Table of Contents
ToggleOverview of the 30 Barrel Brewing System
When it comes to commercial brewing, the 30 Barrel Brewing System is a standout choice for businesses looking to scale their operations without sacrificing quality. This system strikes the perfect balance between production efficiency, scalability, and batch consistency, making it a cornerstone for craft breweries that aim to meet growing consumer demand. But what exactly is a 30 Barrel Brewing System, and why has it become so popular in the brewing industry? Let’s dive in and explore!
What is the 30 Barrel Brewing System?
A 30 Barrel Brewing System is a commercial brewing setup designed to produce batches of beer equivalent to 30 barrels per run. For perspective, one barrel equals 31 gallons, meaning a 30-barrel system can produce 930 gallons of beer per batch. That’s a lot of pints! This scale of production is perfect for medium-sized breweries or craft brewers transitioning to larger markets.
These systems typically include essential components such as mash tuns, lauter tuns, brew kettles, fermenters, and conditioning tanks, all designed to handle the larger volume seamlessly. Thanks to advanced engineering and state-of-the-art materials, these systems ensure precision, efficiency, and high-quality output.
Why is it Called a 30 Barrel Brewing System?
The name “30 Barrel” refers to the system’s capacity to produce 30 barrels of beer in one brewing cycle. It’s a benchmark used in the brewing industry to denote production scale, making it easier for manufacturers and brewers to match equipment to production goals.
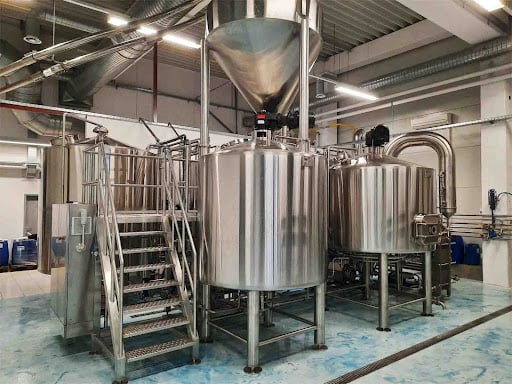
The Advantages of the 30 Barrel Brewing System
The 30 Barrel Brewing System isn’t just about volume; it’s about producing exceptional beer efficiently. Here are some key advantages that make it a go-to choice for craft breweries:
Production Efficiency
Brewing beer at this scale allows for streamlined production processes. With a 30 Barrel Brewing System, you can produce large quantities of beer in a single batch, reducing the time and labor required compared to brewing smaller batches repeatedly. This efficiency translates to lower operational costs and higher profit margins.
Scalability
One of the standout features of the 30 Barrel system is its scalability. It’s ideal for breweries experiencing growth, as it provides the capacity to meet increased demand without the need for multiple smaller systems. Think of it as future-proofing your brewery.
Batch Consistency
Maintaining consistency is crucial for brand reputation. These systems are designed with precise controls for temperature, timing, and ingredient integration, ensuring that every batch tastes exactly as intended. Your customers will appreciate the reliable quality, and you’ll build trust in your brand.
Cost-Effectiveness
While the initial investment may seem significant, the long-term savings are undeniable. Larger batches reduce the cost per gallon of beer produced, and the durability of these systems minimizes maintenance and replacement costs over time.
Technical Specifications and Design Features of 30 Barrel Brewing System
The technical prowess of the 30 Barrel Brewing System sets it apart from smaller setups. Let’s delve into the specifications that make this equipment a brewer’s dream.
Core Components
- Mash Tun: Engineered for optimal conversion of starches into fermentable sugars.
- Lauter Tun: Designed for efficient wort separation, reducing brewing time.
- Brew Kettle: Provides consistent boiling and flavor extraction.
- Fermenters: High-capacity fermenters equipped with precise temperature controls.
- Conditioning Tanks: Ensure beer achieves the desired clarity, carbonation, and taste.
Material Quality
Most systems are constructed from food-grade stainless steel, ensuring durability, easy cleaning, and resistance to corrosion. Advanced insulation layers maintain temperature stability, which is crucial for brewing precision.
Automation Features
Modern 30 Barrel Brewing Systems often include automated controls, allowing brewers to monitor and adjust brewing parameters through digital interfaces. From temperature regulation to ingredient timing, automation ensures precision and reduces the risk of errors.
Energy Efficiency
These systems are designed with energy-saving features, such as heat exchangers and insulated tanks, to minimize power consumption and reduce environmental impact.
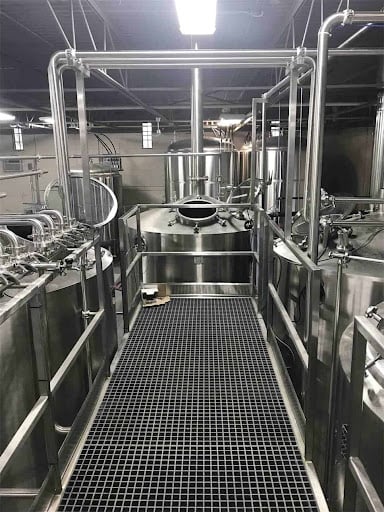
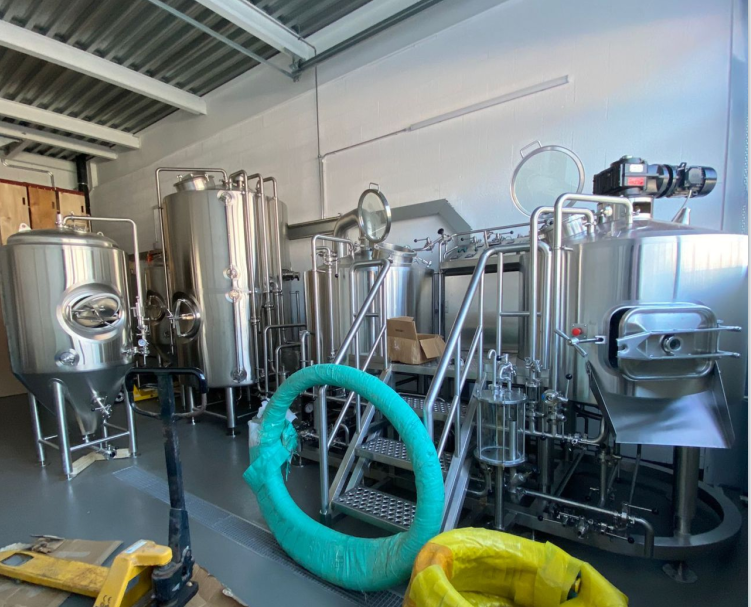
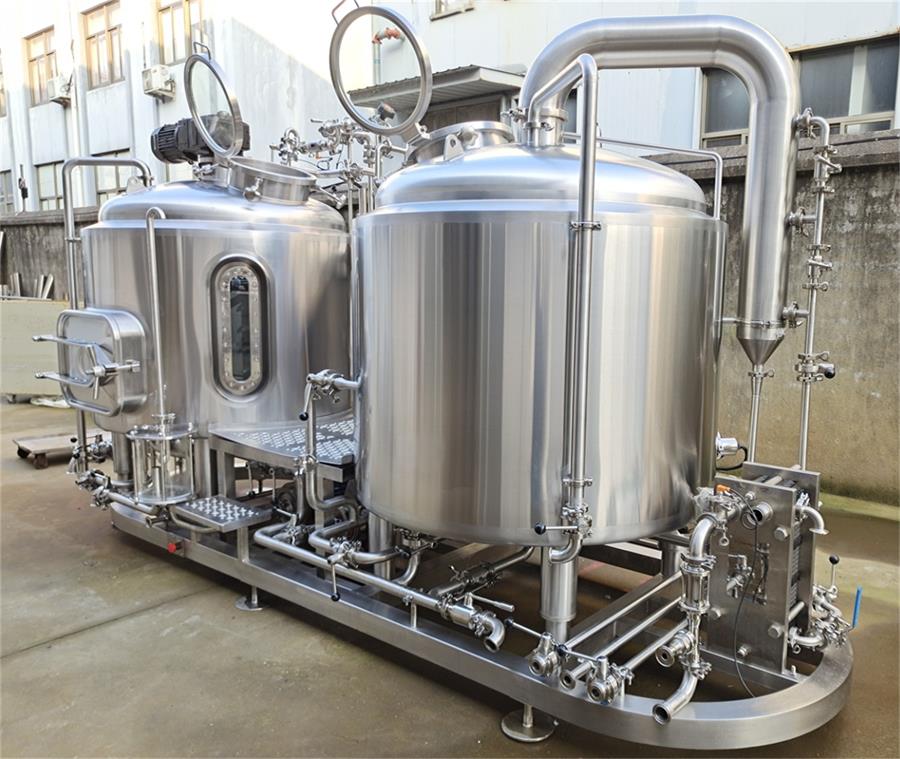
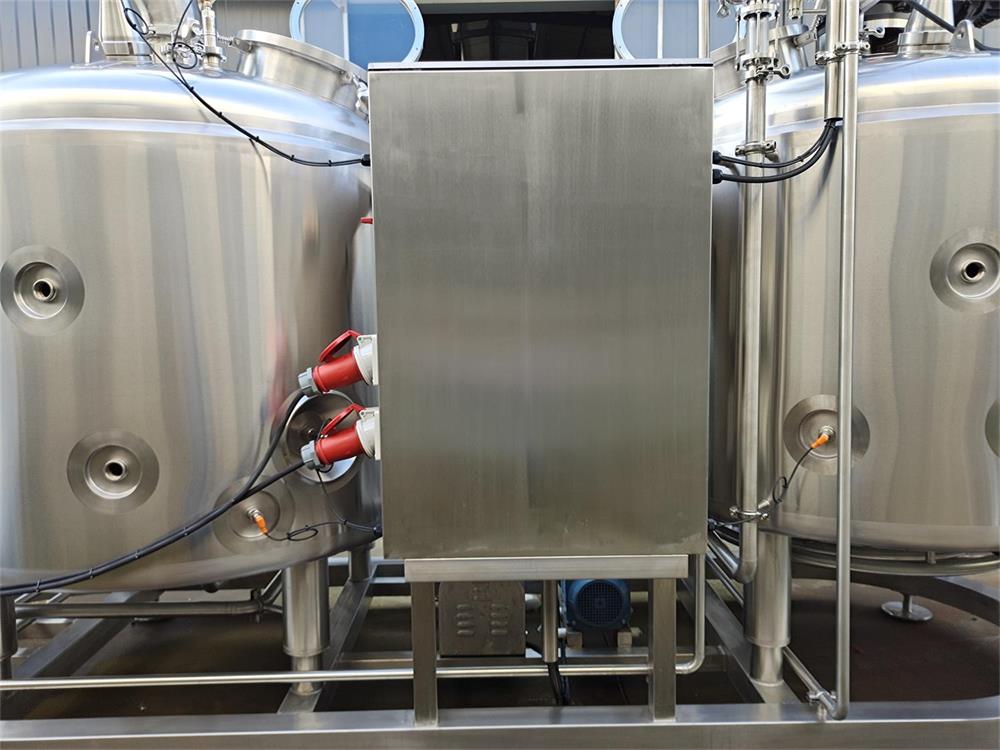
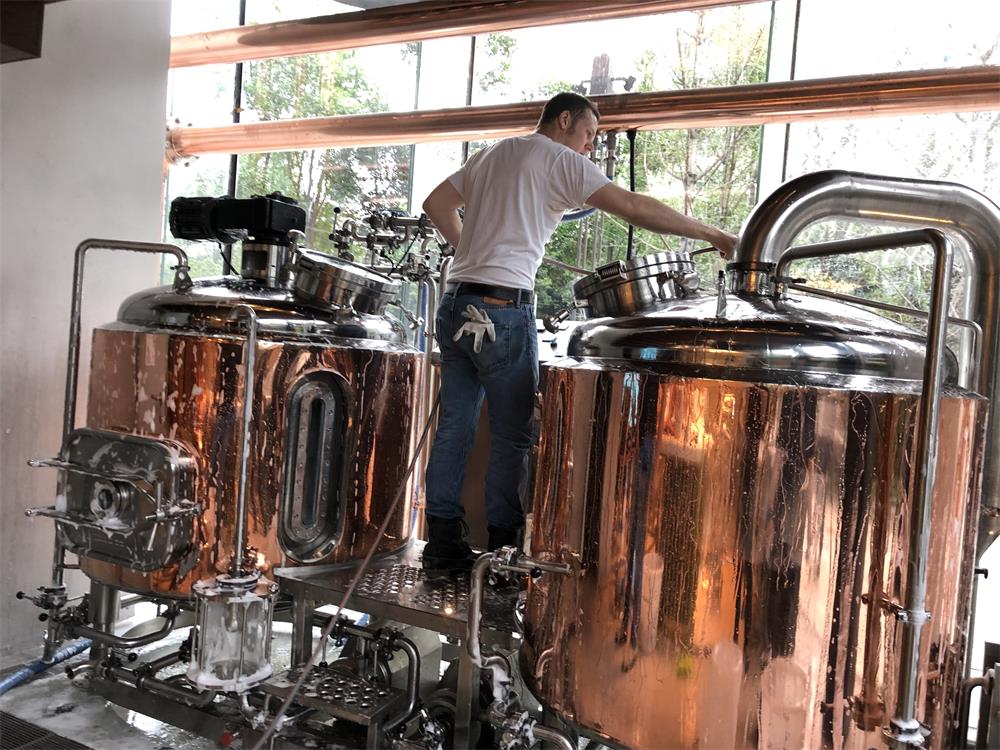
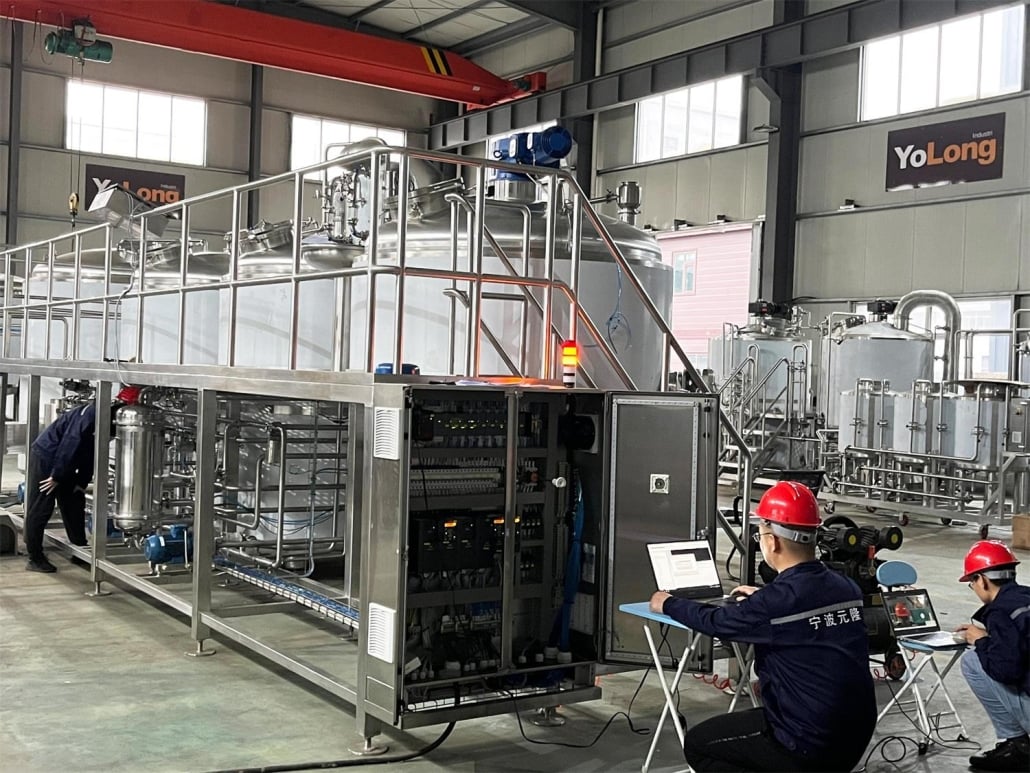
Applicable Scenarios for the 30 Barrel Brewing System
Scenario | Details |
---|---|
Expanding Craft Breweries | Ideal for breweries looking to scale operations to meet rising demand. |
Brewpubs | Supports production of a wide variety of beers on-site for patrons. |
Regional Distribution | Enables breweries to supply beer to a broader geographic area. |
Specialty Beer Production | Suitable for producing seasonal or specialty beers in larger quantities. |
Cost Effectiveness and Long-Term Benefits of the 30 Barrel Brewing System
Factor | Details |
---|---|
Lower Cost Per Batch | Larger batches reduce ingredient and labor costs per gallon. |
Durability | High-quality materials ensure longevity, reducing replacement expenses. |
Energy Savings | Efficient designs lower utility costs over time. |
Revenue Potential | Increased production capacity enables higher sales volumes. |
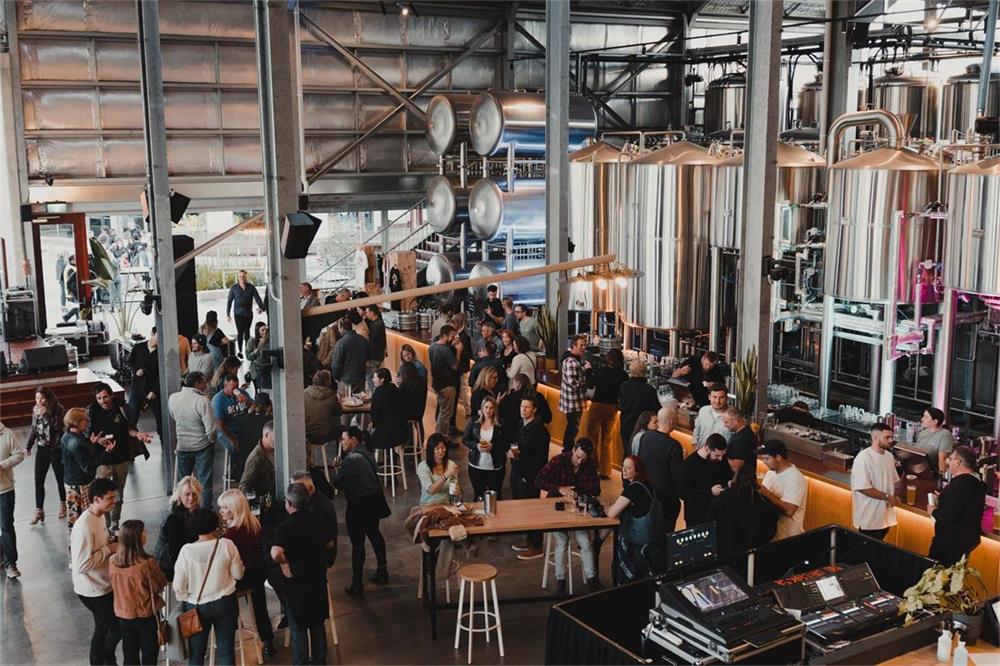
Recommendations for Selecting High-Quality 30 Barrel Brewing Systems
Criteria | Details |
---|---|
Brand Reputation | Research trusted manufacturers with proven track records. |
Customizability | Look for systems that can be tailored to your specific brewing needs. |
After-Sales Service | Choose suppliers offering robust maintenance and support services. |
Warranty | Ensure a comprehensive warranty covers major components. |
User Reviews | Read reviews from other breweries to gauge satisfaction and reliability. |
FAQ
Question | Answer |
---|---|
What size brewery is a 30 Barrel system suitable for? | Perfect for medium-sized breweries and those looking to scale operations. |
How much does a 30 Barrel Brewing System cost? | Prices typically range from $150,000 to $500,000 depending on features. |
What maintenance is required? | Regular cleaning, inspection of seals, and software updates if applicable. |
Can it produce different types of beer? | Yes, it’s versatile enough for various beer styles and recipes. |
How long does it take to brew a batch? | Typically 8-12 hours, depending on the recipe and brewing process. |