When it comes to brewing exceptional beer, the role of commercial brewing tanks is often understated but absolutely critical. These tanks form the heart of any brewery operation, playing a pivotal role in the fermentation, conditioning, and maturation of the final product. In this comprehensive guide, we delve into the world of commercial brewing tanks, exploring their types, importance, customization, maintenance, and more.
Table of Contents
ToggleThe Importance of Commercial Brewing Tanks
Brewing tanks are where the magic happens. They are more than just vessels; they are the environments where yeast transforms wort into flavorful beer. The quality of these tanks directly impacts the quality of the final product. From achieving the right level of carbonation to ensuring the desired flavor profiles, brewing tanks are the canvas on which brewers create their masterpieces.
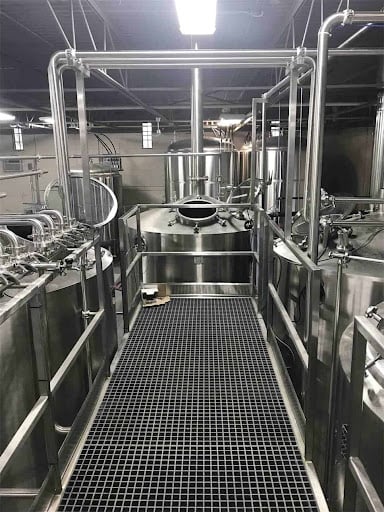
Types of Commercial Brewing Tanks
Fermentation Tanks
Fermentation tanks are where the primary fermentation takes place. Yeast converts sugars into alcohol, and the tank’s design greatly influences yeast activity. These tanks come in various sizes and shapes, each impacting the beer’s outcome differently.
Bright Tanks
Bright tanks are the bridge between fermentation and packaging. They allow further maturation and carbonation while ensuring clarity. A crucial element in achieving a well-balanced beer.
Conditioning Tanks
Conditioning tanks are for secondary conditioning or aging. They are used for lagers, ales, and specialty brews. These tanks provide the time and controlled environment necessary for the beer to reach its optimal flavor.
Mash Tuns and Brew Kettles
Mash tuns and brew kettles are essential for mashing, boiling, and lautering processes. These vessels contribute to the beer’s flavor and mouthfeel by influencing the extraction of sugars, hops, and other compounds.
Factors to Consider When Choosing Commercial Brewing Tanks
Tank Size and Capacity
Selecting the right tank size is crucial. Oversized tanks can lead to stale beer, while undersized tanks may hamper production. Consider both current and future needs.
Material and Construction
Tank material impacts the flavor, quality, and longevity of your beer. Stainless steel is a popular choice due to its durability, hygiene, and resistance to corrosion.
Cooling and Insulation
Temperature control is vital for consistent brewing. Tanks with efficient cooling systems and insulation ensure precise temperature management throughout the brewing process.
Pressure and Safety Features
Pressure-rated tanks are essential for carbonation and proper sealing during fermentation. Incorporating safety features reduces the risk of accidents and ensures a secure working environment.
Proper Maintenance of Commercial Brewing Tanks
Cleaning and Sanitization
Maintaining clean and sanitized tanks prevents contamination and off-flavors. Regular cleaning routines are vital for producing consistent, high-quality beer.
Regular Inspections
Frequent inspections catch issues early, preventing costly downtimes. Check for leaks, wear and tear, and any signs of compromised structural integrity.
Repairs and Upkeep
Promptly addressing repairs and maintenance keeps your brewery running smoothly. Neglecting issues can lead to more significant problems down the line.
Customization and Innovation in Brewing Tanks
Breweries are unique, and so are their brewing processes. Customized tanks can optimize efficiency, accommodate special ingredients, and cater to distinct brewing styles.
The Future of Commercial Brewing Tanks
Advancements in technology and sustainability are shaping the future of brewing tanks. From energy-efficient designs to IoT integration, brewing tanks are evolving to meet the demands of modern brewers.
Sustainability in Brewing Tank Design
Breweries are increasingly prioritizing eco-friendly practices. Sustainable tank designs reduce water and energy consumption, aligning with environmentally conscious brewing.
Ensuring Quality and Consistency in Brewing
Consistency is key to building a loyal customer base. Well-maintained and precisely controlled brewing tanks contribute to consistent flavor profiles and quality.
Tips for Investing in Commercial Brewing Tanks
Research extensively before investing. Consider the brewery’s current and projected production volumes, as well as the potential for expansion.
Cost Analysis and Budgeting
Balancing quality and budget is crucial. Remember that investing in high-quality tanks upfront can lead to long-term savings through reduced maintenance and enhanced product quality.
Case Studies: Successful Breweries and Their Tank Choices
Examining the tank choices of successful breweries provides valuable insights into how tank selection can impact growth, product quality, and customer satisfaction.
Expert Interviews: Master Brewers on Tank Selection
Learn from industry experts who have honed their craft over years of brewing. Their insights can help you make informed decisions about tank selection.
Common Myths about Commercial Brewing Tanks
Myth 1: One-Size-Fits-All Tanks
Different beers have different requirements. Tailoring your tank selection to your beer styles enhances the final product.
Myth 2: Newer Breweries Don’t Need High-End Tanks
Investing in quality tanks from the start sets the foundation for consistent growth and premium beer production.
Myth 3: Tank Maintenance Isn’t That Important
Regular maintenance is the backbone of brewery operations. Neglecting maintenance jeopardizes product quality and business success.
Conclusion
Commercial brewing tanks are more than vessels; they’re the architects of exceptional beer. From fermentation to packaging, these tanks shape the beer’s journey. By understanding their significance, choosing wisely, and maintaining diligently, brewers can craft the perfect brew every time.