Mastering the 20 Barrel Brewing System:from Selection to Benefits
What is a 20 barrel brewing system?
A 20 barrel brewing system refers to a brewing system that can produce 20 barrels (or approximately 620 gallons) of beer at one time. This system is a middle-ground option, larger than the small-scale systems often used by craft brewers and smaller than the large-scale systems used by major breweries.
These systems are comprised of several key components:
- Mash Tun: A vessel where the milled grains are mixed with water. The mixture, known as ‘mash’, undergoes various temperature rests to activate enzymes and convert starches into fermentable sugars.
- Boil Kettle: After mashing, the liquid, now called ‘wort’, is transferred to the boil kettle where it is boiled and hops are added for flavor and bitterness.
- Fermentation Tanks: Post boiling, the wort is cooled and transferred to fermentation tanks. Here, yeast is added and the fermentation process begins.
- Brite Tanks: Once fermentation is complete, the beer is transferred to these tanks where it is carbonated and clarified before packaging.
The 20 barrel brewing system is a popular choice for mid-size breweries, brewpubs, and some larger craft breweries. Its capacity allows for a sufficient scale of production without being overwhelmingly large. Many brewers find this size to be a sweet spot – allowing for both experimentation and larger batch production.
While the setup can vary based on the manufacturer and specific needs of the brewery, the foundational equipment remains consistent across the board. Investing in a 20 barrel brewing system means committing to a substantial production level, making it vital for breweries to understand the nuances and intricacies of the system.
How much does a 20 barrel brewing system cost?
A 20 barrel brewing system’s cost varies based on numerous factors, including manufacturer, additional features, quality of materials, and region. However, they are a significant investment, making it imperative for prospective buyers to understand the price breakdown and what to expect.
Here’s a rough breakdown of pricing based on various features and components:
Component | Price Range (USD) |
---|---|
Mash Tun | $10,000 – $25,000 |
Boil Kettle | $12,000 – $28,000 |
Fermentation Tanks | $15,000 – $35,000 |
Brite Tanks | $13,000 – $30,000 |
Control System | $5,000 – $15,000 |
Additional Features | $5,000 – $20,000 |
The total price for a basic 20 barrel brewing system generally ranges from $60,000 to $153,000. However, with added features like advanced automation, superior materials, or specialized components, the price can go beyond this range.
Beyond the primary components, several other factors can influence the price:
- Automation: Automated systems, which allow for more precise control over brewing parameters, typically come at a premium.
- Material Quality: Brewing systems made with higher grade materials or specialized finishes (like copper) will be pricier.
- Customization: Custom-built systems, tailored to specific brewery needs, often come with additional costs.
- Brand Reputation: Established brands or those known for superior quality can charge a premium for their systems.
- Region: Depending on where you are purchasing from, import taxes, shipping costs, and local manufacturing costs can influence the final price.
- Installation and Training: Some companies offer installation and training services at an additional charge.
- After-Sales Service: Warranties and post-purchase services can add to the overall cost.
Breweries must also consider the operational costs, such as raw materials (grains, hops, yeast), utilities, labor, and maintenance, which aren’t included in the initial investment.
When deciding on a brewing system, it’s essential to look beyond just the initial price. Consider the system’s efficiency, durability, and the manufacturer’s reputation. Remember that the cheapest option might not always be the best in the long run, especially when quality and reliability are paramount.
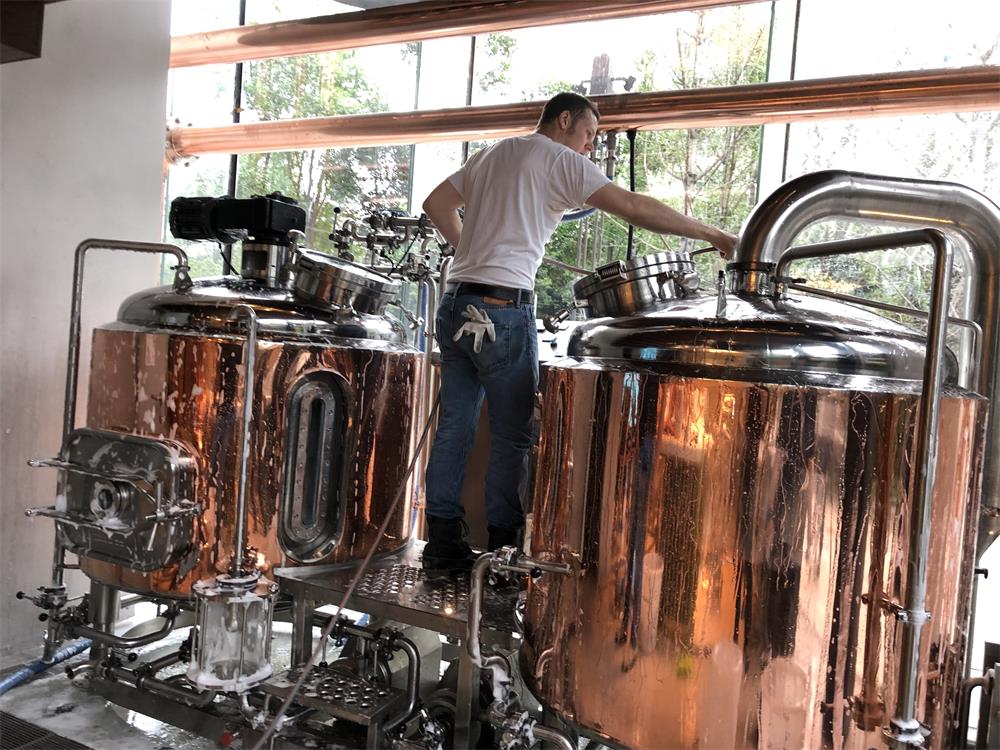
What are the types of 20 barrel brewing systems?
Brewing systems, irrespective of their size, come in various configurations and designs. For the 20 barrel brewing system, distinctions are primarily based on automation levels, material quality, and specific usage. Understanding these types will assist breweries in making informed decisions based on their unique needs.
- Manual Systems: These are the most basic systems, where most operations – from mashing to transferring – require manual intervention. They are typically the most affordable, but they might demand more manual labor and expertise.
- Semi-Automated Systems: Offering a balance between manual and fully automated operations, these systems have some processes that can be controlled automatically, usually through a central control panel.
- Fully Automated Systems: These are the most advanced systems with computerized controls for almost all processes, ensuring precise brewing parameters. They are the most expensive but can lead to significant savings in labor costs and efficiencies.
- Direct Fire vs. Steam Heated: The source of heat can vary. Direct fire systems use open flames, while steam-heated systems use steam generated by an external boiler.
- 2-Vessel, 3-Vessel, and 4-Vessel Systems: This classification is based on the number of vessels or tanks. A 2-vessel system might combine the mash tun and lauter tun, whereas a 4-vessel system would have separate vessels for mashing, lautering, boiling, and whirlpooling.
Type of System | Price Range (USD) |
---|---|
Manual | $50,000 – $80,000 |
Semi-Automated | $80,000 – $120,000 |
Fully Automated | $120,000 – $160,000 |
Direct Fire | $60,000 – $100,000 |
Steam Heated | $70,000 – $130,000 |
The choice of system will depend on a brewery’s budget, brewing philosophy, and production goals. For instance, craft breweries valuing traditional methods might prefer manual systems, while larger operations might lean towards automated systems for efficiency.
Functions of a 20 barrel brewing system
The 20 barrel brewing system serves a multitude of functions, catering to the entire beer production process from raw ingredients to the final packaged product. Understanding each function helps potential brewers appreciate the intricacies of brewing.
- Mashing: This is the first step where crushed grains are mixed with water in the mash tun. Here, starches are converted into fermentable sugars. Different temperature rests activate specific enzymes, impacting the beer’s flavor and body.
- Lautering: After mashing, the liquid is separated from the grain solids in a vessel called the lauter tun. This process extracts the sugary liquid, known as wort, which will be boiled and later fermented.
- Boiling: The wort is boiled in the kettle, typically for an hour. Hops are added at various stages, introducing bitterness, flavor, and aroma to the beer. Boiling also sterilizes the wort.
- Cooling: Post boiling, it’s crucial to cool the wort rapidly to a temperature suitable for yeast addition. This is done using heat exchangers that transfer heat from the wort to cold water or glycol.
- Fermentation: In the fermentation tanks, yeast is added to the cooled wort. The yeast consumes the sugars from the wort, producing alcohol and carbon dioxide. Depending on the beer type, this can last from a few days to several weeks.
- Conditioning: After fermentation, beer needs time to mature. During conditioning, flavors develop and unwanted compounds are precipitated out. This can happen in the fermentation tanks or separate conditioning tanks.
Each function is critical and demands precision. Making alterations at any stage can dramatically change the beer’s final flavor, appearance, and mouthfeel. Thus, understanding each function is pivotal for producing consistent, high-quality beer.
Applications of a 20 barrel brewing system
A 20 barrel brewing system, with its substantial yet not overwhelming capacity, finds applications in a variety of settings. The choice of such a system goes beyond just brewing; it speaks to the aspirations, scale, and ethos of the brewery. Here’s a detailed look at where and why these systems are employed:
- Craft Breweries: Craft beer has witnessed a surge in popularity, and a 20 barrel system is perfect for those looking to upscale from smaller setups. Such systems offer craft brewers the flexibility to experiment with batches, while also ensuring they meet the growing demand.
- Brewpubs and Taprooms: For establishments that brew their own beer on-site to serve directly to customers, a 20 barrel system offers an ideal scale. It allows them to maintain a diverse rotation of beers while ensuring freshness and consistency.
- Pilot Brewing: Even larger breweries might employ a 20 barrel system as a pilot setup. Before committing to large-scale production of a new recipe, breweries can use these systems for test batches, allowing for experimentation and refinement.
- Educational Institutions: Some universities and technical institutes offer brewing courses, using 20 barrel systems for hands-on training. Such systems offer students a realistic brewing experience, bridging the gap between theory and practice.
- Contract Brewing: Some breweries don’t brew their own beer but instead contract it out. In such scenarios, a 20 barrel system can be ideal for producing batches for multiple clients, especially those just entering the market or testing new recipes.
- Seasonal and Special Releases: A 20 barrel system is apt for brewing limited releases. Breweries can produce seasonal beers, festival specials, or commemorate specific events without disrupting their regular production schedules.
- Collaborative Brews: Collaborations between breweries have become popular, where two or more breweries come together to craft a unique beer. A 20 barrel system provides a platform for such joint efforts, producing batches that reflect the combined ethos of the collaborating entities.
- Event Brews: For significant events like beer festivals, competitions, or brewery anniversaries, a 20 barrel brewing system can be employed to produce one-off special brews that highlight the event’s significance.
With its adaptable capacity, the 20 barrel brewing system is not just a piece of equipment; it’s a versatile tool that breweries mold according to their vision and the demands of the ever-evolving beer landscape. Its applications underscore its importance in the modern brewing world, providing brewers with the means to craft, innovate, and celebrate the rich tapestry of beer culture.
How does a 20 barrel brewing system benefit you?
The beer brewing industry has grown exponentially over the past few years, and the demand for efficient and scalable brewing systems has risen in tandem. The 20 barrel brewing system, a favorite among many mid-sized breweries and brewpubs, offers a plethora of benefits to those who employ it.
- Scale of Production: First and foremost, the capacity of a 20 barrel system hits a sweet spot for many brewers. Producing around 620 gallons of beer per batch, it offers substantial output without veering into the realm of massive, industrial-sized operations.
- Cost-Efficiency: For breweries looking to upscale, investing in a 20 barrel system can result in significant cost savings in the long run. The cost per barrel often decreases with larger systems, meaning more profit margins for each beer sold.
- Flexibility in Brewing: This system allows brewers to experiment with new recipes without committing to vast quantities. It offers enough scale for popular staples while leaving room for limited runs or seasonal brews.
- Space Optimization: A 20 barrel system, while substantial, doesn’t demand the kind of space a larger industrial system might. It can be a good fit for establishments with space constraints, like brewpubs or urban breweries.
- Enhanced Consistency: Modern 20 barrel systems often come equipped with advanced controls that ensure consistency across batches. This is pivotal for maintaining brand reputation and ensuring customer satisfaction.
- Expansion Opportunities: For breweries experiencing growth, a 20 barrel system can serve as a stepping stone, bridging the gap between small-scale artisanal setups and large-scale production units.
- Community Engagement: Such systems allow breweries to engage better with their community. Be it through brewery tours, taproom sales, or hosting brewing workshops, a visible, mid-sized brewing operation can be a significant draw for beer enthusiasts.
Brewers need to align their choice of brewing system with their business model, growth aspirations, and the audience they aim to serve. A 20 barrel brewing system, with its blend of scale, efficiency, and flexibility, has proven to be a valuable asset for many in the industry.
How to choose a 20 barrel brewing system?
The decision to invest in a 20 barrel brewing system is significant, and making the right choice is paramount for long-term success. With multiple manufacturers, designs, and features available, the selection process can be daunting. Here’s a guide to help brewers navigate the myriad options:
- Determine Your Needs: Before diving into the specifics, breweries must evaluate their needs. Are you a small brewpub looking to satisfy local demand, or a growing brewery aiming for wider distribution? Your production goals, available space, and budget will significantly influence your choice.
- Material Quality: Opt for systems made of high-quality, food-grade stainless steel. This ensures longevity and maintains the purity of the beer. Some breweries also opt for systems with copper finishes for aesthetic reasons, though these might be pricier.
- Level of Automation: Brewing systems can range from fully manual to entirely automated. Your choice will depend on your brewing philosophy, budget, and staff expertise. Automated systems tend to be more consistent but are more expensive upfront.
- Vessel Configuration: As previously mentioned, systems can come as 2-vessel, 3-vessel, or 4-vessel configurations. Multiple vessels might offer more flexibility but can take up more space and be costlier.
- Heating Source: Decide between direct fire, electric, or steam heating. Each has its advantages and challenges. Direct fire might be cheaper but less efficient, while steam requires a separate boiler but offers even heating.
- Expandability and Customization: Can the system grow with your brewery? Some systems allow for additional tanks or components to be added later. Similarly, customization options can let you tailor the system to your specific needs.
- Manufacturer Reputation: Research potential manufacturers. Look for reviews, testimonials, and, if possible, visit breweries using their systems. Established manufacturers often provide better after-sales service and warranties.
Consideration | Options |
---|---|
Material | Stainless Steel, Copper |
Automation Level | Manual, Semi-Auto, Fully Auto |
Vessel Configuration | 2-Vessel, 3-Vessel, 4-Vessel |
Heating Source | Direct Fire, Electric, Steam |
Expandability | Yes, No |
Remember, the cheapest system isn’t necessarily the best. Factor in long-term costs, efficiency, and potential for growth. Also, consider the intangible aspects – does a particular system align with your brewery’s ethos and vision?
Best 10 20 barrel brewing system manufacturers
With the surge in craft brewing, numerous manufacturers have emerged to cater to the demand for brewing systems. For those considering a 20 barrel brewing system, selecting the right manufacturer can be as crucial as choosing the system itself. Here’s a list of ten esteemed manufacturers in the industry:
- YoLong Brewtech: YoLong Brewtech’s staff work together in our state-of-the-art 36,000 m2 / 3350 ft2 manufacturing plant in the Ningbo City Economic Development Zone, China.
- Ss Brewtech: With a commitment to innovation and quality, Ss Brewtech offers brewing systems that integrate advanced technology with user-friendly designs.
- BrauKon: Hailing from Germany, BrauKon is renowned for its precision engineering and efficient brewing solutions, catering to both small craft breweries and larger operations.
- JV Northwest: A veteran in the industry, JV Northwest has been crafting brewing systems for over three decades. Their systems are known for durability and efficiency.
- DME Brewing Solutions: With installations worldwide, DME offers a combination of quality, innovation, and experience, ensuring brewers get a system that meets their specific needs.
- Alpha Brewing Operations: From manual to fully automated, Alpha Brewing Operations provides a diverse range of systems, emphasizing customization and quality.
- Specific Mechanical Systems: With over 30 years in the industry, Specific Mechanical Systems has garnered a reputation for reliability, quality, and excellent customer service.
- Criveller Group: A global presence in brewing, winemaking, and distilling, Criveller offers top-notch brewing systems that are both efficient and visually appealing.
- Portland Kettle Works: Prioritizing craft brewers, Portland Kettle Works designs systems that are intuitive, efficient, and tailor-made for craft brewing needs.
- PsychoBrew: Known for their smaller systems, PsychoBrew has ventured into larger systems like the 20 barrel ones, maintaining their commitment to quality and innovation.
Manufacturer | Country of Origin | Years in Business |
---|---|---|
YoLong Brewtech | China | 20+ |
Ss Brewtech | USA | 10+ |
BrauKon | Germany | 15+ |
JV Northwest | USA | 30+ |
DME Brewing Solutions | Canada | 25+ |
Alpha Brewing Operations | USA | 10+ |
Specific Mechanical | Canada | 30+ |
Criveller Group | Italy/Canada | 40+ |
Portland Kettle Works | USA | 15+ |
PsychoBrew | USA | 10+ |
Selecting a manufacturer should be a blend of research, budget considerations, and personal preference. Engage with multiple manufacturers, visit their installations if possible, and gather feedback from fellow brewers. This will ensure you land a system that stands the test of time and aligns with your brewery’s aspirations.
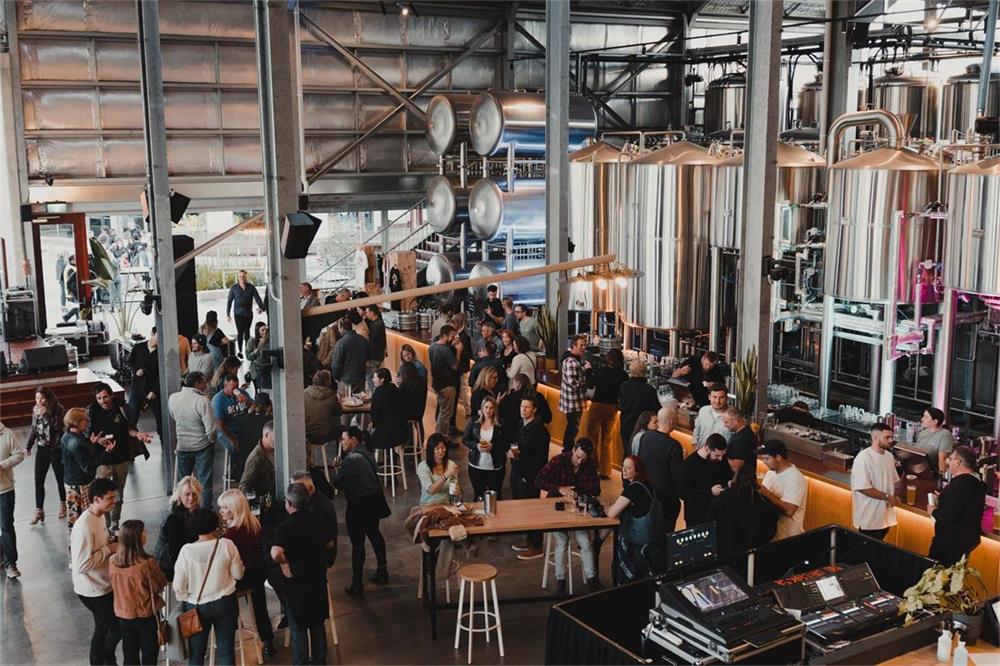
Where to buy a 20 barrel brewing system?
Purchasing a 20 barrel brewing system is a significant investment, and ensuring you source it from the right place is pivotal. Several factors can dictate where one should buy their brewing system:
- Direct from Manufacturers: One of the most direct ways is to purchase straight from manufacturers. This provides the advantage of potentially customizing the system to suit specific needs. Brands like Blichmann Engineering and BrauKon often sell directly to breweries.
- Distributors and Resellers: These are intermediaries who purchase brewing equipment from various manufacturers and resell them. They might offer additional services, like installation and maintenance, making the buying process smoother for some.
- Online Platforms: Websites like Alibaba, ProBrewer, and BreweryTrader serve as marketplaces where various manufacturers and sellers list their brewing systems. This provides an extensive range of options and often detailed customer reviews.
- Trade Shows and Expos: Attending industry trade shows like the Craft Brewers Conference provides an excellent opportunity to see systems firsthand, interact with manufacturers, and gather insights. It’s also an ideal place to negotiate deals.
- Used Equipment Dealers: For those on a tighter budget, buying a used 20 barrel brewing system might be a viable option. Companies like UsedBrewingEquipment.com specialize in sourcing and selling quality used brewery equipment.
- Local Craft Brewery Community: Networking within the local brewery community can sometimes lead to opportunities. Breweries upgrading their systems might sell their older 20 barrel systems at discounted prices.
While there are many avenues to explore, it’s crucial to ensure that the source is reputable. Always conduct thorough research, ask for references, and, if possible, inspect the system firsthand before finalizing a purchase.
Product Advantages of Chinese 20 barrel brewing systems
Chinese brewing equipment has been increasingly gaining traction in the global market. China’s fast-growing manufacturing sector offers various advantages that make their brewing systems an attractive option for many.
- Cost-Effective: One of the most significant benefits of Chinese brewing systems is their cost. Due to large-scale manufacturing capabilities and lower labor costs, Chinese manufacturers often provide competitive prices without compromising on quality.
- High-Quality Materials: Contrary to some misconceptions, many Chinese manufacturers, such as YoLong Brewtech, utilize high-grade stainless steel, ensuring durability and product purity.
- Customization: Companies like YoLong Brewtech pride themselves on their ability to tailor-make brewing systems to the customer’s exact specifications. Whether it’s vessel configuration, automation level, or aesthetic features, customization is often a standout feature.
- Innovation: China’s rapid industrial growth has been accompanied by advancements in technology. This innovation trickles down to brewing equipment, with many Chinese systems featuring the latest in brewing technology.
- Integrated Solutions: Chinese manufacturers often offer integrated solutions, encompassing not just the brewing system but also fermentation tanks, cooling systems, and bottling lines. This holistic approach can simplify the setup process for many breweries.
- Efficient Production Time: With expansive manufacturing facilities like YoLong Brewtech’s 36,000 m2 plant in Ningbo City Economic Development Zone, China, production times can be shorter, ensuring faster delivery.
- Global Shipping and Installation: Most major Chinese brewing equipment manufacturers have experience shipping globally. Many also provide installation services, ensuring the system is set up correctly and efficiently.
- Diverse Product Range: From beer to kombucha, cold-brewed coffee, and infused teas, companies like YoLong Brewtech have diversified their product range to cater to various beverage sectors, showcasing their versatility.
When considering Chinese brewing systems, it’s essential to engage with manufacturers directly, ask for testimonials, and, if possible, inspect the quality firsthand. This due diligence ensures you reap all the benefits that Chinese manufacturing offers.
Best Chinese 20 barrel brewing system supplier
China, with its vast manufacturing landscape, is home to numerous brewing system suppliers. However, one name that consistently stands out in terms of quality, innovation, and customer satisfaction is YoLong Brewtech.
- Established Reputation: Founded in 2004, YoLong Brewtech has over 15 years of experience in the brewing equipment manufacturing business. This deep-rooted expertise has set the benchmark for fabricating custom-designed and pre-made brewing equipment at unparalleled levels of quality and value.
- Comprehensive Product Range: Catering to diverse beverage sectors, from beer to kombucha and cold-brewed coffee, YoLong offers an extensive range of brewing systems. Their versatility is a testament to their commitment to the fast-evolving beverage industry.
- Customization at its Best: YoLong’s state-of-the-art 36,000 m2 manufacturing plant in Ningbo City Economic Development Zone ensures every custom-designed project aligns with the customer’s exact specifications. They possess the capability to meet virtually any specification a customer mandates.
- Dedicated Team: Behind YoLong’s success is its dedicated and experienced team. This team, working cohesively, has propelled the company to its esteemed status as an industry leader in the beverage sector.
- Global Presence: While YoLong is based in China, its influence and presence are undeniably global. They have catered to international demands with impeccable standards, solidifying their position in the worldwide market.
For those looking to invest in a 20 barrel brewing system or any brewing equipment, YoLong Brewtech emerges as a reliable, experienced, and top-tier supplier from China. Their commitment to quality and innovation ensures breweries get systems that stand the test of time and performance.
FAQ:
1. Why should I consider a 20 barrel brewing system?
A 20 barrel brewing system is ideal for medium-sized brewing operations, offering the perfect balance between production scale and manageability. It allows for a sizeable batch while not being overly cumbersome for smaller operations.
2. Are Chinese brewing systems of good quality?
Yes, many Chinese brewing system manufacturers, like YoLong Brewtech, provide high-quality equipment made from top-grade materials. Due diligence is essential to ensure you’re dealing with reputable suppliers.
3. What is the significance of customization in brewing systems?
Customization ensures that the brewing system meets the specific needs of the brewer, from tank configurations to automation levels, helping improve efficiency and product quality.
4. How do I determine the right brewing system size for my needs?
Consider factors like your projected production, space availability, and budget. Consulting with experienced brewers and manufacturers can also provide valuable insights.
5. Can I buy used brewing systems?
Yes, there are platforms and dealers specializing in used brewing equipment. However, ensure thorough inspection and understanding of the system’s history before purchase.
6. How important is post-sales support when purchasing brewing systems?
Extremely important. Brewing systems are intricate, and having access to manufacturer support for maintenance, parts replacement, and troubleshooting can be invaluable.
7. Are there financing options available for brewing systems?
Yes, many manufacturers and dealers offer financing options. Additionally, some financial institutions provide specialized loans or leases for brewing equipment.
Share this entry
Interested in learning more about Brewing Systems including additional details and pricing information? Please use the form below to contact us!
YOLONG BREWERY EQUIPMENT FAQS
- Commercial Brewery / Craft Brewery / Microbrewery / Nanobrewery
- What is The Difference Between Craft Beer and Industrial Beer?
- The Bespoke Differences In Custom Brewing Systems
- Everything You Need to Know About Kettle Souring
- How to Choose Brewing Equipment for Your business?
- How To Choose The-Best Partner To Build Your Commercial Microbrewing System?
- Two Detection Sensors That You Need To Use In Your Brewhouse System
- Remote Control Applications in Brewing Equipment/How does it work?
- How To Clean Your Brand New Brewery Tanks?