10 BBL Brewing Equipment
Brewing beer is a mix of art and science, and having the right equipment makes all the difference. If you’re venturing into the world of professional brewing, a 10 BBL brewing system might just be the sweet spot for your operations. Whether you’re scaling up from a smaller setup or planning your first commercial brewery, this guide will cover all the details you need to know. Let’s dive into the fascinating world of brewing with 10 BBL equipment.
Overview of 10 BBL Brewing Equipment
A 10 BBL brewing system refers to equipment designed to produce ten barrels (approximately 310 gallons) of beer per batch. This size is ideal for mid-sized breweries, brewpubs, or operations looking to balance production capacity with operational efficiency. The system typically includes components like the brewhouse, fermentation tanks, a cooling system, and supporting equipment. But what exactly makes a 10 BBL system stand out?
First off, it’s scalable. A 10 BBL system is large enough to produce commercially viable volumes yet small enough to allow flexibility in brewing different styles. Whether you’re whipping up a classic lager or experimenting with hazy IPAs, this system provides the room to play.
Let’s explore the brewing process, the common components, and how to make the most of your investment.
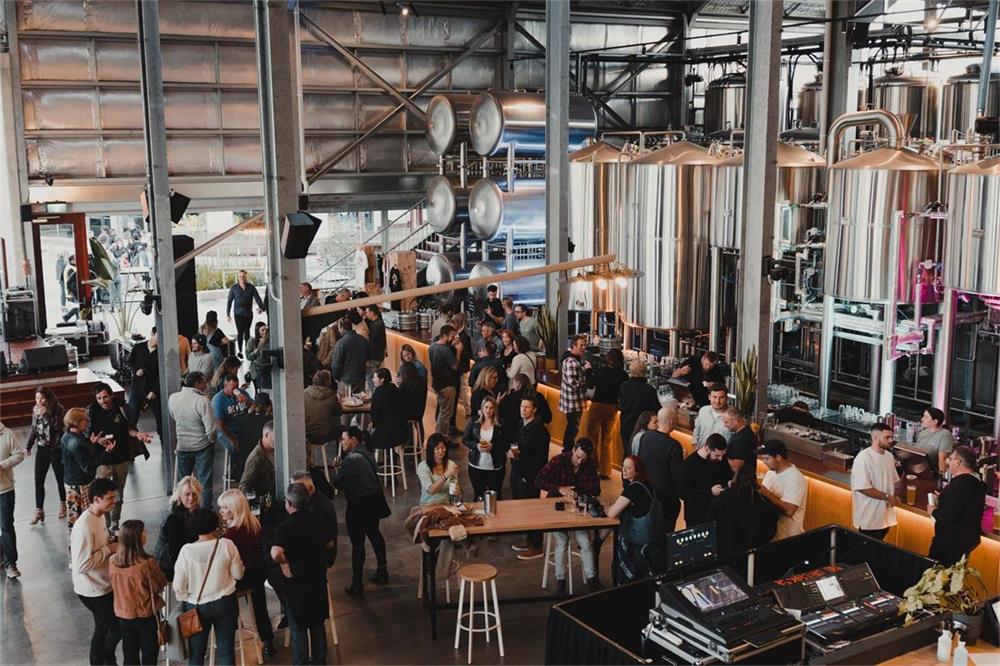
The Brewing Process with a 10 BBL System
Brewing on a 10 BBL system isn’t wildly different from smaller setups, but the scale introduces nuances that require a professional touch. Here’s an overview of the process:
- Mashing: Grains are mixed with hot water in the mash tun to extract fermentable sugars. Precision in temperature control is critical to ensure consistent beer quality.
- Lautering: The wort is separated from the grain husks. A 10 BBL system often includes a lautering tank designed to optimize efficiency and clarity.
- Boiling: The wort is boiled, and hops are added for bitterness, flavor, and aroma. Boil kettles in 10 BBL systems typically come with steam or electric heating options for consistent performance.
- Cooling: After boiling, the wort is rapidly cooled using a heat exchanger to prepare it for fermentation.
- Fermentation: The cooled wort is transferred to fermentation tanks where yeast is added. The size of a 10 BBL fermenter is perfect for achieving professional-grade results, with options for temperature control and pressure regulation.
- Conditioning and Packaging: After fermentation, the beer is conditioned to develop its flavor profile before being packaged into kegs, bottles, or cans.
Troubleshooting Common Issues with Beer Fermenters
Fermenters are the heart of any brewing operation, and they’re not without their quirks. Here are some common issues and how to fix them:
- Temperature Fluctuations: Uneven fermentation can lead to off-flavors. Invest in fermenters with advanced temperature control systems and monitor them closely.
- Contamination: Always clean and sanitize thoroughly. Residual yeast or bacteria can ruin an entire batch.
- Pressure Problems: Overpressurization can damage fermenters or compromise safety. Use pressure release valves and check them regularly.
Key Features of 10 BBL Brewing Systems
Feature | Details |
---|---|
Capacity | Designed to brew 310 gallons per batch, ideal for mid-sized operations. |
Space Requirements | Requires around 500-700 sq. ft. depending on layout and additional equipment. |
Design & Layout | Customizable designs available to optimize for linear or modular workflows. |
Materials | High-grade stainless steel construction for durability and ease of cleaning. |
Customization | Options for automated controls, steam/electric heating, and advanced monitoring systems. |
Suppliers and Price Ranges for 10 BBL Brewing Equipment
Supplier | Price Range | Special Features |
ABC Brewing Solutions | $50,000 – $80,000 | Fully customizable setups, excellent customer support |
ProBrew Systems | $60,000 – $90,000 | Turnkey solutions, automation options |
BrewTech Innovations | $55,000 – $85,000 | Energy-efficient designs, compact layouts |
Advanced Brewery Systems | $70,000 – $100,000 | High-end finishes, premium quality materials |
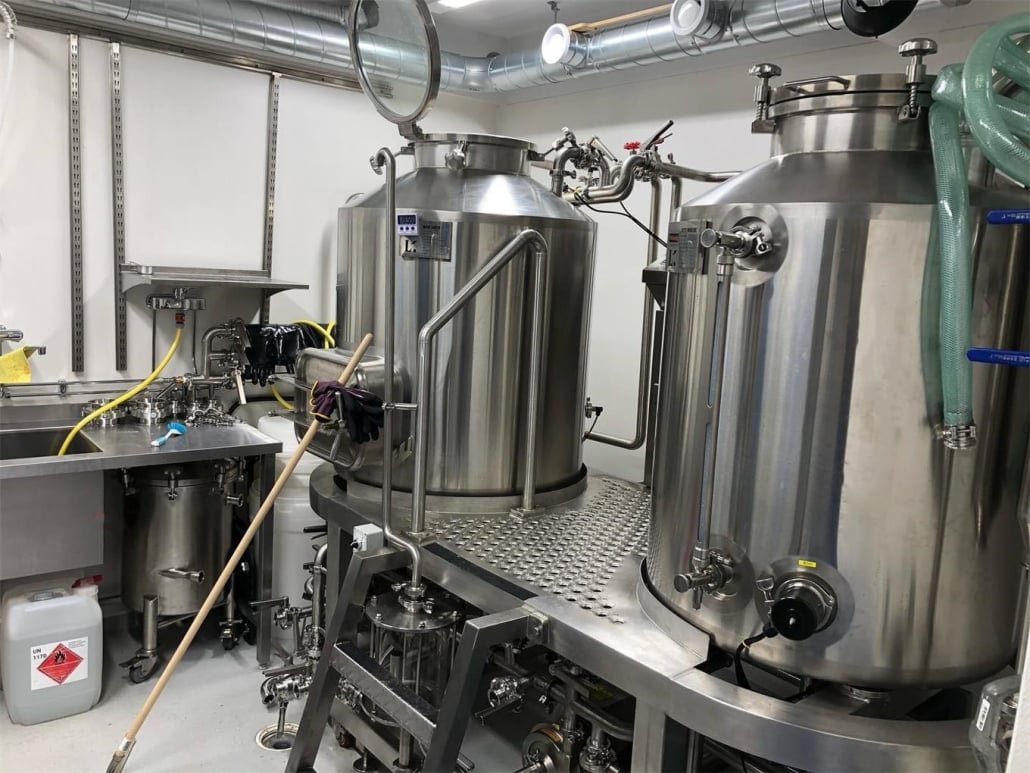
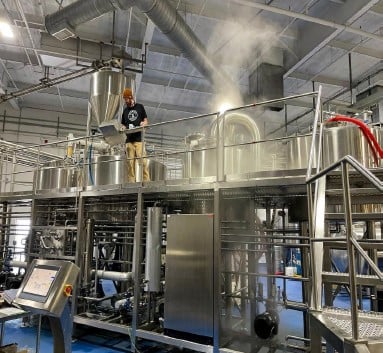
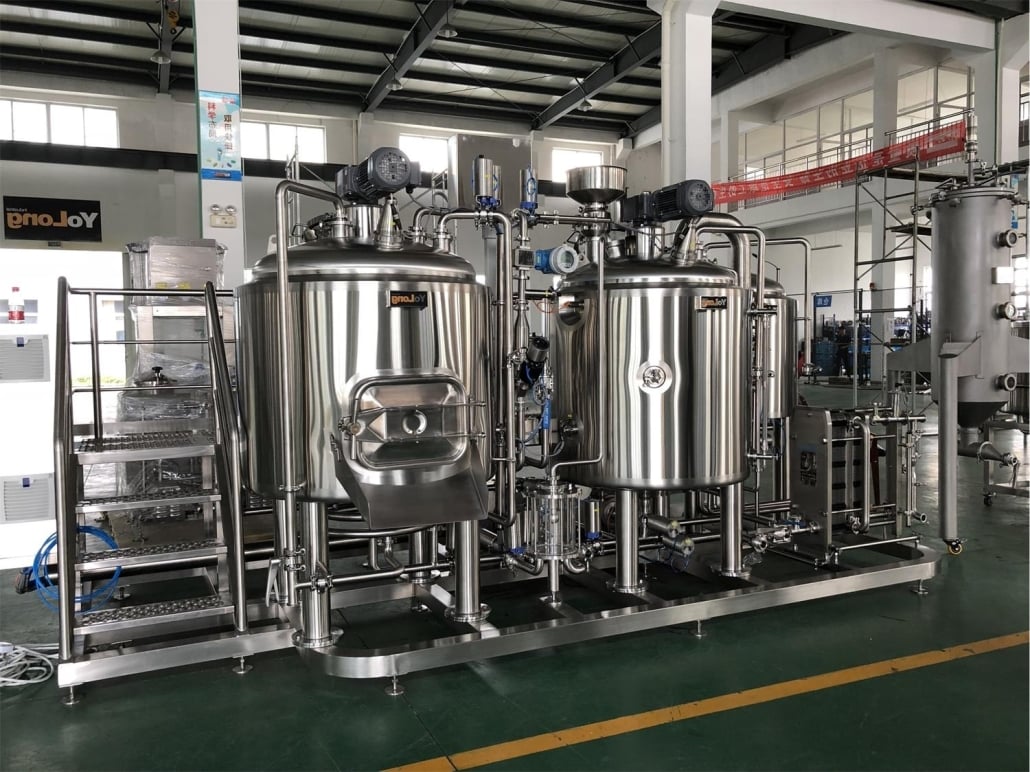
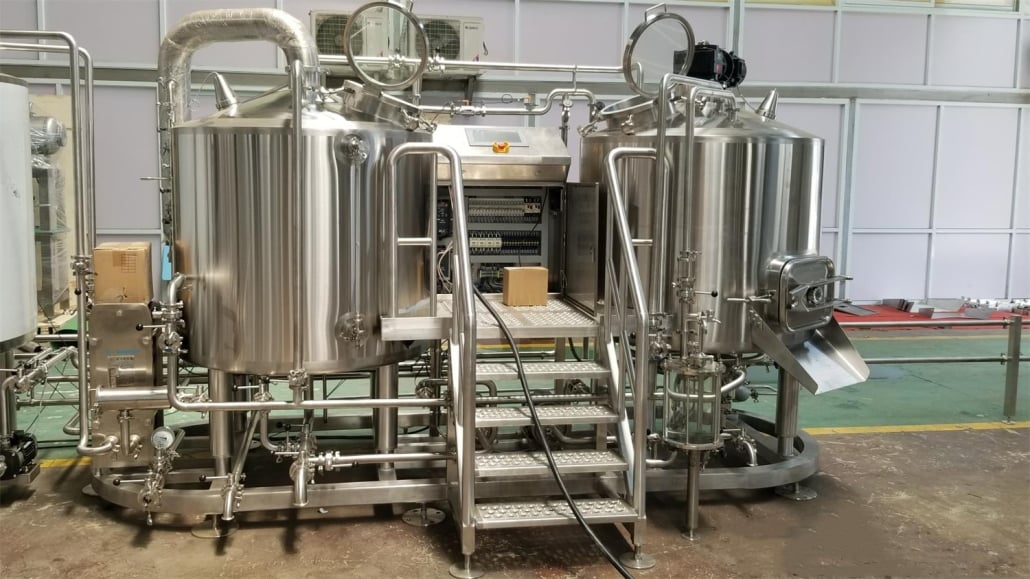
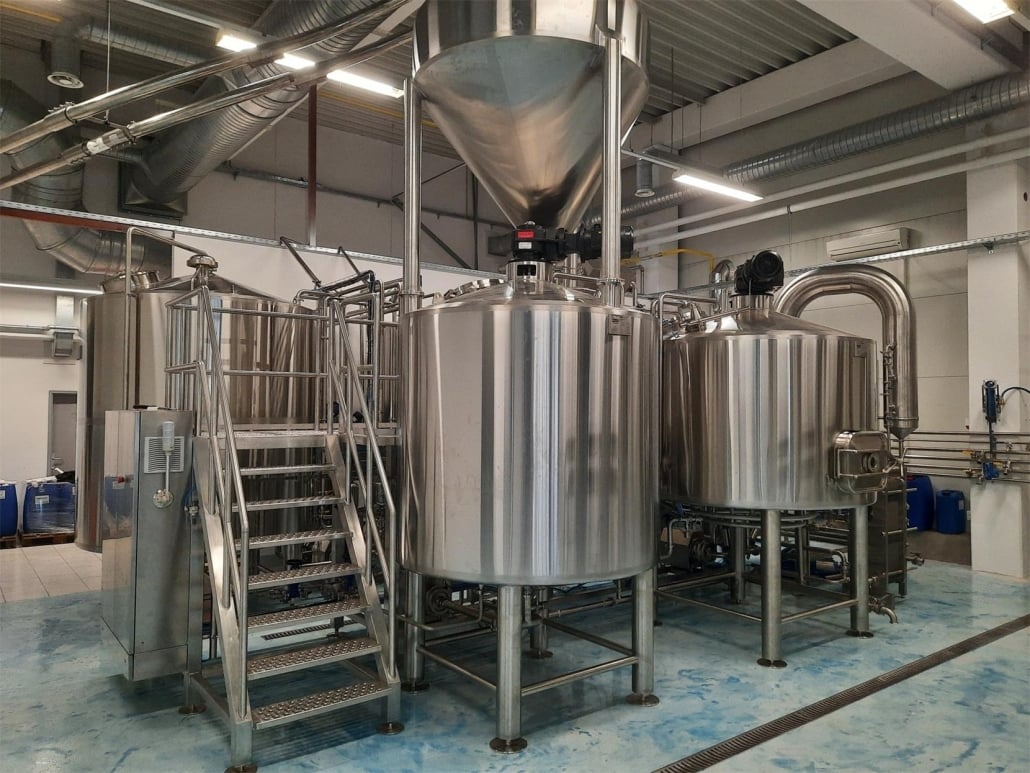
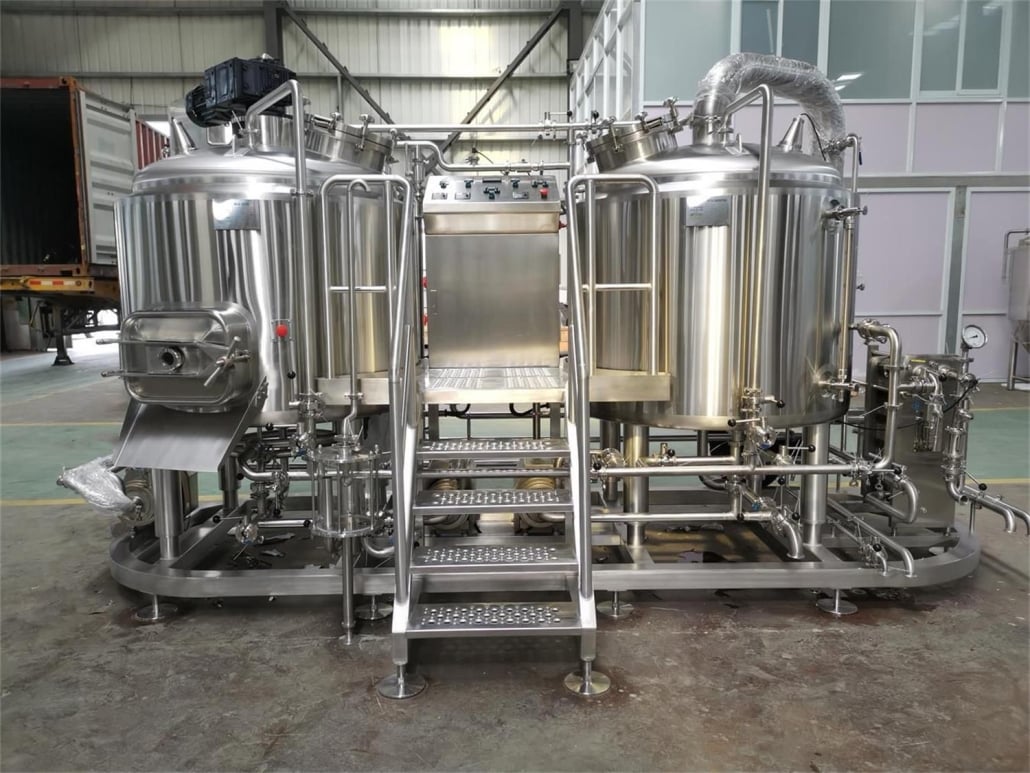
Installation, Operation, and Maintenance
Aspect | Details |
Installation | Requires professional setup, including plumbing, electrical work, and calibration of controls. |
Operation | Intuitive interfaces and training for staff can streamline day-to-day brewing operations. |
Maintenance | Regular cleaning, inspection of seals, and calibration of sensors ensure optimal performance. |
How to Choose the Right Supplier
Factor | Details |
Reputation | Look for suppliers with positive reviews and strong industry presence. |
Customization | Ensure the supplier offers equipment tailored to your brewery’s specific needs. |
After-Sales Support | Check for warranty coverage and availability of technical support. |
Budget | Compare costs across suppliers while factoring in quality and long-term value. |
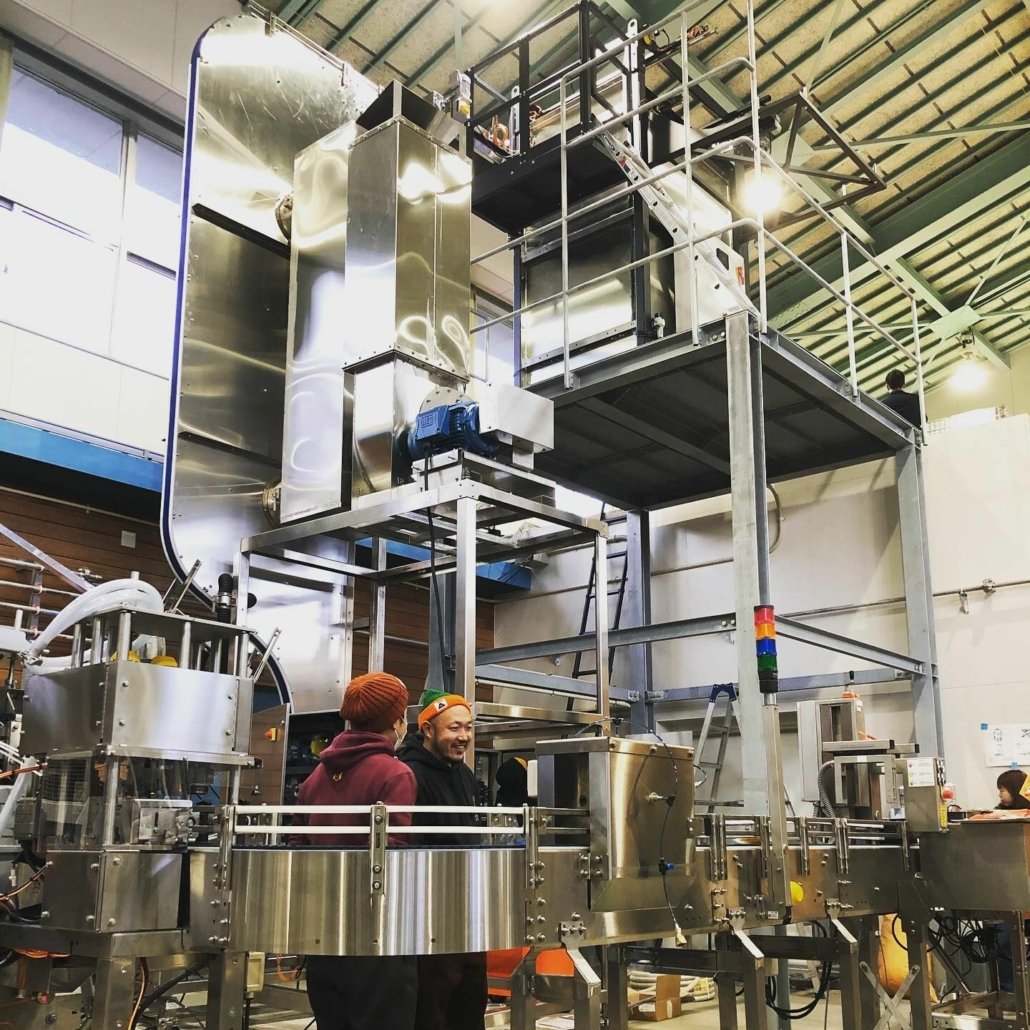
Advantages and Limitations of 10 BBL Brewing Equipment
Aspect | Advantages | Limitations |
Capacity | Perfect balance between small-scale and large-scale | May not suffice for large-scale production |
Flexibility | Great for experimenting with multiple beer styles | Larger setups require more complex infrastructure |
Cost | More affordable than larger systems | Higher initial investment compared to smaller setups |
Ease of Use | Professional-grade automation options | Requires trained staff for operation |
FAQs
Question | Answer |
What is a BBL in brewing? | BBL stands for “barrel,” which is 31 gallons in the U.S. brewing industry. |
How much space do I need for a 10 BBL setup? | Typically 500-700 sq. ft., depending on layout and additional equipment. |
How long does it take to brew with this system? | A complete cycle, from mashing to packaging, takes around 2-3 weeks depending on the beer style. |
What is the cost of a 10 BBL system? | Prices range from $50,000 to $100,000 depending on features and customization. |
Can I expand my system later? | Yes, most systems are designed for scalability with additional tanks and automation options. |
Frequently Asked Questions (FAQ)
1) What utilities are required to run 10 BBL Brewing Equipment reliably?
- Plan for 3‑phase power (typically 208–480V; 100–300 A depending on heat source), 40–70 gpm cold water for knockout via HX, 1–2 refrigeration tons per 10–15 bbl cellar, food-grade CO2, compressed air (80–120 psi, dry/oil-free), and sloped floors with trench drains.
2) Steam vs. electric vs. direct fire for a 10 bbl brewhouse—what’s best?
- Steam offers the best control and efficiency for frequent turns; electric is clean and easier to permit but needs ample service; direct fire has lower capex but lower efficiency and more venting requirements. Choose based on utility availability and long-term OPEX.
3) How many fermenters should pair with a 10 bbl brewhouse?
- A common starting mix is 4–6 unitanks (2–3x brewhouse volume each), plus 1–2 bright tanks. Aim for 4–6x brewhouse volume in total FV capacity to avoid brewhouse idling.
4) What automation delivers the best ROI at this scale?
- PLC/HMI recipe control, VFDs on pumps/augers, mash/lauter temperature PIDs, auto knockout setpoint control, inline volume/flow meters, and basic data logging. Expect reduced variability, faster training, and fewer rebrews.
5) How do I control oxygen pickup on a 10 bbl system?
- Use closed transfers, DAW (deaerated water) for rinses and dilution, CO2 purge manifolds for hoses/valves, keep brite-to-filler runs ≤10 m, and measure DO at knockout and filler inlet.
2025 Industry Trends for 10 BBL Brewing Equipment
- Short-path packaging: colocating brite tanks and canning lines to keep hoses ≤10 m, reducing DO and foam loss.
- Energy recovery by default: wort→HLT heat recovery loops and stack condensers cutting thermal use 15–30%.
- Multiproduct readiness: 10 bbl systems plumbed for seltzer and low/NA beer (dealcoholization partners), with allergen-segregated adjunct rooms.
- Smarter cellars: integrated sensors (temp, pressure, level, DO) feeding cloud dashboards for predictive maintenance.
- Sustainability incentives: utilities offering rebates for VFDs, heat recovery, high-efficiency chillers, and CO2 capture pilots.
Performance & Cost Benchmarks (10 BBL, 2024–2025)
Metric | Typical Range | 2025 Best Practice Target | Notes / Sources |
---|---|---|---|
Water-to-beer ratio (plant) | 3.8–6.0:1 | 3.0–3.8:1 | Brewers Association sustainability |
Brewhouse thermal efficiency | 70–82% | ≥85% w/ heat recovery | Vendor/BA benchmarks |
Knockout DO (ppb) | 10–40 | ≤10 (lagers), ≤20 (ales) | ASBC Methods |
Packaged DO (ppb) | 30–80 | ≤30 (draft ≤20) | ASBC Methods |
Electric energy (kWh/bbl) | 10–20 | 8–12 | DOE, vendor data |
Chiller load reduction (HR loop) | — | 15–30% | Case studies |
Typical capex (brewhouse+cellar) | $50k–$100k | $70k–$120k w/ automation | Supplier quotes vary |
Authoritative sources:
- Brewers Association: https://www.brewersassociation.org/
- ASBC Methods of Analysis: https://www.asbcnet.org/
- U.S. DOE Better Plants (efficiency/rebates): https://www.energy.gov/
Latest Research Cases
Case Study 1: Heat Recovery + Short-Path Packaging on a 10 bbl Brewpub (2025)
Background: Utility costs and high packaged DO (50–70 ppb) limited shelf life.
Solution: Added wort→HLT heat recovery, relocated canning line adjacent to brite cellar (hose run 22 m → 8 m), installed inline DO at filler inlet, and standardized CO2 purges.
Results: Thermal energy use down 21%; packaged DO median 24 ppb; canning waste down 14%; payback estimated at 18–24 months.
Case Study 2: Cellar Right-Sizing to Boost Turns (2024)
Background: 10 bbl system with three 10 bbl FVs caused brewhouse idle time and stockouts.
Solution: Added two 20 bbl unitanks and one 10 bbl brite; implemented simple PLC recipe control and VFDs.
Results: Cellar turns increased from 1.8 to 2.7 per month; labor hours/bbl dropped 12%; annual production up 35% without adding brew days.
Expert Opinions
- John Mallett, Brewing Operations Expert; author of “Malt”
“Design the 10 bbl brewery around utilities and flow. Short, closed paths and heat recovery outperform most shiny upgrades on quality and cost.” - Dr. Tom Shellhammer, Professor of Fermentation Science, Oregon State University
“Measuring DO at knockout and at the filler creates the feedback loop small breweries need to stabilize flavor and extend shelf life.” - Sarah Flora, Brewer and operations consultant
“Right-sized automation—PIDs, VFDs, recipe steps, and data logging—pays back quickly on a 10 bbl system by cutting rework and training time.”
Practical Tools/Resources
- Brewers Association benchmarking and sustainability tools: https://www.brewersassociation.org/
- ASBC Methods (DO/CO2, sensory, micro): https://www.asbcnet.org/
- DOE calculators and incentives (motors/VFDs, heat recovery): https://www.energy.gov/
- Brewer’s Friend calculators (brewhouse efficiency, strike/infusion, carbonation): https://www.brewersfriend.com/
- Vendor application notes (GEA, Pentair, Alfa Laval) on CIP, heat recovery, hygienic piping, and low-oxygen transfers
Last updated: 2025-08-29
Changelog: Added targeted FAQs, 2025 trends with benchmark table, two 10 bbl-focused case studies, expert viewpoints, and practical resources tailored to 10 BBL Brewing Equipment.
Next review date & triggers: 2026-02-28 or earlier if BA/ASBC publish new DO/efficiency benchmarks, utility incentive programs change, or packaged DO exceeds 30 ppb for two consecutive audits.
Share this entry
Interested in learning more about Brewing Systems including additional details and pricing information? Please use the form below to contact us!
YOLONG BREWERY EQUIPMENT FAQS
- Commercial Brewery / Craft Brewery / Microbrewery / Nanobrewery
- What is The Difference Between Craft Beer and Industrial Beer?
- The Bespoke Differences In Custom Brewing Systems
- Everything You Need to Know About Kettle Souring
- How to Choose Brewing Equipment for Your business?
- How To Choose The-Best Partner To Build Your Commercial Microbrewing System?
- Two Detection Sensors That You Need To Use In Your Brewhouse System
- Remote Control Applications in Brewing Equipment/How does it work?
- How To Clean Your Brand New Brewery Tanks?