Overview of 5 BBL Brew Kettles
A 5 BBL Brew Kettle, also called a brewing copper or brewkettle, is a critical vessel in a brewhouse used for boiling wort and adding hops. This guide covers what a 5 BBL brewkettle is, details on configurations and terminology, kettle design considerations, process guidance, customization options, top suppliers and pricing, installation and operation recommendations, and comparisons of different 5 BBL kettles.
What is a Brew Kettle?
A brew kettle, or copper, is a stainless steel vessel used for:
- Boiling wort after mashing – coagulating proteins, sterilizing, extracting hop flavors
- Clarifying and separating trub particles via whirlpooling action
- Holding hot boiled wort prior to fermentation
Key kettle design elements:
- Heavy duty stainless construction to withstand vigorous boiling
- Efficient heating system – steam, direct fire, or electric elements
- Mixing or whirlpool tangential inlets for circulating wort
- Cone bottom design allows trub to settle
Kettles range from 3-15+ BBL sizes for commercial breweries producing up to 3,000 bbls annually. 5 BBL is a common starter scale.
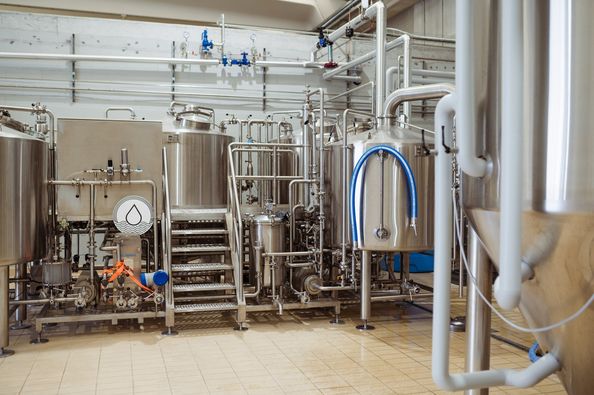
5 BBL Brewing Kettle Equipment Guide
Below summarizes key terminology on 5 BBL kettles and brewhouse vessels:
Vessel | Purpose |
---|---|
Mash Tun | Convert mashed grain starches to fermentable sugars via enzyme activation |
Lauter Tun | Separate sweet wort from spent grains after mashing |
Brew Kettle | Boil wort with hops for bitterness, flavor, aroma |
Whirlpool | Spin hot wort to remove trub particles using centrifugal force |
Heat Exchanger | Rapidly cool boiled wort before yeast is pitched to ferment |
Fermenter | Ferment sugar into alcohol and carbon dioxide |
The brew kettle imparts significant flavor and aroma qualities through wort boiling, hop additions, and hot side clarification processes.
5 BBL Brew Kettle Design and Layout
When configuring a 5 BBL brew house kettle system, key elements to consider include:
Dimensions
- Typically under 7 ft tall to allow manual hop dosing
- 42-48 inch diameter to prevent boil overs
Material
- 304 or 316 stainless construction
- Optional exotic alloys improve heat transfer
Heating System
- Direct fire, steam jacketed, electric elements
- Hybrid systems balance speed, precision of temperature ramps
Agitation
- Spinning inlet or external recirculation for mixing
- Whirlpool tangential inlet to spin out particles
Transfer Piping
- Inlet valves for filling, steaming, recirculation
- Pump out transfer line, sight glass, volume markings
Automation
- Programmable controllers to track/log temps, valve states, runoff trajectories
Optimize staging distances to prevent stuck sparges while enabling efficient wort transfers.
5 BBL Commercial Brewing Process Overview
The key functions the brew kettle performs in a commercial 5 BBL brewhouse process:
Transfer – After lautering, sweet wort is transferred to the brew kettle at the start of a vigorous 60-90 minute boil.
Boiling – The wort is brought to a rolling boil to sterilize it, halt enzymatic activity, extract hop oils, concentrate sugars and proteins, and develop desired color and flavors. Boil strength impacts hop utilization.
Hop Addition – Hops are added at stages over the boil timeline to contribute targeted bitterness, flavor and aroma attributes to the beer.
Coagulation – Heat and hop compounds cause proteins and tannins to coagulate into particles that will later settle as trub.
Clarification – A whirlpool rest circulates wort to use centrifugal force to spin coagulated particles into a cone at the bottom center of the kettle. This clarifies the wort prior to transferring to the fermenter.
Holding – After chilling, finished boiled wort waits in the sanitized brew kettle for a period before getting pitched with yeast in the fermenter.
The tuning of temperatures, timing, hop dosing, circulation patterns, and holding durations in the brew kettle significantly impacts final beer quality, consistency and efficiency.
5 BBL Brew Kettle Customization
While 5 BBL brew kettles have typical capacity targets and standard features, many customization options exist:
Element | Customization Choices |
---|---|
Height/Diameter | Dimensioning based on brewhouse space |
Heating Method | Steam, electric elements, direct fire |
Agitation | Mixing pumps or custom tangential inlets |
Automation | Tailored controllers, sensors, data logging recipes |
Materials | Exotic alloys, interior polish, enhanced coatings |
Geometry | Conical vs cylindrical, angle of conical bottom section |
Ports | Sample valves, sight glasses, cleaning ports |
Options | Integrated whirlpool, wort aeration, heat exchanger |
Work with your brewhouse design team to optimize kettle configuration for your HOPPING schedules, vigor targets, and manual vs automated processes.
5 BBL Brew Kettle Suppliers and Price Range
There are a number of reputable kettle suppliers with quality 5 BBL solutions costing $8,000 to $15,000 depending on features. Custom exotic alloy kettles with extensive automation can run over $20k.
Supplier | Price Range |
---|---|
Specific Mechanical | $9,000 – $13,000 |
Stout Tanks | $8,000 – $12,000 |
Premier Stainless | $10,000 – $14,000 |
Pro Engineering | $9,000 – $13,000 |
Portland Kettle Works | $12,000 – $16,000 |
Additional stainless fabrication suppliers to evaluate include AAA Metal Fabrication, Stellar Brew Equipment, The Vintner Vault, Craftwerk, Spike Brewing, and Psycho Brew. Chinese manufacturers can hit lower price points but generally lack quality controls or customization flexibility compared to US shops.
How to Choose a Reliable Brew Kettle Supplier
Critical factors in selecting a brew kettle partner include:
Criteria | Evaluation Aspects |
---|---|
Build Quality | Material grades, precision fabrication, welds, finishing |
Feature Set | Standard platform vs customizable options |
Customer Service | Responsiveness, order support, issue resolution |
References | Other customers vouching for product and service |
Production Times | Experience meeting lead time targets |
Value | Price relative to quality level and features |
Terms | Payment schedule, warranty coverage, maintenance options |
Thoroughly evaluate vendors on complete picture criteria, not just upfront equipment pricing. Leverage industry references to guide selection. See what existing brewers have to say about supplier relationships beyond the sale.
5 BBL Brew Kettle Installation, Operation and Maintenance
Correct kettle installation, operation, and preventative maintenance ensures performance longevity, safety and beer consistency:
Activity | Description |
---|---|
Installation | Mounting, welding connections, wiring elements, testing valves/piping before first batch. May require contracting. |
Operation** | Following HOPPING, cleaning, transfer standard procedures each batch. Monitoring temps, flows, valve states. |
Maintenance | Inspecting seals, gaskets, replacing worn parts, cleaning, leak checks, instrument calibration. |
Work closely with your equipment provider for installation guidance, operator training, and suggested maintenance programs per batch and annually. Draft SOPs covering kettle procedures during knockout, transfers, cleaning, inspecting, and troubleshooting.
Key Advantages Between 5 BBL Brew Kettle Configurations
Principal alternatives along with relative pros and cons include:
Pros | Cons | |
---|---|---|
Electric Kettle | Precise temp control <br> No boiler required <br> Lower operating costs | Slow ramp up and down <br> Higher install cost |
Steam Kettle | Faster heating <br> Lower install cost <br> Proven longevity | Less precise control <br> Needs steam source |
Direct Fire Kettle | Powerful rapid heating <br> Lower equipment cost | Less consistent control <br> Safety considerations |
Evaluate options against production goals – batch cycle times, automation plans, vapor emissions regulations etc. If focusing on specialty beers, optimize for precision temperature manipulation over speed.
Key Brew Kettle Investment Considerations
As a core brewhouse component shaping beer quality over years, judiciously investing in a brew kettle entails:
- Prioritizing stainless steel grades and fabrication quality – impacts longevity
- Considering expansion plans – space, production scaling, automation goals
- Focusing on heating control precision if brewing delicate beer styles
- Comparing kettle ROI vs other brewhouse equipment investments
- Researching suppliers thoroughly – chat with existing customers on performance
- Budgeting for installation, training, maintenance beyond unit price
Avoid oversizing relative to batch targets losing efficiency and control advantages from customized, smaller dimensioning. But ensure adequate height for hop dosing ergonomics and foaming head space. Seek to balance value, consistency, and flexibility for current and future plans when investing.
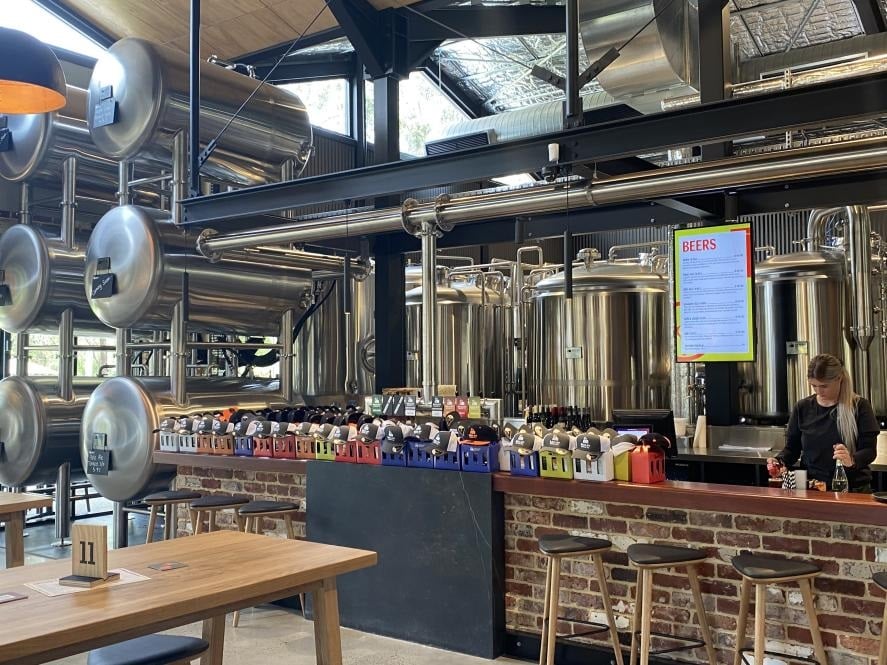
FAQ
Q: What is typical pricing for a new 5 BBL brew kettle?
A: A 5 BBL brew kettle typically costs $8,000 – $15,000 depending on material choices, heating systems, and feature sets from US stainless fabricators. Fully customized systems with exotics and automation can exceed $20k.
Q: What are standard dimensions for 5 BBL kettles?
A: Many 5 BBL kettles are around 84 inches (7 ft) tall x 42-48 inches wide. Exact sizing depends on batch targets, vigor space, and layout. Custom dimensional configuring is common.
Q: Should I choose steam, electric, or direct fire heating?
A: Each system has pros and cons. Steam offers rapid heating important for some beer styles but precision temperature control is harder. Electric gives precise control for delicate beers but slower. Direct fire brings vigor but variability. Many kettle use hybrid heating approaches.
Q: How many hop additions do 5 BBL kettles support?
A: Most 5 BBL kettles offer 3-5 hop addition ports positioning hops for early kettle bitterness, late kettle flavor, and aroma stages. More custom ports can be included.
Q: What material should I choose for my brew kettle?
A: 304 stainless steel is standard for most 5 BBL kettles. 316 has higher corrosion resistance. Optional exotic metals like copper can enhance conductivity and boiling action but add cost.