Table of Contents
ToggleOverview of Commercial Brewing Systems
Commercial brewing systems are specialized equipment setups designed to produce beer on a large scale. They cater to breweries of all sizes, from microbreweries to large-scale production facilities. These systems integrate advanced technology with traditional brewing methods to ensure efficiency, consistency, and scalability. Here’s what makes them essential:
- Capacity: Designed to handle large volumes, ranging from a few barrels to thousands of gallons.
- Precision: Equipped with automated controls for temperature, pressure, and timing to produce consistent batches.
- Customization: Adaptable to different brewing styles and recipes.
- Durability: Made from high-quality materials like stainless steel to withstand rigorous use.
By leveraging a commercial brewing system, breweries can streamline their operations, reduce waste, and maintain high-quality standards. Let’s delve deeper into the components, processes, and considerations involved.
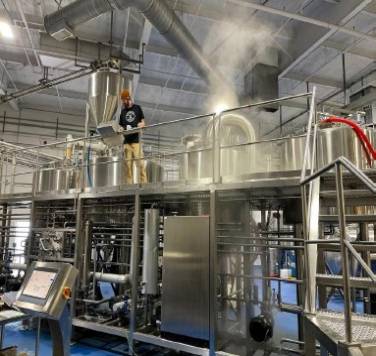
The Brewing Process in Commercial Systems
Understanding how beer is made is key to appreciating the role of a commercial brewing system. Here’s a step-by-step breakdown of the brewing process:
1. Milling
Milling involves crushing malted grains to expose their starches. These starches will later be converted into fermentable sugars. Commercial systems often include an automated mill that ensures consistent grain size for optimal extraction.
2. Mashing
In this stage, the milled grains are mixed with hot water in a mash tun. The heat activates enzymes that convert the starches into sugars. Modern systems use precise temperature controls to ensure the right enzymatic activity for specific beer styles.
3. Lautering
After mashing, the mixture is transferred to a lauter tun, where the liquid wort is separated from the spent grains. Commercial systems often feature advanced lautering mechanisms to maximize wort extraction and minimize losses.
4. Boiling
The wort is then boiled in a kettle, where hops are added for bitterness, flavor, and aroma. Automated systems allow brewers to schedule hop additions at precise intervals.
5. Fermentation
The boiled wort is cooled and transferred to fermenters, where yeast is added. Yeast converts the sugars into alcohol and carbon dioxide. Fermenters in commercial systems often include features like temperature controls, pressure gauges, and sampling ports.
6. Conditioning
During this stage, the beer matures, allowing flavors to develop and impurities to settle. Some systems include bright tanks for final conditioning and carbonation.
7. Packaging
Finally, the beer is filtered, pasteurized (if necessary), and packaged into kegs, cans, or bottles for distribution. Commercial setups often integrate automated packaging lines to streamline this process.
Troubleshooting Common Issues with Beer Fermenters
Fermenters are critical in the brewing process, but they’re not without challenges. Here are some common issues and how to address them:
1. Temperature Fluctuations
- Issue: Inconsistent fermentation temperatures can lead to off-flavors.
- Solution: Use fermenters with precise temperature controls. Regularly calibrate sensors and maintain glycol systems.
2. Contamination
- Issue: Bacterial or wild yeast contamination can spoil the beer.
- Solution: Maintain strict sanitation protocols. Clean fermenters thoroughly after each batch using CIP (Clean-In-Place) systems.
3. Pressure Build-Up
- Issue: Excessive pressure can damage fermenters or affect yeast activity.
- Solution: Use fermenters with built-in pressure relief valves and monitor pressure levels regularly.
4. Poor Yeast Health
- Issue: Stressed or unhealthy yeast may result in incomplete fermentation.
- Solution: Pitch the right amount of healthy yeast and monitor fermentation progress using hydrometers or refractometers.
Key Parameters of Commercial Brewing Systems
To help you choose the right system, here’s a detailed comparison of key parameters:
Parameter | Details |
---|---|
Capacity | Systems range from 5-barrel setups for microbreweries to 100+ barrels for large-scale production. |
Space Requirements | Compact systems are ideal for small spaces, while larger setups require dedicated facilities. |
Design & Layout | Modular designs offer flexibility; integrated systems maximize efficiency. |
Customization | Options for additional tanks, automated controls, and recipe-specific configurations. |
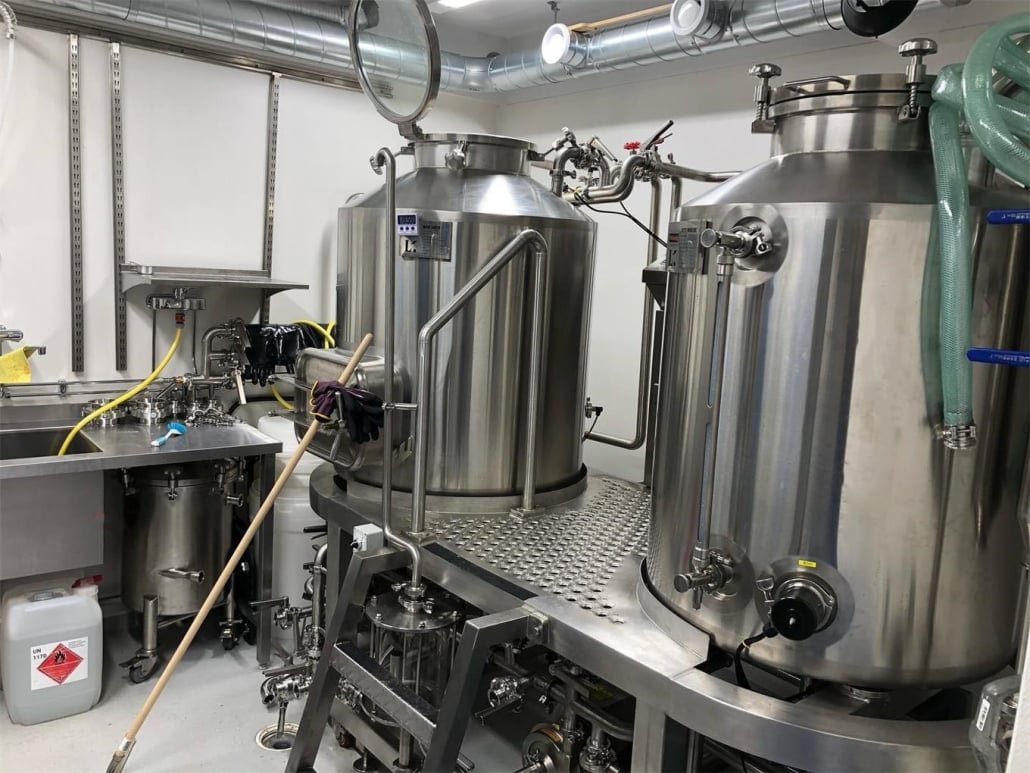
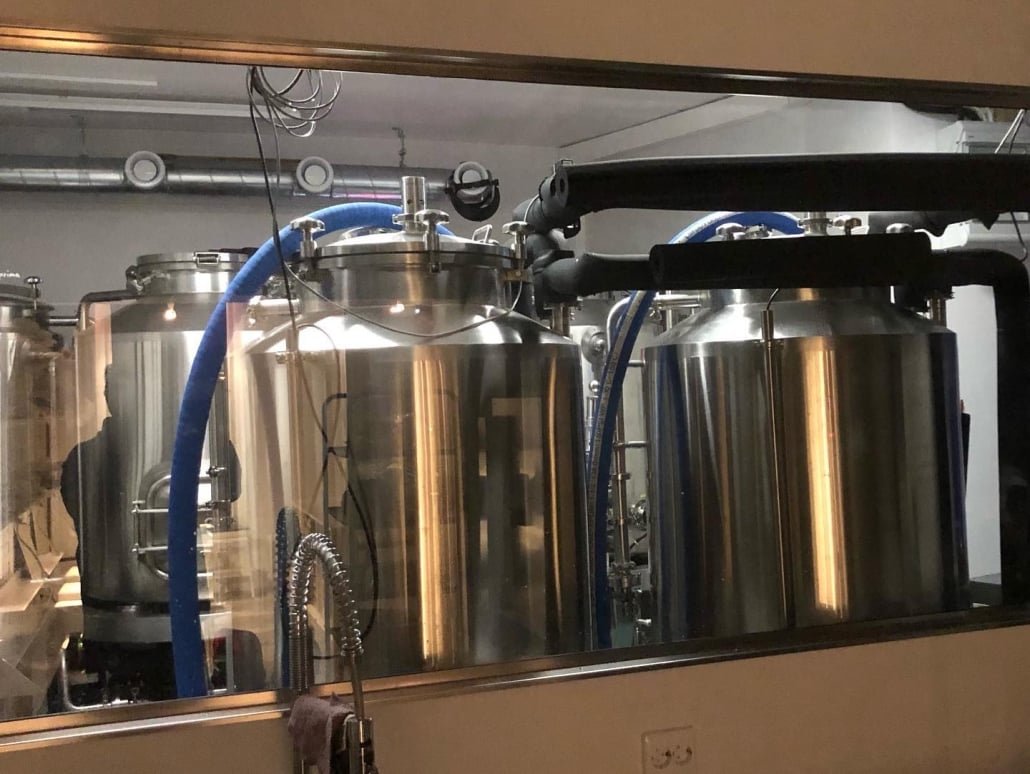
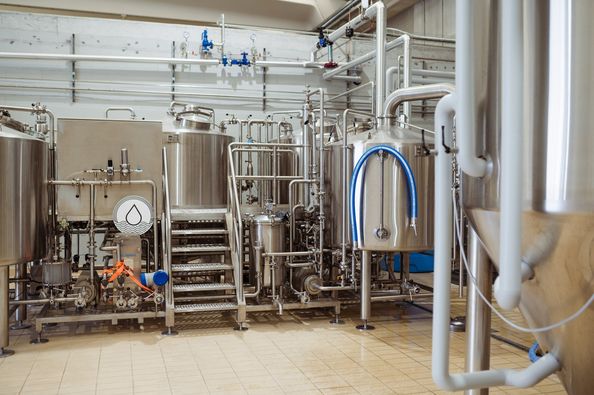
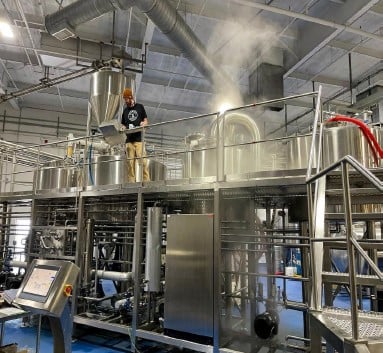
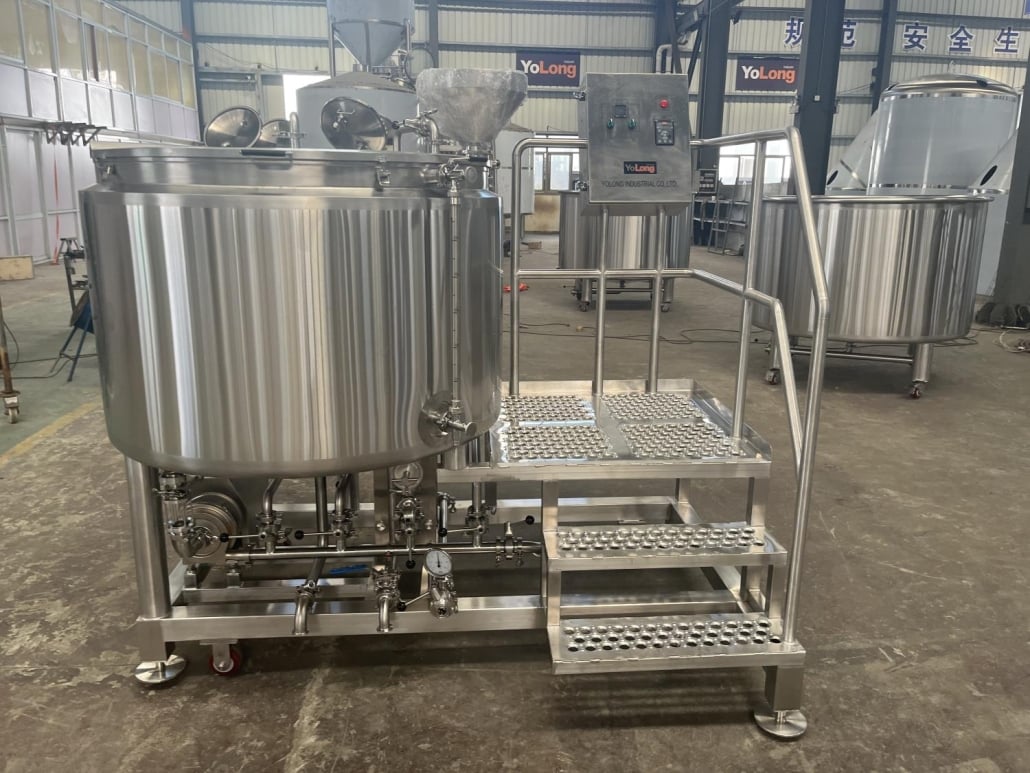
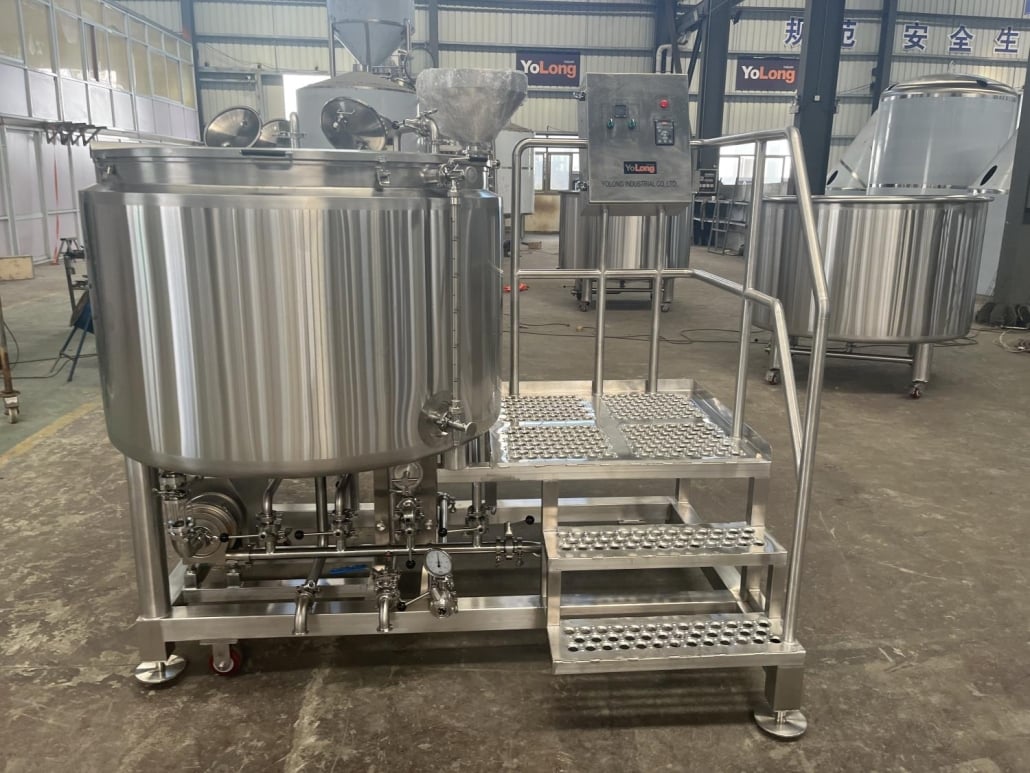
Suppliers and Price Range
Choosing the right supplier is crucial for your brewery’s success. Here’s a comparison of suppliers and their price ranges:
Supplier | Price Range | Special Features |
ABC Brewing Co. | $50,000 – $200,000 | Modular designs, automated controls, custom configurations. |
BrewTech Systems | $75,000 – $300,000 | Advanced automation, energy-efficient designs. |
CraftMaster Brewing | $100,000 – $500,000 | Turnkey solutions, high-capacity setups. |
ProBrew Equipment | $120,000 – $600,000 | Comprehensive support, integrated packaging lines. |
Installation, Operation, and Maintenance
Proper installation, operation, and maintenance are key to maximizing the lifespan and efficiency of your brewing system. Here’s a breakdown:
Aspect | Details |
Installation | Requires professional setup to ensure proper alignment, wiring, and calibration. |
Operation | User-friendly interfaces and training from suppliers simplify daily operations. |
Maintenance | Regular cleaning, part replacements, and software updates prevent downtime. |
How to Choose the Right Supplier
Selecting a supplier is one of the most critical decisions for your brewery. Here are factors to consider:
Factor | Details |
Reputation | Check reviews, testimonials, and case studies from other breweries. |
Support Services | Ensure the supplier offers installation, training, and after-sales support. |
Customization | Look for flexibility to tailor the system to your brewery’s needs. |
Budget | Compare pricing while considering long-term value and operational efficiency. |
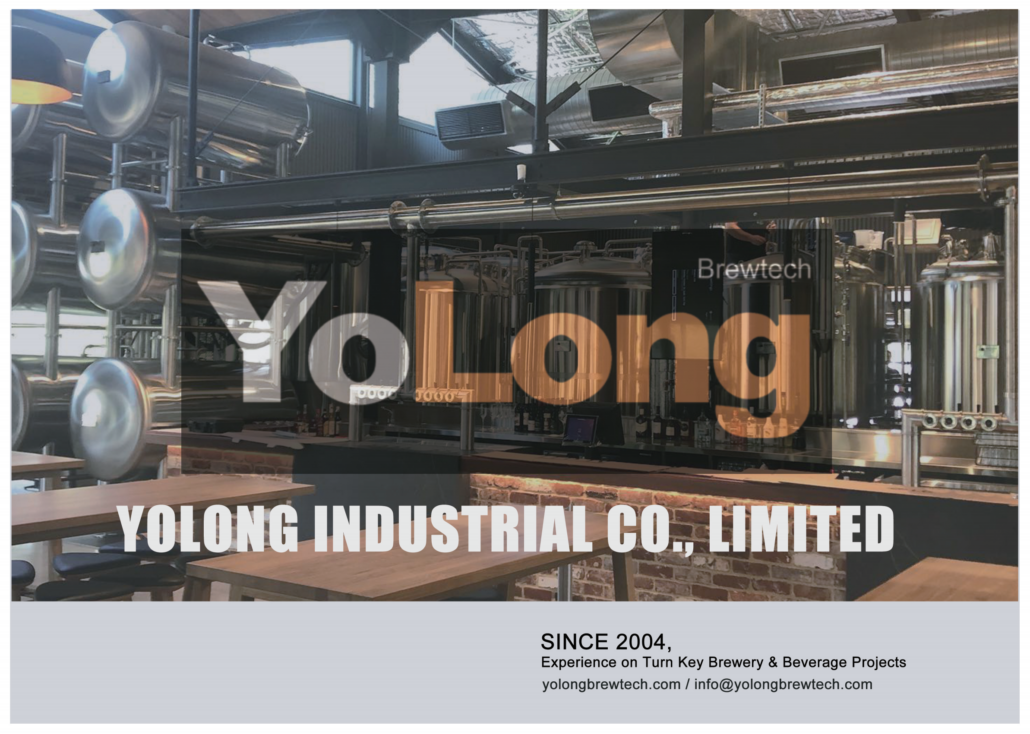
Advantages and Limitations of Commercial Brewing Systems
Aspect | Advantages | Limitations |
Scalability | Enables production growth to meet demand. | High initial investment cost. |
Automation | Reduces manual labor and ensures consistency. | Requires technical expertise for troubleshooting. |
Quality Control | Advanced systems maintain precise brewing conditions. | Complex systems may increase maintenance demands. |
Customization | Tailored setups support diverse beer styles and recipes. | Lead times for custom systems can be long. |
FAQ
Question | Answer |
What is a commercial brewing system? | A setup of equipment designed for large-scale beer production, integrating modern and traditional methods. |
How much does a brewing system cost? | Costs vary widely, ranging from $50,000 to over $600,000 depending on capacity and features. |
How do I maintain a brewing system? | Regular cleaning, routine inspections, and timely part replacements are essential. |
What capacity should I choose? | Choose based on your production goals, starting with a smaller system for new breweries. |
Are commercial systems energy-efficient? | Many modern systems feature energy-saving designs to reduce operational costs. |
This guide offers a comprehensive overview of commercial brewing systems, combining technical insights with practical advice. Whether you’re starting a new brewery or upgrading your equipment, understanding these systems is key to success in the brewing industry.