Table of Contents
ToggleIntroduction
Craft beer has gained immense popularity in recent years, leading to an increased demand for quality brewing equipment. Among the various brewing systems available, the 5bbl brewing system has emerged as a popular choice for small to medium-sized breweries. In this article, we will explore the features, benefits, considerations, and best practices associated with a 5bbl brewing system.
What is a 5bbl Brewing System?
A 5bbl brewing system refers to a brewing setup with a total capacity of 5 barrels, where each barrel holds 31 gallons or approximately 117 liters of liquid. This system allows breweries to produce a significant volume of beer, making it suitable for brewpubs, microbreweries, and regional craft beer producers. The 5bbl brewing system consists of several key components that work together to facilitate the brewing process.
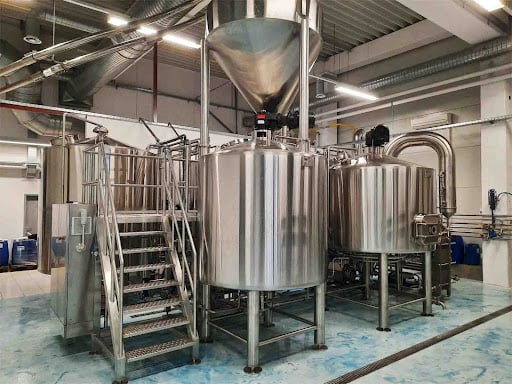
Components of a 5bbl Brewing System
Mash Tun
The mash tun is an essential component of the brewing system where mashing, the process of converting starches into fermentable sugars, takes place. It is equipped with a heating element and a false bottom or manifold system to extract the sweet wort from the grain bed.
Brew Kettle
The brew kettle is where the wort is boiled and hops are added to impart bitterness, flavor, and aroma to the beer. It is equipped with heating elements, temperature controls, and features like whirlpool ports for efficient trub separation.
Fermentation Vessels
Fermentation vessels are where the wort is fermented by yeast, converting sugars into alcohol and producing carbon dioxide. A 5bbl brewing system typically includes multiple fermentation vessels such as fermenters and bright tanks, allowing brewers to simultaneously produce and store different beer styles.
Cooling System
A cooling system is crucial to maintain optimal fermentation temperatures. It typically includes glycol chillers, insulated pipes, and heat exchangers to control the temperature of the fermenting beer and maintain the desired flavors and aromas.
Control Panel
The control panel is the central hub that regulates various aspects of the brewing process, including temperature, pressure, and flow rates. It provides brewers with precise control over the system, ensuring consistency and repeatability in their beer production.
Benefits of a 5bbl Brewing System
Scalability
A 5bbl brewing system offers scalability, allowing breweries to increase their production volume as their business grows. It provides the flexibility to meet the rising demand for craft beer without requiring a complete overhaul of the brewing equipment.
Efficiency
With a 5bbl brewing system, brewers can achieve higher efficiency in their operations. The larger brewing capacity reduces the number of brew cycles required to meet production targets, saving time and resources.
Consistency
Consistency is crucial in the brewing industry, and a 5bbl system enables brewers to maintain consistent quality across batches. The precise control over the brewing process and the use of standardized equipment contribute to consistent flavors, aromas, and overall beer characteristics.
Quality Control
A 5bbl brewing system allows brewers to have better control over the brewing parameters, resulting in improved quality control. With tighter control over temperature, flow rates, and other critical variables, brewers can create beer with desired characteristics, reducing the likelihood of off-flavors or inconsistencies.

Factors to Consider When Choosing a 5bbl Brewing System
When selecting a 5bbl brewing system, brewers should consider several factors to ensure it aligns with their specific needs and requirements.
Space and Location
Before investing in a 5bbl brewing system, it’s important to evaluate the available space and location. The system should fit comfortably in the designated area, allowing for smooth operations and future expansions if needed.
Budget
Budget plays a significant role in choosing a brewing system. Brewers must consider the initial investment cost, as well as ongoing expenses for maintenance, utilities, and raw materials.
Brewing Capacity
The desired brewing capacity should be considered based on current demand and projected growth. While a 5bbl system offers a substantial volume, it’s essential to assess if it aligns with the target market and production goals.
Equipment Quality
Investing in high-quality brewing equipment ensures durability, reliability, and optimal performance. Brewers should research reputable manufacturers and consider factors such as material quality, craftsmanship, and warranty.
Customization Options
Some brewers may have specific requirements or preferences for their brewing system. Considering customization options such as additional features, control panel upgrades, or specific vessel designs can contribute to a better brewing experience.
Setting Up a 5bbl Brewing System
Setting up a 5bbl brewing system requires careful planning and execution to ensure a smooth start to production.
Space Preparation
Before installing the brewing equipment, the designated space needs to be prepared. This includes ensuring proper flooring, utilities such as water, drainage, and electrical connections, and adequate ventilation.
Installation of Brewing Equipment
The installation process involves placing and connecting the various components of the brewing system, including the mash tun, brew kettle, fermentation vessels, cooling system, and control panel. Following the manufacturer’s guidelines and seeking professional assistance, if required, can help ensure a successful installation.
Testing and Calibration
After installation, it’s essential to thoroughly test and calibrate the brewing system to ensure its proper functioning. This includes checking for any leaks, verifying temperature control, calibrating instruments, and conducting test runs to familiarize oneself with the system’s operation.
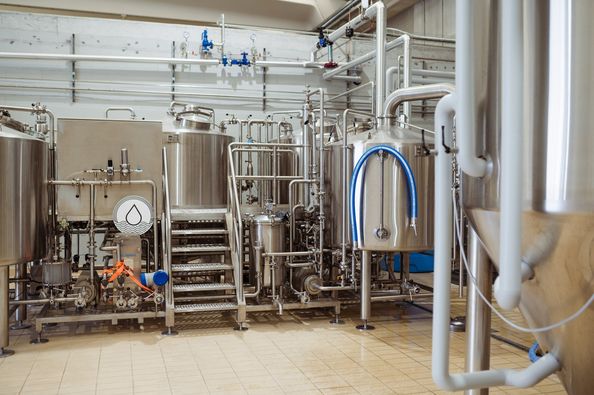
Maintenance and Cleaning
To ensure the longevity and consistent performance of a 5bbl brewing system, regular maintenance and cleaning are necessary.
Regular Maintenance
Regular maintenance tasks include inspecting and cleaning brewing vessels, checking and replacing worn-out gaskets or seals, lubricating moving parts, and performing routine equipment checks. Adhering to a maintenance schedule helps identify and address any issues before they escalate and ensures the system operates at its best.
Cleaning Procedures
Proper cleaning is crucial to prevent contamination and maintain the quality of the beer. Cleaning procedures typically involve the use of brewery-specific cleaning agents, thorough rinsing, and sanitization of all brewing equipment. Following established cleaning protocols and maintaining cleanliness standards significantly contributes to producing high-quality beer.
Common Challenges with 5bbl Brewing Systems
While a 5bbl brewing system offers numerous advantages, there are some common challenges that brewers may encounter.
Wort Loss
During the brewing process, wort loss can occur due to various factors such as equipment design, dead space, or inefficient transfer of liquid. Brewers must be mindful of wort loss and implement strategies to minimize it, such as optimizing equipment layout, improving transfer methods, or adjusting recipe formulations.
Temperature Control
Maintaining precise temperature control throughout the brewing process is essential for producing consistent and high-quality beer. However, fluctuations in ambient temperature or inadequate insulation can pose challenges. Brewers should invest in temperature control solutions like glycol chillers or jacketed vessels to overcome these issues.
Oxygen Exposure
Oxygen exposure can lead to off-flavors and oxidation in beer, negatively impacting its quality and shelf life. Proper handling and transfer techniques, as well as the use of closed systems and inert gases, can help minimize oxygen exposure during various stages of the brewing process.
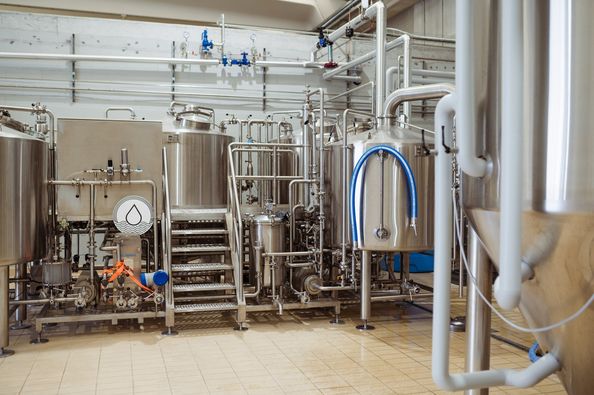
Best Practices for Operating a 5bbl Brewing System
To optimize the operation of a 5bbl brewing system and produce exceptional beer, brewers should follow certain best practices.
Recipe Development
Investing time and effort in recipe development is crucial for creating unique and flavorful beers. Brewers should experiment with different ingredients, yeast strains, and brewing techniques to refine their recipes and create a diverse lineup of beers.
Water Treatment
Water quality significantly impacts the taste and overall characteristics of beer. Brewers should consider water treatment techniques such as filtration, pH adjustment, and mineral additions to achieve desired brewing water profiles and enhance beer flavors.
Fermentation Management
Maintaining proper fermentation conditions is essential for consistent and successful fermentation. Brewers should monitor fermentation temperatures, yeast health, and fermentation progress to ensure optimal flavor development and attenuation.
Quality Assurance
Implementing quality control measures throughout the brewing process is crucial. This includes regular sensory evaluations, laboratory testing for key parameters, and adherence to standard operating procedures to maintain consistency and uphold quality standards.
Safety Measures
Brewery operations involve various hazards, including high temperatures, pressurized vessels, and chemical handling. Brewers should prioritize safety by implementing safety protocols, providing appropriate training to staff, and maintaining a safe working environment.
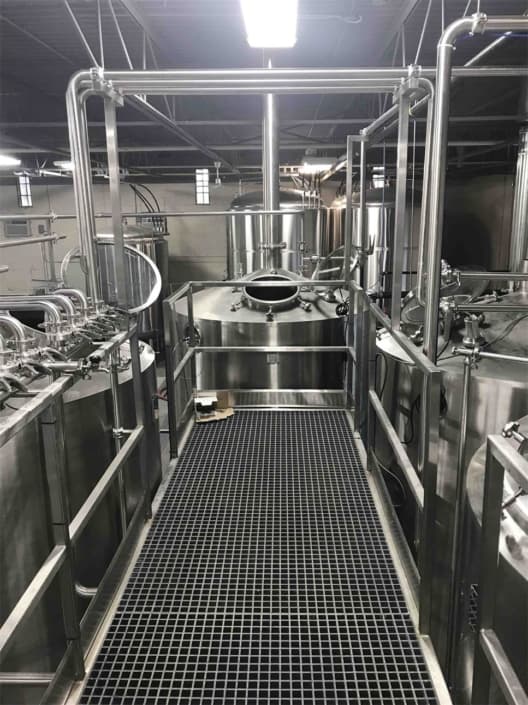
Conclusion
A 5bbl brewing system offers small to medium-sized breweries the ability to produce a significant volume of high-quality beer. By understanding its components, benefits, considerations, and best practices, brewers can effectively operate and optimize their brewing system. With scalability, efficiency, and control over the brewing process, a 5bbl brewing system becomes an essential tool for breweries aiming to meet consumer demand and create exceptional craft beer.
FAQs
1. How much beer can a 5bbl brewing system produce?
A 5bbl brewing system has a capacity of approximately 155 gallons or 580 liters per batch. It allows breweries to produce around 500-600 gallons (1900-2300 liters) of beer per week, depending on the fermentation and packaging schedule.
2. Can a 5bbl brewing system be expanded in the future?
Yes, one of the advantages of a 5bbl brewing system is its scalability. If a brewery’s production needs increase, additional fermenters and bright tanks can be added to expand the brewing capacity.
3. How long does it take to brew a batch with a 5bbl brewing system?
The brewing time can vary depending on the recipe and brewing techniques. On average, it takes around 6 to 8 hours for mashing, boiling, and cooling, followed by fermentation, which typically takes 1 to 2 weeks. Additional time is required for carbonation and packaging.
4. Can a 5bbl brewing system be used for pilot batches?
Yes, a 5bbl brewing system can be used for pilot batches. It allows brewers to test new recipes, experiment with different ingredients, and gather feedback before scaling up to larger production volumes.
5. What are some popular styles of beer brewed with a 5bbl brewing system?
A 5bbl brewing system can produce a wide range of beer styles. Popular choices include IPAs, stouts, pale ales, lagers, wheat beers, and specialty brews such as barrel-aged beers or sour beers. The versatility of the system allows brewers to cater to various consumer preferences and create diverse beer portfolios.