Overview of 20 BBL Brewhouse
A 20 barrel (BBL) brewhouse is a medium-sized professional beer brewing system with a capacity to produce 20 barrels of beer per batch. This system is commonly used by microbreweries and brewpubs to efficiently produce craft beer on a commercial scale.
With a 20 BBL capacity, this brewhouse can output around 310-420 gallons per batch, or approximately 620-840 gallons per brew day. This allows an estimated annual production volume between 3,000-10,000 BBLs depending on the number of batches brewed per week. The flexibility of a 20 BBL brewhouse makes it suitable for expanding small breweries aiming to grow production and distribution.
20 BBL Brewhouse Equipment Guide
The 20 BBL brewhouse system consists of several key components for mashing, lautering, boiling, whirlpooling, cooling, and fermenting beer. Here is an overview of the equipment:
Equipment | Description |
---|---|
Mash tun | Stainless steel vessel where the milled grains are mixed with hot water to convert starch into fermentable sugars. Common size is 20 BBL. |
Lauter tun | Separates sweet wort from grains. Usually combined with the mash tun in a brew-in-a-bag system. |
Kettle | Boils the wort with hops for flavor and preservation. Typically 20-30 BBL capacity. |
Whirlpool | SEPARATOR to remove hops and coagulated proteins after boiling using a spinning motion. |
Heat exchanger | Cools down hot wort quickly before fermentation. Plate or tubular style. |
Fermenters | Stainless steel, cone bottom tanks where yeast ferments the wort into beer. Multiple 20 BBL units. |
Brite tanks | Pressurized vessels for carbonating, clarifying and storing finished beer. ≥20 BBL capacity. |
Piping | Plumbing connects all vessels for transferring liquids. Manual or automated. |
Control panel | Controls temperatures and timing of key processes. Can be manual or computerized. |
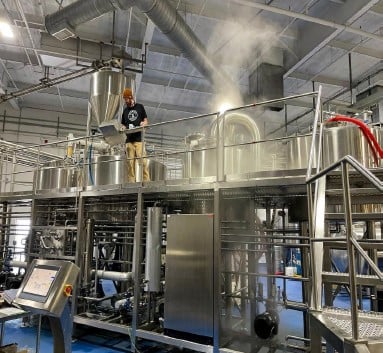
Types of 20 BBL Brewhouse Systems
20 BBL brewhouse systems are available in different configurations and price ranges to suit unique production goals:
Type | Description | |
---|---|---|
Traditional brewery | Has separate mash tun and lauter tun for mashing and lautering. More manual operation but better efficiency. | |
Brewpub brewhouse | Compact 3-vessel gravity flow system with combined mash/lauter tun. Lower cost, easy to use. | |
Steam brewery | Uses steam heating instead of direct fire. Consistent, efficient, eco-friendly. | |
Electric brewhouse | Heated by electricity instead of gas or steam. Precise control, operational flexibility. | |
Automated system | Highly computerized operation with more hands-off functionality. | |
Custom fabrication | Tailored system designed for specific space, capacity or vision requirements. | \ |
20 BBL Brewhouse Brewing Process
The typical brewing process in a 20 BBL brewhouse consists of these basic steps performed in stainless steel vessels:
- Milling – The grains are coarsely cracked by a mill to expose starches.
- Mashing – The milled grain is mixed with hot water in the mash tun and held for 1-2 hours at 150-160°F to convert starches into fermentable sugars. The result is sweet wort.
- Lautering – The grain particles are separated from the sweet wort which contains the sugar. The sweet wort is sent to the brew kettle.
- Boiling – The wort is boiled vigorously with hops for 1-2 hours to extract flavors, aromas and bitterness. Coagulated proteins form a removable hot break.
- Whirlpooling – The hot wort is circulated to create a whirlpool effect separting the clear wort from the hop debris and precipitated proteins.
- Cooling – The protein-free hopped wort passes through a plate heat exchanger bringing it down to yeast pitching temperature, around 45-65°F.
- Fermenting – The cooled wort is aerated and pitched with yeast in fermenters. Yeast converts sugars into alcohol and CO2 over 1-3 weeks at 45-68°F.
- Maturation – The young beer is conditioned for clarity and flavor in bright beer tanks before packaging.
20 BBL Brewhouse Design and Layout
A 20 BBL brewhouse requires careful equipment sizing, facility layout and production planning. Here are key considerations:
Facility Size and Layout
Parameter | Details |
---|---|
Space requirement | Approximately 2500-5000 sq ft |
Floor area | Enough space for all vessels, spacing for operations and maintenance access |
Ceiling height | ≥ 18 feet height to accommodate tall vessels |
Layout | Logical sequential flow between processes. Linear side-to-side or compact multi-level. |
Expansion | Space to add more fermenters, brite tanks, production capacity in the future |
Tasting room | Can be incorporated for taproom sales |
Offices, storage, restrooms etc. | Support areas as required |
Production Volume and Capacity
Details | Recommendations |
---|---|
Batch size | 20 BBL main brew length |
Batches per week | 1-5 depending on production targets |
Peak output | Up to 10,000 BBLs annually if maximizing capacity |
Fermenter and brite tank qty and size | ≥ 4x 20 BBL fermenters <br> ≥ 2x 20 BBL brite tanks |
Flexibility and Customization
A 20 BBL brewhouse offers flexibility for customization:
- Mash filters or traditional lauter tun
- Direct fire or steam heating
- Electric or automation upgrades
- Layout and spacing for easy operation
- Raw material handling systems
- CIP capabilities and waste handling
- Labeling, milling or packaging integration
Within infrastructure constraints, brewers can select options to suit their workflow, efficiency goals, beer styles and future growth plans.
20 BBL Brewhouse Suppliers and Pricing
Many brewhouse manufacturers offer well-engineered turnkey 20 BBL systems. Here is a comparison of popular suppliers and price indications:
Supplier | Price Range | Offerings |
---|---|---|
Specific Mechanical | $250,000 – $500,000 | Custom US-made systems |
Premier Stainless | $200,000 – $350,000 | Budget to highend systems |
Portland Kettleworks | $180,000 – $280,000 | Innovative kettles |
JVNW | $250,000 – $400,000 | Planning to packaging |
AAA Metal Fabrication | $220,000 – $380,000 | Custom fabrication |
American Beer Equipment | $190,000 – $320,000 | Smart electric brewhouses |
Pricing can vary widely depending on the features, customization, automation and optional accessories chosen. Allow 15-20% additional for installation, shipping, peripheral equipment etc. Leasing programs are also available to spread out capital investment over 5+ years.
20 BBL Brewhouse Installation, Operation and Maintenance
Setting up a 20 BBL brewhouse has technical requirements – work with an experienced mechanical contractor.
Stage | Details |
---|---|
Installation | Proper assembly, welding, insulation, plumbing, wiring by qualified professionals |
Commissioning | Testing vessels at pressure, tuning process flow, control parameters and safety features. |
Initial operation | Producing test batches to validate quality and consistency before full production. |
Ongoing operation | Following SOPs for each process stage, tracking fermentation, monitoring quality. |
Maintenance | Daily and weekly cleaning and sanitizing procedures, preventative maintenance as per manufacturers’ recommendations. |
Have brewery technicians and operators get hands-on equipment training for startup and optimize processes until beer quality targets are achieved.
How to Select a 20 BBL Brewhouse Supplier
Choosing the right 20 BBL brewhouse supplier is key to seamless project execution. Below are the main factors brewers evaluate:
Criteria | Considerations |
---|---|
Reputation and experience | Proven track record, customer reviews, case studies for systems of similar capacity |
Equipment quality | High-grade stainless steel vessels and parts, precise fabrication, durable |
Specialization expertise | Extensive knowledge guidance for commercial 20 BBL system requirements |
Customization capabilities | Flexibility to tailor the system layout, accessories, controls etc |
Service and support | Responsive pre-sales expertise. Post-sales for troubleshooting issues |
Advantages and Limitations of 20 BBL Brewhouse
The 20 BBL brewhouse system offers unique pros and cons compared to smaller homebrew-sized or larger 60+ BBL commercial systems:
Advantages
- Medium batch size balances production volume and hands-on control
- Flexible output levels from a few hundred to thousands of barrels per year
- Lower capital investment than very large capacity systems
- Handles wider variety of beer styles and innovations
- Intimate brewhouse allows meticulous attention to quality
- Supports small business why providing operating efficiencies
Limitations
- Requires significant upfront financial commitment
- Batch size limits very high volume production
- More manual labor than highly automated systems
- Restricted quantity for mass distribution outside local region
- Space and infrastructure needs are still demanding
Within their production sweet spot, 20 BBL brewhouses successfully blend capacity, flexibility and quality for professional craft breweries.
Comparing Electric vs Direct Fire 20 BBL Brewhouses
Brewers choose between electric or direct gas-fired brewhouse heating options by comparing pros and cons:
Criterion | Electric Brewhouse | Direct Fire Brewhouse |
---|---|---|
Initial cost | Higher equipment cost | Lower equipment cost |
Operating costs | Lower energy bills | Higher gas bills |
Process control | Very precise temperature modulation | Some variability batch to batch |
Efficiency | Excellent thermal efficiency | Lower efficiency |
Safety | No open flames or gas line risks | Fire risk if not properly installed |
Electric brewhouses provide modern advantages, while direct fire units are more traditional. Brewmasters select fuel source based on production goals, budgets and safety preferences.
FAQs
What does 20 BBL mean?
20 BBL stands for 20 barrel brewhouse. A barrel is a standard brewing measure equal to 31 US gallons. So 20 BBL = 620 gallons per batch.
What size brewery uses a 20 BBL system?
A 20 barrel brewhouse is typically used by microbreweries and brewpubs producing 300-30,000 barrels per year. At maximum capacity, it can output around 10,000 barrels annually.
How much beer can you produce with a 20 BBL brewhouse?
Operating 1-5 batches weekly, annual production with a 20 BBL system can range realistically between 1,000-10,000 barrels of beer. Efficiency and production schedule determine exact volumes.
How much does a 20 BBL brewhouse cost?
A new 20 BBL brewhouse system usually costs $180,000 to $500,000 depending on the configuration – with an average price around $300,000. Additional costs apply for shipping, installation, peripherals.
What is the difference between a 10 BBL and 20 BBL brewhouse?
- Batch volume – 10bbl makes 155 gallons per batch, 20bbl makes 310 gallons per batch
- Annual production – 10bbl lower; 20bbl can produce up to 10,000bbls
- Vessel size – 20bbl has larger mash tun, kettle etc.
- Cost – 20bbl system has higher equipment cost
So a 20 BBL system has double the capacity and output potential compared to a 10 BBL brewhouse.