Maximizing Beer Fermentation Tanks
Overview: Why Maximizing Beer Fermentation Tanks Matters
Brewing beer is both an art and a science. At the heart of this process lies the fermentation tank, a vessel where yeast transforms sugars into alcohol and carbon dioxide. By optimizing these tanks, breweries can increase production, maintain consistency, and reduce operational costs. Whether you’re a craft brewer or a large-scale manufacturer, understanding how to maximize fermentation tanks can be the difference between good beer and great beer.
Different Types of Beer Fermentation Tanks
Beer fermentation tanks come in various types, each suited to different brewing processes and scales. Here’s a closer look at some common types:
1. Cylindroconical Fermentation Tanks
These are the industry standard for modern breweries. Their cone-shaped bottoms allow for efficient yeast collection and sediment removal, making them ideal for large-scale operations.
2. Open Fermentation Tanks
As the name suggests, these tanks have open tops, allowing for more oxygen interaction. They’re typically used for traditional styles like Belgian ales and wheat beers, where specific flavor profiles are desired.
3. Horizontal Fermentation Tanks
These tanks are often used in lager brewing. Their design increases the surface area, promoting faster yeast settling and enhancing flavor clarity.
4. Unitanks
Unitanks are versatile and can perform both primary fermentation and conditioning. This multi-functional design saves space and simplifies the process for smaller breweries.
Each type of tank has its pros and cons, and selecting the right one depends on the brewing style, production volume, and desired flavor characteristics.
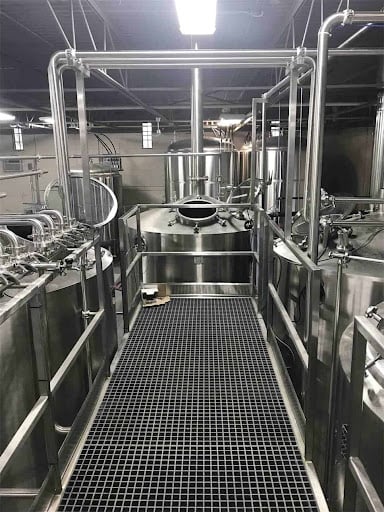
The Basic Functions of Beer Fermentation Tanks
To maximize efficiency, it’s essential to understand the primary functions of fermentation tanks. These include:
1. Capacity Management
The tank’s size directly affects production volume. Proper capacity utilization ensures that breweries can meet demand without overextending resources.
2. Temperature Control
Maintaining the right temperature is crucial for yeast activity. Modern tanks often feature advanced temperature control systems, allowing precise regulation for optimal fermentation.
3. Easy Cleaning and Maintenance
Sanitation is non-negotiable in brewing. Tanks designed for easy cleaning, with features like spray balls and smooth interiors, reduce the risk of contamination and save time.
By focusing on these functions, breweries can streamline their processes and ensure consistent beer quality.
Key Factors to Maximize Efficiency
1. Optimal Tank Design
Choosing tanks with features like insulated walls, advanced cooling systems, and ergonomic designs can significantly improve efficiency.
2. Advanced Monitoring Systems
Modern fermentation tanks often include sensors for pH, temperature, and pressure. These systems allow brewers to monitor and adjust fermentation parameters in real-time.
3. Yeast Management
Healthy yeast is the cornerstone of effective fermentation. Implementing a robust yeast harvesting and pitching system ensures consistent results.
4. Space Utilization
For smaller breweries, space is often at a premium. Compact tanks or unitanks can help maximize production without requiring additional square footage.
Technology and Innovation in Beer Fermentation Tanks
The brewing industry has embraced technology to enhance fermentation. Here’s a table outlining some key innovations:
Technology | Description | Benefits |
---|---|---|
Automated Temperature Control | Sensors and automated cooling jackets regulate temperatures. | Ensures consistent yeast activity. |
CIP (Clean-In-Place) Systems | Automated cleaning systems integrated into tanks. | Saves time and reduces contamination. |
Pressure Fermentation | Tanks designed to withstand higher pressures. | Allows for carbonation during fermentation. |
IoT Integration | Internet-connected tanks for remote monitoring and control. | Enhances efficiency and reduces errors. |
These advancements not only improve productivity but also enable brewers to experiment with new styles and techniques.
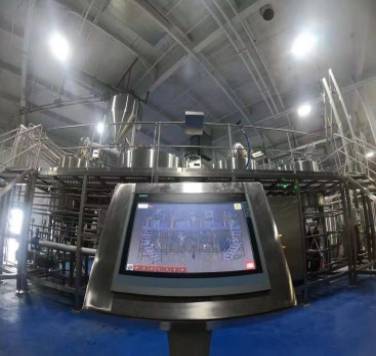
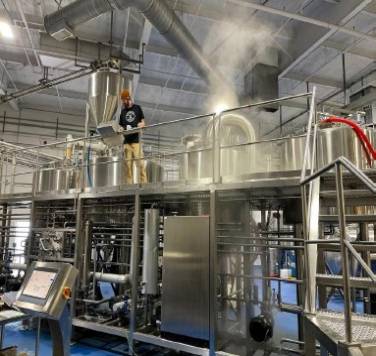
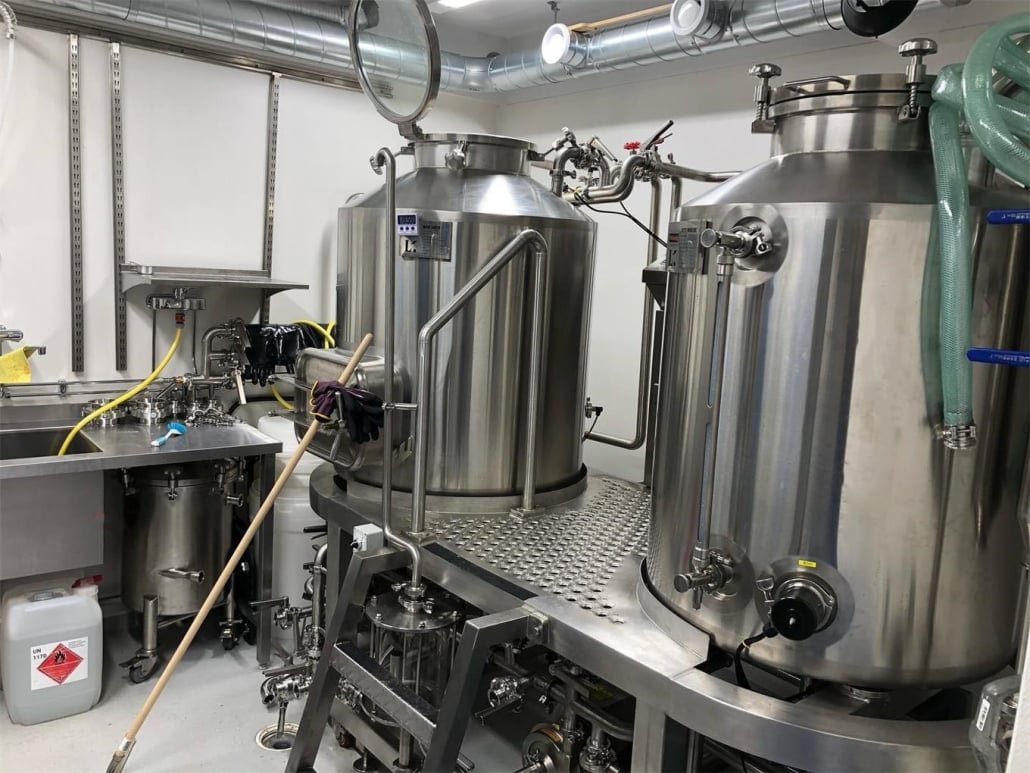
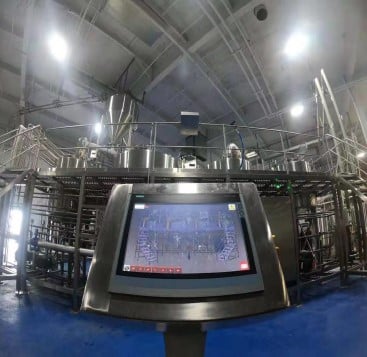
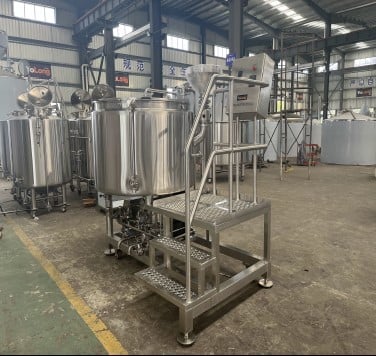
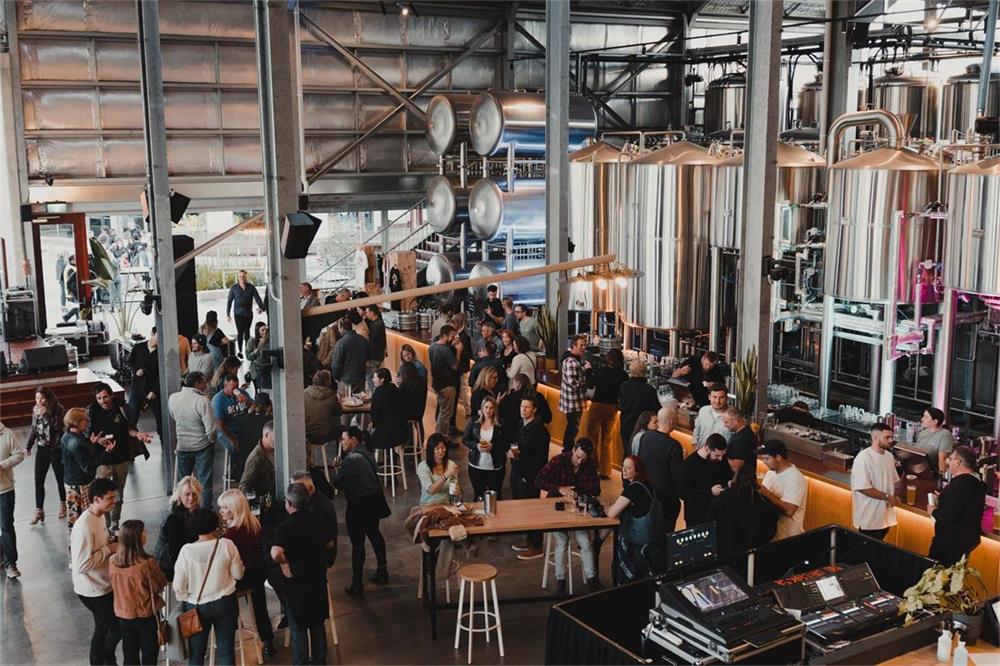
Common Challenges and Solutions in Maximizing Fermentation Tanks
1. Inconsistent Temperature Control
Challenge: Uneven temperatures can lead to off-flavors and stalled fermentation.
Solution: Invest in tanks with advanced cooling systems and regular calibration.
2. Contamination Risks
Challenge: Bacteria and wild yeast can ruin entire batches.
Solution: Implement rigorous cleaning protocols and use tanks with smooth, easy-to-clean surfaces.
3. Limited Production Capacity
Challenge: Scaling up production without additional space can be difficult.
Solution: Use vertical tanks or unitanks to maximize space efficiency.
How to Choose the Right Beer Fermentation Tanks
Selecting the right fermentation tank involves considering several factors:
1. Production Volume
Determine your current and future production needs. Oversizing can waste resources, while undersizing limits growth.
2. Brewing Style
Different beer styles require specific tank features. For instance, ales may benefit from open tanks, while lagers need horizontal designs.
3. Budget and Space
Evaluate your budget and available space. Compact, multi-functional tanks are ideal for smaller breweries.
4. Technology Integration
Modern tanks with IoT and automation can improve efficiency but come at a higher cost. Balance the investment with long-term benefits.
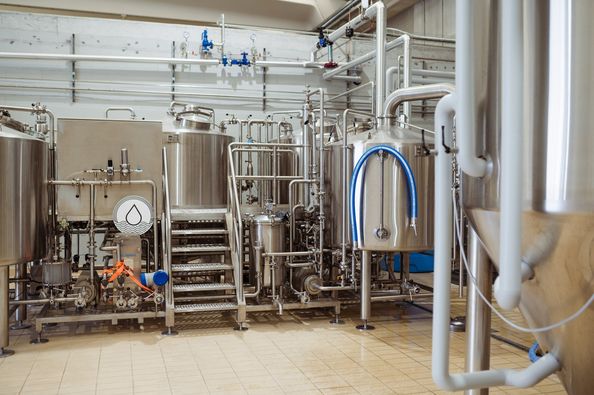
FAQs
Question | Answer |
---|---|
What is the ideal temperature for fermentation? | It depends on the beer style. Ales typically ferment at 60-75°F, while lagers require 45-55°F. |
How often should fermentation tanks be cleaned? | Tanks should be cleaned after every batch to maintain hygiene and prevent contamination. |
What is the lifespan of a fermentation tank? | With proper maintenance, stainless steel tanks can last 20+ years. |
Can fermentation tanks be customized? | Yes, many manufacturers offer custom tanks tailored to specific brewery needs. |
How do I prevent yeast from sticking to the tank walls? | Use tanks with smooth interiors and incorporate an effective agitation system. |
Share this entry
Interested in learning more about Brewing Systems including additional details and pricing information? Please use the form below to contact us!
YOLONG BREWERY EQUIPMENT FAQS
- Commercial Brewery / Craft Brewery / Microbrewery / Nanobrewery
- What is The Difference Between Craft Beer and Industrial Beer?
- The Bespoke Differences In Custom Brewing Systems
- Everything You Need to Know About Kettle Souring
- How to Choose Brewing Equipment for Your business?
- How To Choose The-Best Partner To Build Your Commercial Microbrewing System?
- Two Detection Sensors That You Need To Use In Your Brewhouse System
- Remote Control Applications in Brewing Equipment/How does it work?
- How To Clean Your Brand New Brewery Tanks?