Table of Contents
ToggleIntroduction
Brewing beer is an age-old art that has evolved significantly with technological advancements. Among the crucial elements of the brewing process are fermentation tanks. These specialized vessels play a pivotal role in converting wort into beer through the fermentation process. In this article, we will delve into the world of brewery fermentation tanks, exploring their types, functionalities, maintenance, and the latest innovations.
What are Brewery Fermentation Tanks?
Brewery fermentation tanks are containers used to ferment the wort, a mixture of water, malt, hops, and yeast, during the beer-making process. The fermentation stage is where yeast converts sugars into alcohol and carbon dioxide, giving beer its alcoholic content and natural carbonation. Brewery fermentation tanks are specially designed to facilitate this transformation and allow brewers to control various parameters throughout the process.
The Importance of Brewery Fermentation Tanks
Maintaining Optimal Conditions
The success of the fermentation process depends on maintaining precise conditions within the fermentation tank. Factors such as temperature, pressure, and oxygen levels need to be carefully regulated to ensure the yeast’s optimal performance.
Fermentation Process
Understanding the fermentation process is crucial for brewers. Explaining the key steps of fermentation and the role of yeast will help readers grasp the significance of fermentation tanks in this complex and delicate process.
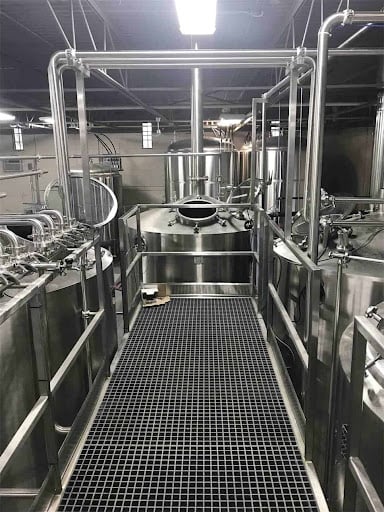
Types of Brewery Fermentation Tanks
Conical Fermenters
Conical fermenters are one of the most common types used in breweries. We will explore their unique design, benefits, and why they are favored by many brewers.
Open Fermentation Tanks
Although less common in modern breweries, open fermentation tanks have their advantages. We will discuss their historical significance and their influence on beer flavors.
Unitank Fermenters
Unitank fermenters serve a dual purpose, eliminating the need to transfer the beer between vessels during fermentation and maturation. This section will elaborate on their versatility and efficiency.
Horizontal Fermentation Tanks
Horizontal fermentation tanks are gaining popularity due to their space-saving design and ease of maintenance. We will examine how they compare to other types.
Factors to Consider When Choosing Fermentation Tanks
Size and Capacity
Selecting the right tank size is critical for breweries aiming to meet production demands without compromising beer quality. We will offer insights into choosing appropriate tank sizes based on brewery scale.
Material and Construction
The choice of materials used in fermentation tank construction impacts beer quality and tank longevity. We will discuss the pros and cons of various materials, such as stainless steel and plastic.
Cooling and Insulation
Maintaining the right temperature during fermentation is crucial. This section will delve into cooling and insulation methods used to control temperature fluctuations.
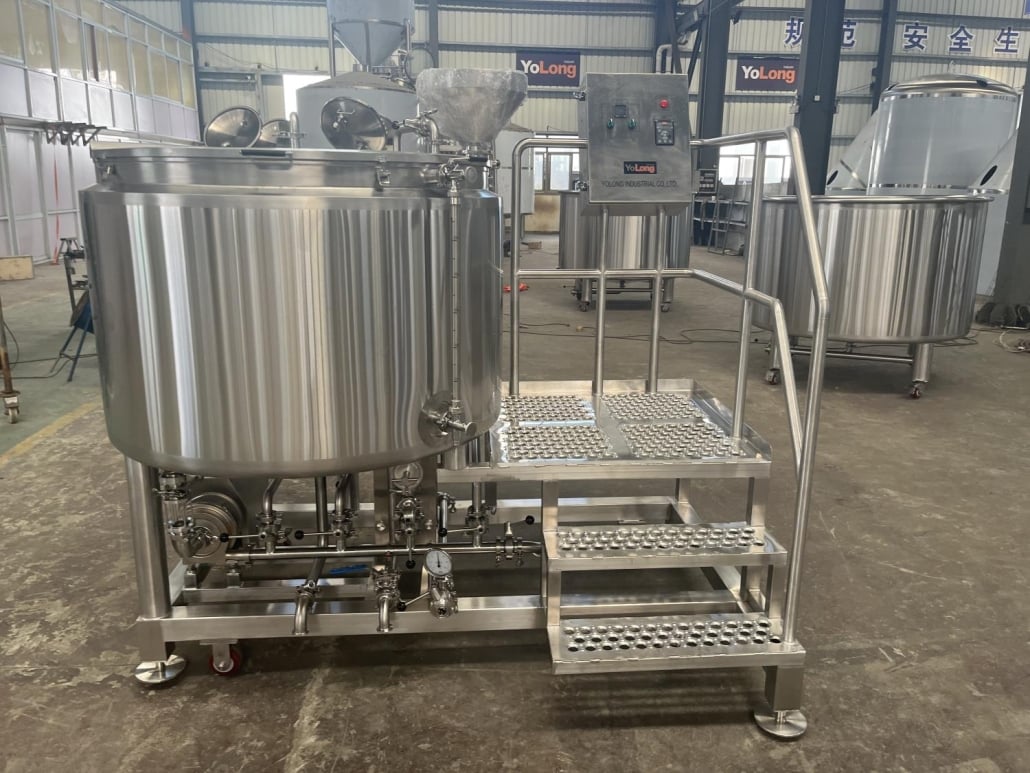
Cleaning and Sanitization of Fermentation Tanks
Manual Cleaning
Proper cleaning is essential to prevent contamination and off-flavors. This section will guide brewers on the importance of thorough manual cleaning.
CIP (Clean-in-Place) Systems
For larger breweries, automated CIP systems can streamline the cleaning process. We will explain the advantages and considerations for implementing CIP systems.
Managing Temperature during Fermentation
Cooling Jackets
Cooling jackets are a common method of regulating temperature during fermentation. We will detail their operation and benefits.
Glycol Chilling Systems
Larger breweries often employ glycol chilling systems for precise temperature control. This section will highlight their advantages and potential challenges.
Fermentation Control and Monitoring
Fermentation Software and Automation
Modern breweries are embracing automation to monitor and control fermentation parameters. We will explore software solutions and their role in the brewing process.
Monitoring Parameters
Monitoring various fermentation parameters is crucial for consistent beer quality. This section will discuss key parameters and their ideal ranges.
Troubleshooting Common Fermentation Issues
Stuck Fermentation
Stuck fermentation can be a significant setback for brewers. We will discuss common causes and remedies to tackle this issue.
Contamination
Contamination can ruin entire batches of beer. This section will offer guidance on identifying and preventing contamination.
Off-flavors
Off-flavors in beer can be a result of fermentation issues. We will explore common off-flavors, their causes, and how to prevent them.
Innovation in Fermentation Tank Technology
Bioreactors and Advanced Fermenters
Cutting-edge technology is making its way into brewing, with bioreactors and advanced fermenters revolutionizing the process. We will discuss their potential impact.
IoT Integration
Internet of Things (IoT) integration is transforming breweries, offering real-time monitoring and data analysis. We will explore how IoT is reshaping the brewing industry.
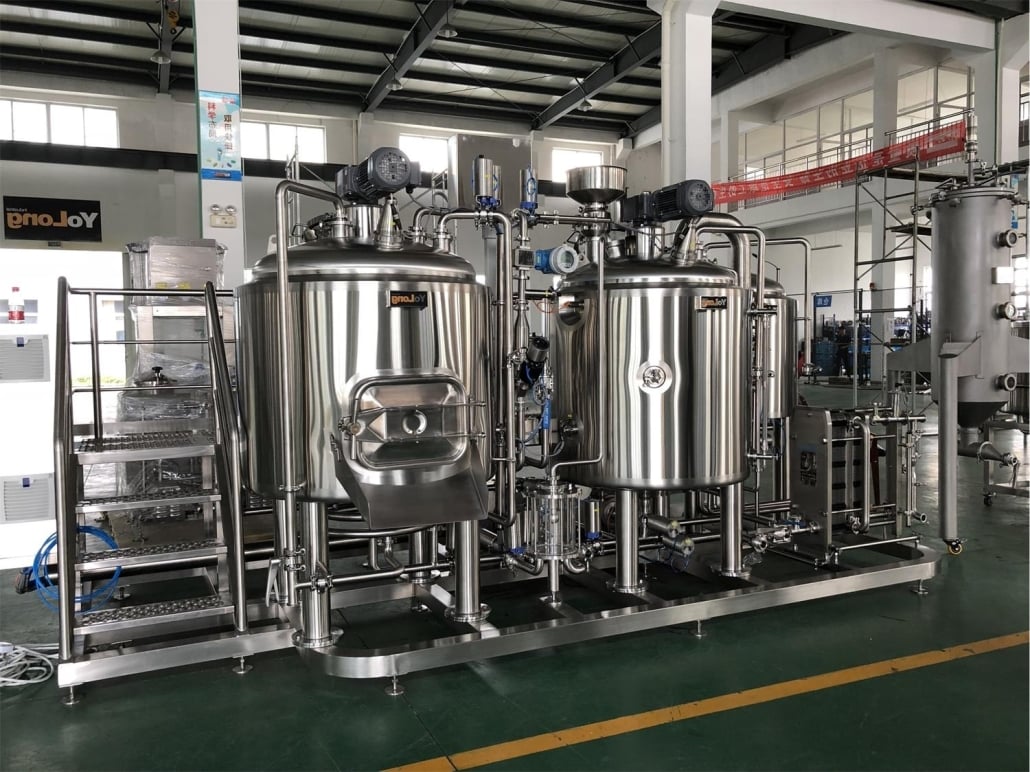
Sustainable Practices in Brewing with Fermentation Tanks
Energy Efficiency
Breweries are increasingly adopting sustainable practices to reduce energy consumption during fermentation. We will highlight some eco-friendly initiatives.
Water Conservation
Water is a precious resource, and breweries are taking steps to minimize water usage without compromising quality.
Waste Management
Brewing generates waste, and responsible waste management practices are gaining prominence. This section will cover sustainable waste management strategies.
Fermentation Tank Maintenance and Longevity
Regular Inspections
Routine inspections are vital for detecting and preventing issues before they escalate. We will guide brewers on best practices for tank inspections.
Preventative Maintenance
Proper maintenance can extend the life of fermentation tanks and ensure consistent performance. This section will offer preventative maintenance tips.
Case Studies: Successful Breweries and their Fermentation Tanks
Brewery A: Craft Brewing Success
We will explore the journey of a successful craft brewery and how their fermentation tank choices influenced their growth.
Brewery B: Scaling with Fermentation Tanks
Scaling a brewery can be challenging. We will examine how a brewery utilized fermentation tanks to facilitate expansion.
Future Trends in Brewery Fermentation Tanks
Sustainable Materials
The future of fermentation tanks lies in eco-friendly materials that reduce the environmental impact of brewing. We will explore innovative materials like biodegradable plastics, recycled steel, and sustainable composites that are gaining popularity in tank manufacturing.
Increased Automation
Automation is set to play a more significant role in brewery operations, including fermentation processes. We will discuss how automated fermentation systems can improve efficiency, reduce human errors, and ensure consistent beer quality.
Customization Options
Breweries are becoming more diverse, with unique brewing styles and recipes. This section will delve into the trend of customizable fermentation tanks, allowing brewers to tailor tanks to their specific needs.
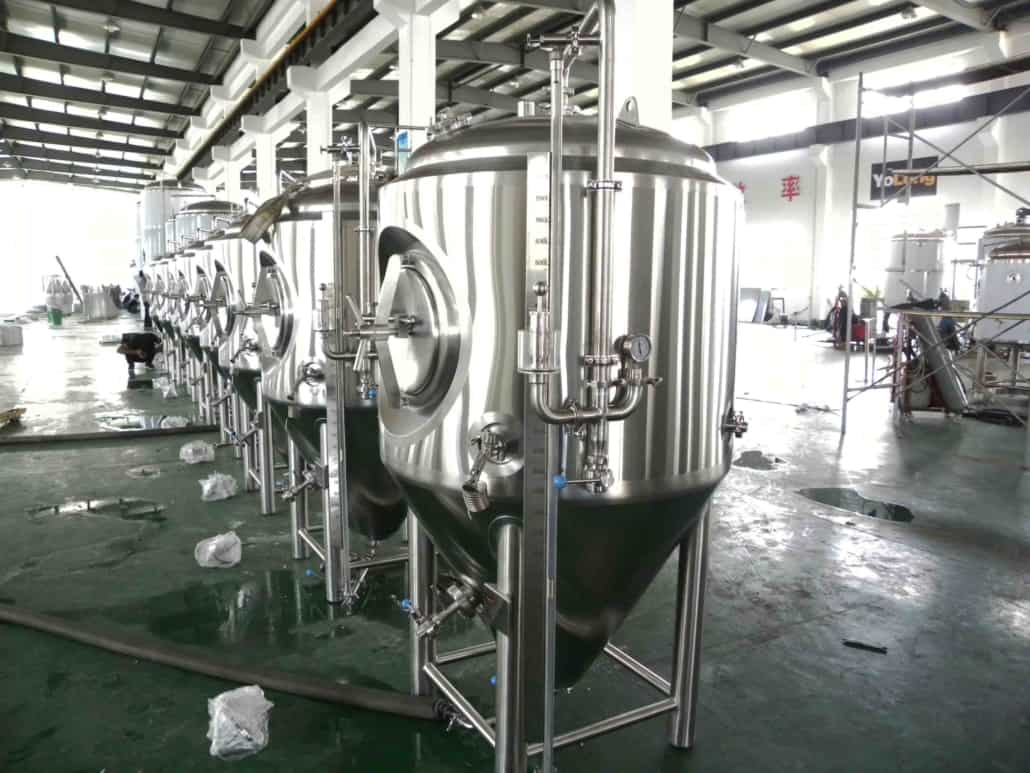
Conclusion
Brewery fermentation tanks are the heart of the brewing process, converting wort into delicious beer. Choosing the right tank, maintaining it, and embracing innovative technologies are crucial for success in the brewing industry. By optimizing fermentation processes, breweries can enhance beer quality, streamline production, and embrace sustainable practices for a greener future.
FAQs: Brewery Fermentation Tanks
Q: What is the primary function of brewery fermentation tanks?
A: Brewery fermentation tanks are used to ferment wort, converting sugars into alcohol and carbon dioxide to produce beer.
Q: What are conical fermenters, and why are they popular?
A: Conical fermenters are a common type of brewery fermentation tank with a tapered shape. They are favored for their ease of cleaning and yeast harvesting.
Q: How do cooling jackets work in fermentation tanks?
A: Cooling jackets are channels around the tank that allow cold water or glycol to flow, regulating the fermentation temperature.
Q: What are some common issues brewers face during fermentation?
A: Stuck fermentation, contamination, and off-flavors are some common challenges brewers encounter during fermentation.
Q: How can breweries implement sustainable practices in fermentation?
A: Breweries can adopt energy-efficient processes, reduce water consumption, and manage waste responsibly to embrace sustainability.