Craft breweries are all the rage these days. They bring a personal touch to beer, offering unique flavors and that delightful local vibe. But behind every pint of artisanal beer is a system of specialized equipment working tirelessly. If you’re venturing into the craft brewing world, understanding the tools of the trade is essential. In this article, we’ll dive deep into the essentials, processes, suppliers, and even the pros and cons of different systems.
Table of Contents
ToggleOverview of Craft Brewery Equipment
Craft brewery equipment consists of a range of specialized tools designed to facilitate the brewing process. From mashing and fermentation to packaging, each piece of equipment serves a vital role. Here are the core components:
- Mashing Tun: Used to mix crushed grains with water, converting starches into fermentable sugars.
- Boil Kettle: Where the wort is boiled and hops are added for flavor.
- Fermenters: Tanks where yeast converts sugars into alcohol and carbon dioxide.
- Bright Tanks: Used to carbonate beer and prepare it for packaging.
- Cooling Systems: Essential for regulating temperatures during fermentation.
- Cleaning Systems: Keep the equipment hygienic and free of contaminants.
Each of these tools is designed to optimize efficiency, ensure quality, and maintain consistency. Let’s dive deeper into the brewing process and the role each piece of equipment plays.
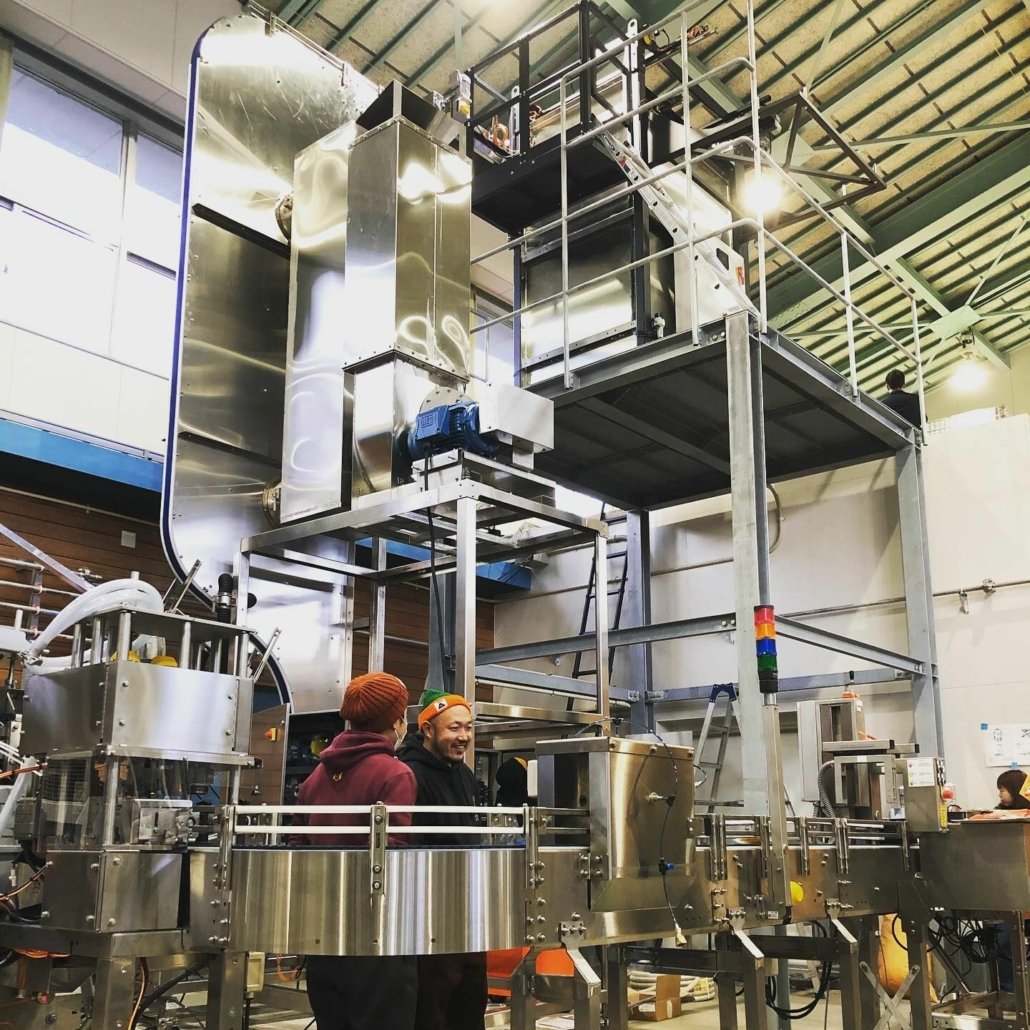
Troubleshooting Common Issues with Beer Fermenters
Fermenters are the workhorses of any brewery, but they’re not without challenges. Here are some common issues and solutions:
- Temperature Fluctuations: Fermentation requires precise temperature control. If your beer isn’t fermenting as expected, check the cooling system for faults or leaks.
- Contamination: A funky smell or taste? It’s likely due to improper cleaning or sealing. Regular cleaning and sanitizing are non-negotiable.
- Pressure Build-up: Fermentation produces CO2, and without proper venting, tanks can become dangerous. Ensure your valves and vents are functioning correctly.
- Stuck Fermentation: If the yeast stops working prematurely, it could be due to insufficient nutrients or incorrect temperature.
Proactive maintenance and regular checks are your best defense against these issues.
The Brewing Process Explained
Brewing beer is both art and science, requiring precision at every step. Here’s a breakdown:
- Mashing: Crushed grains (malt) are mixed with hot water in the mashing tun. This activates enzymes that break down starches into fermentable sugars.
- Lautering: The mixture is transferred to a lauter tun, where the liquid wort is separated from the grain husks.
- Boiling: The wort is boiled in the kettle, and hops are added for bitterness and flavor.
- Cooling: After boiling, the wort is rapidly cooled to fermentation temperature using a heat exchanger.
- Fermentation: The cooled wort is transferred to fermenters, where yeast is added to convert sugars into alcohol.
- Conditioning: Beer is transferred to bright tanks for carbonation and flavor refinement.
- Packaging: The finished beer is packaged into kegs, cans, or bottles.
Every stage requires precision and the right equipment to produce high-quality beer.
Capacity, Space, Design, and Layout of Craft Brewery Equipment
Feature | Details |
---|---|
Capacity | Ranges from 1-barrel (small-scale) systems to 30+ barrels for mid-sized craft breweries. Larger systems increase production but require more space. |
Space Requirements | Compact designs are available for small breweries, but larger setups need dedicated areas with appropriate ventilation and drainage. |
Design | Modular systems allow for expansion. Stainless steel is the material of choice for durability and hygiene. |
Layout | Efficient layouts minimize movement between equipment and optimize workflow. Custom layouts depend on brewery size and production goals. |
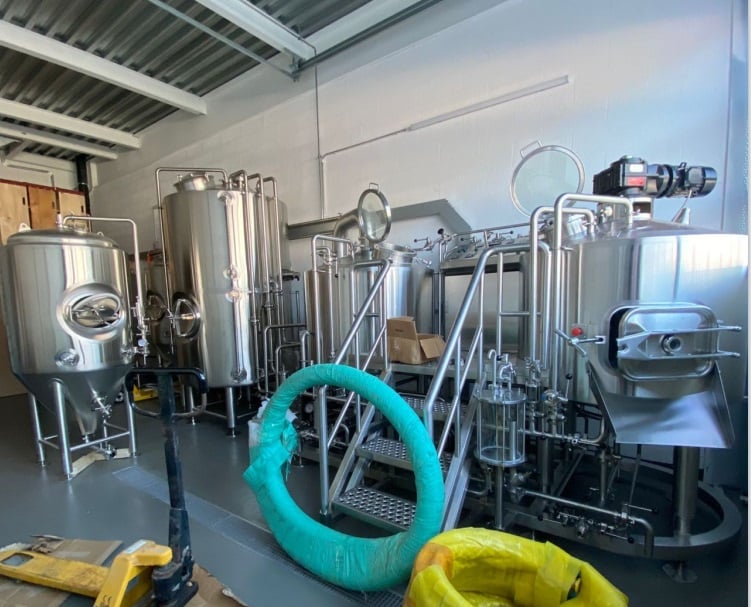
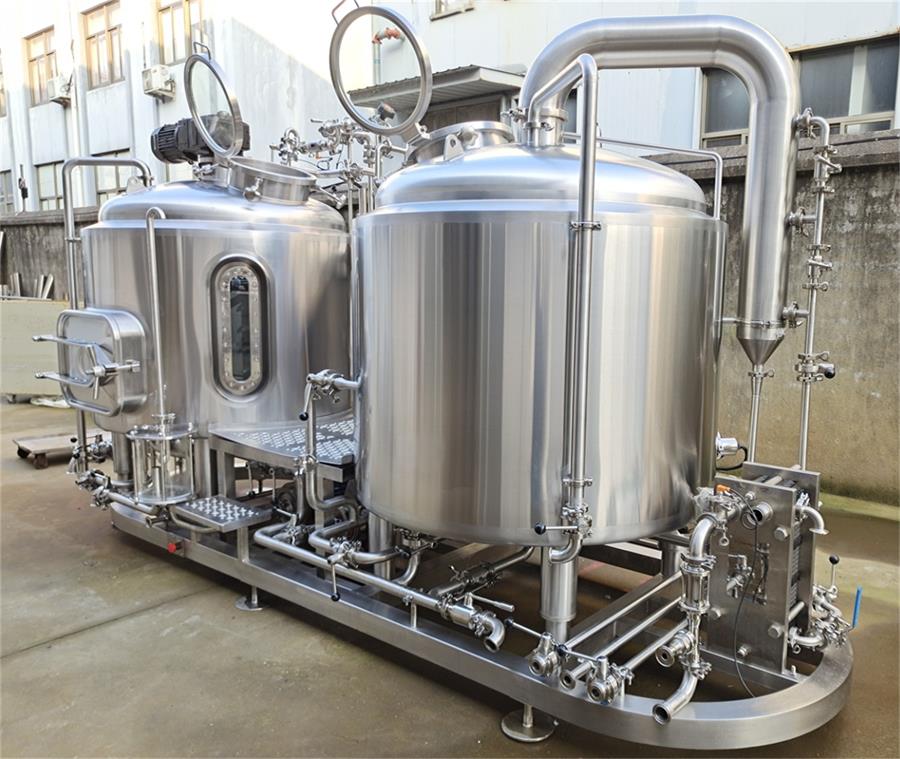
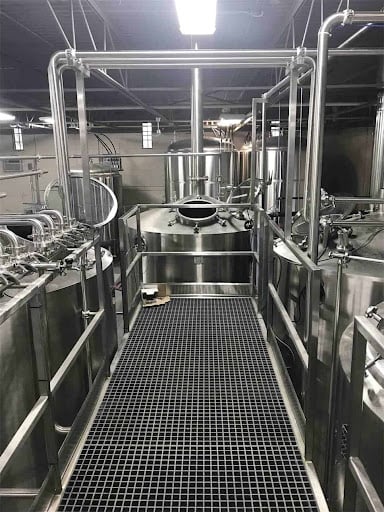
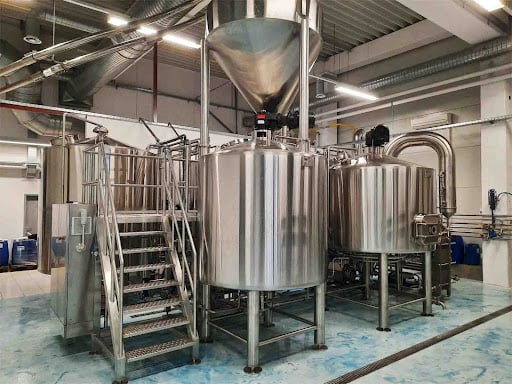
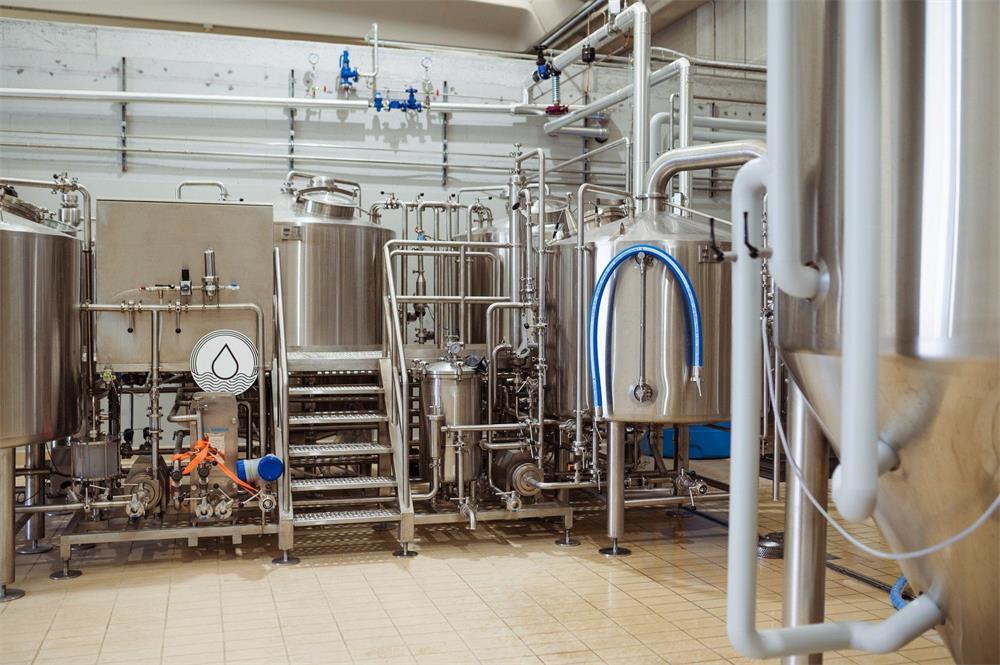
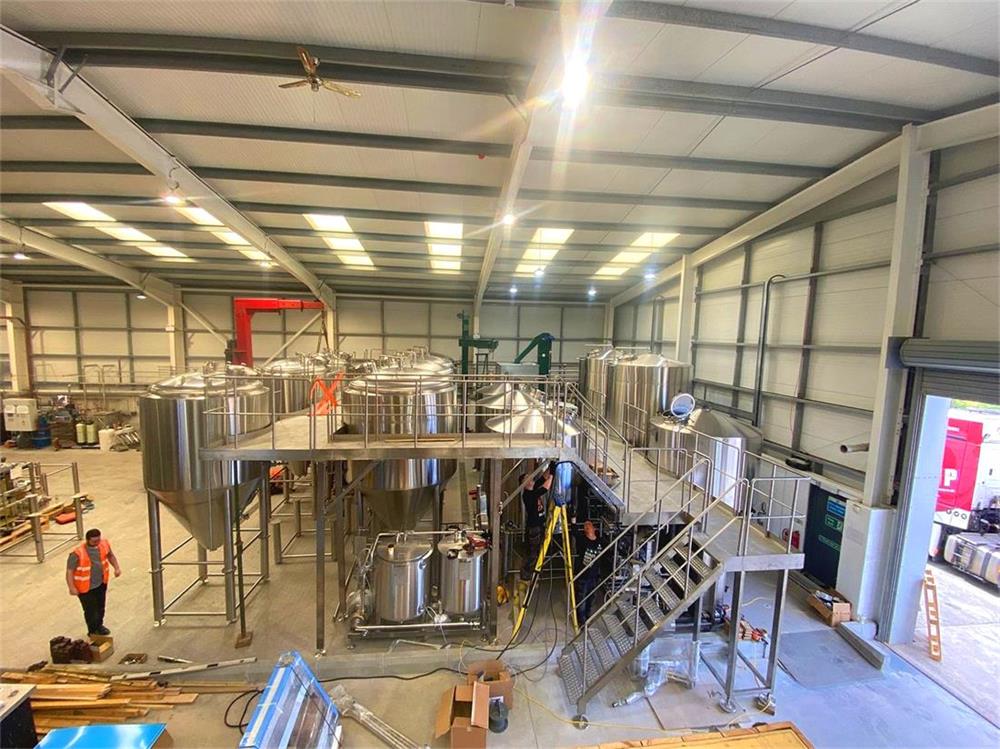
Suppliers and Price Range of Craft Brewery Equipment
Supplier | Price Range | Specialization |
---|---|---|
ABC Brew Systems | $10,000 – $50,000 | Small to mid-sized brewing systems with customization options. |
BrewTech Co. | $20,000 – $100,000 | Known for advanced automation and high-capacity systems. |
Global Brewing Supplies | $15,000 – $70,000 | Focus on sustainable and energy-efficient designs. |
Local Craft Solutions | $8,000 – $40,000 | Ideal for start-ups and nano breweries. |
Prices vary based on capacity, customization, and additional features.
Installation, Operation, and Maintenance of Craft Brewery Equipment
Aspect | Details |
---|---|
Installation | Requires skilled technicians to assemble tanks, connect cooling systems, and set up electrical components. |
Operation | Includes automated controls for temperature and pressure. Training is recommended for operating advanced systems. |
Maintenance | Regular cleaning, inspecting seals and valves, and ensuring proper calibration of sensors and controls. |
Proper installation and consistent maintenance extend the life of your equipment and ensure optimal performance.
Choosing the Right Supplier
Factor | Details |
---|---|
Reputation | Research customer reviews and testimonials to gauge reliability. |
Customization Options | Look for suppliers offering tailored solutions to meet your brewery’s unique needs. |
After-Sales Support | Ensure they provide training, maintenance, and readily available spare parts. |
Budget | Balance cost with quality—cheaper isn’t always better when it comes to durability. |
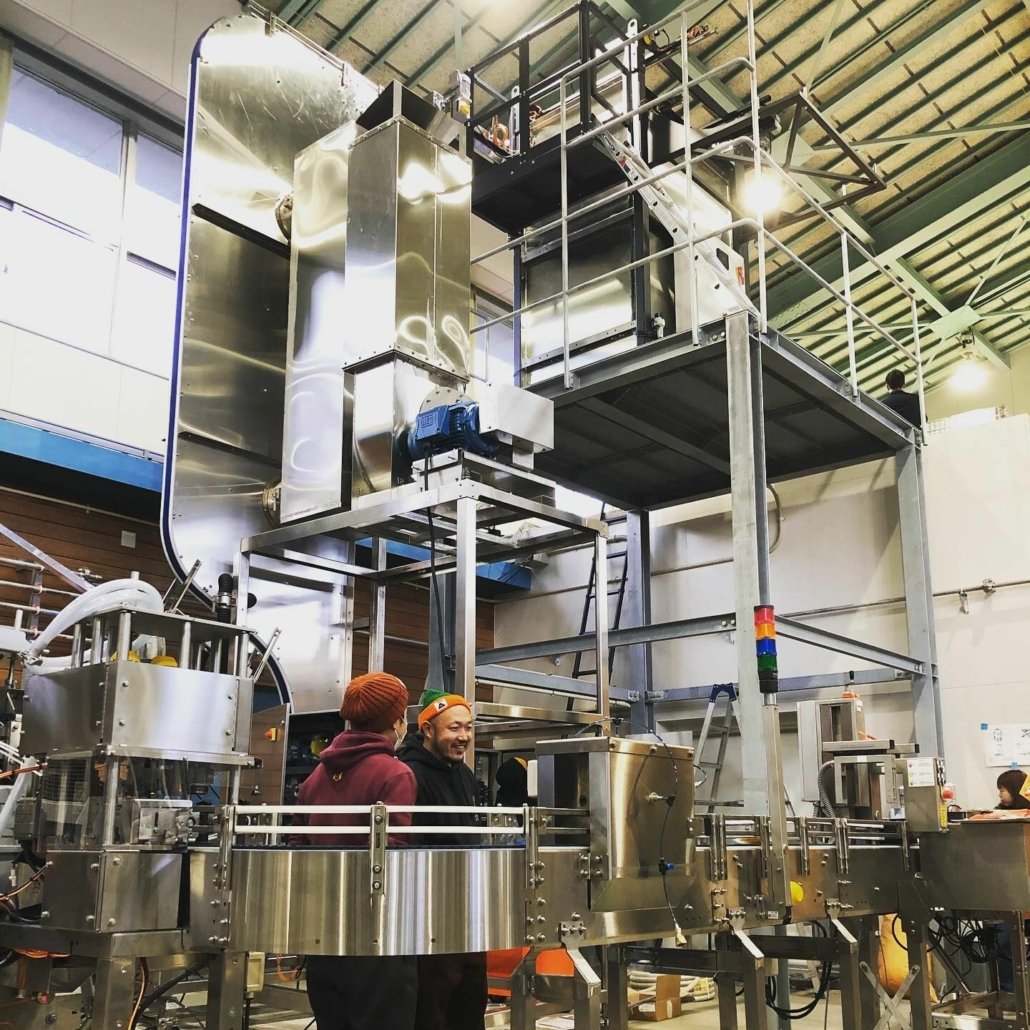
Pros and Cons of Craft Brewery Equipment
Aspect | Advantages | Limitations |
---|---|---|
Modularity | Allows expansion as the brewery grows. | Initial cost can be high. |
Automation | Improves consistency and efficiency. | May require specialized training to operate. |
Durability | Stainless steel equipment lasts for decades. | Regular maintenance is essential to prevent wear and tear. |
FAQs
Question | Answer |
---|---|
What size system should I start with? | Consider your production goals; nano breweries typically start with 1-3 barrel systems. |
How much does a brewery setup cost? | Costs range from $50,000 to $500,000 depending on capacity and automation. |
How often should equipment be cleaned? | After every batch, with periodic deep cleaning to remove buildup. |
Can I upgrade my system later? | Yes, modular systems are designed for expansion as your business grows. |