Unleashing the Potential of a 15 Barrel Brewing System
Introduction
In the world of craft brewing, the size and efficiency of brewing systems play a crucial role in meeting the demands of a growing market. One such popular brewing system is the 15 barrel brewing system. Designed to strike the perfect balance between production capacity and operational flexibility, this system is highly favored by both established breweries and ambitious newcomers. This article explores the ins and outs of the 15 barrel brewing system, its advantages, components, brewing process, and more. So, let’s dive in and discover why this system is making waves in the craft brewing industry.
What is a 15 Barrel Brewing System?
Before we delve into the details, let’s clarify what a 15 barrel brewing system actually is. A 15 barrel brewing system refers to a set of equipment used in the beer production process, capable of producing approximately 465 gallons (1760 liters) of beer in a single batch. The system typically consists of various vessels and components that work together to convert raw ingredients into high-quality beer, ready to be enjoyed by discerning beer enthusiasts.
Advantages of a 15 Barrel Brewing System
Increased Production Capacity
A significant advantage of a 15 barrel brewing system is its increased production capacity compared to smaller systems. As breweries grow and demand rises, the ability to produce larger batches becomes crucial for meeting market needs while maintaining product consistency.
Efficiency in Brewing Process
The 15 barrel brewing system offers notable efficiency improvements over smaller systems. With larger vessels and automated controls, brewers can streamline the brewing process, reducing manual labor and optimizing time management.
Cost-effectiveness
While a 15 barrel brewing system requires a higher initial investment than smaller systems, it proves to be more cost-effective in the long run. The larger batches result in reduced labor and packaging costs per unit of beer, making it a sound financial choice for expanding breweries.
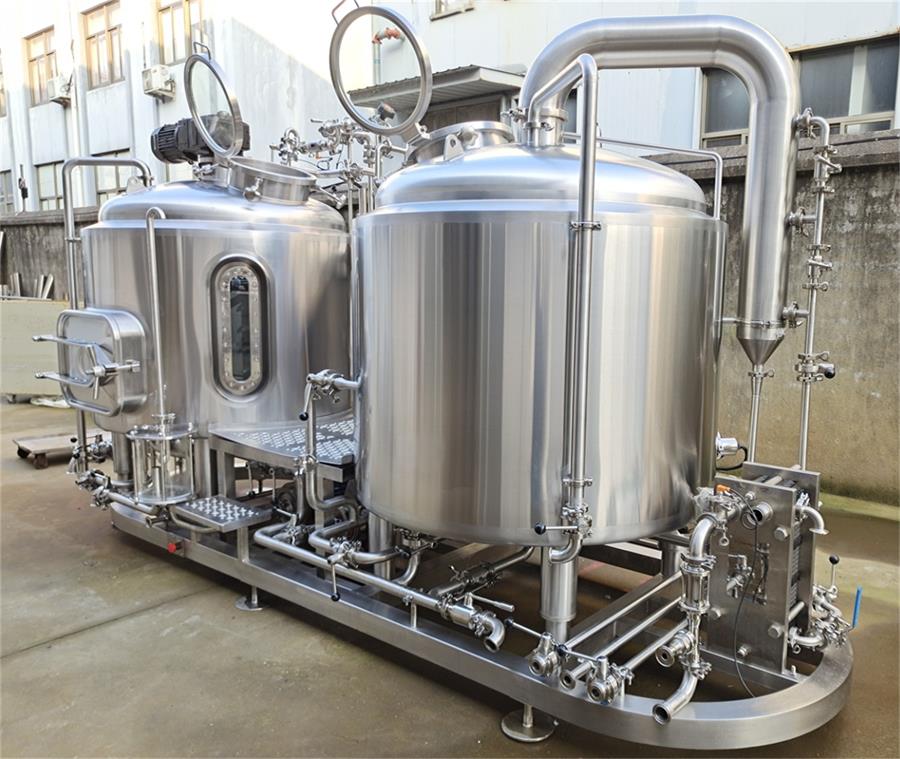
Components of a 15 Barrel Brewing System
A 15 barrel brewing system comprises several key components that work in harmony to produce outstanding beer consistently.
Brew Kettle
The brew kettle is a vital component where the milled grains are mixed with water and boiled with hops to extract flavors, bitterness, and aromas. It is equipped with a heating system to control the boiling process.
Mash Tun
The mash tun is responsible for the mashing process, where milled grains are mixed with hot water to convert starches into fermentable sugars. It provides the ideal conditions for enzymatic activity.
Fermentation Tanks
Fermentation tanks are where the magic happens – yeast converts sugars into alcohol and carbon dioxide, turning wort into beer. These tanks come in various sizes and materials to accommodate different brewing styles.
Wort Chiller
The wort chiller rapidly cools down the boiled wort to a temperature suitable for yeast fermentation. It is essential to achieve the desired flavor profile and prevent off-flavors.
Control Panel
The control panel acts as the brain of the brewing system, allowing brewers to monitor and adjust various parameters such as temperature, pressure, and timing during the brewing process.
Stay tuned for the next part, where we will explore the rest of the components and processes involved in a 15 barrel brewing system, along with tips for selecting the right location for your brewery.
Selecting the Right Location for a 15 Barrel Brewery
Choosing the right location for your 15 barrel brewery is a critical decision that can significantly impact your business’s success. Here are some factors to consider:
- 5.1 Accessibility: Ensure your brewery is easily accessible to suppliers, distributors, and customers. A location with good transportation links can reduce logistics costs and attract more visitors.
- 5.2 Zoning and Permits: Check local zoning regulations to ensure your brewery can operate legally at the chosen location. Obtain all necessary permits to avoid potential legal issues.
- 5.3 Market Presence: Research the existing craft beer market in the area. A location with a strong craft beer culture and a thriving craft beer community can offer great opportunities for growth.
- 5.4 Foot Traffic: If you plan to have a taproom or retail space, consider a location with high foot traffic to attract walk-in customers and increase sales.
- 5.5 Utility Requirements: Confirm that the chosen location can meet your utility needs, including water supply, electricity, and waste disposal.
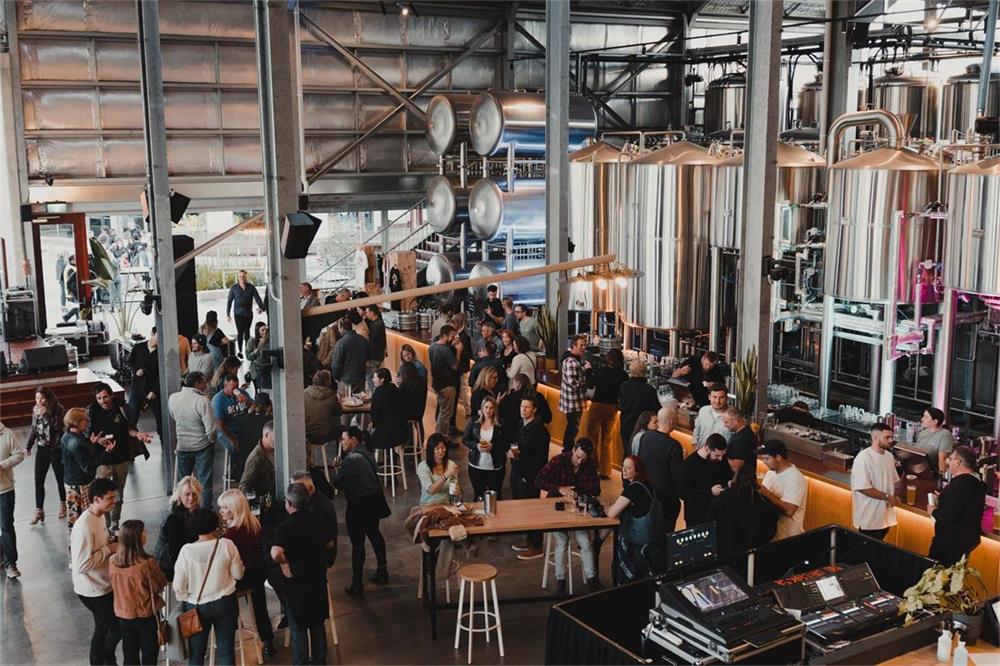
Installation and Setup Process
Installing and setting up a 15 barrel brewing system requires careful planning and execution. Here’s an overview of the process:
- 6.1 Facility Preparation: Ensure the chosen facility is equipped to handle the weight and size of the brewing equipment. Make necessary modifications to accommodate the system.
- 6.2 Equipment Installation: Carefully install each component of the brewing system, ensuring all connections are secure and in compliance with safety standards.
- 6.3 Testing and Calibration: Thoroughly test each component to ensure they function correctly and accurately. Calibrate the control panel to maintain precise brewing conditions.
- 6.4 Training and Staffing: Train your brewing team on how to operate and maintain the 15 barrel brewing system. Hiring experienced staff can streamline the setup process.
Brewing Process with a 15 Barrel System
Now that your 15 barrel brewing system is up and running, let’s explore the brewing process step by step:
Mashing
Mashing begins by mixing milled grains with hot water in the mash tun. The mixture is held at specific temperatures to activate enzymes that convert starches into fermentable sugars.
Boiling
After mashing, the wort is transferred to the brew kettle for boiling. During this process, hops are added to impart bitterness and aroma to the beer. Boiling also sterilizes the wort.
Fermentation
Once the wort is cooled, it is transferred to fermentation tanks, and yeast is added. Yeast converts sugars into alcohol and carbon dioxide during fermentation, creating beer.
Conditioning
After fermentation is complete, the beer undergoes a conditioning phase to mature and develop its flavors. This period allows any remaining off-flavors to dissipate, resulting in a smoother taste.
Cleaning and Maintenance
Proper cleaning and maintenance are vital to ensuring the longevity and consistent performance of your 15 barrel brewing system.
- 8.1 Regular Cleaning Schedule: Implement a thorough cleaning schedule for all brewing equipment, including tanks, kettles, and pipes, to prevent contamination and off-flavors.
- 8.2 Preventative Maintenance: Conduct regular maintenance checks on all components, identifying and addressing potential issues before they become major problems.
- 8.3 Training Staff on Maintenance: Train your brewing team on proper cleaning and maintenance procedures to maintain a well-functioning system.
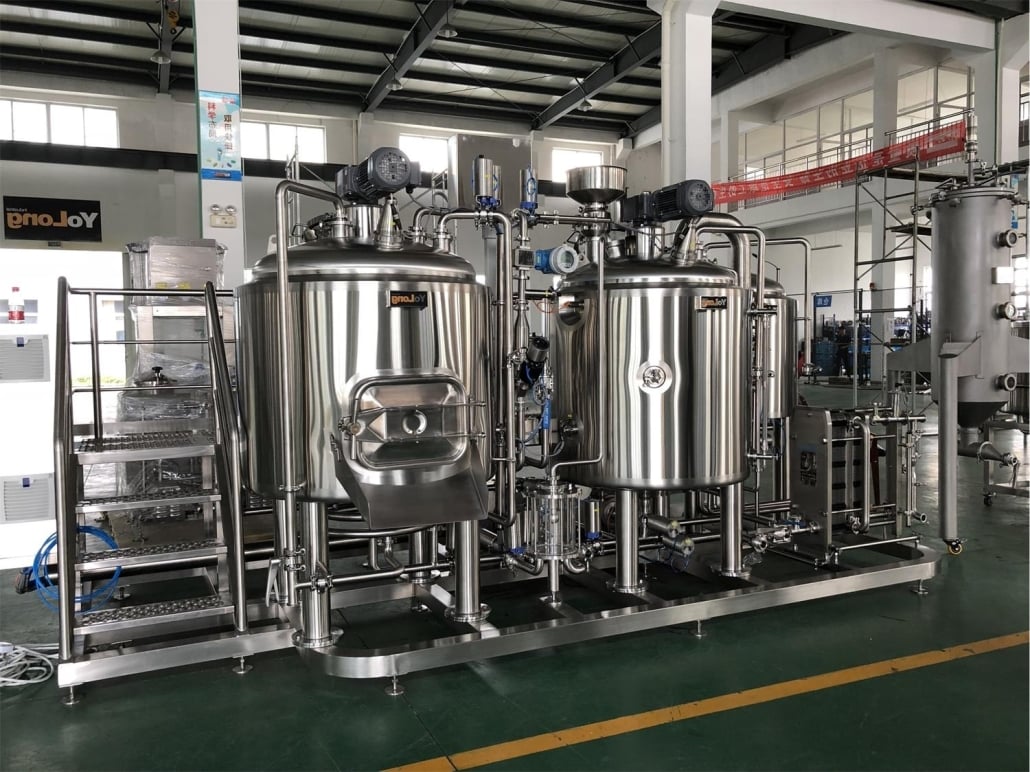
Quality Control and Assurance
Maintaining high-quality standards is crucial for the success of your brewery. Implementing a robust quality control process is essential.
- 9.1 Quality Testing: Regularly test beer samples for flavor, aroma, and consistency. Conducting sensory evaluations can help identify any deviations from desired characteristics.
- 9.2 Record-keeping: Keep detailed records of each batch, including ingredients, brewing parameters, and quality test results. This data can be invaluable for troubleshooting and improvement.
- 9.3 Feedback from Customers: Listen to customer feedback and reviews to understand how well your beer is received in the market and identify areas for improvement.
Stay tuned for the next part, where we will explore popular brewing styles and delve into sustainability and environmental considerations in a 15 barrel brewing system.
Popular Brewing Styles with a 15 Barrel System
With your 15 barrel brewing system in full swing, it’s time to explore the diverse array of beer styles you can produce:
Ales
Ales are top-fermented beers that encompass a wide range of styles, including Pale Ales, India Pale Ales (IPAs), Brown Ales, and more. They are known for their fruity and robust flavors, often featuring a variety of hops.
Lagers
Lagers are bottom-fermented beers that are typically characterized by a clean and crisp taste. Pilsners, Bocks, and Märzen are some popular lager styles you can craft with your 15 barrel system.
IPAs
IPAs deserve special attention due to their immense popularity among craft beer enthusiasts. With a 15 barrel system, you can experiment with different hop varieties and brewing techniques to create a wide range of IPAs, from hazy New England IPAs to bitter West Coast IPAs.
Stouts and Porters
Stouts and Porters are dark, rich, and full-bodied beers, often featuring roasted malt flavors, chocolate notes, and coffee undertones. They are a perfect choice for cooler seasons.
Sustainability and Environmental Considerations
As a responsible brewery owner, it’s essential to consider sustainability and environmental impact:
- 11.1 Water Conservation: Implement water-saving practices during the brewing process, such as recycling water and optimizing cleaning procedures.
- 11.2 Energy Efficiency: Invest in energy-efficient equipment and technologies to reduce your brewery’s carbon footprint.
- 11.3 Waste Management: Implement effective waste management practices, including recycling, to minimize the environmental impact of your brewery.
Challenges and Troubleshooting
Running a brewery comes with its fair share of challenges. Here are some common issues you may encounter:
- 12.1 Consistency: Ensuring batch-to-batch consistency can be challenging but is essential for building a loyal customer base.
- 12.2 Equipment Malfunctions: Be prepared to troubleshoot and fix equipment malfunctions promptly to minimize downtime.
- 12.3 Inventory Management: Managing inventory efficiently can be complex, but it’s vital for meeting customer demand and avoiding waste.
The Future of 15 Barrel Brewing Systems
As the craft beer industry continues to grow, the future looks bright for 15 barrel brewing systems. With ongoing advancements in technology and a thriving craft beer culture, these systems will remain a popular choice for ambitious brewers.
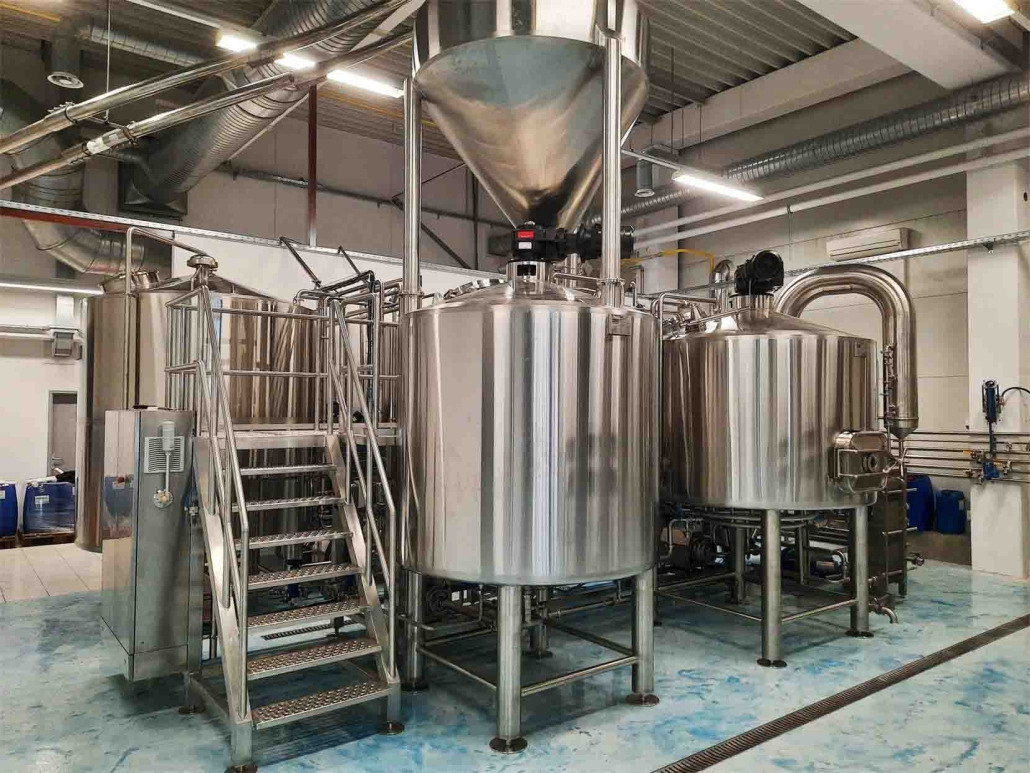
Conclusion
In conclusion, a 15 barrel brewing system offers a perfect balance of production capacity, efficiency, and cost-effectiveness for breweries seeking growth and success. From selecting the right location to mastering the brewing process and maintaining quality, careful planning and attention to detail are key to thriving in the competitive craft beer market. Embrace sustainability, stay adaptable to industry trends, and continue experimenting with various beer styles to keep your brewery relevant and appealing to beer enthusiasts. Cheers to your journey in the world of craft brewing!
FAQs
Q1: Can I upgrade my brewing system to a larger capacity in the future?
Yes, many breweries choose to upgrade to larger brewing systems as their business expands. However, it’s essential to carefully plan the transition and consider the logistical and financial implications.
Q2: Are 15 barrel brewing systems suitable for small craft breweries?
While 15 barrel brewing systems are generally more suitable for medium-sized breweries, they can be used by smaller craft breweries with ambitions for growth. It’s important to assess your current and future production needs before investing.
Q3: Can I brew small batches with a 15 barrel system?
Yes, most 15 barrel brewing systems allow brewers to adjust batch sizes, enabling them to brew smaller batches if needed. This flexibility is advantageous for experimenting with new recipes and limited-edition releases.
Q4: How can I market my craft beer effectively?
Effective marketing is crucial for the success of your craft beer. Utilize social media, brewery events, collaborations, and partnerships to create a strong brand presence and connect with your target audience.
Share this entry
Interested in learning more about Brewing Systems including additional details and pricing information? Please use the form below to contact us!
YOLONG BREWERY EQUIPMENT FAQS
- Commercial Brewery / Craft Brewery / Microbrewery / Nanobrewery
- What is The Difference Between Craft Beer and Industrial Beer?
- The Bespoke Differences In Custom Brewing Systems
- Everything You Need to Know About Kettle Souring
- How to Choose Brewing Equipment for Your business?
- How To Choose The-Best Partner To Build Your Commercial Microbrewing System?
- Two Detection Sensors That You Need To Use In Your Brewhouse System
- Remote Control Applications in Brewing Equipment/How does it work?
- How To Clean Your Brand New Brewery Tanks?