7 BBL Brew Kettles
A 7 BBL brew kettle is a key piece of equipment in a professional microbrewery setup with an annual production capacity around 1,000 to 3,000 barrels. This guide provides craft brewers an overview of 7 BBL brew kettle covering capacity details, layout considerations, top suppliers, pricing, installation and maintenance best practices plus pros vs cons comparisons.
Overview of 7 BBL brew kettle
A kettle is essentially a giant, specialized pot for boiling wort during the beer production process. 7 BBL brew kettle handle batch sizes of 7 barrels or ~220 gallons per brew.
Table 1: Background on 7 BBL Brew Kettles
Attribute | Details |
---|---|
Purpose | Boiling wort to extract flavors, sterilize, promote reactions |
Batch Size | Typically 7 barrels or ~220 gallons |
Scale | Suitable for microbreweries ~1,000 to 3,000 BBL annual output |
Key Components | Kettle, stand, burner(s), valves, sight glass, fittings |
Use Points | Used after mashing and lautering, before fermentation |
For small to mid-sized craft breweries, 7 BBL kettles offer reasonably efficient production runs while still enabling immense flexibility around recipe experimentation. Understanding capacity requirements during growth stages is key when specifying appropriately sized brewhouse equipment.
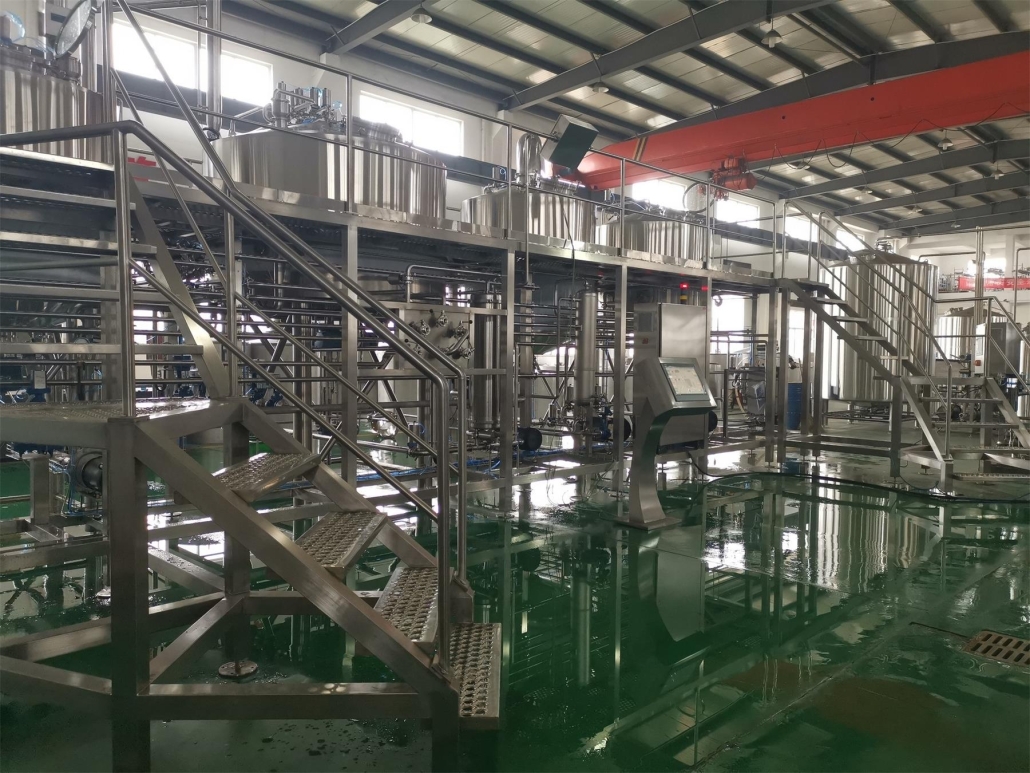
Types of 7 BBL brew kettle
While most kettles share fundamental attributes around holding boiling wort, various kettle orientations and feature sets aim to optimize ergonomics, performance, or floorspace depending on the brewery layout.
Table 2: Types of 7 BBL brew kettle
Type | Attributes | Considerations |
---|---|---|
Conical bottom | Cone-shaped interior | Promotes whirlpooling, trub separation |
Flat bottom | Rectangular bottom | Easier cleaning access |
Single vessel | Integrated boil kettle | Compact footprint, lower cost |
2-vessel | Separate mash tun and boil kettle | Flexible recipes, better efficiency |
Floor mounted | Ground installation | Heavy stability, easy cleaning |
Pub style | Elevated with external heat source | Saves floorspace, moveable |
Electric | Cleaner burning, accurate power | Higher infrastructure needs |
Gas-fired | Lower install costs, ventilation needed | Potential temperature variances |
Selecting attributes like kettle floorspace arrangement, number of vessels in the brewhouse, heating source types, ease of cleaning access, material choices, etc. depend on budgets, existing infrastructure, and workflow considerations.
Understanding key equipment decisions empowers brewers to tailor optimal brewhouse infrastructure matching business objectives as startups scale towards wider distribution while retaining exceptional quality, consistency, and branding throughout growth phases.
The Brewing Process Using 7 BBL brew kettle
In typical brewery operations, the boiling phase utilizes 7 BBL kettles after initial mashing to extract sugars and add unique flavoring characteristics:
- Malted grains are combined with hot water in the mash tun for saccharification converting starches into fermentable sugars.
- The sweet liquid wort is then lautered through the grains to filter out solids while rinsing more sugars into the wort.
- The sweet wort is then transferred into the 7 BBL brew kettle where it reaches boiling temperature. Vigorous heating facilitates:a. Extracting aromatic hop oils contributing bitterness, flavor, and aromab. Concentrating wort to desired amounts through evaporationc. Promoting caramelization and Maillard reactions adding color and flavord. Sterilizing wort preventing unwanted infections
- After the boil phase finishes, wort moves to the fermenter where yeast are pitched to metabolize sugars into alcohol and CO2 while producing subtle flavor compounds.
The rapid heating and rolling boil inside the 7 BBL brew kettle represents a crucial processing step enabling craft brewers to create unique beer recipes that build brand loyalty with supporters.
Key Specifications for 7 BBL brew kettle
Crafting an optimal kettle system requires balancing factors like batch sizes, space constraints, production workflow, infrastructure limitations, and budgets.
Table 3: 7 BBL Brew Kettle Considerations
Parameter | Options | Factors |
---|---|---|
Volume | 6.5-7.5 BBL range | Standard barrelage increments |
Height | 48-84 inches | Optimal sight glass viewing, ergonomics |
Diameter | 36-48 inches typically | Smaller saves floorspace |
Material | Stainless steel (304, 316) | Corrosion resistance, cleaning, cost |
Heating systems | Gas, electric, steam | Power infrastructure, ventilation, rapid heating needs |
Cleaning access | CIP sprayballs, cleaning ports, sight glass | Simplify sanitization |
Automation | Programmable controllers | Consistency, labor savings, data logging |
Customization | Manifold designs, sight window position, base profiles | Unique branding elements |
Prioritizing demands around batch sizes, peak hourly/daily brewhouse throughput, floorspace limitations, and available energy sources facilitates appropriate decision making when selecting the brew kettle system optimal for the operation. This empowers steady scaling while retaining exceptional quality, unique branding, and efficient economics even during seasonal variability or disruptions.
Layout and Design of 7 BBL Brewhouses
Optimizing kettle positioning in the brewhouse along with ergonomic considerations allows smoother operator workflows translating into higher consistency while minimizing injuries across long shifts.
Table 4: 7 BBL Brewhouse Layout Guidelines
Strategy | Benefits | Considerations |
---|---|---|
Two-tier layout | Gravity liquid transfer | Requires platforms/stairs access |
Round layout | Efficient single operator movement | Relies on valves for routing |
Linear layout | Intuitive start-to-finish flow | Increases floorspace needs |
Control panel accessibility | Monitoring, rapid adjustment | Position to prevent obstructions with vessels |
Sight glass visibility | Volume measurement, safety | Ensure adequate viewing angles |
Cleaning access | CIP sprayballs reach all surfaces | Doors/ports for interior access |
Ergonomic valve handles | Reduced repetitive strain | Offset 10-20 degrees off vertical |
Anti-fatigue floor mats | Reduces leg strains | High-traction, not slippery when wet |
By modeling personnel movement patterns and placing kettles appropriately to gravity assist transfers between vessels, overall efficiency and safety improves dramatically. This reduces chances of spills or burns which delay production and risks contaminating entire batches.
Thoughtful equipment layouts, ergonomic kettle design elements, and smooth brewer workflows mutually reinforce each other – especially vital as small startups expand towards 24 hour capacity across multiple shifts to meet seasonal or growing distribution demands.
Top 7 BBL Kettle Manufacturers
Reputable commercial brewhouse fabricators offer versatile 7 BBL kettles scalable from pilot systems up to large production scenarios. They also provide modular options as needs grow.
Table 5: Leading 7 BBL Kettle Producers
Company | Offerings |
---|---|
ROLEC | Fully-customizable kettles and brewhouses |
JV Northwest | Quality kettles focused on craft brewers |
AAA Metal Fabrication | Custom brewing equipment |
Psycho Brew | Specialty brewhouse engineering |
The Vintner Vault | Custom wine, beer, distilling equipment |
These commercial outfitters offer 7 BBL kettles spanning:
- Standard vs custom designs: Pre-engineered templates balance costs while customized fabrications meet niche layout requirements
- Electric vs gas firing: Matching available energy infrastructure
- Manual vs automated: Level of control system integration dictating repeatability and data collection opportunities
Top vendors collaborate with clients iteratively translating specific workflow priorities, infrastructure constraints, and quality expectations into tailored solutions productizing unique craft brewing capabilities and experiences.
Pricing Details on 7 BBL brew kettle
Quality kettles and brewhouses carry substantial upfront investments ranging $50,000 to $250,000+ for full 7 BBL systems. However these equip brewers to efficiently produce ~1,000 to 3,000 barrels annually when combined with fermentation and serving tanks.
Table 6: 7 BBL Brew Kettle Pricing
Component | Price Range |
---|---|
7 BBL kettle | $20,000 – $60,000 |
Gas burner system | $5,000 – $15,000 |
Stand, platform | $5,000 – $20,000 |
Valves, fittings, sensors | $5,000 – $15,000 |
Integrated control system | $10,000 – $25,000 |
Total System Cost | $50,000 – $250,000+ |
Custom fabrications with automated features and exotic alloys escalate capital investments, so prescribing appropriate specifications catering to true business requirements proves essential.
For example, manual vs automated vessels may carry a $20,000+ premium. But this may pay back rapidly through 5+ years of labor cost savings – especially vital when expanding output. Thinking holistically about true project lifetime costs rather than just upfront sticker pricing facilitates smarter investments.
Installation and Operation of 7 BBL Setups
Proper kettle installation and ongoing operation/maintenance practices ensure smooth beer production plus maximize equipment lifetimes all while minimizing safety or contamination risks.
Table 7: 7 BBL Kettle Best Practices
Activity | Recommendations |
---|---|
Delivery/positioning | Leverage professionals given weight. Double check alignments. |
Ventilation | Ensure adequate CFM ratings to manage heat/steam |
Utility connections | Pressure test water, steam, glycol piping. Engage experts as needed. |
Cleaning verification | Hot water cycles confirming drainage from all sections |
Control calibration | Test sensors against independent instruments |
Preventative maintenance | Establish routine inspection checklists per manufacturer guidance |
Ongoing care best practices encompass:
- Periodic replacement of gaskets and fittings
- Inspecting sight glasses and level instruments
- Testing calibration of sensors and automated controls
- Touch-up any surface corrosion or wear
- Leak checks identifying steam, wort or cooling water escapes
Following suggested maintenance intervals and immediately addressing minor issues maximizes uptime while achieving the full production lifetime expectancy from 7 BBL kettle equipment investments.
Selecting the Right Kettle Vendor
Given the central role kettles play governing production quality and consistency for years, prudent selection of an appropriate brewhouse outfitter proves crucial for maximizing value and growth potential.
Table 8: Partner Selection Considerations for Brew Kettles
Criteria | Assessment Guidance |
---|---|
Portfolio suitability | Wide range of options? Scalability for growth? |
Customization capabilities | Accommodate specific layout needs? |
Construction quality | Robust but serviceable materials and finishes? |
Established reputation | Proven track record across customer base? Safety focus? |
Service capabilities | Responsive support structure? Preventative options? |
Operator training | Thorough instructions and ongoing reference options? |
Developing trusted, responsive relationships with equipment experts through iterative consultations ensures optimal tailoring around current and future objectives. This allows smoothly upgrading infrastructure without production interruptions even during seasonal demand spikes or aggressive business expansion phases.
Carefully evaluating potential providers against key benchmarks provides confidence in customized complex kettle system performance for the long haul.
Pros vs Cons of 7 BBL Brewhouse Setups
While substantial capabilities come with 7 BBL kettles, certain inherent challenges must also be managed related to production constraints, operating skills needs, and infrastructure requirements.
Table 9: Advantages vs Considerations for 7 BBL Kettles
Pros | Cons |
---|---|
~1,000-3,000 annual barrel capacity | Significant startup capital investments |
Flexible small batch experimentation | Potential labor model changes with automation |
Efficient use of ingredients | Requires skilled brewers familiar with equipment |
Test markets for new products | Possible facility build-outs or upgrades |
Preserves artisanal quality | Cleanliness rigor needed to prevent infections |
Custom branding elements | Requires specialized trades for utility connections |
The throughput capacities for annual beer production spanning 1,000 to 3,000 barrels places 7 BBL operations in an optimal size niche – benefiting from economics of scale while retaining signature small batch flexibility.
However, pursuing these sizable production volumes does require astute planning around labor additions, quality control enhancements, and infrastructure readiness to properly accommodate growth changes as market access expands.
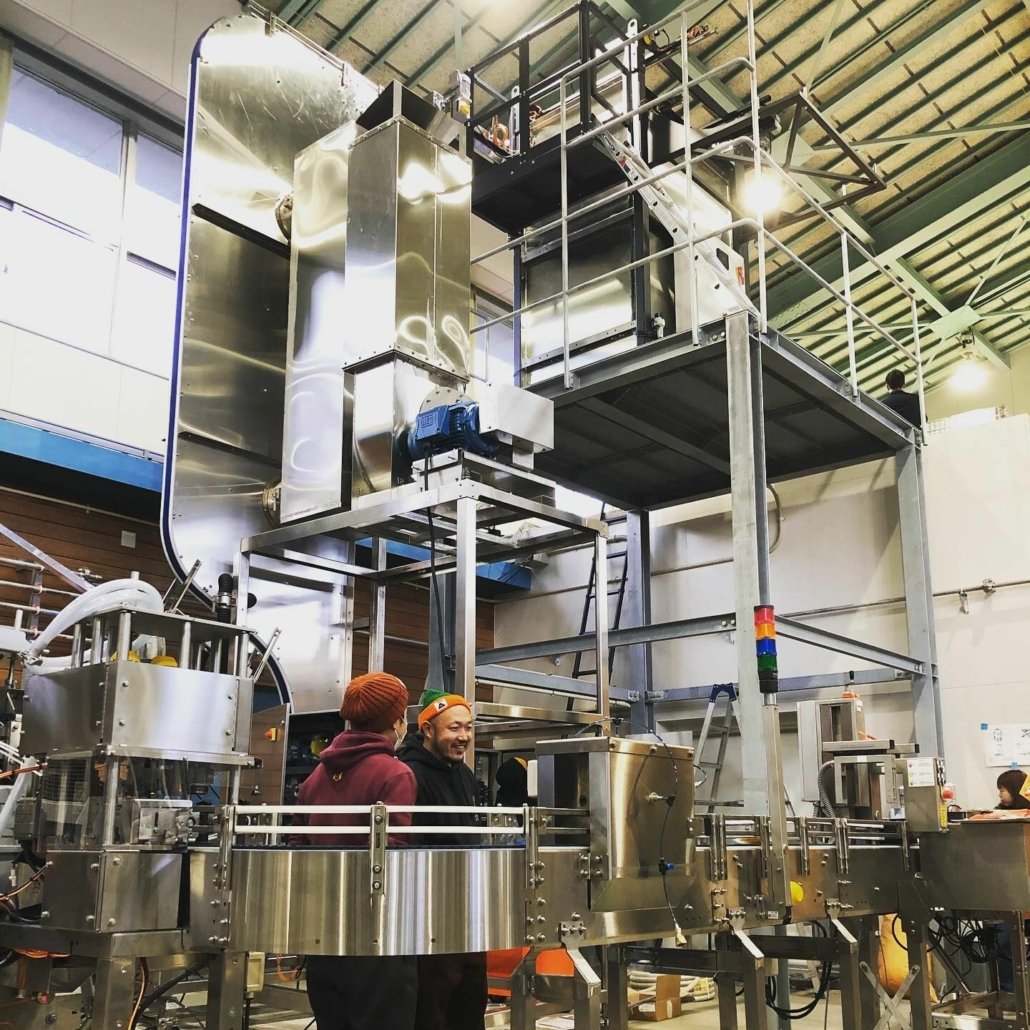
FAQ
Q: What type of floorspace is needed for a full 7 BBL brewhouse?
A: Expect to allocate ~500-1,000 sq ft to comfortably fit a 7 BBL kettle, mash tun, fermentation tanks, and workflow space for operators. Ceiling height of 10+ feet is also preferable.
Q: Should breweries choose automated or manual kettle systems?
A: Automating elements like heating, transfer valves or cleaning can provide consistency benefits once dialed in. But may reduce flexibility for experimental recipes. Also consider skill sets and labor costs/availability.
Q: What are the most common problems observed with 7 BBL kettles?
A: Issues around leakage at fittings, gaskets or sight glasses, burner inconsistencies, sticky valves or aging sensors negatively impact production quality if left unaddressed. Proactive inspections minimize headaches.
Q: What safety risks should brewers mitigate around kettles?
A: Hot wort handling risks scalding. Electricity and gas supply safe containment protocols are mandatory. Ensure fire suppression systems suit brewhouse equipment and layouts. Have written safety procedures.
Q: How often might a brewery expect to replace a 7 BBL kettle system?
A: With routine maintenance of gaskets, sensors etc, plus avoiding excessive thermal shock cycles, 20+ year lifetimes are reasonable expectations for welded kettles themselves. Value upgrades around controls or burners may occur earlier.