Table of Contents
ToggleOverview of Direct Fire Brewing Systems
Brewing beer is both an art and a science, and the equipment you choose can significantly impact your results. Among the various brewing methods, direct fire brewing systems are a traditional yet effective option for many brewers. These systems heat the brewing kettle using an open flame, which creates a unique brewing environment that some brewers swear by. But what makes direct fire systems special, and how do they stack up against other methods?
In this guide, we’ll dive deep into everything you need to know about direct fire brewing systems. Whether you’re a homebrewer exploring new options or a professional looking to upgrade your equipment, this guide covers it all—from system features and troubleshooting tips to comparative tables and FAQs.
What Are Direct Fire Brewing Systems?
Direct fire brewing systems use an open flame to heat the brewing vessel directly from below. Unlike other methods such as steam or electric heating, direct fire systems rely on gas burners to provide intense, consistent heat. This setup is often praised for its simplicity, affordability, and ability to achieve rapid temperature changes.
Key characteristics of direct fire systems include:
- Direct Heat Transfer: The flame directly contacts the bottom of the kettle, delivering efficient heat.
- Versatility: Suitable for small-scale homebrewers and large-scale commercial operations.
- Cost-Effectiveness: Generally less expensive to purchase and operate compared to steam systems.
But why do brewers choose direct fire systems over alternatives? Let’s explore the brewing process and its nuances.
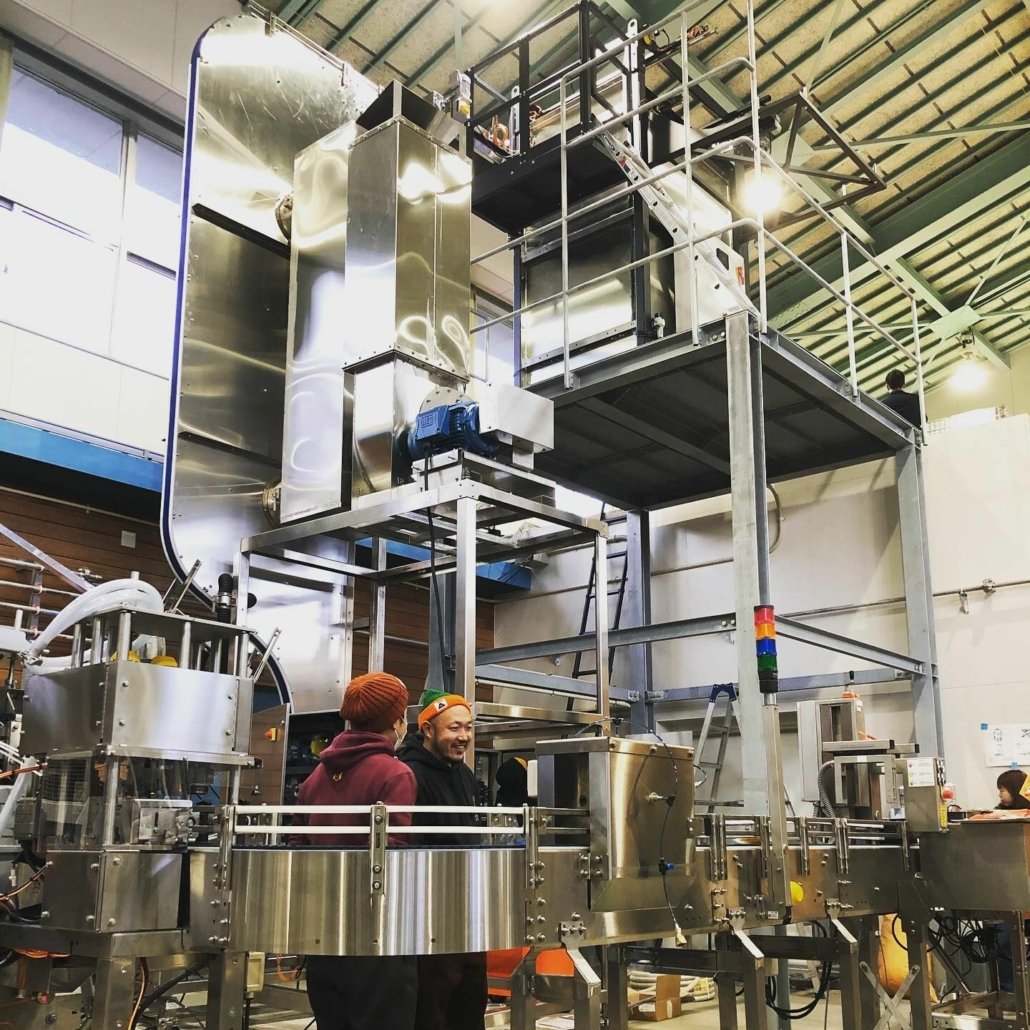
The Brewing Process Using Direct Fire Systems
Brewing beer involves several stages, from mashing and boiling to fermenting and packaging. Here’s how direct fire systems fit into the process:
- Mashing: In direct fire systems, the mash tun is heated from below, allowing precise temperature control. Brewers can achieve step mashing by adjusting the flame intensity.
- Boiling: The boiling stage is where direct fire systems truly shine. The open flame provides rapid heating, reducing the time it takes to reach a rolling boil. This efficiency is particularly beneficial for high-gravity beers.
- Cooling: Post-boil, direct fire systems don’t contribute directly to cooling but pair well with external chillers to bring the wort to fermentation temperature.
- Fermentation and Beyond: While fermentation happens in separate vessels, the precise boiling achieved in a direct fire system ensures a clean, high-quality wort—the foundation of great beer.
Troubleshooting Common Issues with Beer Fermenters
Even with a high-quality brewing system, issues can arise. Here are common problems brewers encounter with fermenters and how to address them:
Inconsistent Fermentation Temperatures
- Problem: Fluctuating temperatures can lead to off-flavors.
- Solution: Invest in temperature control solutions such as insulated jackets or glycol systems.
Stuck Fermentation
- Problem: Yeast activity halts before reaching the target gravity.
- Solution: Aerate the wort thoroughly before pitching yeast and consider adding yeast nutrients.
Contamination
- Problem: Unwanted microbes spoil the batch.
- Solution: Implement rigorous cleaning and sanitizing protocols for all brewing equipment.
Key Considerations: Capacity, Design, and Customization
Feature | Details |
---|---|
Capacity | Ranges from 5-gallon homebrew setups to 30-barrel commercial systems. |
Design | Compact designs suitable for tight spaces; larger systems for big batches. |
Customization | Options for burners, kettle materials (stainless steel or copper), and add-ons like thermometers and sight glasses. |
Choosing the right size and configuration depends on your brewing goals. Homebrewers may prefer a 10-gallon system, while commercial breweries might need something more substantial.
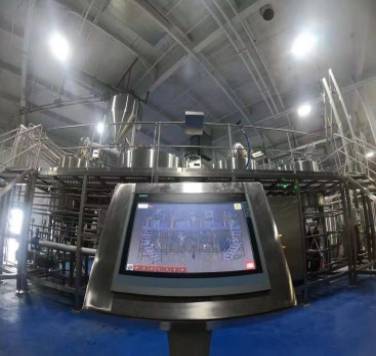
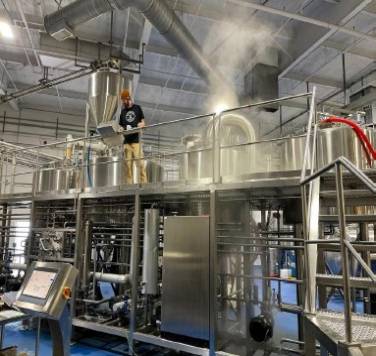
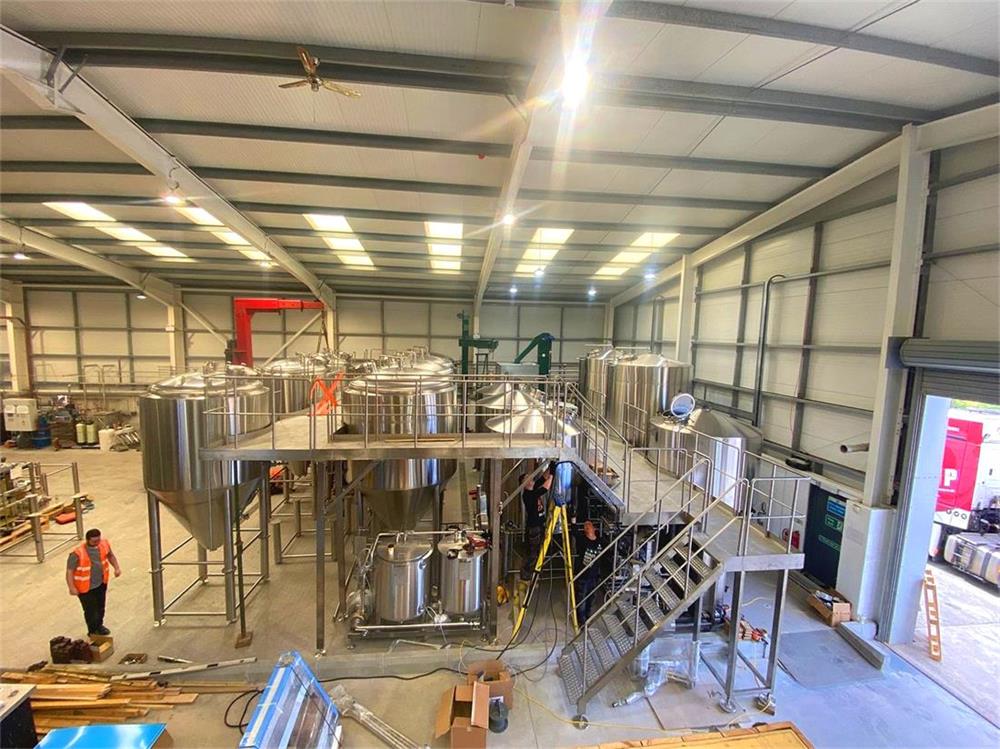
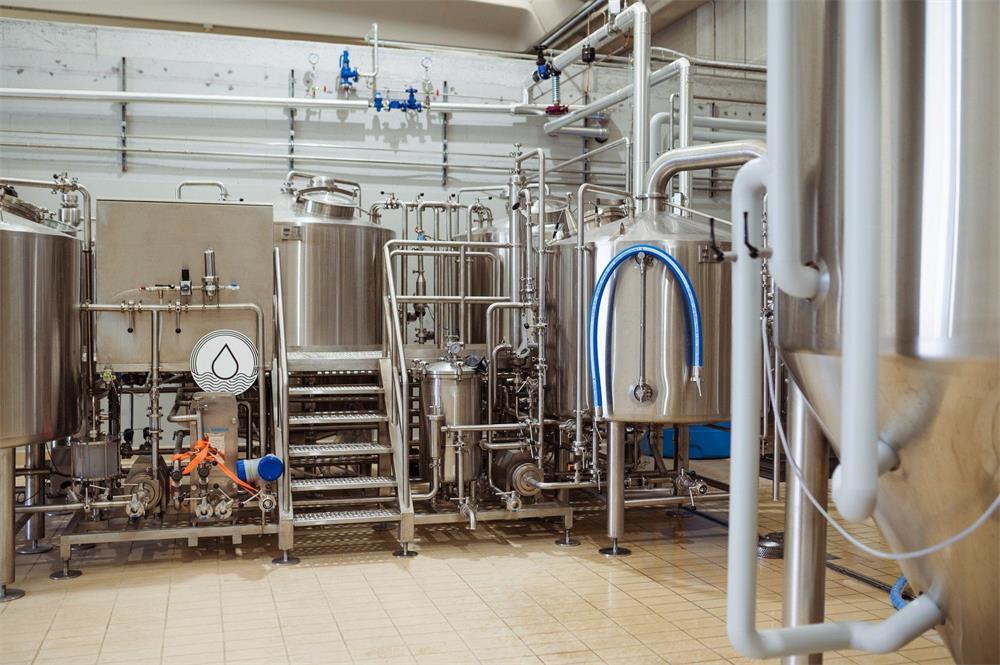
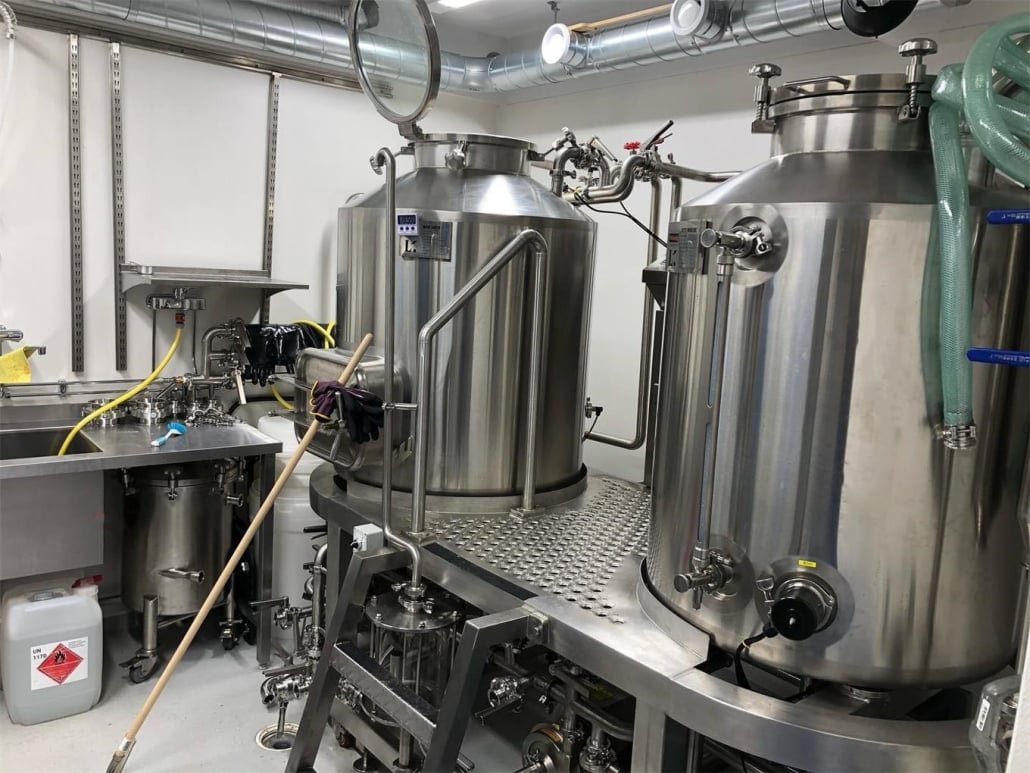
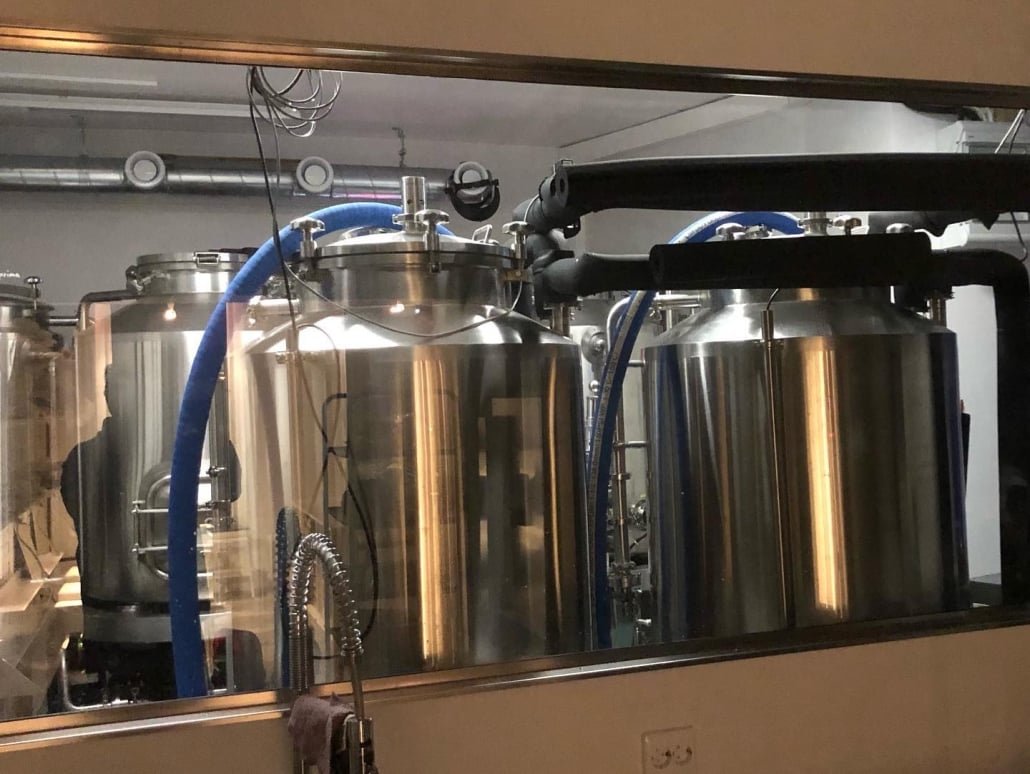
Suppliers and Price Range
Supplier | Price Range | Special Features |
---|---|---|
Spike Brewing | $1,000 – $5,000 | Durable stainless steel kettles with precise temperature control. |
Blichmann Engineering | $2,000 – $6,000 | Innovative designs with efficient burners and advanced features. |
Ss Brewtech | $1,500 – $4,500 | High-quality, customizable brewing systems. |
Custom Metalcraft | $3,000 – $10,000 | Commercial-grade systems tailored to specific brewery needs. |
Installation, Operation, and Maintenance
Aspect | Details |
---|---|
Installation | Requires proper ventilation and gas line setup. Consult local codes for compliance. |
Operation | Easy to use; adjust the flame intensity to control heat. |
Maintenance | Regular cleaning to remove soot buildup; check burner functionality. |
How to Choose a Supplier
Factor | Considerations |
---|---|
Reputation | Look for suppliers with strong reviews and industry recognition. |
Customer Support | Ensure the supplier offers responsive customer service and warranties. |
Customization | Choose a supplier who can tailor the system to your specific needs. |
Budget | Compare options to find the best value within your price range. |
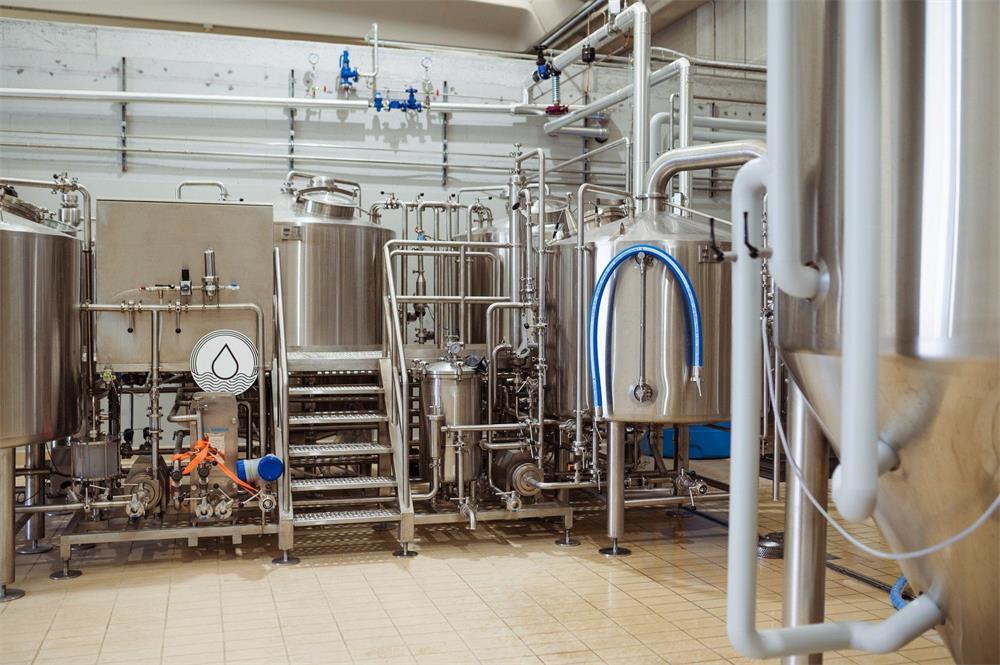
Advantages and Limitations of Direct Fire Brewing Systems
Advantages | Limitations |
---|---|
Affordable initial investment compared to steam systems. | Potential for uneven heating if not properly monitored. |
Simple to install and operate. | Requires a well-ventilated space due to open flame. |
Rapid heating for efficient brewing cycles. | Can create caramelization on kettle bottoms with some recipes. |
FAQ
Question | Answer |
---|---|
What fuels are used for direct fire systems? | Typically propane or natural gas, depending on availability and setup. |
Are direct fire systems suitable for all beers? | Yes, but they excel with styles requiring precise temperature control. |
How do I prevent scorching? | Use a thick-bottomed kettle and stir frequently during heating. |
Can I upgrade my system later? | Yes, many systems are modular and allow for add-ons like pumps or chillers. |