – 38″ height |
Jacket/Coil | Glycol cooling channels welded on exterior of tank or interior cooling coil |
Insulation | 1″-2″ thick spray foam |
Automation Package | Pumps, valves, sensors, controls in prewired portable or wall mount panel |
Serving System | Integrated under-tank draft components |
Typical dimensions for a 3 BBL uni-tank are 24″-36″ diameter x 48″-72″ straight side shell height. The total height increases to 78″-102″ including the domed top headspace. Weight is 350-700 lbs empty depending on material thickness.
Customization of 3BBL Tanks
Many custom options are available when ordering a 3BBL uni-tank:
Parameter | Customization Choices |
---|---|
Alloys | 304, 304L, 316, 316L stainless steel |
Thickness | 10 gauge, 12 gauge, 14 gauge |
Finish | Interior polish from 20 grit (coarse) to 180 grit (mirror)<br>Exterior polish from Scotchbrite to 8 mirror |
Port Quantity | Number, size, position and type of fittings |
Port Connections | Tri-clamp, threaded, flanged, butt weld |
Automation Extent | More sensors, pumps – personalized control logic |
Insulation Thickness | 1″-3″ thick spray foam insulation |
Cooling Design | Glycol jacket vs. cooling coil; cooling surface area |
Rectangular Chambers | Internals like cooling coils can be shaped |
Serving Setup | Number of faucets, flow control, drip tray, glass rinser |
With modular tanks, features like cooling, insulation, automation are handled through add-ons. Fully custom tanks allow the highest integration and optimization to meet specific brewery requirements.
Suppliers and Pricing
Many tank fabricators offer 3BBL brite tanks in stock or built to order. Pricing varies from $4,000 to $15,000 depending on the features and quality:
Supplier | Base Price Range |
---|---|
SS Brewtech | $4,000 – $6,000 |
MEP Engineering | $5,000 – $8,000 |
JV Northwest | $6,000 – $10,000 |
Psycho Brew | $8,000 – $12,000 |
ABS Commercial | $10,000 – $15,000 |
Customization, automation, shipping and installation costs extra. Get vendor quotes to compare pricing for the same tank configurations. China-made import tanks from Alibaba start under $3,000 but have higher risk. Quality USA and Canada-built tanks give the best ROI and resale value despite higher upfront cost. Consider full costs over the 15-20 year tank lifetime.
Installation Factors
Proper installation of 3 BBL brite tanks involves material handling, site prep, utilities, permitting and contractors.
Task | Installation Requirements |
---|---|
Receiving Tank | Forklift 4,000 lb capacity; pallet jack; lifting slings |
Location | Concrete floor; ceiling height; doorway width for entry |
Assembly | Leak test; interconnect piping, wires, glycol; calibration |
Electrical | 120V/20A circuit; disconnect box; outlets; wire runs |
Plumbing | Potable water line >15 GPM; floor drain; glycol supply/return |
Ventilation | Hood exhaust ducting; 500 CFM system |
Permits | Federal – brewer’s notice; state/county – boiler, hoods |
Use an experienced tank installer or in house operations team. Get engineering approval for customized platforms.
Standard Operating Procedures
Day to day operation of a 3 BBL brite tank involves fermentation, transfer, carbonation, filtration and cleaning cycles. Refer to the manufacturer’s instructions for safety warnings and specific procedures.
Activity | SOP Overview |
---|---|
Fermentation | Fill yeast-pitched wort; set glycol temperature profile; monitor density daily |
Beer Transfer | Open inlet/outlet valves; use CO2 or pump for closed transfers |
Force Carbonation | Set CO2 pressure to ~15 PSI based on temperature; rock tank |
Beer Filtration | Recirculate through 0.5 micron filter; confirm clarity |
Serving | Set serving pressure based on line length and size; check foam, taste |
CIP Cleaning | Mix caustic and acid solutions; clean spray balls, pumps; meet contact times |
The manufacturer, local brewers or master brewers groups can provide best practice recommendations for ideal fermentation, cellaring and serving. Join online forums for community advice too.
Maintenance Requirements
Preventative maintenance ensures safe operation, consistent quality, and maximum lifespan from 3BBL brite tanks.
System | Maintenance Tasks | Frequency |
---|---|---|
Gaskets | Inspect tank doorways and fittings; replace worn gaskets | Monthly |
Valves | Disassemble, clean and lubricate valves | Quarterly |
Sensors | Check calibration of level, pressure and temperature sensors | Quarterly |
Coil/Jacket | Inspect for leaks or damage; pressure test | Annually |
Pumps | Replace seals; lubricate; check impeller condition | Annually or per runtime hours |
Fittings | Verify tri-clamp torque; replace faulty fittings | As needed |
CO2 Regulator | Change internal cartridge; lubricate | Every 5 years |
Keep maintenance logs to track tasks, inventory parts, and plan capital upgrades.
Budget approximately 5% of the tank system cost per year for maintenance and repairs. Having backup stock of spare parts minimizes downtime if repairs are needed.
Choosing Brite Tank Suppliers
Many factors go into choosing the right 3BBL brite tank provider for your brewery:
Consideration | Evaluation Criteria |
---|---|
Budget | Compare vendor quotes; define must-have features |
Lead Time | Production schedule: days to weeks from order to delivery |
Customization | Ability to tailor tank design and automation to brewery preferences |
Construction | Welds, fittings, surface finish – indicators of quality |
Warranties | Coverage duration for tank, glycol unit, other components |
References | Check reviews and testimonials from past customers |
Customer Service | Responsive sales and technical support team |
Get free design quotes from 3-5 suppliers before down selecting. Arrange on-site visits to existing tank installations for other local breweries if possible.
Comparing 3 BBL Brite Tank Options
All 3 BBL uni-tanks are not made equal. Use the following criteria to critically evaluate options from different vendors:
Advantages of 3 BBL Brite Tanks
- Flexible multi-purpose fermentation, filtering, serving, storage
- Large enough for commercial batches; fits through 36″ doorways
- Scalable tank capacity for growing craft breweries
- Cost effective and energy efficient compared to 1 or 7+ BBL sizes
- Pre-engineered systems quick to install; customizable designs
- Rugged stainless steel easy to maintain and long lifespan
- Optional automation simplifies operations
Disadvantages & Challenges
- Too small for mass production; difficult to fully automate
- Mobile serving tanks don’t suit fixed draught line installations
- Shorter vessels prone to foaming with high carbonation beers
- Quality issues reported with China import tanks
- Budget custom builds can lack engineering rigor
- Glycol jackets less efficient than interior cooling coils
- Difficult access for stirring yeast during fermentation
Engineered brite tanks balance functionality, efficiency, economics, and ease of use for the projected production scale and brewing needs. Carefully evaluate options before ordering.
Typical Brewery Applications
3 BBL brite tanks have the right capacity for a number of beer production applications:
Application | Details |
---|---|
Taproom Serving | 1 to 3 tanks for ales, lagers, and specialties support a small tasting room |
Pilot Brewery | Test recipes; educate brewers; support 3-5 BBL brewhouse |
Retail Brewpub | Serve guest beers alongside 500-1500 BBL/year capacity |
Barrel-Aged | Extended wood aging under pressure transfers to brite tank at finish |
Quality Lab | Frequent yeast harvesting; propagate pure cultures; QC testing |
R&D Center | Innovate recipes on 3 BBL before scaling up batches |
Choose vertical or horizontal tanks to best fit brewhouse layout, cellar height, and serving logistic needs. Glycol cooling offers more stable temperature control than jacketed fermenters. Get a chiller unit sized 30-50% beyond tank capacity for faster ramp down during peak summer heat.
Automate tank cleaning and closed transfers where possible to improve efficiency. Consider mobile serving options today that can convert to fixed draft lines later as business grows.
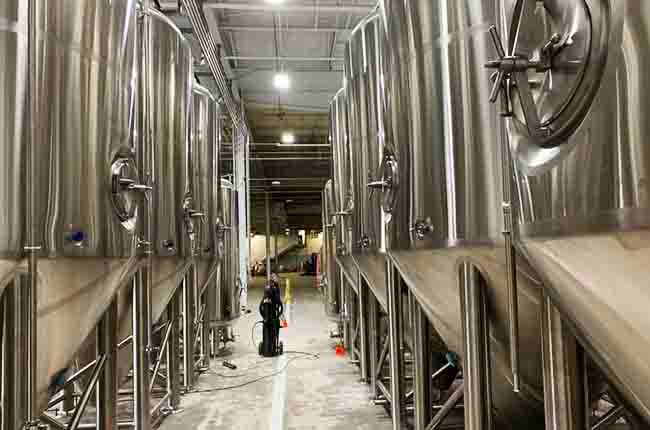
FAQ
Q: What size brewery is a 3BBL brite tank suited for?
A: A 3BBL unitank fits best in a small to medium craft brewery producing 150-1000 barrels per year on a 3-15 BBL brewhouse. The capacity matches well for scaling test batches to full production or serving taproom favorites.
Q: How many 3BBL tanks are needed to supply a taproom?
A: We recommend a minimum of 2 brite tanks – one serving beer while the second cleans and sanitizes. An additional 1-2 units allows you to ferment, filter and carb ales and lagers simultaneously for more variety.
Q: Should I choose a vertically or horizontally oriented brite tank?
A: It depends on your goals and constraints – vertical tanks fit in more cellar layouts but horizontal tanks allow easier cleaning and access. Both work well once properly designed and configured.
Q: What design customizations make the most difference?
A: Focus customizations on features that truly impact production quality and efficiency based on your specific beer types and business model. Glycol cooling, yeast harvesting, flexible fermentation and streamlined cleaning automation are common choices to differentiate tanks.
Q: Should I buy Chinese import tanks to save money initially?
A: Import tanks can have quality issues and little vendor support. Carefully evaluate construction, warranty and total cost of ownership vs. benefits. For critical production equipment, reputable North American suppliers generally make the best long term investment.