15 BBL brewing equipment
Overview of 15 BBL brewing equipment
A 15 BBL brewing equipment allows medium-large craft breweries to scale up annual production between 5000 to 10,000 barrels while retaining flexibility for specialty small batches.
With a brewhouse batch capacity of 31 gallons x 15 = 465 gallons or 1554 liters per brew, 15 BBL configurations suit taproom brewpubs graduating beyond 10 BBL as well as smaller regional production facilities.
These automated stainless steel brewhouses represent a sizable investment between $900,000 to $1.8 million installed but deliver higher output volume and efficiencies. Their strategic batch size bridges production gaps between mid-sized 10 BBL and larger 30 BBL mega-breweries.
This guide provides a detailed analysis of 15 BBL professional brewing technology – covering equipment configurations, sizing calculations, layouts, customization options, pricing, supplier selection criteria, operations best practices, pros and cons, and expert recommendations.
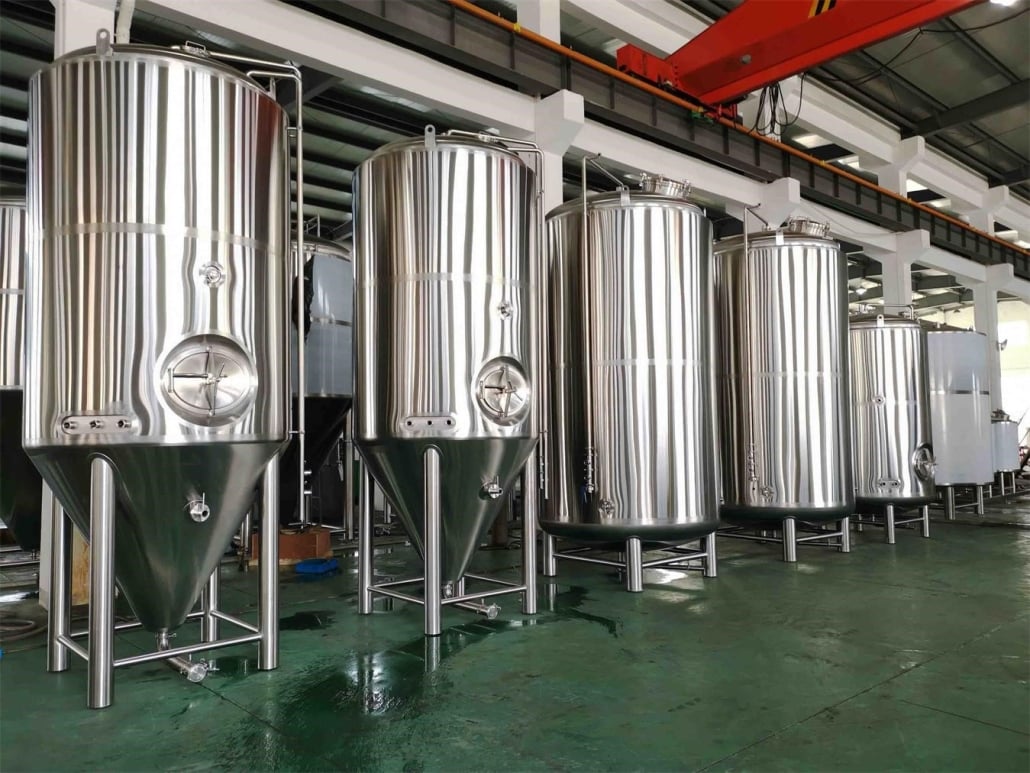
Types of 15 BBL brewing equipment
15 BBL brewhouses are available in 4-vessel and 3-vessel configurations from leading brewery equipment manufacturers:
4-Vessel Brewhouses
With separate hot liquor tank, mash tun, lauter tun and brew kettle vessels connected via transfer pipes and pumps.
Advantages: Traditional process, flexibility for complex recipes
Disadvantages: Larger footprint, more manual operations
3-Vessel Brewhouses
Combine mashing and lautering functions into one vessel. More compact layout.
Advantages: Lower cost, smaller footprint
Disadvantages: Restrictions on specialty ingredients
Type | Number of Vessels | Automation Level |
---|---|---|
4-Vessel | Hot Liquor Tank + Mash Tun + Lauter Tun + Kettle | Medium |
3-Vessel | Mash/Lauter Tun + Kettle (+ Whirlpool) | High |
Within these configurations, additional options include multi-stage mash filters, internal/external calandria boiling systems, whirlpool settlers, yeast propagators, steam generators etc. – all customizable to balance functionality, degree of automation and budget.
15 BBL brewing equipment Batch Size and Capacity
The “15 barrel” denomination refers to a single completed batch volume capacity. One beer barrel = 31 US gallons.
So 15 barrel systems allow brewing 15 x 31 = 465 gallons per full brewing cycle from mashing to boiling, cooling and fermentation.
In practical annual production terms:
- Max brews per week: 4 to 5
- Annual beer output at 80% utilization: 7500 to 10,000 barrels
- Actual yield per 15 BBL batch after losses: 400 gallons, or 1500 liters
- Sellable case equivalent per batch at 355ml/bottle: 570 cases
- Fermentation tank capacity needed: Up to 30 BBL, or 4x batch size
For a taproom restaurant pairing, this matches daily draft consumption of 300 liters while allowing distribution growth. Larger brewpubs may consider dual 15 BBL systems for peak demand. For production breweries targeting 20,000 barrels yearly, installing multiple units allows staggered brewing cycles.
15 BBL brewing equipment Design and Layout Considerations
Constructing or upgrading facilities for 15 BBL professional brewing equipment involves many infrastructure factors:
Height: 30 ft floor to ceiling for overhead clearance of tanks, pipes, mezzanines, cranes
Flooring: Reinforced concrete floor graded for drainage, HACCP compliant
Power: 480V, 3-phase electrical supply with 400 amp+ capacity for heating elements
Water: 1.5 inch diameter supply lines for high flow hydraulic demands
Steam: Clean steam generator and piping for heating mash tuns
Cooling: Glycol chilling with supply and return manifold connections
Ventilation: Humidity, fume and odor control systems
Safety: Chemical storage compliance, emergency eyewash stations
Ancillary: Adjacent cold storage, water treatment, boiler and compressor rooms
Expansion: Floor space for doubling batch capacity over 5 year growth
In terms of optimal brewhouse layout design:
- Grain handling and raw material receiving bay near mash tun inlet
- Ergonomic work triangles allowing single operator movement between vessels
- Gravity flows utilized before pump transfers where possible
- Services access underneath vessels without confined spaces
- Utilities, electrical, drains planned for maintenance access
- Quality lab and control room visibility across equipment
- Open architecture allows modular expansion
- Restaurant/tasting room aesthetic views of brewery
There are significant construction planning interdependencies between brewhouse capabilities, building engineering constraints, production growth plans and budget. Experienced brewery design consultants manage these complex tradeoffs from end-to-end.
Customization Options for 15 BBL brewing equipment
While turnkey templates allow faster commissioning, 15 BBL breweries involve considerable customization during design stages:
Parameter | Customization Choices |
---|---|
Batch Volume | 10 BBL, 15 BBL, 20 BBL, 30 BBL |
Vessel Fabrication | Stainless grade, thickness, finish |
Equipment Mix | More vessels, mash filters, whirlpools etc. |
Levels of Automation | GMP sensors, automated valves, programmable controls |
Piping | Custom manifold arrangements |
Heating Options | Electric, steam, gas |
Cooling Design | Glycol, chilled water, combined |
Media | Find tuning for water mineralization etc |
CIP System | Spray balls, SIP connections |
Safety | Pressure relief valves, emergency stops |
Eco-efficiency | Heat reclaim, solar renewable integration |
Motivations for above customizations include:
- Innovation: Specialized vessels for new beer types and flavors
- Flexibility: Enable wider variety of recipes with finer control
- Performance: Faster heating, cooling and brew lengths
- Automation: Reduce repetitive manual work, increase consistency
- Yields: Maximize extract efficiency, minimize losses
- Quality: Precise control of mash pH, temperatures and transfers
- Ergonomics: Easier lifting, movement and operations access
- Future-proofing: Built-in capability to add modular functions
Overall the aim is optimizing productivity, beer taste consistency, equipment longevity and safety – while staying on budget.
Selecting 15 BBL brewing equipment Manufacturers and Suppliers
Finding qualified brewhouse engineering contractors as business partners ensures successful budgeting, design, project coordination and after-sales support for customized 15 BBL systems:
Parameter | Vendor Evaluation Criteria |
---|---|
Core Competency | Number of years focused on brewhouses |
Client Portfolio | Case studies of systems delivered |
Vendor References | Testimonials from existing customers |
Technical Expertise | In-house engineering capabilities |
Customization Skills | Fabricator partnerships for made-to-order |
Industry Activity | Memberships in trade associations |
Thought Leadership | Speaking sessions, published articles |
Business Transparency | Clear contact info and ownership info |
Project Methodology | Defined design, build and support stages |
Warranties | Equipment defect, performance coverage terms |
Post-sales Support | Response time, remote troubleshooting |
Additional considerations are staging progress payments instead of full upfront deposits, including performance testing criteria, visiting existing sites for product quality, and getting operator references on ease of use.
It is also important to understand modular expansion capabilities for future production growth in the overall solution space. A strong long-term brewhouse partner brings both strategic project management and engineering specialization across vessels, valves, automation, controls, fermentation, cleaning and ongoing optimizations.
Pricing and Cost Analysis of 15 BBL brewing equipment
A turnkey 15 BBL brewhouse represents $900,000 to $1.8 million in capital equipment investment installed, with ongoing operating expenses estimated between $150 to $350 per barrel yearly.
Breaking this down:
Equipment | Price Range |
---|---|
Core Brewhouse | $550,000 to $1.2 million |
Ancillary Systems | $150,000 to $300,000 |
Commissioning Services | $150,000 to $200,000 |
Facilities Upgrade | $150,000+ |
Total Installed Cost | $1 million to $1.8 million |
Core Brewhouse
This covers stainless steel brewing vessels for mashing, lautering, boiling and whirlpooling, interconnecting pipes, valves, pumps, motors, automation programming, control panels and sensor instrumentation.
A basic 3-vessel 15 BBL brewhouse starts around $550,000 versus $1.2 million for a sophisticated 4-vessel brewing system with advanced automation.
Ancillary Systems
Additional production infrastructure like fermentation tanks, brite tanks, reverse osmosis water treatment, CIP systems, compressed air, chilling systems, granular media handling and storage etc.
Commissioning Services
Expert integration assistance for equipment installation wiring, piping, safety compliance, software configuration, trial brew runs and staff training.
Facilities
Potential upgrades to flooring, mezzanines, drainage, electric service, glycol piping, ventilation etc to meet brewhouse operation requirements.
With good design, operations best practices and preventive maintenance, 15 BBL hardware should deliver consistent production with 5+ years lifespan. Thereafter upgraded equipment may be warranted to support growth to 30 BBL batches. We next examine the staffing, utilities, operational and maintenance factors influencing utilization, quality, revenues and profitability.
Operating 15 BBL brewing equipment
Successfully operating 15 BBL commercial beer equipment requires skilled personnel and robust processes focused on safety, consistency and peak equipment effectiveness:
Staffing: 15 BBL brewhouses perform well with 4 to 5 trained operational personnel – allowing for staggered shift rotations.
Utilities: Continuous supply of electricity, water, steam and compressed air with redundancy. Glycol chilling precision enables ideal fermentation temperatures.
Maintenance: Weekly and monthly preventative maintenance as per OEM guidelines including calibrations, lubrications and spare parts inventory.
Monitoring: Automated sensors and data capture for temperature, pH, density, valve status at every stage into brewing software for analytics.
Safety: Guard rails on platforms, emergency stop circuits, audible and visible alarms, safety interlocks on valves and motor starters. Staff training drills.
Optimization: Software guided process tuning for managing yields via adjunct addition rates, sparging rinse parameters, wort aeration, media adjustments.
Consistency: Documented recipes, batch records and standard operating procedures enforced by brewmasters during every brew.
Cleaning: Caustic and acid based CIP protocols between batches maintained rigorously including tanks, filters, pipes etc to prevent contamination and maximize longevity.
While equipment scale up from smaller pilot breweries is exciting, putting detailed SOPs and quality systems first is critical before pursuing rapid growth. Working with a brewhouse engineering partner helps establish processes at start rather than reactively fixing issues. Training staff both on initial usage and continuous learning enables leveraging the full multi-year lifespan of stainless equipment.
How to Choose Between 15 BBL brewing equipment Manufacturers
Bidding evaluations on customized 15 BBL brewhouse systems involve subjective judgments across technical parameters, services and intangible trust factors:
Use this impartial weighted ranking matrix to score competing proposals:
Weight | Mfr 1 | Mfr 2 | Mfr 3 | |
---|---|---|---|---|
Equipment Pricing | 25% | Score | Score | Score |
Customization Range | 15% | Score | Score | Score |
Lead Time | 10% | Score | Score | Score |
Build Quality and Safety | 20% | Score | Score | Score |
Installation Services | 10% | Score | Score | Score |
Ongoing Support | 15% | Score | Score | Score |
Overall Reputation | 5% | Score | Score | Score |
Weighted Total Score | 100% | – | – | – |
For each criteria:
- Allocate weight as a % based on importance priorities
- Rate each manufacturer from 1 to 10 on meeting requirements
- Objectively assess weighted score totals
Intangibles like brewhouse design innovation, operator ergonomics and user experience still influence decisions. Visiting existing installations first-hand adds insights on service relationships beyond brochures.
While upfront capital outlay dominates decision making, target 5+ year utilization via flexibility, quality, yield optimizing features and expert support services. This holistic lifecycle approach minimizes overall beer cost per barrel.
Pros and Cons of Investing in 15 BBL brewing equipment
Understanding the technical and operational tradeoffs helps set pragmatic expectations when upgrading production capacity:
Pros
- Scalable batch size maximizes annual beer output
- Faster cycle times increase revenue potential
- Improved automation enhances process control
- Lower price per barrel compared to smaller systems
- Builds brand distribution beyond taprooms
- Match capacity for many full-service restaurants
- Efficient bridge between 10 BBL and 30 BBL scales
- Draw tourists with visual brewing theater
- Optional add-on malting system
- Supports wider variety of beer types
Cons
- Large capital expenditure budget needs justification
- Increased sales and promotion costs
- Additional regulations and tax overhead
- Needs continuous utility supply chains
- Staffing challenges to find skilled operators
- Infrastructure upgrades likely required
- Unique customization can increase project timelines
- Restricted flexibility in some pre-built templates
- Equipment ROI horizon above 3 years
Aligning brewhouse capabilities with restaurant pairing demand forecasts, production schedules, brand positioning and staff capabilities allows mitigating typical mid-sized brewery challenges.
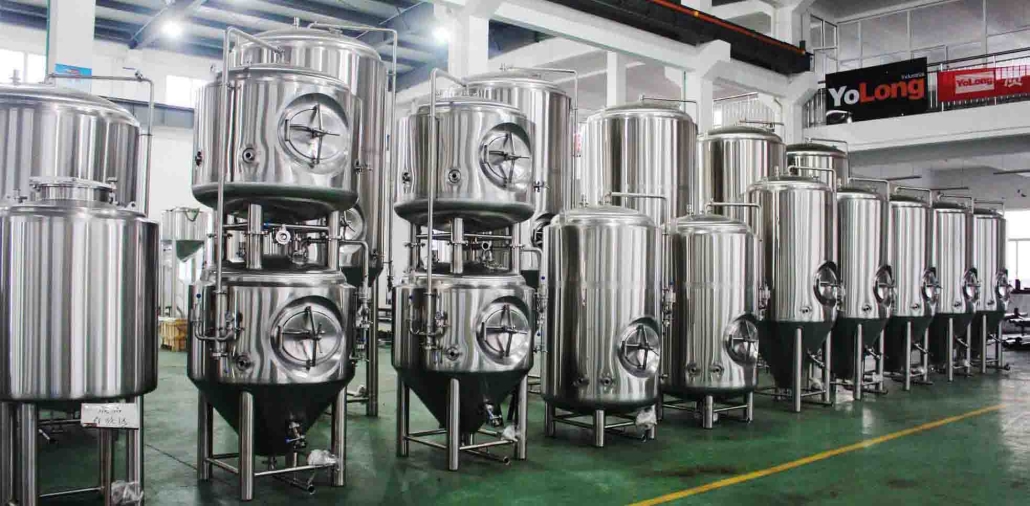
FAQ
Q: What annual production is optimal for a 15 BBL system?
A: Well designed 15 BBL brewhouses can deliver between 5000 to 10,000 barrels yearly when efficiently operated for 4 to 5 batches weekly at 75% utilization.
Q: What custom capabilities typically provide the best ROI?
A: Automated sensors and actuators reduce manual errors and labor costs. Whirlpool systems increase extract efficiency. Advanced boiling control allows faster brew length flexibility.
Q: What is the average breakeven period for a 15 BBL system investment?
A: With solid operating protocols and business plans accounting for both fixed and variable expenses, 15 BBL equipment investments can breakeven within 3 years in favorable markets.
Q: What expertise is absolutely recommended to outsource?
A: Structural engineers for floor loading certifications, process safety management experts, software programmers for automated brewing controls, and specialized electricians. Trying to save costs here can risk safety or commercial delays.
Q: Should we invest in semi-automatic or fully automatic equipment?
A: Evaluate the pros and cons aligned with your brewing innovation plans, staffing capabilities and business scale up roadmap. There is always room to add automation later – but consider future proofing infrastructure upfront.
Conclusion
Deploying the right-sized 15 BBL automated stainless steel brewing equipment allows emerging craft beer brands to expand distribution while retaining artisanal differentiation. Carefully designing facilities and customizing vessels to balance functionality, budget and lead times is vital along with choosing qualified brewhouse engineering partners. Considering maintenance and safety aspects early while planning quality centric standard operating procedures enables smoothly commissioning these million dollar systems. When matched with business operational expertise, talented brewmasters and patient capital, purpose-built 15 barrel brewhouses can unlock profitable next stage growth trajectories for specialty brewpubs by producing 5000 to 10,000 barrels per year.