7 BBL Brite Tank Guide
A brite tank, also known as a bright beer tank or conditioning tank, is a critical component in the beer production process. As the name suggests, brite tanks allow freshly brewed beer to clarify and stabilize after initial fermentation, resulting in a crystal “bright” appearance, optimized flavor, and extended shelf life.
This guide covers key considerations for 7 barrel (BBL) brite tanks from layout and design, to suppliers and pricing, installation and maintenance best practices. Comparison tables help highlight the pros, cons and capabilities of different 7 BBL tank setups.
Overview of 7 BBL Brite Tanks
With a capacity of 7 barrels or 217 gallons (820 liters), 7 BBL brite tanks are a popular size for many mid-sized craft breweries producing specialty beers. Typical batch ranges run from ~150 to 1000 barrels. Critical goals the brite tank accomplishes:
- Allows yeast and solids to settle, clarifying beer
- Provides final carbonation of beer
- Serves as temporary beer storage tank prior to packaging
- Enables easy sampling and quality control checks
- Allows precision temperature control critical for flavor
7 Key Questions to Consider for a Brite Tank
- What total capacity is needed? Identify peak production volumes.
- How many tanks are optimal to prevent bottlenecking?
- What level of automation is preferred for monitoring and control?
- What floor space is available in the brewery? Consider vertical vs horizontal tank orientation.
- What level of customization is needed – logos, sight glasses, connections, etc.?
- What level of craftsmanship and component quality is most important?
- What budget has been allocated for the brite tank system?
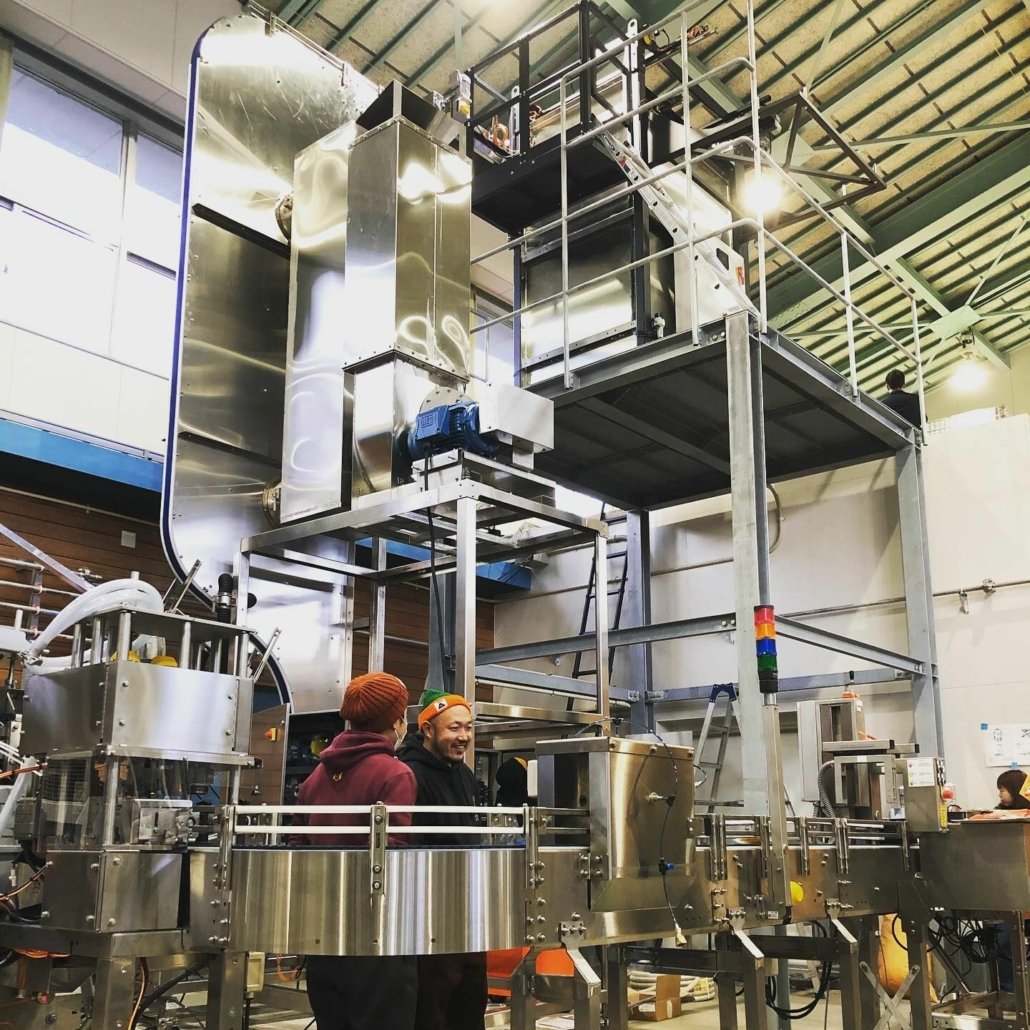
Types of 7 BBL Brite Tank Systems
There are two primary 7 BBL brite tank setups – vertical or horizontal tank orientation, with modular stands or custom tank sculpting.
Vertical vs Horizontal 7 BBL Tanks
Vertical Tanks
- Take up less floorspace
- Allow taller tank height for the same volume
- Easy top access via ladder for maintenance
- Require stands or platforms for installation
Horizontal Tanks
- Have smaller overall height profile
- Allow walk-in access for cleaning and inspection
- Increased floor space requirements
- Often mounted on casters for flexibility
Complete Brewing Systems
Many suppliers offer integrated platforms combining the brite tank with glycol chilling, carbonation, racks, pipes and valves mounted together for simplified setup.
For the 7 BBL size, a 2-tank system is common, allowing one tank for newly fermented beer, while the 2nd tank clarifies. This provides sufficient capacity for back-to-back brewing batches.
7 BBL Brite Tank Capacity, Design and Layout
Sizing Specifications
Tank Size | Dimensions (D x H) | Total Volume | Volume per Batch |
---|---|---|---|
7 BBL Vertical | 36″ D x 96″ H | 217 Gallons | 150 to 300 Gallons |
7 BBL Horizontal | 96″ L x 36″ H | 217 Gallons | 150 to 300 Gallons |
Many hardware configurations and tank sculpting designs possible for a 7 BBL capacity depending on space constraints.
Key Tank Features
Manway
Large diameter opening for tank entry, cleaning and inspection. Minimum 22-26″ diameter recommended.
Sight Glass
Clear view window to visually verify fluid levels and process status, with lighting. Available in different shapes.
Legs
Support structure that raises tank off ground for access. Bolt-down flanges available.
Pressure Relief Valve
Safety release device using precision spring/piston to vent overpressure and prevent damage.
Sample Valve
Outlets that allow collecting liquid samples for analysis and quality checks without entry.
Cleaning Ports
Specialized openings optimized for tank interior spray balls and cleaning solution flow.
Customization & Branding Options
Nearly all brite tank fabricators allow some level of customization, upgrade options and reconfiguration to tailor the system to unique production environments and layouts required.
Logo & Branding
Add custom logos, emblem and vivid branding using specialized etching, durable paint or directly on stainless steel finish.
Level Monitoring
Include electronic fluid level switches or sensors, indicators and alarms to automate monitoring.
Quality Assurance
Special titanium alloy interiors, electropolish, higher grade steel and finishes, inspection ports and sleeves.
Automated Systems
Integrate pumping, CIP, temperature and carbonation controls managed by centralized computer system and software.
Modular Stands
Optimize vertical footprint by choosing from range frame heights and widths to lift tanks off floor.
Brite Tank Brewing Process
The brite tank is one of the last vessels beer contacts before packaging. This overview covers the key conditioning and clarification processes:
First, freshly fermented beer is transferred into the brite tank from the fermenter once primary fermentation completes, allowing the yeast to settle. Precision cooling brings temperature down to 33-35°F which clarifies and stabilizes the beer.
Isinglass finings or other additives can be injected for further haze removal. The clean, cooled environment prevents off-flavors from developing.
Finally, precision carbonation takes place by spunding CO2 into the brite tank for desired carbonation level based on style of beer. Some systems automate dosing based on volume. The tank is then ready for packaging or serving.
7 BBL Brite Tank Pricing from Leading Suppliers
A new 7 BBL brite tank setup costs between $25,000 to $60,000 depending on options chosen. Approximate pricing from top equipment manufacturers is summarized below.
7 BBL Brite Tank Cost Comparison
Company | Base Price Range | Typical Options Added |
---|---|---|
JV Northwest | $25,000 – $35,000 | Controls, fittings, sculpting |
SS Brewtech | $30,000 – $50,000 | Branding, automation |
Premier Stainless | $32,000 – $60,000 | Custom fabrication |
AAA Metal | $28,000 – $48,000 | Platforms, fittings |
Key Price Factors
Hardware & Controls
Costs scale with level of temp sensors, alarms, valves and automation wanted.
Fabrication & Build
More intricate tank sculpting, etching and specialized options increase expense.
Quantity & Configuration
Bulk orders, standardized systems with multiple units decrease overall pricing.
Shipping
Tanks manufactured overseas (China, India) have lower cost but higher shipping fees.
Brite Tank Supplier Selection
Choosing the ideal brite tank fabricator depends on factors like quality, customization capability, reputation and customer service.
How to Choose a Brite Tank Supplier
Consideration | Evaluation Criteria |
---|---|
Build Quality & Track Record | • Years in business<br>• Tank certification levels <br>• Reviews of product robustness <br>• Warranty policies |
Customization Capability | • Range of layout and sculpting options<br>• Fittings, valves, accessories offered <br>• Custom branding , logos ability |
Lead Times & Supply Dependability | • Order backlog status <br>• Lead time accuracy <br>• Change order flexibility |
Overall Value Proposition | • Relative cost vs competitors <br>• Perceived quality and service reputation <br>• Provider specialization level |
Asking detailed questions and assessing real-world installations is key for choosing the optimal system. Sourcing locally often makes post-purchase support and maintenance easier.
Comparing Pros and Cons of 7 BBL Configurations
There are always tradeoff considerations when selecting brite tank size and layout.
Pros and Cons Comparison
Pros | Cons | |
---|---|---|
2x 7 BBL Vertical Tank Sets | • Small footprint, lifts off floor <br> • Maximize brewery ceiling height | • Access requires climbing/ladder <br> • Requires stand, platform |
7 BBL Horizontal Tanks | • No need for external stand <br>• Walk-in easy access <br>• Flexible modular placement | • Uses more floorspace <br>• Can’t stack multiple units <br>• Lower height capacity |
Pre-packaged Systems | • Simplified install <br>• Pre-integrated parts | • Less customization flexibility <br> • Higher upfront cost |
7 BBL Single Tank | • Lower upfront cost | • Limited volume per batch <br>• Single point of failure risk |
3x 7 BBL Tank Sets | • Allows overlapping brews <br>• Redundancy backup | • Uses extensive floor space <br>• Much higher installed cost |
Considering peak production schedules, plant layout, and expansion plans helps dictate the ideal tank count and orientation.
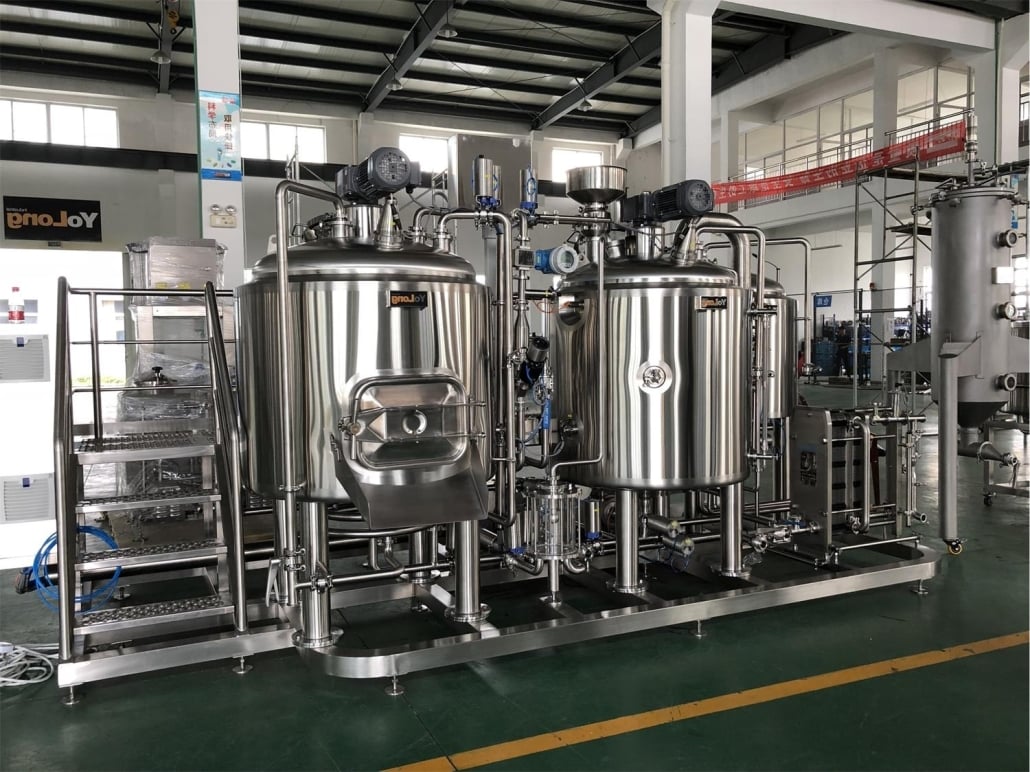
Brite Tank Operation and Maintenance
Proper brite tank operation and care is vital for maximizing equipment lifetimes, ensuring great tasting consistent beer, and avoiding downtime or costlier repairs.
Brite Tank Best Practices
- Follow manufacturer cleaning and sanitization methods using approved chemicals and concentrations
- Replace gaskets, fittings, valves at recommended intervals or when wear noticed
- Watch for corrosion, chips, leaks during inspections and address quickly
- Confirm pressure relief valves still functional; test interlocks and probes
- Keep detailed logs for calibration, service intervals and maintenance checks
- Review brewing process data; optimize fermenter-to-brite transfers
- Consider preventative maintenance service contracts for specialized work
With active monitoring and preventative care, 7 BBL brite tanks can reliably serve small breweries for over 15-20 years.
FAQ
What is the cost per barrel of a 7 BBL brite tank system?
The per barrel expense considering the full system cost typically ranges from $900 – $2000. Lower cost tanks have higher per barrel expense when including necessary additions like stands, chilling, piping, etc. to complete the system.
What are the best 7 BBL brite tank dimensions?
For a vertical 7 BBL tank, optimal dimensions are ~36″ diameter by 7-8 ft height. Expect 6×4 ft footprint or larger for a 7 BBL horizontal tank, with 4 ft height. These provide an ideal beer depth for clarifying and sufficient real estate for fittings.
How many batches can a 7 BBL brite tank process per day?
A single 7 BBL tank can process 1-2 batches per day, depending on beer type, while a dual 2x 7BBL tank setup can handle 2-4 batches per day during continuous operation.
What are the most critical design choices?
Key considerations include number of tanks (always have backup), ability to control temperature precisely, clean-in-place (CIP) capabilities, ease of access for cleaning and inspection, reliability and level of “future-proofing” flexibility for growth.
Can brite tanks be leased instead of purchased?
Yes, both fixed term and flexible leasing options are offered by tank lessors. This shifts upfront capital expenditure to ongoing operating expenditure payments. Terms typically run from 3 to 7+ years. Leasing also can bundle maintenance packages. Evaluate cash flow timing and total cost of ownership tradeoffs when considering purchase vs lease options.
Share this entry
Interested in learning more about Brewing Systems including additional details and pricing information? Please use the form below to contact us!
YOLONG BREWERY EQUIPMENT FAQS
- Commercial Brewery / Craft Brewery / Microbrewery / Nanobrewery
- What is The Difference Between Craft Beer and Industrial Beer?
- The Bespoke Differences In Custom Brewing Systems
- Everything You Need to Know About Kettle Souring
- How to Choose Brewing Equipment for Your business?
- How To Choose The-Best Partner To Build Your Commercial Microbrewing System?
- Two Detection Sensors That You Need To Use In Your Brewhouse System
- Remote Control Applications in Brewing Equipment/How does it work?
- How To Clean Your Brand New Brewery Tanks?