5 BBL Stackable Brite Tanks
5 BBL Stackable Brite Tanks refer to final conditioning vessels for clearing and carbonating beer after primary fermentation. Stackable brite tanks maximize storage in a small brewhouse footprint. We elaborate specifications, design options, installation considerations and compare suppliers of 5BBL brite tanks while highlighting best practices for operation and maintenance procedures.
5 BBL Brite Tank Equipment Guide
This table summarizes key specifications for 5BBL brite beer tanks:
Parameter | Details |
---|---|
Function | Post-fermentation conditioning |
Capacity | 5 barrels or 155 gallons |
Construction | Stainless steel – 304 or 316 grades |
Shape | Vertical or horizontal |
Jacket design | Single, half or fully jacketed |
Cooling method | Glycol, refrigerant or chilled water |
Pressure rating | 60-120 PSI typical |
Stackability | Up to 3-4 high typical |
Tank bottom | Slope or cone bottom designs |
Process connections | Sanitary tri-clamp style fittings |
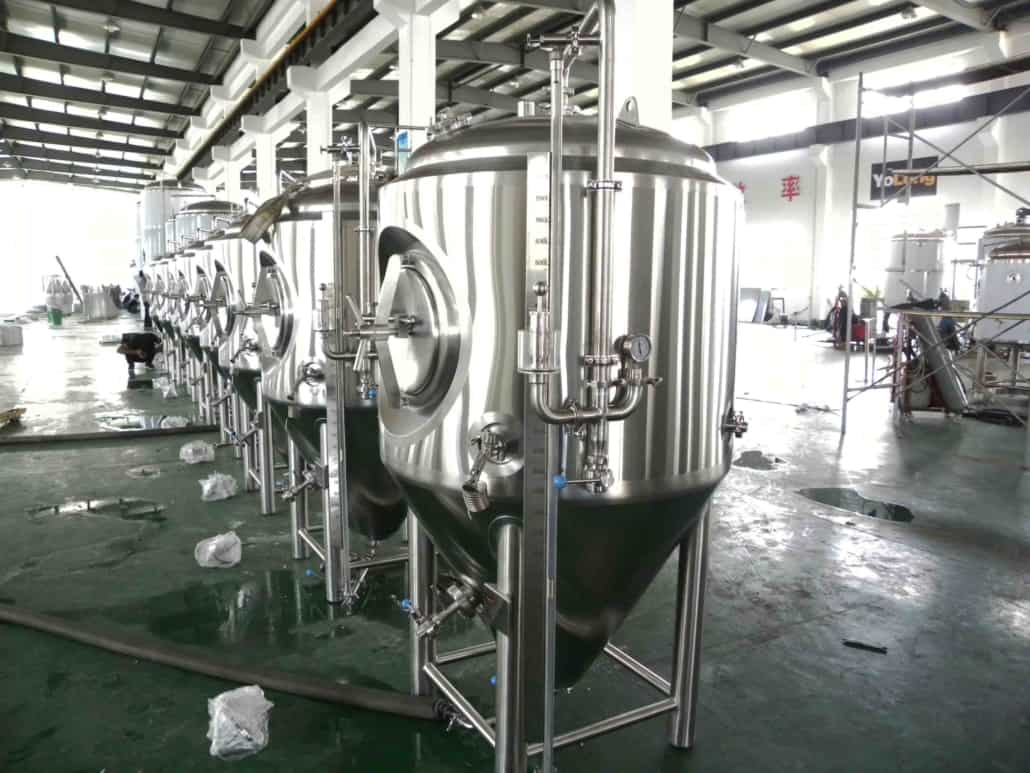
Types of 5 BBL Stackable Brite Tanks
Standard configurations include:
Vertical stackable tanks
- Most affordable simple design
- Smaller footprint stacking up to 3 high
- Top manway access hatch
Horizontal tanks
- Longer footprint, stack double rows
- Half-jacket or paddle cooled options
- Side access manway doors ease cleaning
Custom shapes
- Non-standard dimensions
- Optimized tank farms
- Uniquely designed brewhouses
5 BBL Brite Tank Design Elements
Key features differentiating quality and functionality:
Element | Options | Considerations |
---|---|---|
Inner shell | 304/316L stainless standard <10Ra finish | Meets sanitation requirements |
Outer Shell | 304 stainless typical | Protect tanks in exposed settings |
Insulation | 1-2” injected foam | Saves energy; dampens noise |
Cooling jacket | Half, three-quarter or full jacket | Balance performance and first costs |
Stack frames | Carbon steel stands | Reinforced floors; anchor to walls |
Manways | Round ports with camlocks | Convenient top/side entry access |
CO2 inlet | Carbonation stone diffusers | Adjustable regulators for precise volumes |
Sample valve | Pull mid-conditioning samples | Ensure clarity and taste prior to packaging |
Sight/light glass | Visual inspection | Borosilicate or stainless steel |
Mixing | Sanitary centrifugal pumps | Avoid foaming delicate beers |
Flow meters | Volumetric transfers in/out | Match packaging rates; prevent spills |
CIP sprayball | Interior spray cleaning | Automated cycles reduce labor |
5 BBL Stackable Brite Tank Suppliers
Company | Base Price Range | Offerings |
---|---|---|
JV Northwest | $7,500 to $11,000 | Cost-effective stock tanks; fast delivery |
SS Brewtech | $9,000 to $15,000 | UniTanks; modular upgrades |
AAA Metalcraft | $12,000 to $22,000 | Fully customized tanks |
Psycho Brewatic | $15,000 to $30,000 | Specialize in multi-stack systems |
Premier Stainless | $18,000 to $45,000 | Industry leading quality |
Spike Brewing | $20,000 and up | Innovative Micro Consul design |
American Beer | $22,000 to $38,000 | Broad selection; feature packages |
Additional tank fabricators exist nationwide. Evaluate design quality, warranty terms lead times and landed pricing.
Installing 5 BBL Stackable Brite Tanks
Proper installation ensures safety, functionality and serviceability:
System | Requirements | Specs |
---|---|---|
Electrical | Dedicated 230V outlets per tank | NEMA 6-15R receptacles typical |
Plumbing | Potable hot/cold 0.5” NPT | Individual isolation valves |
Flooring | 4” minimum concrete thickness | Grade beams if mezzanine supported |
Ventilation | Roof jack with fan | Avoid pressure buildup |
Platform | Diamond plate stair access | Safety railings for 4ft+ work areas |
Seismic | Bolted floor anchors | Restrict tank movement during quakes |
Delivery path | Clear wide route to tank farm | Double door access to brewhouse |
Operating 5 BBL Stackable Brite Tanks
Utilize best practices for clearing, carbonating and packaging:
Parameter | Guidelines | Tips |
---|---|---|
Filling | Bottom fill under backpressure | Prechill and CO2-purge vessel |
Cold crash | Reduce temperature 2°F daily | Promotes sedimentation; don’t freeze |
Carbonation | 8-15 PSI @ 33-40°F typical | Rock tanks for absorption; vent excess headspace CO2 |
Dry hopping | Mesh containers for easy extraction | Maintain cold temps to limit oxidation |
Transferring | Bottom draining with CO2 top-up | Avoid oxygen uptake; 0.6 micron sterile filter in-line |
Sampling | Prior to packaging approval | Taste/appearance/gravity checks ensure quality |
Tank management | First-in, first-out scheduling | Log packaging date, production lot on labels |
Maintenance of 5 BBL Stackable Brite Tanks
Routine care sustains performance, while annual preventative maintenance protects system investments:
Task | Frequency | Method |
---|---|---|
Inspect fittings | Monthly | Tighten loose tri-clamps |
Gaskets check | Monthly | Ensure door seals intact |
Visual inspection | Monthly | Check for fluid leaks indicating fouling |
Clean glycol stains | Quarterly | Inspect chiller heat exchangers |
Lubricate gaskets | Quarterly | Apply o-ring safe lubricant |
Inspect insulation | Annually | Patch damage; replace if mold an issue |
Test pressure relief valves | Annually | Safely discharge test gas |
Check stacks/frames | Annually | Re-tighten anchor bolts; touch up paint |
Calibrate sensors | Annually | Certify accuracy of pressure, temperature sensors |
Selecting a 5 BBL Brite Tank Fabricator
Assess providers across these weighted criteria:
Criteria | Weight | Notes |
---|---|---|
Construction quality | 15 | Welds, finish, dimensional tolerances |
Feature set offered | 10 | Assess usefulness for your needs |
Customization capability | 10 | Unique tank geometry if needed |
Freight/Lead time | 10 | Ensure delivery fits project schedule |
Install support offered | 5 | On-site guidance value |
Warranty terms | 10 | At least 1 year workmanship |
Service reputation | 15 | Response times, expertise, availability |
Client references | 10 | Aim for local brewers as references |
Brand reputation | 15 | Google reviews and testimonials |
Comparing Vertical vs Horizontal 5 BBL Brite Tanks
Parameter | Vertical | Horizontal |
---|---|---|
Footprint efficiency | Superior stacking in tight spaces | Consumes more floor space |
First cost per barrel | Lower capital outlay | Cost premium for variable diameter horizontal builds |
Ergonomics | Top hatch entry ergonomically challenging | Side ports improve accessibility |
Transfer flexibility | Typically only one connection point | Often designed with multiple process ports at different levels |
Cleanability | Requires tank climbing for inspection and scrubbing | Easier manual and automated CIP cleaning |
Flexibility | Simple up/down stack logistics | Side by side installation; rearrange tank farm layout |
Mixing effectiveness | Generally inferior due to shape | Better flow dynamics and pump suction |
Construction lead times | Shorter delivery common | Horizontal builds often longer lead times |
Key Advantages of 5 BBL Stackable Brite Tanks
- Stack up to 4 high saving floorspace
- Fast delivery times for stock model vertical tanks
- Lower capital costs than fermenters
- Chill brightness and dial-in carbonation ideal for packaging
- Safely store filtered beer avoiding concessions
- Simplified cleaning versus fermenters
- Standardized parts between tanks
- Scale tank farms out over years
- Easy relocation and rearrangement
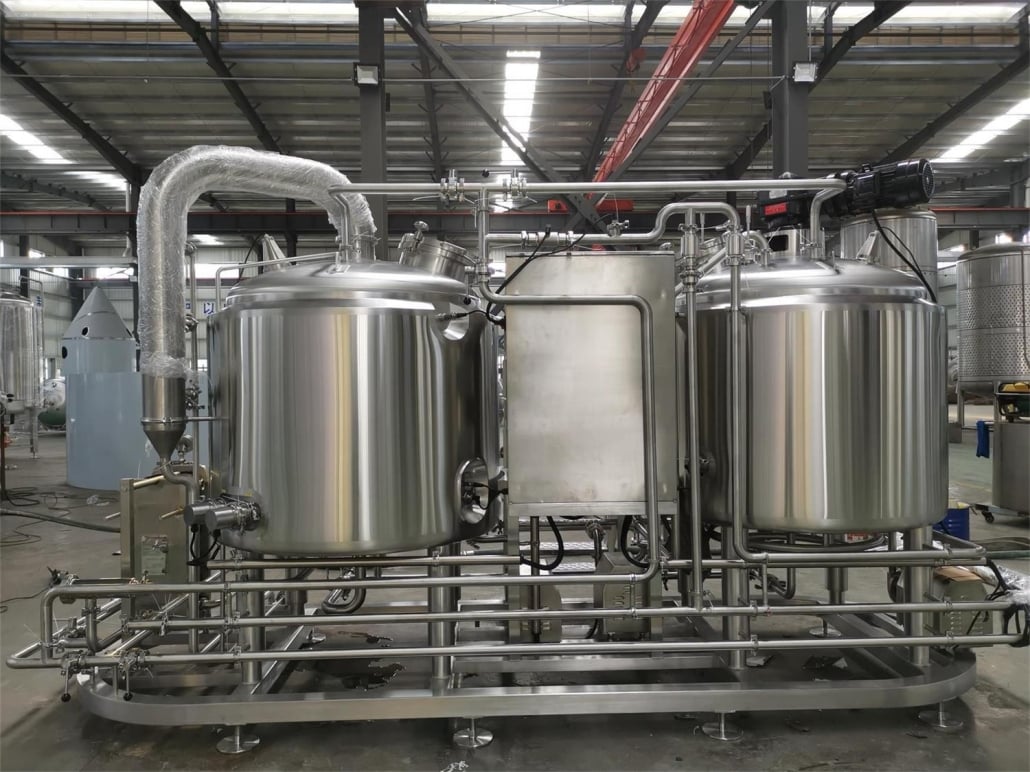
Limitations of 5 BBL Stackable Brite Tanks
- Ceiling height restrictions may limit vertical stacking
- Access hatches ergonomically challenging
- Insufficient mixing can lead to temperature stratification without agitator pumps
- Require gently transferred chilled beer to avoid foaming
- Premium charged for non-standard dimensions
- Longer lead times for custom tank designs presently
- Conditioning requires longer tied-up tank time versus fermentation
- Additional space needed for glycol chiller units
FAQ
What is the typical footprint for a 5BBL brite tank system?
A stacked set of two 5BBL brite tanks with elevated staging platform occupies roughly a 6ft x 6ft area. Horizontal tanks consume more floorspace with their elongated dimensions.
How many turns can brewers expect yearly from a 5BBL brite system?
With adequate tank capacity averaging 3 weeks pre-packaging residence time, a conservatively projected annual turn rate equates to 15-18 batches. At faster throughput with just 1 week conditioning, upwards of 25 batches are possible yearly.
Is heat exchanger cooling superior to glycol jackets for brite tanks?
Plate heat exchangers can save initial costs and energy for some brewhouse scales. However glycol allows precise temperature control within 0.1°F, handles frequent duty cycling well, and enables lowering the process fluid below groundwater temps for maximum chilling. Glycol systems suit small batch producers aiming for very consistent tanks.
Should I insulate brite tanks?
While foam insulation theoretically conveys thermal savings, the reality is exposed vertical tanks gain negligible efficiency especially once opened routinely. Prioritize jacketing only the most heavily utilized conditioning tanks.
What material should brite tank access hatches be constructed from?
Type 304 stainless steel with double compression seals makes for durable, chemical resistant hatch construction. Many fabricators offer round manway ports reduced to just 12” diameter improving ergonomics. Spec doors you can comfortably open/close at maximum reach height.
Which manufacturers offer the most advanced monitoring capabilities?
Look to Progressive Stainless, AAA Metalcraft and Spike Brewing for innovative monitoring and automation feature options like wireless temperature monitoring with data logging, integrated flow meters with batch tracking, and touchscreen PLC interfaces with smartphone connectivity for notifications. Expect premium pricing but gain operational insight.
Share this entry
Interested in learning more about Brewing Systems including additional details and pricing information? Please use the form below to contact us!
YOLONG BREWERY EQUIPMENT FAQS
- Commercial Brewery / Craft Brewery / Microbrewery / Nanobrewery
- What is The Difference Between Craft Beer and Industrial Beer?
- The Bespoke Differences In Custom Brewing Systems
- Everything You Need to Know About Kettle Souring
- How to Choose Brewing Equipment for Your business?
- How To Choose The-Best Partner To Build Your Commercial Microbrewing System?
- Two Detection Sensors That You Need To Use In Your Brewhouse System
- Remote Control Applications in Brewing Equipment/How does it work?
- How To Clean Your Brand New Brewery Tanks?