Overview of 7 BBL Brewhouse Systems
A 7 barrel (BBL) brewhouse is a medium-sized professional beer brewing system with a capacity to produce 7 barrels or 217 gallons per batch. This brewhouse size is well-suited for small to mid-size microbreweries and taprooms looking to sell beer on premises or distribute locally.
This guide covers key considerations in choosing, designing, installing and operating an efficient 7 BBL brewhouse optimized for your production goals and budget.
Types of 7 BBL Brewhouse Systems
There are two main types of 7 BBL brewhouse systems:
Table: 7 BBL Brewhouse System Types
System Type | Description |
---|---|
Traditional | Manually operated, custom fabricated stainless steel brewhouse vessels with steam heating. Requires an experienced brewer. |
Automated | PLC-controlled system with pumps, sensors, motors for automation. Program recipes & schedules. Easier to operate. |
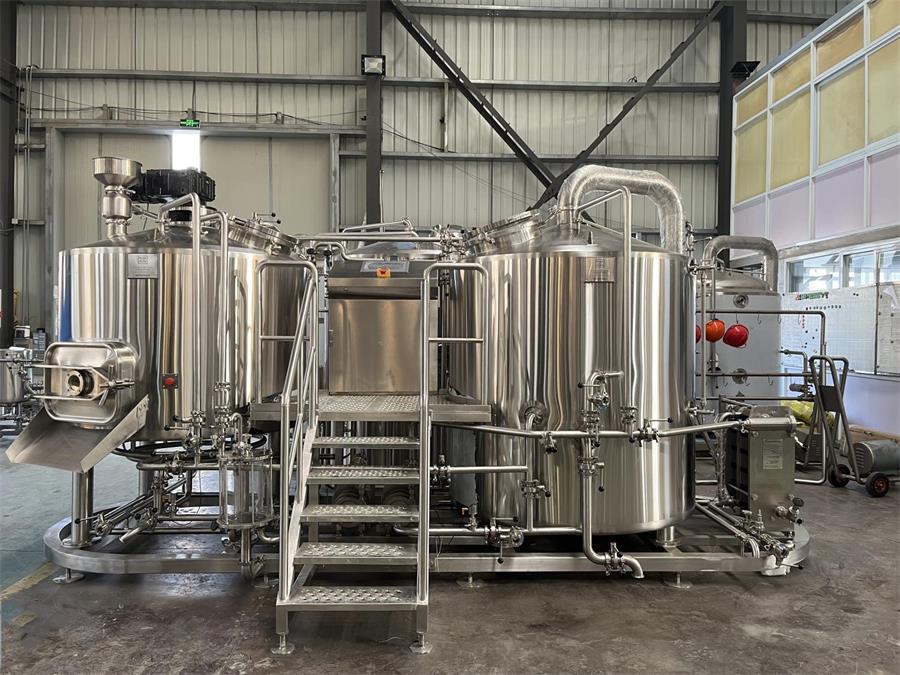
7 BBL Brewhouse Brewing Process
A typical brewing process flow through a 7 BBL brewhouse system is as follows:
Milling → Mash Conversion → Lautering → Wort Boil → Whirlpool → Cooling → Fermentation → Conditioning → Filtration → Packaging
During milling, the malted barley grains are cracked open to allow access during mashing. In mash conversion, the grains are steeped in hot water activating enzymes to convert starch into fermentable sugars. The sugary liquid wort is then separated from grains using a lauter tun. The wort then undergoes boiling, whirlpool and cooling before yeast is pitched to ferment the sugars into alcohol and CO2. After fermentation, the green beer is conditioned and filtered before being packaged.
7 BBL Brewhouse Capacity, Design and Customization
When selecting and designing a 7 BBL brewhouse, key considerations include:
Table: 7 BBL Brewhouse Capacity and Design Factors
Parameter | Details | Customization Options |
---|---|---|
Batch Size | 7 barrel (BBL) = 217 gallonsper batch | Custom sized brewhouses from 3–15 BBL |
Mashing Capacity | 10–14 BBL to allow grains absorption swelling during mashing | Mash filter size, rakes, sensors etc. |
Boiling Rate | 15-30 gallons per hour boil-off rate | Powerful gas/electric boil kettle |
Whirlpool Design | Swirl direction, slope, depth for trub separation | Spin cycle customization |
Temperature Control | Precision sensors & valves for hitting mash, boil, pitch temps | Automated variable speed pumps |
Recipe Programming | Store recipes with timed temperature steps and valve actuations | Touchscreen HMI, data tracking |
Brewing Flexibility | Accommodate lagers, ales, specialty beers | Interchangeable vessels, modular design |
Physical Size | 10-15 ft length x 8-12 ft width x 8-14 ft height | Layout optimization, compact/split design |
Production Rate | 150-300 BBL per month, 24/7 operation | Semi vs Fully automated, staffing |
Consider the types of beers you wish to produce, ingredients, seasonal variations and packaging to determine the features and functionality needed in your brewhouse early on. An experienced brewhouse manufacturer can help customize the system to meet your specific production goals.
7 BBL Brewhouse Suppliers and Pricing
There is a wide range of brewhouse suppliers, prices and options when investing in 7 BBL systems:
Table: 7 BBL Brewhouse Manufacturers and Costs
Supplier | Base Price Range | Key Offerings |
---|---|---|
Specific Mechanical | $100,000 – $250,000 | Custom manual and automated brewhouses, modular Italian-made |
Premier Stainless | $150,000 – $300,000 | Traditional custom steam heated kettles & mash tun |
JV Northwest | $180,000 – $350,000 | Automated touchscreen electric brewhouses |
Brewmation | $200,000 – $400,000 | Complete automated precision brewing controls |
AAA Metal Fabrication | $120,000 – $180,000 | Manual systems focused on affordability |
Evolution Stainless | $250,000 – $450,000 | Integrated eco-friendly steam, electric & solar |
Psycho Brew | $300,000 – $600,000 | Ultra-modern automated using IoT sensors |
Craftwerk | $150,000 – $250,000 | German-engineered steam & gas fired kettles |
Prices vary widely depending on level of automation, imported hardware costs, fabrication rates and value-added services offered. Get detailed quotes before deciding on the right brewhouse supplier for your needs.
7 BBL Brewhouse Installation, Operation and Maintenance
Proper installation, operation and preventative maintenance are key to maximizing uptime and keeping your 7 BBL brewhouse running efficiently for years:
Table: 7 BBL Brewhouse Installation and Operation Factors
Function | Details |
---|---|
Installation | Foundation, layout, electrical, plumbing, ventilation, safety, permitting |
Staff Training | Equipment training on operating procedures |
Brewing Process | Standard operating procedures for recipes consistency |
Cleaning & Sanitation | CIP spray balls, chemicals, cleaning schedule |
Calibration & Alerts | Volume, temperature sensor calibration, tank level alerts |
Preventative Maintenance | Regular inspection schedule, replace wear items |
Service & Support | Maintenance contracts, on-call support response time |
Develop detailed standard operating procedures, cleaning regimens, maintenance logs and staff training plans. This ensures smooth operations, consistent quality and minimized unplanned downtime. Partner with your brewhouse manufacturer for continued service and support.
How to Select the Right 7 BBL Brewhouse Supplier
Choosing the optimal 7 BBL brewhouse system for your brewery involves:
Table: How to Evaluate and Select 7 BBL Brewhouse Suppliers
Consideration | Assessment Criteria |
---|---|
Reputation & Experience | Years in business, number of systems installed, client reviews |
Customization Capabilities | Flexibility to meet specialized requirements |
Brewing Efficiency & Quality | Precision in hitting temps and timings for yield and taste |
Ease of Use | Intuitive design and controls for simplicity |
Service & Support | Response time, availability of parts/service, maintenance plans |
Value for Investment | Performance, reliability and payback period given costs |
Local Representation | Installation, commissioning and service partnerships |
Evaluate each brewhouse supplier against these criteria relative to your organization’s priorities using detailed RFPs, reference checks, facility tours and pilot batches. This drives an informed decision balancing custom features, budget and long-term service support.
Comparing Pros and Cons of 7 BBL Automated Brewhouses
Automated brewhouses provide advantages in efficiency, consistency and labor savings – but also carry higher costs and complexity:
Table: Pros and Cons of Automated 7 BBL Brewhouses
Pros | Cons |
---|---|
Precise temperature and timing control | Twice the capital expense of manual |
Automated cleaning and record keeping | Complex programming and controls |
Store recipes for perfect repeatability | Require specialized technical support |
Reduce labor requirements | Potential for costly electronic failures |
Hands-off remote monitoring | Lengthy troubleshooting procedures |
Easy scale up with modular expansions | Generally imported hardware markups |
Weigh the benefits against drawbacks smartly based on available capital, staff competencies and brewing goals. Starting semi-automated also provides a middle ground.
Limitations and Considerations of 7 BBL Brewhouse Systems
While 7 BBL brewhouses are efficient small batch setups, be aware of inherent scale and flexibility limitations:
Table: Scaling Challenges with Expanding 7 BBL Brewhouses
Limitation | Implication | Mitigation Strategy |
---|---|---|
Max Batch Size | Limited to peak volumes around 15 BBL per batch | Start with larger 10-15 BBL system |
Ingredient Handling | Manual grain handlingwon’t keep up with growth | Automate milling, moving and cleaning |
Packaging Bottleneck | Manual labeling, boxing, palletizingpace constraints | Integrate inline bottling, canning, kegging |
Refrigeration Capacity | 7 BBL fermentation andbrite tanks max out | Plan modular cold room expansions |
Steam Boiler Capacity | Eventually hits max steaming rate per hour | Upgrade to 20-30 BBL electric steam generator |
Starting too small risks major investments in upgrades soon. But overbuilding capacity too early carries high costs. Consult experts to define scaling roadmap.
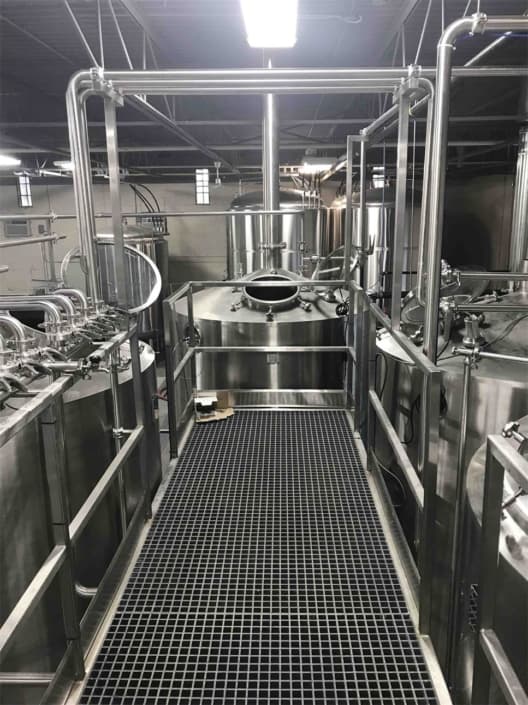
FAQs
Table: Frequently Asked Questions About 7 BBL Brewhouse Systems
Question | Answer |
---|---|
How much can a 7 BBL brewhouse produce annually? | 2,600 to 5,200 barrels per year is typical operating single or 2 shifts daily, assuming good uptime. |
What size building is needed to house a 7 BBL system? | Allow 15 ft x 15 ft of space for the brewhouse itself. Total building size including fermentation and storage would need to be 2000 to 4000 sq. ft. |
Can I buy a used 7 BBL brewhouse system? | Yes, buying used can save substantially on costs – but may carry risk of mechanical issues or condition concerns. Inspect carefully before purchase. |
Should I buy domestic or imported 7 BBL hardware? | Domestic provides ease of service but costs more. Imported cuts expense by 30% but sacrifices convenience and customization. |
What are the most critical factors in selecting supplier? | Evaluate reputation, quality, serviceability, support capabilities and staff competency above just price alone. |