Pilot Brewing System:11 Essential Components and Benefits
Introduction
In the world of brewing, innovation and experimentation are key drivers of success. Craft breweries, in particular, strive to create unique and flavorful beers that captivate the taste buds of their customers. One tool that has become indispensable for achieving this goal is a pilot brewing system. In this article, we will explore what a pilot brewing system is, its components, benefits, working principles, selection criteria, examples, and future trends. So, let’s dive in!
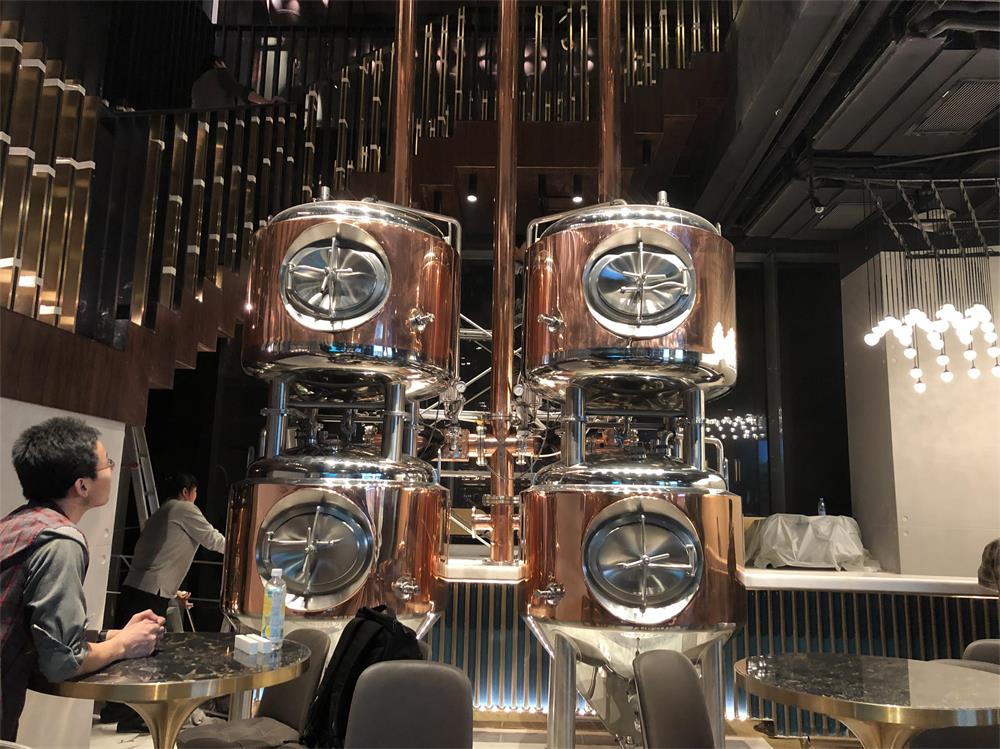
What is a Pilot Brewing System?
A pilot brewing system is a small-scale brewing setup designed to test and develop new beer recipes. It serves as a playground for brewers to experiment with different ingredients, techniques, and flavor combinations before scaling up production. By using a pilot brewing system, breweries can refine their recipes, ensure consistency, and gather feedback from consumers without committing to large-scale production.
Components of a Pilot Brewing System
A pilot brewing system consists of several key components that work together to facilitate the brewing process. Let’s take a closer look at each of them:
Brew Kettle
The brew kettle is where the brewing process begins. It is a large vessel used for boiling the wort, a mixture of water and malt extract. The brew kettle is equipped with heating elements, temperature controls, and whirlpooling mechanisms to ensure precise and efficient boiling.
Mash Tun
The mash tun is where the mashing process takes place. It is responsible for converting the starches in the malt into fermentable sugars. The mash tun contains a false bottom or a filter system to separate the liquid wort from the spent grain.
Fermenter
The fermenter is a vessel where yeast is added to the wort to initiate fermentation. It provides an environment for the yeast to convert sugars into alcohol and produce flavors and aromas. The fermenter should be equipped with temperature control systems and a means to collect the carbon dioxide produced during fermentation.
Wort Chiller
The wort chiller is used to rapidly cool down the boiled wort to a temperature suitable for yeast fermentation. It can be a heat exchanger or an immersion coil that circulates cold water around the wort.
Control System
A pilot brewing system requires a control system to monitor and regulate various parameters such as temperature, pressure, and timing. This system ensures consistency and repeatability in the brewing process.
Accessories
Additional accessories may include pumps for liquid transfer, valves for flow control, gauges for pressure monitoring, and cleaning systems for maintaining hygiene.
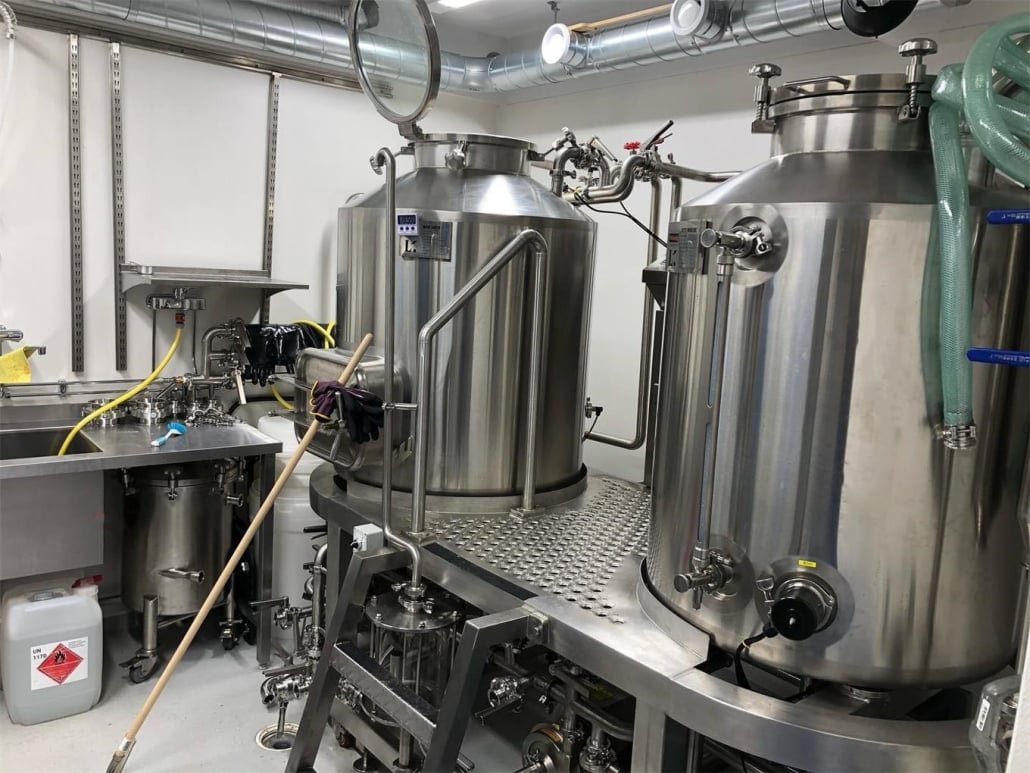
Benefits of a Pilot Brewing System
Using a pilot brewing system offers several advantages for breweries. Let’s explore the key benefits:
Experimentation and Recipe Development
A pilot brewing system provides a platform for brewers to unleash their creativity and experiment with new recipes. They can test different combinations of ingredients, hop varieties, yeast strains, and brewing techniques to achieve unique flavors and profiles.
Quality Control and Consistency
With a pilot brewing system, breweries can meticulously control every aspect of the brewing process, ensuring consistent results. They can fine-tune parameters such as mash temperatures, hop additions, and fermentation conditions to produce high-quality and reproducible beers.
Cost-Effectiveness
Before investing in large-scale production, breweries can use a pilot brewing system to validate their recipes and concepts. This helps minimize the risk of producing a batch that might not resonate with consumers, ultimately saving costs on ingredients, packaging, and marketing.
Training and Education
Pilot brewing systems serve as valuable training tools for brewers, allowing them to develop their skills and knowledge. It provides a hands-on learning experience, enabling brewers to understand the intricacies of the brewing process and experiment with different brewing techniques.
How Does a Pilot Brewing System Work?
Now that we understand the components and benefits of a pilot brewing system, let’s delve into how it works:
Recipe Creation and Ingredients
Brewers start by formulating a recipe based on their desired beer style and flavor profile. They carefully select malt varieties, hops, yeast strains, and adjuncts to achieve their intended taste. The recipe serves as a blueprint for the brewing process.
Mashing and Boiling
The brewing process begins with mashing, where the malt is mixed with hot water to extract sugars. The mash tun maintains specific temperature ranges to activate enzymes that break down the starches. After mashing, the liquid, known as wort, is transferred to the brew kettle for boiling. During boiling, hops are added for bitterness, flavor, and aroma.
Fermentation and Conditioning
Once the wort is cooled down, it is transferred to a fermenter, and yeast is added. Fermentation occurs as yeast consumes sugars, producing alcohol, carbon dioxide, and various flavor compounds. After primary fermentation, the beer undergoes conditioning, where it matures and clarifies.
Packaging
Once the beer has reached the desired flavor and clarity, it can be packaged in bottles, cans, or kegs for distribution and consumption.
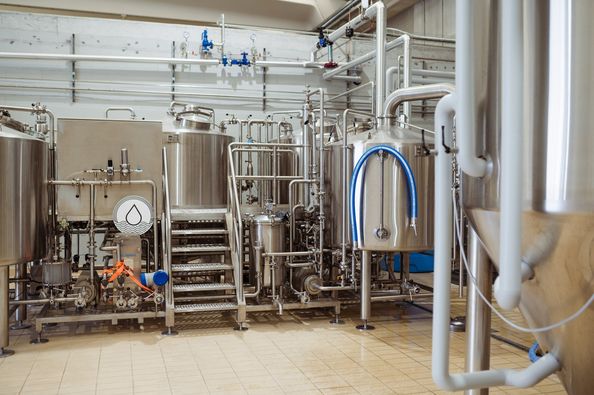
Choosing the Right Pilot Brewing System
When selecting a pilot brewing system, brewers should consider the following factors:
Batch Size and Production Capacity
The desired batch size and production capacity determine the scale of the pilot brewing system. It should align with the intended purpose, whether it’s for small-scale experimentation or larger-scale recipe development.
Automation and Control Features
Automation and control features enhance the brewing process by providing precise control over parameters. Brewers should consider
Automation and Control Features (continued)
the level of automation they require, such as temperature and pressure control, programmable recipes, and data logging capabilities. Advanced control systems can streamline operations and improve efficiency.
Flexibility and Upgradability
Breweries should assess the flexibility and upgradability of the pilot brewing system. It should allow for future expansions or modifications as the brewery grows. Flexibility in terms of recipe customization and equipment compatibility is also essential.
Budget and Cost Considerations
Budget constraints play a significant role in selecting a pilot brewing system. Breweries should evaluate the cost of the system, including equipment, installation, and ongoing maintenance. It’s important to find a balance between affordability and the desired features.
Examples of Pilot Brewing Systems
Pilot brewing systems come in various sizes and configurations. Here are three examples that cater to different production scales:
Small-Scale Pilot Brewing Systems
Small-scale pilot brewing systems are ideal for nano-breweries or brewpubs. They typically have a batch size ranging from 20 to 100 liters (5 to 25 gallons). These systems are compact, easy to operate, and cost-effective. They provide a platform for small-scale experimentation and recipe development.
Medium-Scale Pilot Brewing Systems
Medium-scale pilot brewing systems are suitable for small to medium-sized craft breweries. They have a batch size ranging from 500 to 1,000 liters (130 to 260 gallons). These systems offer more automation and control features compared to small-scale systems. They are designed for breweries looking to scale up production and test recipes for larger batches.
Large-Scale Pilot Brewing Systems
Large-scale pilot brewing systems are designed for commercial breweries with significant production capacity. They have batch sizes exceeding 1,000 liters (260 gallons). These systems often mimic the functionality of full-scale brewing systems, allowing breweries to conduct extensive recipe development, quality control, and market testing.
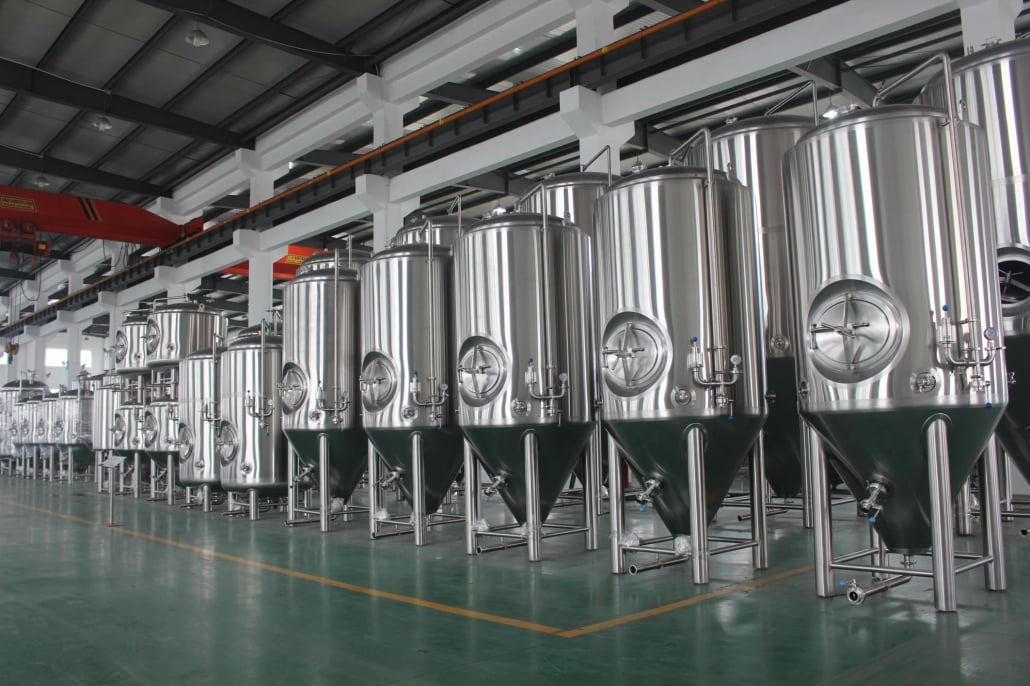
Case Study: Benefits of a Pilot Brewing System for Craft Breweries
To understand the practical benefits of a pilot brewing system, let’s consider a case study of a craft brewery. XYZ Craft Brewery implemented a pilot brewing system as part of their expansion plans. The system allowed them to create small test batches of experimental beers and receive direct feedback from their taproom customers.
Using the pilot brewing system, XYZ Craft Brewery could fine-tune their recipes, make adjustments based on customer preferences, and gauge market demand for new flavors. This helped them avoid the risk of producing large batches of beer that might not resonate with consumers. Additionally, the pilot brewing system served as a valuable training tool for their brewing team, allowing them to experiment and refine their brewing techniques.
The feedback and data collected from the pilot brewing system guided XYZ Craft Brewery’s decision-making process for scaling up production and launching new beers. As a result, they experienced increased customer satisfaction, improved product quality, and higher sales.
Future Trends in Pilot Brewing Systems
The world of pilot brewing systems continues to evolve with emerging trends and technologies. Here are some future trends to watch out for:
Integration of IoT and Automation
Pilot brewing systems are increasingly incorporating Internet of Things (IoT) technologies to enhance automation and data-driven decision-making. IoT-enabled sensors and devices can monitor and control various parameters remotely, allowing brewers to optimize processes and collect valuable data for analysis.
Sustainable Brewing Practices
As sustainability becomes a global priority, pilot brewing systems are adapting to incorporate eco-friendly practices. This includes energy-efficient heating and cooling systems, water conservation measures, and the use of renewable energy sources. Breweries are also exploring innovative ways to repurpose brewing by-products and minimize waste.
Advancements in Control Systems
Advancements in control systems are making pilot brewing systems more user-friendly and efficient. Smart control panels, intuitive interfaces, and integrated software solutions are simplifying the brewing process, reducing human error, and enabling real-time monitoring and adjustment of brewing parameters.
Collaborative Brewing Platforms
Collaborative brewing platforms are gaining popularity in the craft beer industry. These platforms allow brewers from different breweries to come together and share resources, equipment, and knowledge. Pilot brewing systems can facilitate these collaborations, fostering innovation and creativity in the brewing community.
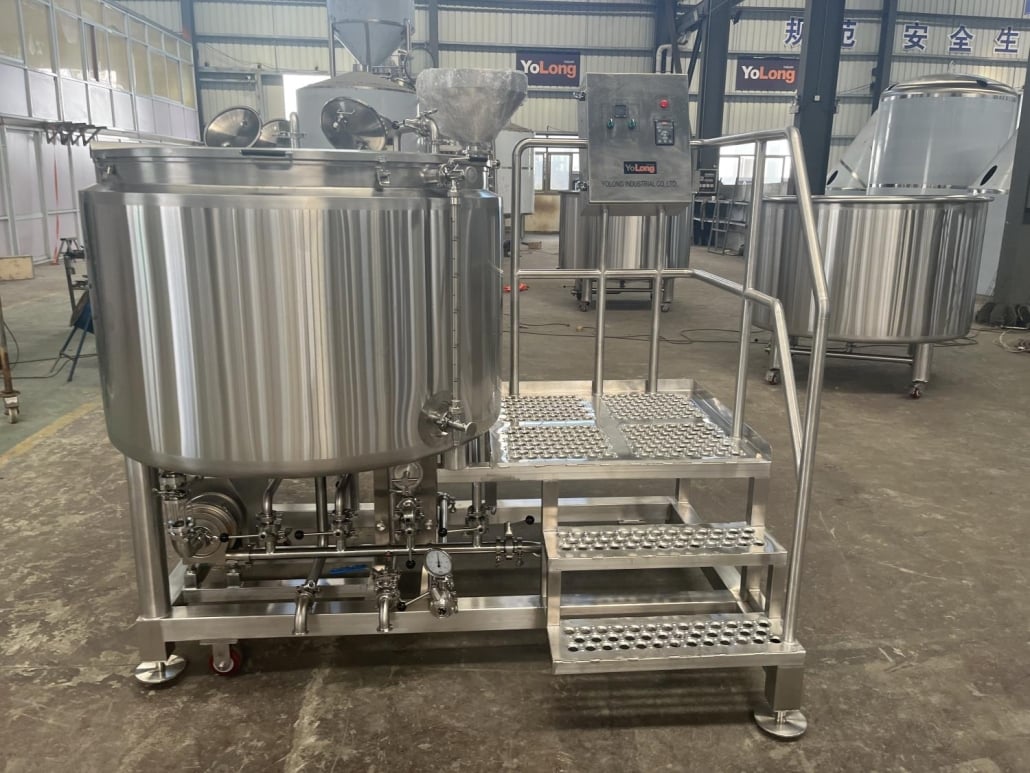
Conclusion
Pilot brewing systems have revolutionized the craft beer industry, enabling breweries to experiment, refine recipes, and deliver unique and high-quality beers to consumers. With their flexibility, control, and cost-effectiveness, pilot brewing systems have become indispensable tools for breweries of all sizes. By investing in the right pilot brewing system and harnessing its benefits, breweries can drive innovation, improve product quality, and ultimately thrive in the competitive brewing landscape.
FAQs
Q1: Can a pilot brewing system be used for large-scale production?
A1: No, pilot brewing systems are designed for small-scale experimentation and recipe development. They are not intended for large-scale production. Breweries typically use pilot brewing systems to test and refine their recipes before scaling up.
Q2: How much does a pilot brewing system cost?
A2: The cost of a pilot brewing system can vary depending on the size, features, and manufacturer. Small-scale systems can range from $5,000 to $15,000, while medium and large-scale systems can cost anywhere from $30,000 to over $100,000.
Q3: Can a pilot brewing system help improve the consistency of beer production?
A3: Yes, one of the key benefits of a pilot brewing system is its ability to ensure consistency in beer production. Brewers can fine-tune parameters, experiment with different variables, and replicate successful recipes, resulting in consistent and reproducible beer batches.
Q4: Can a pilot brewing system be used by homebrewers?
A4: While pilot brewing systems are primarily used by commercial breweries, some homebrewers with a passion for experimentation and recipe development may invest in small-scale pilot systems. These systems allow homebrewers to replicate the professional brewing process on a smaller scale.
Q5: Are pilot brewing systems suitable for all beer styles?
A5: Yes, pilot brewing systems can be used to develop recipes for a wide range of beer styles. Whether it’s traditional styles, experimental brews, or seasonal specialties, a pilot brewing system provides brewers the flexibility to create and refine recipes according to their desired beer styles.
Share this entry
Interested in learning more about Brewing Systems including additional details and pricing information? Please use the form below to contact us!
YOLONG BREWERY EQUIPMENT FAQS
- Commercial Brewery / Craft Brewery / Microbrewery / Nanobrewery
- What is The Difference Between Craft Beer and Industrial Beer?
- The Bespoke Differences In Custom Brewing Systems
- Everything You Need to Know About Kettle Souring
- How to Choose Brewing Equipment for Your business?
- How To Choose The-Best Partner To Build Your Commercial Microbrewing System?
- Two Detection Sensors That You Need To Use In Your Brewhouse System
- Remote Control Applications in Brewing Equipment/How does it work?
- How To Clean Your Brand New Brewery Tanks?