Table of Contents
ToggleOverview of Brewery Design Layouts
A well-thought-out brewery layout integrates functionality with aesthetics. Whether it’s a nano-brewery tucked into a garage or a sprawling craft brewery, the layout must balance space, workflow, and expansion possibilities. Key considerations include:
- Workflow Efficiency: Equipment placement should minimize movement between stages of brewing.
- Space Optimization: Compact layouts are ideal for small breweries, while larger spaces need logical zoning.
- Aesthetics: Breweries with public-facing spaces, like taprooms, need to look as good as they function.
- Scalability: The layout should accommodate future growth without significant overhauls.
Each brewery has unique needs, but these principles are universal. Let’s explore the brewing process and its layout implications.
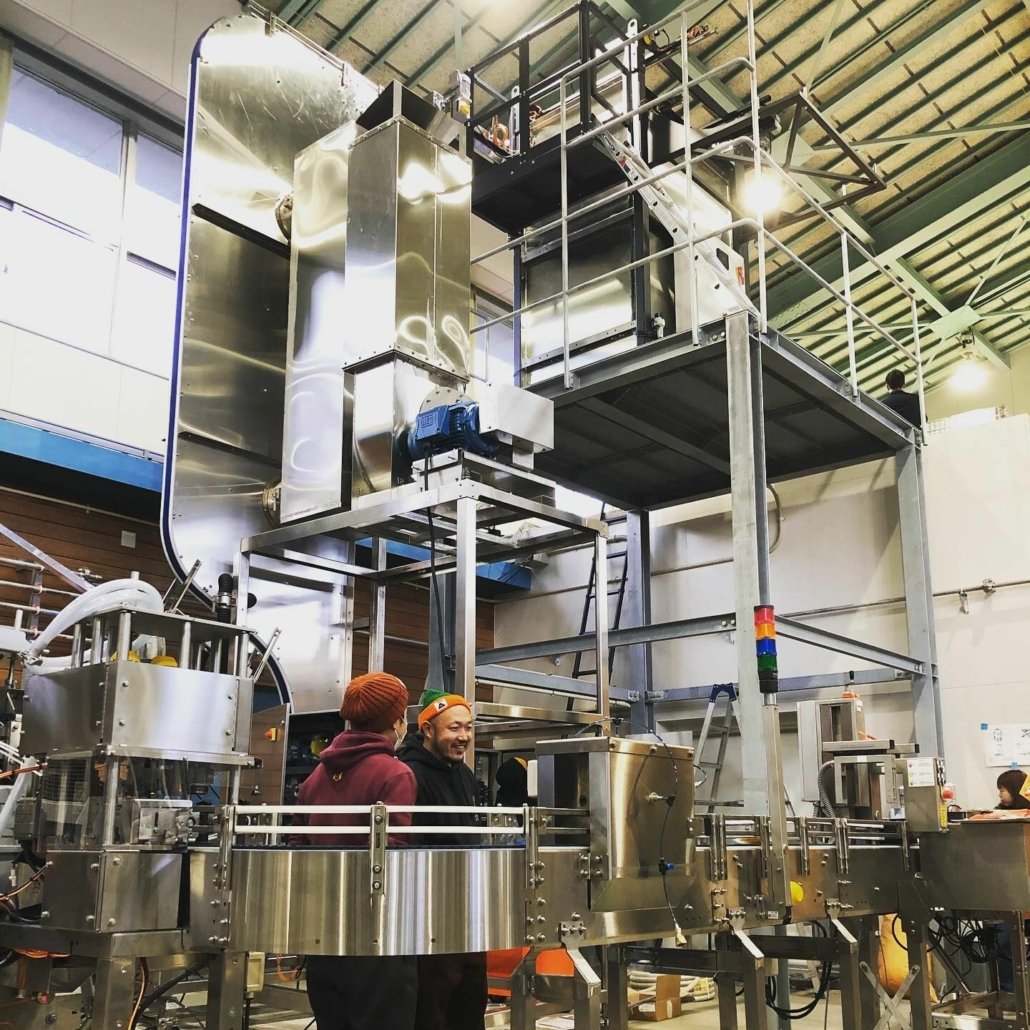
Troubleshooting Common Layout Issues
No layout is perfect, but foreseeing common challenges can save headaches later. Here are frequent issues and solutions:
- Bottlenecks in Workflow: Equipment too close or too far apart? This can disrupt the brewing rhythm. Map out each step before committing to a layout.
- Poor Drainage: Water and beer spills are inevitable. Without proper drainage, you’re looking at slippery hazards and cleanup nightmares. Invest in sloped flooring and ample drains.
- Limited Expansion Options: Many breweries outgrow their original layout. Consider future equipment additions and leave space for upgrades.
- Customer Flow in Taprooms: Public areas need a separate flow from production zones for safety and efficiency. Create distinct pathways and barriers where needed.
The Brewing Process and Its Impact on Layout
Understanding the brewing process helps determine the most efficient layout. Here’s how each stage translates into spatial and equipment needs:
- Milling: Grains are crushed in a mill to expose fermentable sugars. Position mills near the mashing tun to reduce transport time.
- Mashing and Lautering: The mash tun and lauter tun should sit close to each other. These tanks are where starches convert to sugars and wort is separated from grain.
- Boiling: The boil kettle, where wort is boiled and hops added, needs ventilation to handle steam.
- Cooling: Wort is rapidly cooled using a heat exchanger. Place this near fermentation tanks for quick transfer.
- Fermentation: Fermenters must have temperature control and adequate spacing for maintenance.
- Conditioning and Packaging: Bright tanks and packaging areas require separate spaces to maintain cleanliness and organization.
Capacity, Space, Design, and Customization Options
Feature | Details |
---|---|
Capacity | Nano systems (1-5 barrels), micro systems (5-30 barrels), or larger setups for regional breweries. |
Space Requirements | Nano-breweries need ~500 sq ft; mid-sized breweries may require 5,000+ sq ft for equipment and storage. |
Design | Modular systems are popular for flexibility. Stainless steel is standard for durability and hygiene. |
Customization | Custom tanks, unique layouts, and tailored workflows to match production goals and space constraints. |
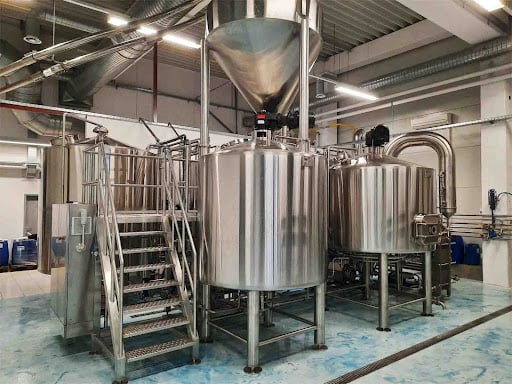
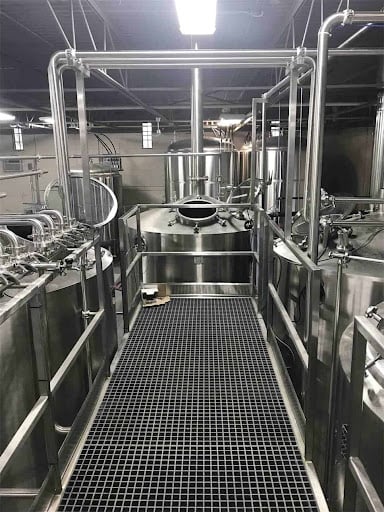
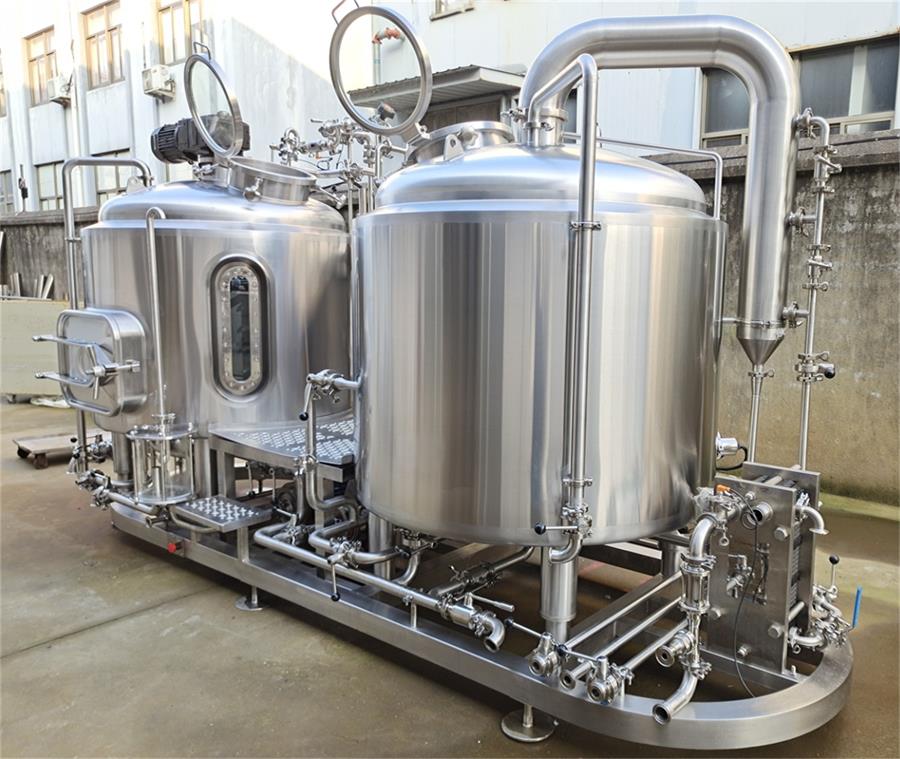
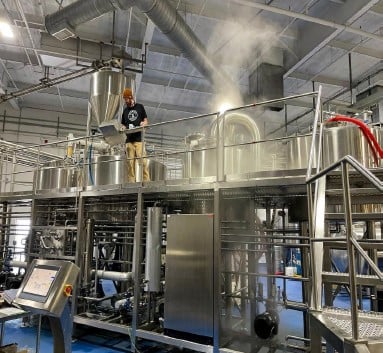
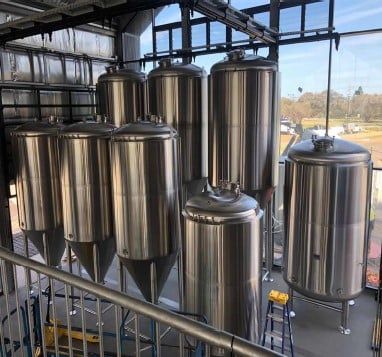
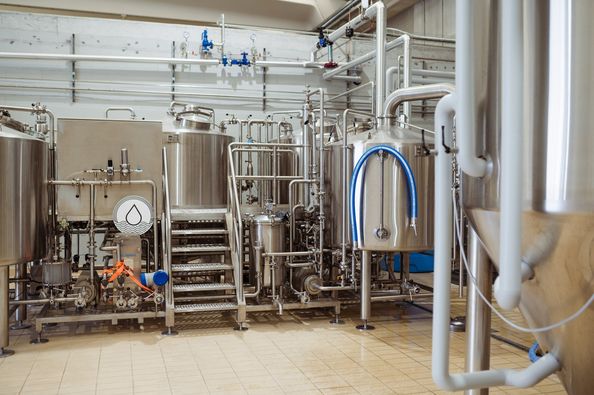
Suppliers and Price Ranges for Brewery Equipment
Supplier | Price Range | Specialization |
---|---|---|
ABC Brew Systems | $20,000 – $200,000 | Compact systems for small-scale brewing with scalable options. |
BrewTech Co. | $50,000 – $500,000 | High-capacity systems with cutting-edge automation features. |
CustomBrew Equipment | $30,000 – $150,000 | Focus on custom designs for unique brewery layouts. |
Local Craft Innovators | $15,000 – $100,000 | Affordable solutions for nano and microbreweries. |
Installation, Operation, and Maintenance of Brewery Equipment
Aspect | Details |
---|---|
Installation | Requires professional setup, including plumbing, electrical work, and calibration of brewing systems. |
Operation | Automated systems simplify processes but may require training. Manual systems need skilled operators. |
Maintenance | Routine cleaning, lubrication of moving parts, and calibration of sensors to ensure consistent performance. |
How to Choose the Right Brewery Design Layout
Factor | Details |
---|---|
Production Goals | Start with your expected output; this dictates equipment size and layout. |
Space Availability | Work with what you have, but leave room for future expansion. |
Budget | Balance quality with affordability. Cheaper options might compromise longevity. |
Customer Interaction | For breweries with taprooms, integrate aesthetics into your functional layout. |
Comparing Pros and Cons of Layout Options
Aspect | Advantages | Disadvantages |
---|---|---|
Linear Layout | Simplifies workflow and is easy to expand. | Requires more space and might increase walking distance. |
U-Shaped Layout | Compact and efficient for small spaces. | Harder to expand without major overhauls. |
Zoned Layout | Separates production, storage, and public areas for better organization. | Requires careful planning and often more space upfront. |
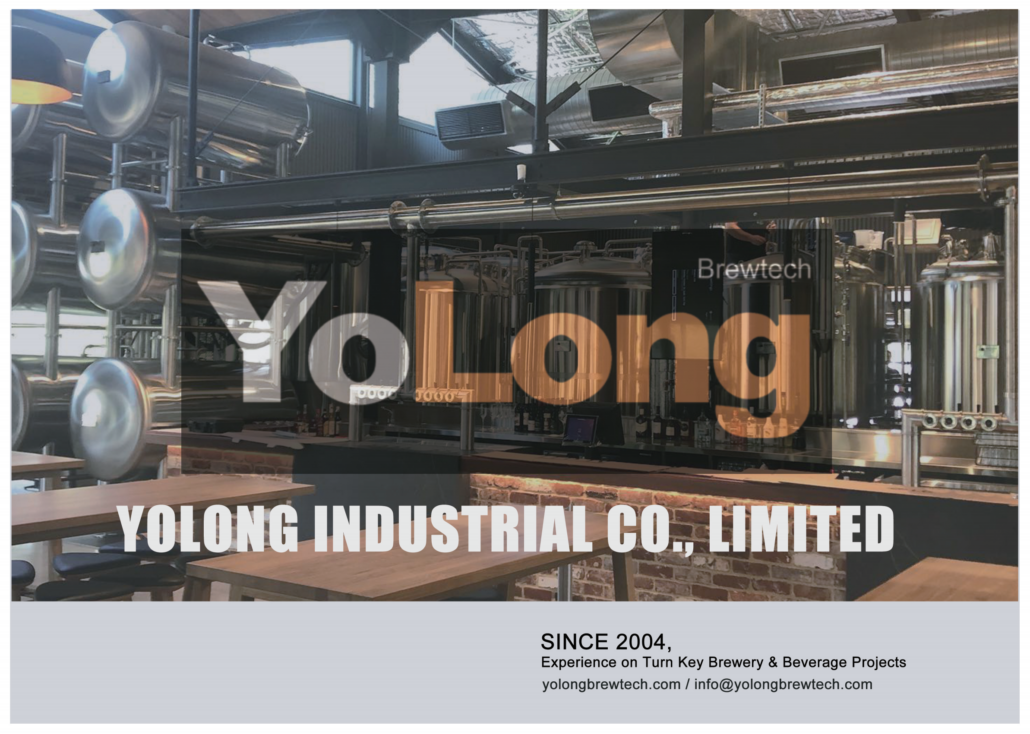
FAQs
Question | Answer |
---|---|
How much space does a brewery need? | Nano-breweries can operate in as little as 500 sq ft; larger setups need 5,000+ sq ft or more. |
Can I retrofit an existing space? | Yes, but it may require significant modifications for drainage, ventilation, and equipment placement. |
What layout is best for a taproom brewery? | Zoned layouts work best, separating production areas from customer-facing spaces. |
How do I plan for future expansion? | Choose modular equipment and design layouts with additional room for tanks and storage. |
Conclusion
Designing a brewery layout isn’t just about fitting equipment into a space; it’s about creating harmony between workflow, aesthetics, and functionality. With the right approach, you’ll set up a brewery that doesn’t just make great beer but also operates smoothly and scales easily. Remember, the best layouts evolve with your needs. Cheers to smart planning and successful brewing!