7 BBL Brewhouse
Brewing beer is as much an art as it is a science. The tools you use can significantly impact the flavor, quality, and consistency of your beer. One critical piece of brewing equipment is the 7 BBL brewhouse. Whether you’re a seasoned brewery owner or a newcomer in the beer-making business, understanding the features, specifications, and overall functionality of a 7 BBL brewhouse is essential for success.
In this guide, we will delve into the details of what a 7 BBL brewhouse entails, its design, capacity, and the brewing process it supports. Additionally, we will provide an in-depth look into various equipment types, suppliers, installation, and operational guidance, all while keeping SEO best practices in mind.
Overview of a 7 BBL Brewhouse
A 7 BBL (Barrel) brewhouse refers to brewing equipment with a capacity of seven barrels. To put that into perspective, one barrel is approximately 31 gallons, meaning a 7 BBL system produces about 217 gallons of beer in one batch. This size is ideal for craft breweries, small to medium-sized brewpubs, or establishments looking to scale production.
The 7 BBL brewhouse strikes a balance between production capability and space efficiency, making it a popular choice for brewers seeking moderate production without requiring massive industrial space. Its versatility in brewing a variety of beer styles ensures it’s perfect for experimentation as well as mass production of core recipes.
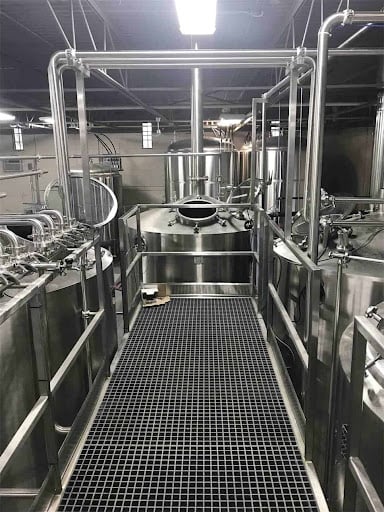
Equipment Guide for a 7 BBL Brewhouse
A brewhouse is made up of multiple components that work in harmony to produce beer. Here’s a breakdown of essential equipment you’ll find in a 7 BBL brewhouse:
- Mash Tun: The mash tun is where the malted grains are mixed with water to convert starches into fermentable sugars. In a 7 BBL system, a mash tun can range from simple insulated tanks to fully automated systems with temperature control.
- Lauter Tun: The lauter tun is responsible for separating the spent grains from the sugary liquid, or wort. In many 7 BBL systems, the mash tun and lauter tun are combined into one unit.
- Boil Kettle: After the wort is extracted, it is boiled in the kettle. During this stage, hops are added for bitterness, flavor, and aroma. Boil kettles in a 7 BBL system typically feature advanced control options for temperature management.
- Hot Liquor Tank (HLT): This tank holds and heats water for brewing purposes. Hot water is essential for mashing and sparging (rinsing grains), as well as cleaning the brewhouse.
- Fermenters: Once the wort is boiled and cooled, it is transferred to fermenters where yeast is added to convert sugars into alcohol. Fermenters in a 7 BBL system can vary in shape and functionality, from simple cylindrical tanks to more complex conical designs.
- Bright Beer Tank (BBT): A bright beer tank is used for carbonating, clarifying, and storing beer before packaging or serving. In a 7 BBL system, a BBT is essential for ensuring your beer has the right amount of carbonation and clarity.
Equipment Types in a 7 BBL Brewhouse
Equipment | Function | Key Features |
---|---|---|
Mash Tun | Converts malted grains to fermentable sugars | Insulated design, temperature control |
Lauter Tun | Separates wort from grains | Sparging arms, false bottom |
Boil Kettle | Boils wort and adds hops for flavor | Temperature control, steam or electric heating options |
Hot Liquor Tank | Provides hot water for mashing and cleaning | Heating elements, insulation |
Fermenters | Fermentation process where yeast converts sugars to alcohol | Conical design, glycol cooling jacket |
Bright Beer Tank | Carbonates, clarifies, and stores finished beer | Pressure control, carbonation stones |
The Brewing Process with a 7 BBL Brewhouse
The brewing process in a 7 BBL brewhouse follows similar steps to smaller or larger systems, but it provides scalability that allows for more production while retaining control over the quality of the beer. Here’s an overview of how the process unfolds:
- Mashing: Grains are added to the mash tun along with hot water from the hot liquor tank. The water is heated to a specific temperature that activates enzymes to convert starches into fermentable sugars.
- Lautering: After mashing, the mash is transferred to the lauter tun (or in a dual-function tun), where the wort is separated from the spent grains. The wort is then collected into the boil kettle.
- Boiling: In the boil kettle, the wort is boiled, and hops are added at different stages for bitterness, flavor, and aroma. This step also sterilizes the wort, ensuring a clean fermentation.
- Fermentation: After boiling, the wort is cooled and transferred to fermenters. Yeast is added to begin the fermentation process, converting the sugars into alcohol and carbon dioxide.
- Conditioning and Carbonation: Once fermentation is complete, the beer is transferred to the bright beer tank for conditioning. Here, it undergoes carbonation and is clarified before it’s ready for packaging or serving.
Capacity, Space, Design, and Customization of a 7 BBL Brewhouse
Choosing the right 7 BBL brewhouse goes beyond production capacity. Factors such as space requirements, design layout, and customization options can greatly impact the efficiency of your brewery. Let’s explore these in greater detail.
Parameter | Details |
---|---|
Capacity | Produces 217 gallons (7 BBL) per batch, with potential for multiple batches daily. |
Space Requirements | Requires around 300-500 square feet, depending on layout and auxiliary equipment. |
Design Layout | Customizable configurations to fit existing spaces, such as stacked fermenters or horizontal tanks. |
Customization Options | Customizable with automation controls, additional tanks, or specific materials like stainless steel. |
A key aspect of customization is the option to choose automation levels. For example, fully automated systems may come with programmable logic controllers (PLC) for temperature, pH levels, and fermentation monitoring, while semi-automated systems offer more manual control.
Suppliers and Price Range of a 7 BBL Brewhouse
Investing in a 7 BBL brewhouse involves weighing costs against the features and benefits of the equipment. Here’s an overview of leading suppliers and the price range you can expect for a 7 BBL system.
Supplier | Price Range | Notable Features |
---|---|---|
Stout Tanks & Kettles | $70,000 – $120,000 | Stainless steel construction, glycol jackets, customizable configurations |
Brewmation | $80,000 – $130,000 | Automated systems with PLC control, customizable brew kettles |
Specific Mechanical | $85,000 – $140,000 | Highly efficient heating, ergonomic designs, and premium build quality |
Portland Kettle Works | $75,000 – $125,000 | Focus on sustainability, energy-efficient designs, and scalable options |
It’s important to consider not just the upfront cost, but also long-term benefits such as efficiency, energy consumption, and the ability to expand or upgrade the system over time.
Installation, Operation, and Maintenance of a 7 BBL Brewhouse
The installation, operation, and maintenance of a 7 BBL brewhouse require careful planning to ensure smooth production. Let’s dive into the key aspects of each phase:
Phase | Details |
---|---|
Installation | Installation takes 2-3 weeks and includes configuring tanks, piping, and electrical components. |
Operation | Daily operation involves mashing, boiling, and fermenting, with brewing times averaging 6-8 hours per batch. |
Maintenance | Routine maintenance includes cleaning tanks, checking seals and valves, and ensuring proper glycol flow. |
Regular maintenance helps ensure that your system operates efficiently and extends its lifespan. Most suppliers offer maintenance packages or support to help with troubleshooting and repairs.
How to Choose a 7 BBL Brewhouse Supplier
Choosing the right supplier for your brewhouse is a crucial decision. Factors such as cost, customer service, reputation, and customization options can greatly impact your satisfaction with the final product. Here’s a breakdown of what to look for:
Factor | Importance |
---|---|
Reputation | Look for suppliers with proven track records in the brewing industry. Check reviews and testimonials. |
Customization Options | Choose a supplier that offers the level of customization you need for your brewery’s specific requirements. |
Customer Support | Ensure the supplier provides installation help, operational training, and ongoing support. |
Pricing | Consider both the upfront costs and potential long-term savings from more efficient systems. |
Advantages and Limitations of a 7 BBL Brewhouse
Every brewing system has its pros and cons. Here’s a quick look at the advantages and limitations of a 7 BBL brewhouse:
Advantages | Limitations |
---|---|
Ideal for scaling craft beer production | Requires significant initial investment |
Efficient use of space and energy | Can be complex to operate without proper training |
Customizable to meet specific needs | Maintenance can be time-consuming |
Supports diverse brewing styles | Limited to medium-sized production runs |
While the advantages often outweigh the limitations, understanding both sides is critical to making an informed purchase decision.
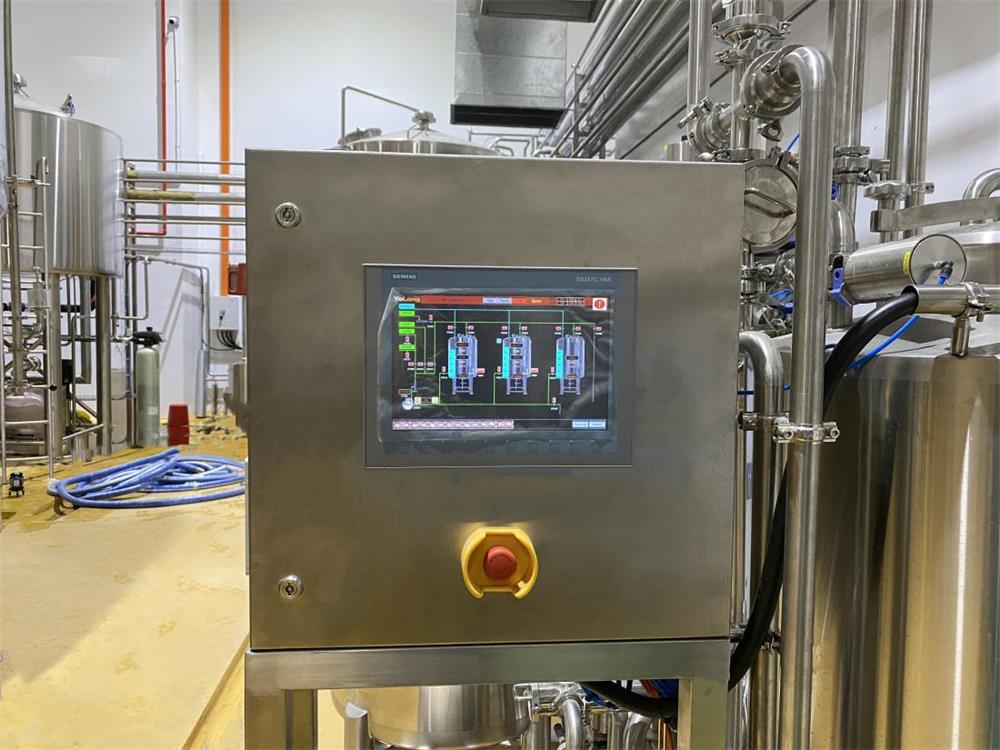
FAQ
Question | Answer |
---|---|
What does 7 BBL stand for? | 7 BBL stands for seven barrels, equivalent to approximately 217 gallons of beer per batch. |
Is a 7 BBL brewhouse suitable for a startup brewery? | Yes, it’s ideal for startup breweries due to its scalability and balance between production capacity and space requirements. |
How long does it take to brew with a 7 BBL system? | A full brewing cycle typically takes 6-8 hours, depending on the recipe and process steps. |
Can a 7 BBL brewhouse be automated? | Yes, many 7 BBL systems offer automation options such as temperature control, flow regulation, and monitoring systems. |
What is the typical lifespan of a 7 BBL brewhouse? | With proper maintenance, a 7 BBL brewhouse can last 15-20 years or more. |
Conclusion
A 7 BBL brewhouse is an excellent investment for small to medium-sized breweries looking to scale production while maintaining control over beer quality. With the right equipment, suppliers, and maintenance plans, a 7 BBL system can deliver consistent, high-quality beer for years. By understanding the details of this brewing system, you can optimize your brewery for success—both in terms of production and profitability.
Share this entry
Interested in learning more about Brewing Systems including additional details and pricing information? Please use the form below to contact us!
YOLONG BREWERY EQUIPMENT FAQS
- Commercial Brewery / Craft Brewery / Microbrewery / Nanobrewery
- What is The Difference Between Craft Beer and Industrial Beer?
- The Bespoke Differences In Custom Brewing Systems
- Everything You Need to Know About Kettle Souring
- How to Choose Brewing Equipment for Your business?
- How To Choose The-Best Partner To Build Your Commercial Microbrewing System?
- Two Detection Sensors That You Need To Use In Your Brewhouse System
- Remote Control Applications in Brewing Equipment/How does it work?
- How To Clean Your Brand New Brewery Tanks?