How to Automate a Microbrewery
As we all know, brewing is a very interesting thing, but it is also a tedious labor process. Because of the limited manpower and a large number of parameters and ranges that need to be controlled, large breweries have chosen an automated design model.
Need to introduce automation technology for microbrewery? The answer is yes. Because of the reasonable introduction of automation, while ensuring the brewing pleasure of the brewer, it will liberate the brewers a lot of time and energy to learn and promote, is it better to study new tastes?
According to statistics, the equipment capacity of micro-brewery that has not been fully introduced into automation is generally 3HL-15HL, accounting for 83% of the total. Many owners think that automation will be a big investment.
In fact, the automation of micro-brewery is very different from that of large-scale breweries. It does not require a lot of investment, because only the necessary automated processes are designed automatically, not all. For example, the pump is automatically controlled to transfer the wort so that the brewer acts as a process control leader rather than a process executor. For the automation of brewhouse, it depends on PLC (Programmable Logic Controller) and HMI (Human Machine Interface).
Focusing on the design and optimization of micro-brewery for 15 years, YoLong has communicated with thousands of brewers around the world, learning from each other, summarizing and designing control modes and methods suitable for micro-brewers, as follows. The models we generally choose are-
Model One
SIEMENS—PLC (SIMATIC S7-1200 or ET200SP ) + touch screen model (select Simatic Basic Panel or Simatic Comfort Panel based on customer requirements)
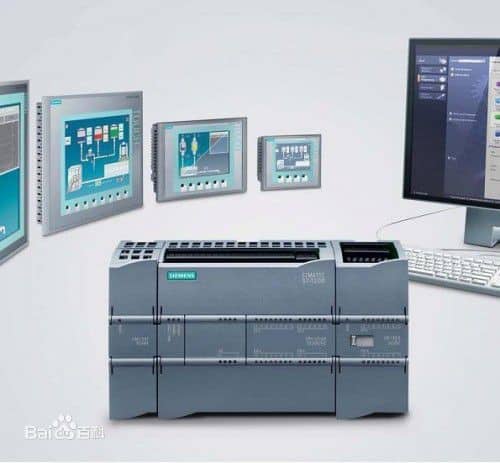
SIMATIC S7-1200
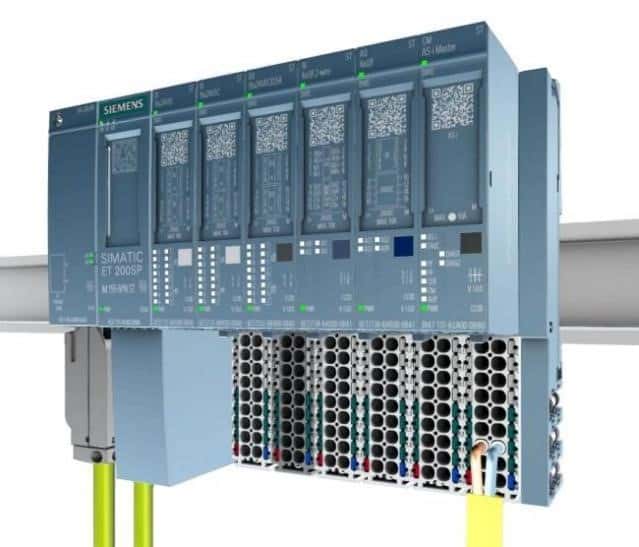
ET200SP
Model Two
ALLEN-BRADLEY —–PLC (ControlLogix Series) + touch screen, configure series and matching HMI based on control points and customer post-expansion requirements.
There are eight parts in the automation control.
1. Automatic control of water mixing station
The automatic control of the water mixing station is used to control the cold water and hot water mixing before mashing.
Timing, quantitative, and constant temperature control can be realized.
For example, we want to inject 550L of 65℃water into the mashing tun at 9:35 am on June 20, it can be realized by this control system.
The principle is to install the Burkert PID regulating valve on the hot water pipe, install the temperature sensor and E+H flow meter on the water mixing chamber outlet pipe. its actuator is a pneumatic butterfly valve.
The process flow chart of the automatic control of the water mixing station is shown on the right and the working principle shown in the picture below.
2. Automatic temperature control
Temperature automatic control is relatively easy to implement, the temperature is detected by the IFM temperature sensor, and the temperature signal is converted to 4~20mA analog signal sent to the PLC. When the PLC analyzes and reaches the set temperature, the switching signal of I/O is given to the relay of the actuator to control the switching of the actuator (valve or heating tube).
There are two kinds of temperature sensors commonly used at present,
- One is with the transmitter, the role of the transmitter is to regulate the resistance change into current or voltage signal output to PLC, commonly used The signal is 0-10V, 0-20mA, 4-20mA)
- The other is without transmitter, and the resistance value of the sensor with temperature Change and change, PLC collects resistance value, after conversion, correspondingly displays different temperature values
2.1 Temperature control in the brewhouse
Most brewers want to achieve segmented leaching brewing, but for small equipment, mashing and lauter are mostly integrated, and electric heating tubes cannot be installed due to the presence of rake knife. Therefore, if segmental brewing is achieved, steam heating is the most common method.
Our usual selection is temperature sensor combined with steam solenoid valve to achieve the purposes of control.
After the temperature sensor feeds back the signal to the PLC, then the PLC controls the opening and closing of the steam solenoid valve, directly realizes the control of the heating, thereby indirectly automatically controlling the temperature parameter.
The temperature sensor and steam solenoid valve are usually selected as follows:
Temperature sensor
- IFM_ TD2841 (with transmitter, output 4-20mA signal)
- IFM_TM4361 (without transmitter)
Steam solenoid valve
- Burkert_0355
For more information about Burkert, please click the link below
https://www.burkert.com.cn/cn/products/dian-ci-fa
The temperature control of boiling is relatively simple, and the boiling time can be set. Here we have configured anti-overflow protection for unsupervised (detailed in the sixth-security location).
The picture below shows the parameter display status of the brewing process control panel.
2.2Temperature control in the fermentation
Segmented fermentation can accommodate more types of beer. The brewer can set the length of each fermentation period and the corresponding temperature according to his own ideas.
The automatic control system can realize the precise control of the temperature of each stage. The principle of control is similar to brewing stage, and the temperature sensor is used to feedback the signal to the PLC, then the PLC will control the opening and closing of the ice water solenoid valve, so it can achieve the control of the temperature inside the fermenters.
After sealed fermenters, there is no need for the brewer to monitor the site because the temperature control is all done by the control system. At the same time, brewers have more time to study brewing processes and formulations.
The temperature sensor and ice water solenoid valve are usually selected as follows:
Temperature sensor:
- IFM-8004
Ice water solenoid valve:
- Burkert-5281
For more information about Burkert, please click the link below
https://www.burkert.com.cn/cn/products/dian-ci-fa
The picture below shows the parameter display status of the segmented fermentation process control panel.
3. Material transfer
For microbrewery, the transfer of fluids allows one-button transfer without the need to manually open the valve, which also avoids the loss of beer caused by manually open operation errors.
This part is mainly controlled by the PLC that is compiled with the program to directly control the actuator to achieve the control action(starting butterfly valve)
For pneumatic butterfly valves, we generally choose the model:
- LYSF–IDQX-7
- Alfa-Laval-LKB ISO CL
The picture of the touch screen display panel is shown below-
The start butterfly valve can also be an emergency manual switch, and the touch screen has a second prompt to open the valve and a manual indication after manually opening the valve. The operation prompt is as shown below.
4. Level Control
The liquid level sensor is installed on the corresponding tank body to communicate with the PLC to realize liquid level self-control. The general device is on a hot water tank. (The amount of water in the mashing tun can be automatically controlled by the flow meter of the water mixing station.)
The functions that can be achieved are:
- The liquid level is displayed (displayed on the HMI panel or mobile phone)
- Liquid level automatic control: automatic water supply to the required volume of liquids to set the upper and lower water levels.
- Anti-overflow (When the liquid level reaches the specified position, the actuator will be automatically controlled to close the inlet to prevent overflow.)
- Anti-low level (prevent the pump from idling to protect the pump)
Liquid level sensor, radar type and pressure type. It is not recommended to use radar type liquid level sensor. It has great requirements on liquid state. After testing, generally, IFM pressure sensor is selected.
For the liquid level sensor, we generally choose the model:
The liquid level is displayed(in the tank)
- 2270-P-1N-4 (+GF+)
Anti-overflow
- LMT 105
Anti-low level
- LMT 121
5. Time control
Another advantage of PLC is the precise control of time, which can be easily achieved by performing an operation at a certain time. For example, before brewing, store the water in the hot water tank at a set temperature and control the process of the staged fermentation.
6. Security protection
When we designing equipment and procedures, consideration should be given to the safety of the brewer, the safety of the equipment and the quality control of the beer.
What we often do is:
- The idling protection of the pump, realized by installing IFM flow monitor SI6800 through the pump inlet pipe.
- Boiled tun anti-overflow, realized by electronic liquid level sensor LMT121.
- Emergency stop, in the event of an emergency, or when the brewer thinks that it must stop as quickly as possible, a quick one-click stop is achieved through a very eye-catching button.
7. Monitoring
With the site manager installed on your phone, we can achieve no need for on-site monitoring during the fermentation process, but we can use the mobile phone to remotely monitor and understand the progress of fermentation in real-time.
In this case, the brewer’s time is greatly liberated. When you are out, you can open your mobile phone and check the real-time situation of your fermenters.
8. Historical data query
we can query past history for data saving and analysis.
Brewers can analyze previously brewed data, which is very helpful in improving brewing levels and beer flavor development.