Comprehensive Guide to the 500L Brewing System
Brewing beer has become more than just a hobby for many enthusiasts and professionals alike; it’s an art and a science. When scaling up operations, one of the most popular setups is the 500L brewing system. This guide will walk you through everything you need to know about the 500L brewing system—from the equipment you’ll need, brewing processes, and customization options, to how to choose the right supplier. We’ll also compare prices, suppliers, and discuss the pros and cons to help you make an informed decision.
Overview of the 500L Brewing System
A 500L brewing system is a medium-sized setup that is ideal for craft breweries, pubs, and even small commercial brewing ventures. This system allows brewers to produce up to 500 liters of beer per batch, making it a solid choice for those who need a balance between production volume and space. The system includes various components such as brewhouses, fermentation tanks, and control systems, each designed to make the brewing process efficient and customizable.
Brewers opting for the 500L system typically look for consistency, quality, and scalability, as these systems can grow with the business. With a 500L system, you can produce enough beer to serve a decent-sized crowd without requiring the footprint and resources of a larger, industrial setup.
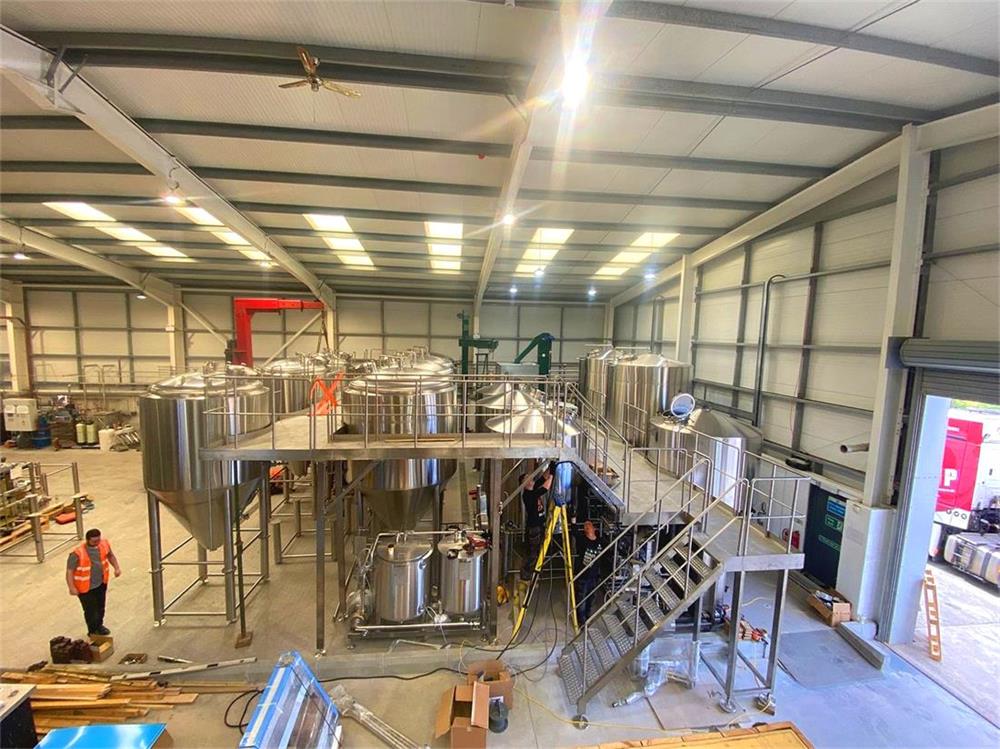
Equipment Guide for the 500L Brewing System
When considering a 500L brewing system, the equipment involved is crucial. Here’s an overview of the necessary components:
- Brewhouse: The heart of the operation where the mash, boil, and whirlpool processes occur. It often includes a mash tun, lauter tun, and kettle.
- Fermentation Tanks: These tanks allow for the fermentation process and can vary depending on the fermentation style (top vs bottom fermenting).
- Heat Exchanger: Critical for controlling temperatures during the brewing process, especially post-boiling.
- Control Panel: For automating processes and ensuring consistent brewing.
- CIP (Clean-In-Place) System: For easy cleaning and maintenance of brewing equipment.
Types of Equipment in a 500L Brewing System
Component | Description |
---|---|
Brewhouse | Central to the brewing process, often consists of mash, lauter, boil, and whirlpool kettles. |
Fermentation Tanks | Where the beer ferments. The number of tanks depends on production needs. |
Heat Exchanger | For cooling the wort quickly after the boiling process. |
Control Panel | Manages temperature, timing, and other key brewing processes. |
CIP System | A Clean-in-Place system to facilitate easy cleaning without disassembling equipment. |
Glycol Chiller | Maintains the temperature of fermentation tanks, ensuring a stable environment for fermentation. |
The Brewing Process Using a 500L Brewing System
The brewing process remains largely consistent whether you’re brewing at home or on a commercial scale, but a 500L brewing system comes with added sophistication for precision and volume control. Below is a breakdown of the brewing stages:
- Mashing: Grains are soaked in hot water to activate enzymes that convert starches into sugars. In a 500L system, the mash tun can handle large quantities while ensuring even heating and stirring.
- Lautering: Once mashing is done, the liquid wort is separated from the grain solids in the lauter tun. This stage is crucial for ensuring clarity in the wort.
- Boiling: The wort is then boiled to sterilize it and allow for the addition of hops, which gives beer its flavor and aroma.
- Whirlpooling: This step helps to separate the solid particles from the liquid before fermentation. A well-designed whirlpool tank is key in a 500L brewing system for efficient particle removal.
- Fermentation: The cooled wort is transferred to the fermentation tanks where yeast is added. The fermentation tanks in a 500L system are designed to handle the volume and maintain the required temperature.
- Conditioning: Post-fermentation, the beer is conditioned for several weeks to improve flavor and clarity before being packaged.
Capacity, Space, Design, and Layout of a 500L Brewing System
The layout and design of a brewing system are essential for efficient production and to ensure that the space is utilized effectively. A 500L system is versatile in its configuration, but here are key considerations:
Parameter | Details |
---|---|
Capacity | 500L per batch, suitable for small-scale commercial brewing. |
Space Requirements | Requires about 60–100 square meters depending on the setup and storage needs. |
Design | Customizable with options for manual or semi-automatic control. Typically made from stainless steel for durability and easy cleaning. |
Layout | Can be designed in a linear or compact configuration depending on the space available and workflow optimization. |
Customization | Options for additional equipment, automation, and tank sizing depending on specific brewery needs and budget. |
Price Range and Suppliers of 500L Brewing Systems
The price of a 500L brewing system can vary depending on the brand, materials, and additional features. Below is a table with an overview of suppliers and their typical price ranges.
Supplier | Price Range (USD) | Customization Options |
---|---|---|
ABC Brewing Solutions | $50,000 – $70,000 | Custom configurations available for brewhouse layout |
BrewTech Systems | $60,000 – $80,000 | Offers full automation options and custom fermentation tanks |
SS BrewTech | $55,000 – $75,000 | Stainless steel construction with advanced control panels |
Deutsche Beverage Technology | $65,000 – $90,000 | High-end systems with modular design |
Tiantai Brewing Equipment | $40,000 – $65,000 | Customizable sizes, international shipping |
Installation, Operation, and Maintenance of a 500L Brewing System
Installing a 500L brewing system requires precision and expertise to ensure smooth operation. While many suppliers offer installation services, the brewery owner must understand the system’s operation and maintenance requirements.
Aspect | Details |
---|---|
Installation | Typically done by the supplier, including setup of tanks, piping, and control systems. |
Operation | Can be manual, semi-automatic, or fully automated. The control panel helps manage brewing temperatures, timing, and other factors. |
Maintenance | Regular cleaning using the CIP system is essential. Annual servicing of control panels and heat exchangers is recommended. |
How to Choose a Supplier for a 500L Brewing System
Choosing the right supplier is crucial for ensuring quality and efficiency in your brewing process. Here are some factors to consider:
Factor | Details |
---|---|
Reputation | Look for suppliers with positive reviews and a history of successful installations. |
Customization Options | Ensure the supplier offers the ability to tailor the system to your specific needs, such as adding more fermentation tanks or adjusting the layout. |
Support and Training | Check if the supplier provides after-sale support and training for staff to operate the system. |
Price vs. Quality | Balance cost with the quality of materials used (e.g., stainless steel). Avoid low-priced systems with cheap components. |
Warranty and Service | A good supplier will offer a warranty and regular service options to maintain the system’s efficiency. |
Advantages and Limitations of a 500L Brewing System
Like any brewing system, the 500L setup has its advantages and disadvantages, depending on your specific needs.
Advantages | Limitations |
---|---|
Produces enough beer for small-scale commercial operations | Requires more space and investment compared to smaller systems |
Customizable to fit specific brewing styles or requirements | May not be sufficient for larger-scale commercial production |
Efficient and scalable for growing breweries | Installation and maintenance costs can be high |
Can be semi-automated or fully automated | Higher complexity requires skilled operators |
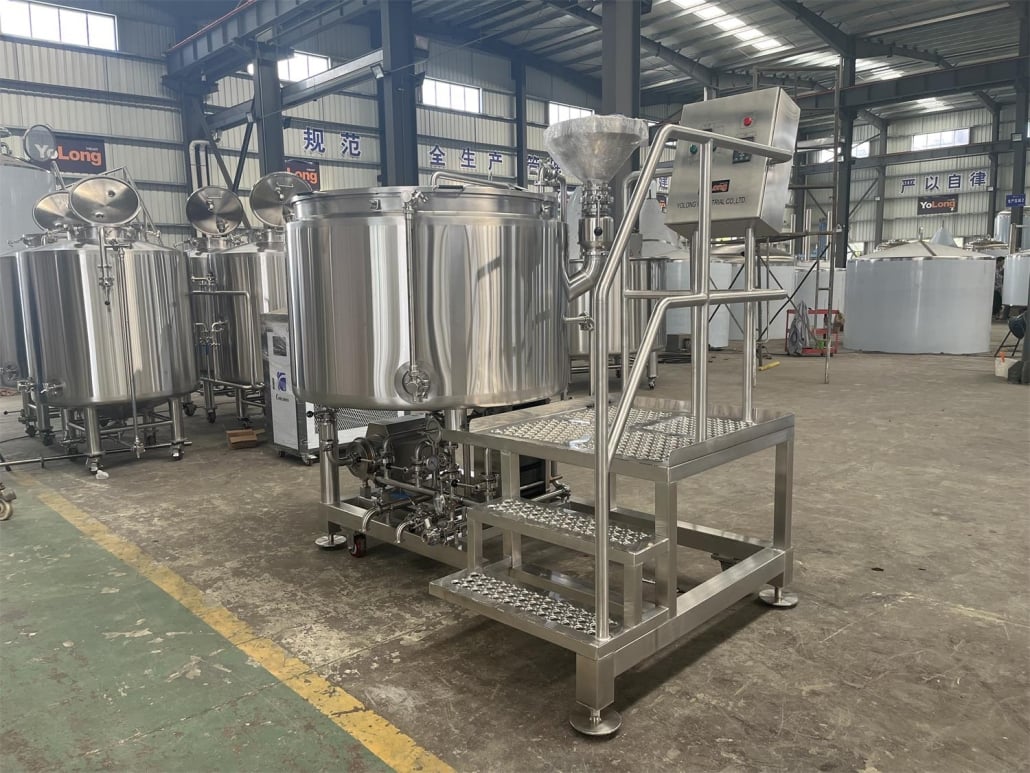
FAQs
Question | Answer |
---|---|
How much space does a 500L brewing system require? | Approximately 60–100 square meters depending on the system’s layout and additional storage requirements. |
Can I customize the 500L brewing system to my specific needs? | Yes, most suppliers offer a range of customization options including tank sizes, control systems, and brewhouse configurations. |
How much does a 500L brewing system cost? | Prices typically range from $40,000 to $90,000, depending on the supplier, level of customization, and additional features. |
How long does it take to install a 500L brewing system? | Installation can take anywhere from a few days to several weeks, depending on the complexity of the system and the installation environment. |
Do I need special training to operate a 500L brewing system? | While basic brewing knowledge is essential, many systems come with semi-automated controls that make operation more accessible. Suppliers often offer training. |
What are the maintenance requirements for a 500L system? | Regular cleaning through the CIP system, along with annual checks and maintenance for the control panel, heat exchanger, and other critical components. |
Conclusion
A 500L brewing system is an excellent choice for small to medium-sized breweries looking to scale up production without moving into the complexities of large-scale operations. With the ability to customize, automate, and grow with your needs, this system offers a versatile solution for professional brewing. When selecting a system, consider the equipment, layout, supplier reputation, and costs to ensure you make the right investment for your brewery’s future.
Share this entry
Interested in learning more about Brewing Systems including additional details and pricing information? Please use the form below to contact us!
YOLONG BREWERY EQUIPMENT FAQS
- Commercial Brewery / Craft Brewery / Microbrewery / Nanobrewery
- What is The Difference Between Craft Beer and Industrial Beer?
- The Bespoke Differences In Custom Brewing Systems
- Everything You Need to Know About Kettle Souring
- How to Choose Brewing Equipment for Your business?
- How To Choose The-Best Partner To Build Your Commercial Microbrewing System?
- Two Detection Sensors That You Need To Use In Your Brewhouse System
- Remote Control Applications in Brewing Equipment/How does it work?
- How To Clean Your Brand New Brewery Tanks?