Table of Contents
ToggleIntroduction
Craft beer enthusiasts and professional brewers are constantly seeking efficient and reliable brewing systems to create outstanding brews. One such system that has gained popularity in the industry is the 5 barrel brewing system. In this article, we will explore the features, benefits, components, brewing process, considerations for choosing, and maintenance of a 5 barrel brewing system. So, grab a pint and let’s dive in!
What is a 5 Barrel Brewing System?
A 5 barrel brewing system refers to a set of equipment used in the beer production process, specifically designed to produce 5 barrels of beer in a single batch. One barrel of beer is equivalent to 31 gallons or 117 liters. This system includes various components and vessels necessary for mashing, boiling, fermenting, conditioning, and packaging beer.

Benefits of a 5 Barrel Brewing System
Increased Production Capacity
The primary advantage of a 5 barrel brewing system is its increased production capacity compared to smaller homebrewing systems. With a 5 barrel system, breweries can brew larger quantities of beer, catering to the growing demand of their customers or expanding into new markets.
Flexibility in Brewing Operations
A 5 barrel brewing system provides brewers with the flexibility to experiment with different recipes and brew styles. The larger capacity allows for more creativity, enabling brewers to produce a diverse range of beers to satisfy the evolving tastes of consumers.
Consistent Quality Control
Maintaining consistent quality is crucial for any brewery’s success. A 5 barrel brewing system offers precise temperature and pressure controls, allowing brewers to replicate recipes with accuracy. This consistency ensures that every batch of beer meets the high-quality standards expected by customers.
Cost Efficiency
While larger than homebrewing systems, a 5 barrel brewing system is still relatively compact and more cost-effective than larger commercial systems. This makes it an ideal choice for small to medium-sized breweries looking to scale up their production without breaking the bank.
Scalability
As breweries grow and demand increases, a 5 barrel brewing system offers scalability. Brewers can expand their operation by adding more 5 barrel units, allowing them to meet rising demands while maintaining the same brewing process and recipe consistency.
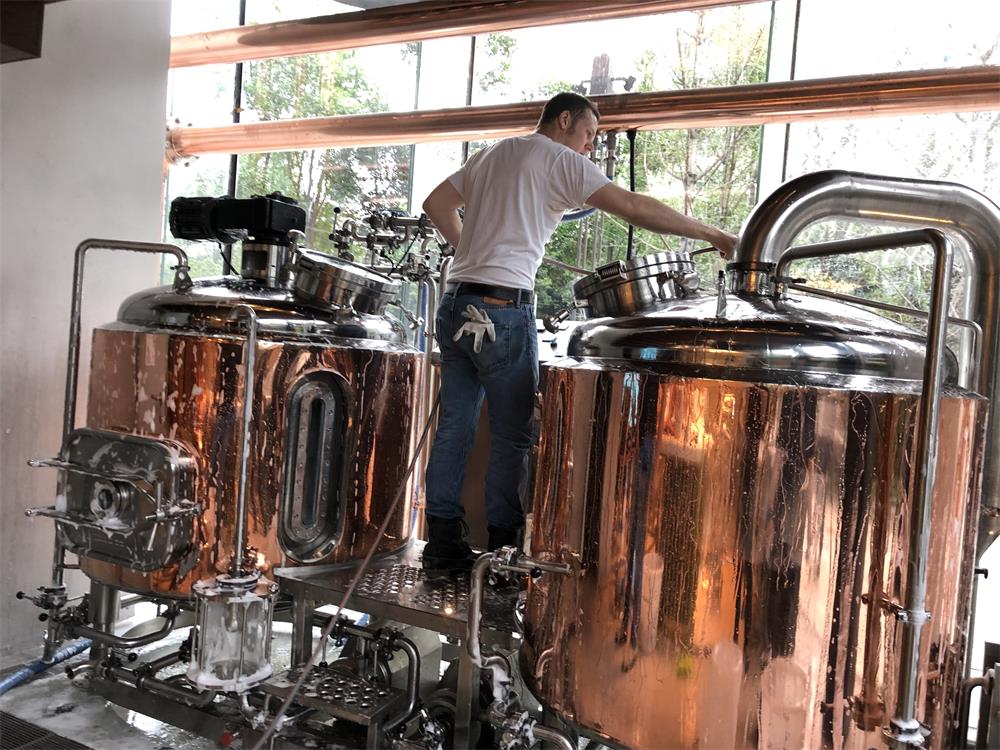
Components of a 5 Barrel Brewing System
To better understand how a 5 barrel brewing system operates, let’s explore its key components:
Mash Tun
The mash tun is where the mashing process takes place. It is a vessel equipped with temperature controls that enable the conversion of starches into fermentable sugars. This vessel typically includes a false bottom or a manifold to separate the liquid wort from the grain.
Brew Kettle
The brew kettle is where the wort is boiled, hops are added, and flavors are developed. This vessel usually features a heating element, temperature controls, and a whirlpool arm to create a uniform mixture. The boil time and hop additions greatly influence the beer’s bitterness, aroma, and flavor profile.
Fermentation Vessels
After boiling, the wort is transferred to fermentation vessels, often cylindrical conical tanks (CCTs). These vessels provide a controlled environment for yeast to ferment the sugars into alcohol and carbon dioxide. CCTs offer precise temperature control, pressure relief valves, and sampling ports for monitoring the fermentation process.
Cooling System
Maintaining proper fermentation temperatures is crucial for yeast health and flavor development. A 5 barrel brewing system incorporates a cooling system that uses glycol or chilled water to regulate the temperature in the fermentation vessels. This ensures consistent and controlled fermentation throughout the brewing process.
Control Panel
The control panel is the central command center of the brewing system. It allows brewers to monitor and adjust various parameters such as temperature, pressure, and timing. The control panel ensures precise control over the brewing process, guaranteeing consistent results with each batch.
Brewing Process with a 5 Barrel Brewing System
A 5 barrel brewing system follows a standardized brewing process, including the following steps:
Mashing
The mashing process begins by mixing milled grains with hot water in the mash tun. The enzymes present in the grains convert starches into fermentable sugars. The mash is held at specific temperatures for various durations to achieve desired sugar extraction.
Boiling
Once the mash is complete, the wort is transferred to the brew kettle for boiling. During this phase, hops are added at specific times to impart bitterness, flavor, and aroma to the beer. Boiling also sterilizes the wort, removes unwanted compounds, and stabilizes the beer.
Fermentation
After boiling, the wort is rapidly cooled and transferred to the fermentation vessels. Yeast is added, and fermentation begins. The yeast consumes the sugars, converting them into alcohol and carbon dioxide. This stage typically lasts several days to weeks, depending on the beer style.
Conditioning
Following fermentation, the beer enters a conditioning phase, allowing flavors to harmonize and any remaining yeast or sediment to settle. This step improves the beer’s overall flavor, clarity, and stability. Conditioning can take place in the fermentation vessels or specialized conditioning tanks.
Packaging
Once the beer has conditioned, it is ready for packaging. Common packaging options include kegs, cans, or bottles. The beer is carefully filtered or carbonated, ensuring it is clear and appropriately carbonated before sealing. From here, it is ready to be distributed and enjoyed by beer lovers.
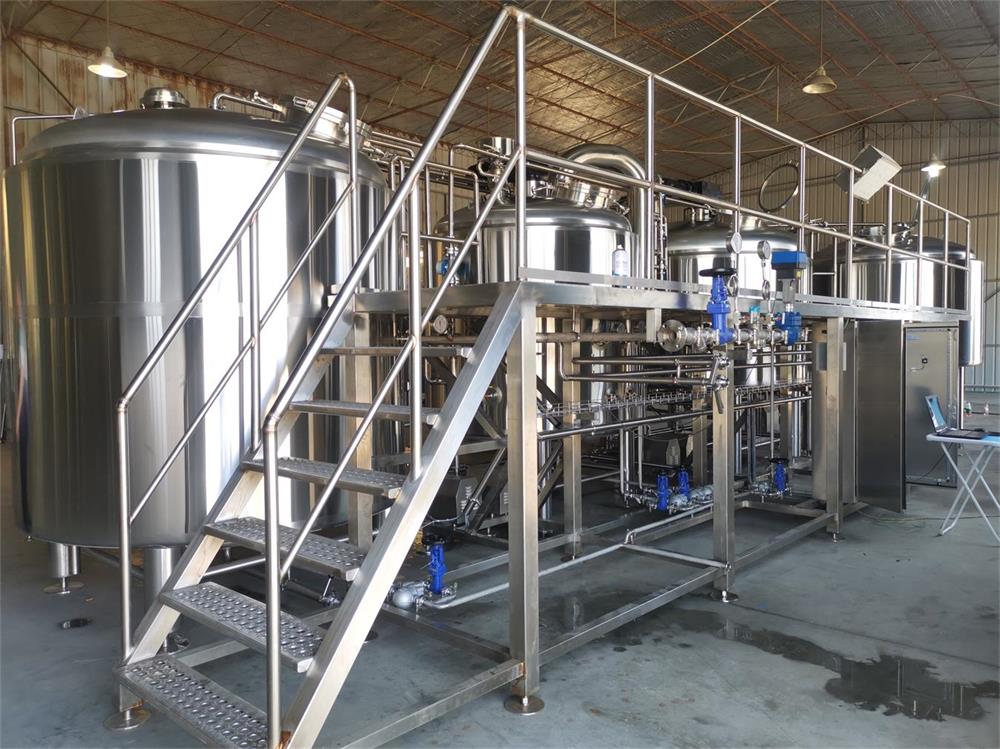
Considerations for Choosing a 5 Barrel Brewing System
When selecting a 5 barrel brewing system, several factors should be considered:
Space and Facility Requirements
Evaluate the available space and ensure the brewing system can be accommodated in your facility. Consider ceiling height, floor load-bearing capacity, and utility requirements such as water, electricity, and drainage.
Budget and Investment
Determine your budget and the level of investment you are willing to make. Consider the initial cost of the brewing system, installation expenses, and ongoing operational costs. It’s important to strike a balance between quality and affordability.
Brewing Goals and Production Volume
Define your brewing goals and estimate your production volume requirements. Ensure that the 5 barrel brewing system you choose can accommodate your desired output and future growth. Consider factors such as the number of batches you intend to brew per day or week, as well as the types of beer you plan to produce.
Quality and Reliability
Quality is paramount in the brewing industry. Look for a 5 barrel brewing system from a reputable manufacturer known for producing reliable and durable equipment. Read reviews, seek recommendations from fellow brewers, and inquire about warranties and customer support.
Support and Service
Brewing systems require regular maintenance and occasional repairs. Choose a manufacturer that offers responsive customer support and readily available spare parts. Reliable technical assistance and prompt service can minimize downtime and ensure smooth operations.
Maintenance and Cleaning of a 5 Barrel Brewing System
To ensure the longevity and performance of your 5 barrel brewing system, regular maintenance and cleaning are essential. Here are some key tasks to consider:
- Equipment Inspections: Regularly inspect all components, including valves, pumps, and heating elements, for signs of wear or damage. Replace any faulty or worn-out parts promptly.
- Cleaning Regimen: Develop a comprehensive cleaning regimen for your brewing system, including thorough cleaning of tanks, pipes, and filters. Use appropriate cleaning agents and sanitizers to maintain hygiene and prevent contamination.
- Preventive Maintenance: Schedule routine maintenance tasks, such as lubricating moving parts, checking electrical connections, and calibrating temperature sensors. This proactive approach helps identify and address potential issues before they escalate.
- Water Treatment: Depending on your water source, consider implementing water treatment methods to address any water quality issues that could affect the brewing process or beer flavor. Consult with experts or water treatment professionals for guidance.
- Documentation and Record-Keeping: Maintain detailed records of maintenance tasks, cleaning procedures, and any repairs or modifications performed on the brewing system. These records can help identify patterns, track equipment performance, and ensure compliance with regulations.
By following a comprehensive maintenance plan, you can extend the lifespan of your 5 barrel brewing system, optimize performance, and produce consistently high-quality beer.
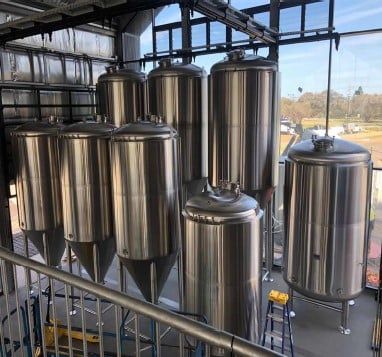
Conclusion
Investing in a 5 barrel brewing system opens doors to increased production capacity, brewing flexibility, consistent quality control, and cost efficiency for breweries of various sizes. Understanding the components, brewing process, and maintenance requirements empowers brewers to make informed decisions when selecting the right system for their needs. By considering factors such as space, budget, brewing goals, and the reputation of manufacturers, brewers can embark on a successful journey of brewing excellence with a 5 barrel brewing system.
FAQs
1. How much beer does a 5 barrel brewing system produce?
A 5 barrel brewing system can produce approximately 155 gallons or 590 liters of beer per batch.
2. Can I use a 5 barrel brewing system for homebrewing?
While it is technically possible to use a 5 barrel brewing system for homebrewing, it is more commonly used in commercial settings due to its larger size and higher production capacity.
3. Can a 5 barrel brewing system be upgraded to a larger system in the future?
Yes, one of the advantages of a 5 barrel brewing system is its scalability. Breweries can expand their operations by adding more 5 barrel units or upgrading to larger brewing systems as their production demands increase.
4. Are 5 barrel brewing systems suitable for brewpubs?
Yes, 5 barrel brewing systems are commonly used in brewpubs as they provide the capacity to brew on-site and meet the demand for fresh beer directly at the pub.
5. What is the approximate cost of a 5 barrel brewing system?
The cost of a 5 barrel brewing system can vary depending on the manufacturer, features, and customization options. Generally, it ranges from several tens of thousands to a few hundred thousand dollars, depending on the complexity and quality of the system.