2 BBL Stackable Brite Tanks
Brite tanks, also known as bright beer tanks, are stainless steel vessels used for clarifying, conditioning and carbonating beer after primary fermentation and before packaging. This guide covers 2 BBL Stackable Brite Tanks including types, design, sizing, suppliers, pricing, installation, operation, maintenance and comparisons.
Overview of 2 BBL Stackable Brite Tanks
2 BBL refers to a tank size holding approximately 2 barrels or 62 gallons. Stackable tanks allow vertically interlocking multiple units to save floor space. Key features of quality brite tanks:
- Stainless steel material – durable and easy to clean
- Stackable conical or cylindrical shapes
- Jacketed cooling and insulation
- CIP sprayballs for cleaning
- Glycol/steam heating and chilled water cooling
- Sanitary fittings – valves, ports, tubing, sight glasses and more
- Pressure rated vessels supporting carbonation
- Automated cleaning/filling capabilities
Stackable brite tanks provide flexible vessel options for bright beer handling – clarifying, aging, carbonating and storing craft beer between fermentation and packaging.
Benefits of 2 BBL Stackable Brite Tanks
- Save floor space with vertical footprint
- Scale capacity adding more tanks
- Flexible beer transfer with multiple tanks
- Automated cleaning and sanitation
- Consistent beer quality and carbonation
- Small batches for experimental recipes
- Cylindrical or conical tanks available
Typical 2 BBL Brite Tank Specifications
Parameter | Typical Specification |
---|---|
Size | 2 BBL/62 Gallons |
Height | 73 – 96 inches |
Diameter | 20 – 24 inches |
Material | Stainless Steel (304 or 316) |
Construction | Fully Welded |
Finish | Interior Polish < 10 Ra |
Couplings | Tri-clamp fittings |
Insulation | 1- 2″ Foam or Jacket |
Cooling System | Glycol Heat Exchanger + Chilled Water |
Heating System | Steam, Electric or Hot Water Heat Exchanger |
Temperature Range | 33- 80°F |
Pressure Rating | 60-150 psi |
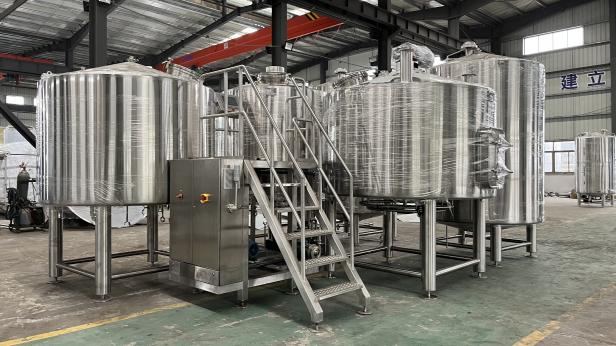
Types of 2 BBL Stackable Brite Tanks
2 BBL brite tanks are commonly available in two configurations suitable for stacking:
Cylindrical Tanks
- Vertical orientation
- Flat tank ends
- Rest on integrated frame with casters
- Simple internal design
- Lower cost option
Conical Stackable Tanks
- Sloped cone bottom
- Require interlocking kits
- Stainless steel legs
- Rotate tanks for outlet access
- Higher quality construction
- Facilitate complete drainage
Other specialty brite tank styles like horizontal or custom tanks are possible but less common at the 2 BBL scale.
Table: 2 BBL Stackable Brite Tank Models
2 BBL Model | Type | Dimensions | Frame Kit |
---|---|---|---|
Uni-Brite | Cylindrical | 24x24x73 inches | Optional |
Nano Cylindrical | Cylindrical | 20x20x75 inches | Integrated |
Micro-Conical | Conical | 24x24x96 inches | Required |
Nano-Conical | Conical | 22x22x84 inches | Required |
2 BBL Brite Tank Design and Customization
2 BBL brite tanks provide a range of standard and optional features to match brewery preferences:
Table: 2 BBL Stackable Brite Tank Design Aspects
Design Aspect | Options |
---|---|
Material | 304 or 316L Stainless Steel |
Construction | Fully Welded, Spun Metal |
Finish | Electropolish <10 Ra, Passivation |
Insulation | Foam, Jacketed |
Cooling/Heating | Glycol, Steam, Electric |
Automation | Programmable PLC, Sensors |
Fittings | Tri-clamp, Threaded, Flanged |
Ports | Thermowells, Sight Glasses |
Geometry | Cylindrical, Conical, Custom Shapes |
Frame | Casters, Stationary Legs, Interlocks |
Compliance | ASME, CRN, CE, UL-508A |
Options | Level Meters, Lighting, Platform Ladder |
Most suppliers offer additional upgrades like automated temperature and level sensors, variable frequency drive pump systems, integrated chilling with remote condensing units and custom solutions tailored unique needs.
Conical geometries allow complete drainage for transfer flexibility but require interlocking kits or platforms. Cylindrical tanks are simpler and thus more budget friendly. Optimize accessories and tank type based on production scale, space and budget considerations. Quality USA-made small batch brite tanks balance affordability with functionality.
2 BBL Stackable Brite Tank Suppliers & Pricing
Quality stainless steel brite tanks sized at 2 BBL are commonly available from $3000-$7000 based on features. Many USA suppliers manufacture tanks and can customize models.
Table: 2 BBL Stackable Brite Tank Suppliers
Supplier | Location | Tank Models |
---|---|---|
Ss Brewtech | USA | Uni-Brite Cylindrical |
Spike Brewing | USA | Nano-Conical, Nano Cylindrical |
JV Northwest | USA | Variety of shapes/sizes |
American Beer Equipment | USA | Uni-tank Cylindrical |
Premium Stainless | Canada | Micro-Conical |
Table: 2 BBL Stackable Brite Tank Sample Pricing
2 BBL Model | Type | Average Price Range |
---|---|---|
Uni-Brite | Cylindrical | $3000 – $4500 |
Nano Cylindrical | Cylindrical | $3200 – $5000 |
Micro-Conical | Conical | $5000 – $7000 |
Nano-Conical | Conical | $4000 – $6000 |
Exact pricing varies based on specifications chosen. Get quotes from multiple vendors on different tank models to fit quality, functionality, budget and lead time needs.
Installing and Operating Stackable Brite Tanks
Proper brite tank installation and operation ensures quality beer production:
Table: 2 BBL Stackable Brite Tank Installation & Operation
Parameter | Guidelines |
---|---|
Location | Indoors, level surface; access to utilities |
Setup | Level tanks; interlock conicals securely |
Connections | Tri-clamp fittings for fluid lines |
Safety | Pressure relief valves; SOPs |
Cooling | Connect glycol/chiller lines per spec |
Filling | Bottom fill inlet with top outlet |
Process | Adjust temperature, carb level, residence time per beer type |
Cleaning | Automated CIP sprayballs; chemical wash |
Maintenance | Inspect fittings, gaskets; replace wear parts |
Ideally integrate brite tanks into an automated brewhouse system for temperature control, cleaning and fluid transfer. Stagger interlocks between tanks to allow pump and valve clearance. Position cylindrical tanks on casters for mobility or bolt conicals securely to platform legs. Follow all pressure guidelines and safety procedures during operation.
Considerations for Selecting Brite Tanks
Analyze brewery goals, production scale and growth plans when selecting brite tanks:
Table: How to Choose 2 BBL Stackable Brite Tanks
Decision Factor | Details |
---|---|
Production Volume | Current and 5 year projected batch sizes |
Beer Variety | Lagers, ales, specialty beers dictate parameters |
Design Quality | Construction, fittings, geometry, finish |
Dimensions | Height, diameter limits; floor space |
Automation | Gauges, sensors, actuators needs |
Delivery Timelines | Standard lead times vs expedited |
Budget | Compare vendor quotes; factor options, shipping |
Location | Supplier proximity for service and support |
Standards | ASME, CRN certification; metric sizing |
Prioritizing quality, flexibility and automation support will maximize longevity of the tanks as a brewery grows. Conical interlocking kits require more upfront effort to integrate but enable condensed footprint and draining capabilities.
Pros and Cons of 2 BBL Stackable Brite Tanks
Table: Advantages & Disadvantages of Stackable Brite Tanks
Pros | Cons |
---|---|
Vertical small footprint | Initial equipment investment |
Flexible production scale | Conical tanks require interlocks/platform |
Portable cylindrical tanks | Thermal mass retains temperature |
Automated cleaning systems | Condensation concerns need mitigation |
Well engineered fittings, ports, valves | Control complexity scales with tanks count |
Many USA suppliers to choose from | Delivery lead times up to 12 weeks |
Scalable capacity adding more tanks | Requires indoor temperature controlled space |
Enable experimental and specialty batches | Staff training for operations and maintenance |
For pilot systems or brewpubs, stackable brite tanks balance efficient use of space with modular functionality to grow. Simpler cylindrical tanks can work for starting small while still offering automated cleaning and controls.
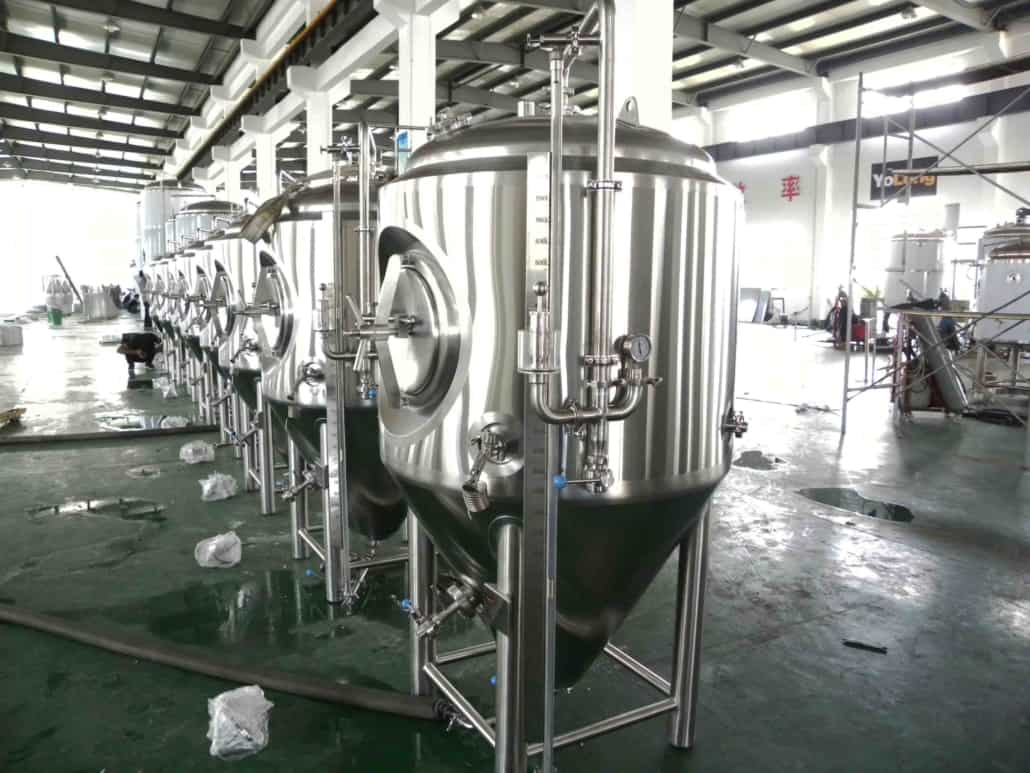
Frequently Asked Questions
How many 2 BBL brite tanks are ideal to start with?
A minimum of two tanks allows one tank for clearing/cooling while another fills from fermentation, with room to grow. This enables overlapping processing between cycles. Plan tank quantities based on the brewhouse batch frequency and peak beer demand.
What are the easiest portable tanks to use?
Cylindrical brite tanks around 7 feet tall with casters integrated on the frame offer the most convenience for mobility compared to conicals requiring interlocking. Opt for a single unit with integrated cooling instead of a series of tanks.
What degree of automation should be used?
Ambitious breweries will benefit from programmable PLC controls enabling timed CIP sequences, temperature ramps and alarms. Economical ones can start with basic thermostats and ball valves then add automated sensors and pumps later as production expands.
Is direct steam injection for heating safe in brite tanks?
Steam introduces safety hazards, pressure concerns and air pickup requiring mitigation. Indirect heating using steam exchangers or electric elements avoids these issues and facilitates precision temperature control.
How are shortened beer contact time and oxygen exposure avoided when transferring?
Bottom fill inlets with top mounted sample valves allow fluid displacement. Similarly raising outlets up the cone on conicals reduce turbulence. Keep transfers closed and chilled with jacket cooling to minimize contact time. Automated systems significantly help reduce risks.
Conclusion
With the quality stainless steel construction and commercial grade engineering needed for proper beer clarifying and carbonating, 2 BBL stackable brite tanks enable craft brewers to flexibly scale production while automating critical processes. Careful specification of dimensions, fittings, automation and accessories provides a centralized vessel solution future-proofed for growth. When configured thoughtfully to match brewery space constraints and functionality goals, brite tanks check all the boxes for delivering freshness and consistency with every pint.
Share this entry
Interested in learning more about Brewing Systems including additional details and pricing information? Please use the form below to contact us!
YOLONG BREWERY EQUIPMENT FAQS
- Commercial Brewery / Craft Brewery / Microbrewery / Nanobrewery
- What is The Difference Between Craft Beer and Industrial Beer?
- The Bespoke Differences In Custom Brewing Systems
- Everything You Need to Know About Kettle Souring
- How to Choose Brewing Equipment for Your business?
- How To Choose The-Best Partner To Build Your Commercial Microbrewing System?
- Two Detection Sensors That You Need To Use In Your Brewhouse System
- Remote Control Applications in Brewing Equipment/How does it work?
- How To Clean Your Brand New Brewery Tanks?