Table of Contents
ToggleOverview of the 5 BBL Brewing System
The term 5 BBL Brewing System refers to a brewing system with a capacity of 5 barrels (BBL), or approximately 155 gallons of beer per batch. This size is ideal for craft breweries looking to balance output and manageability. Compact yet powerful, these systems are designed for versatility, quality, and scalability.
- Capacity: 155 gallons per batch
- Ideal for: Microbreweries, brewpubs, and small craft beer producers
- Customization: Extensive options available for layouts, design, and additional features
- Materials: Typically stainless steel for durability and hygiene
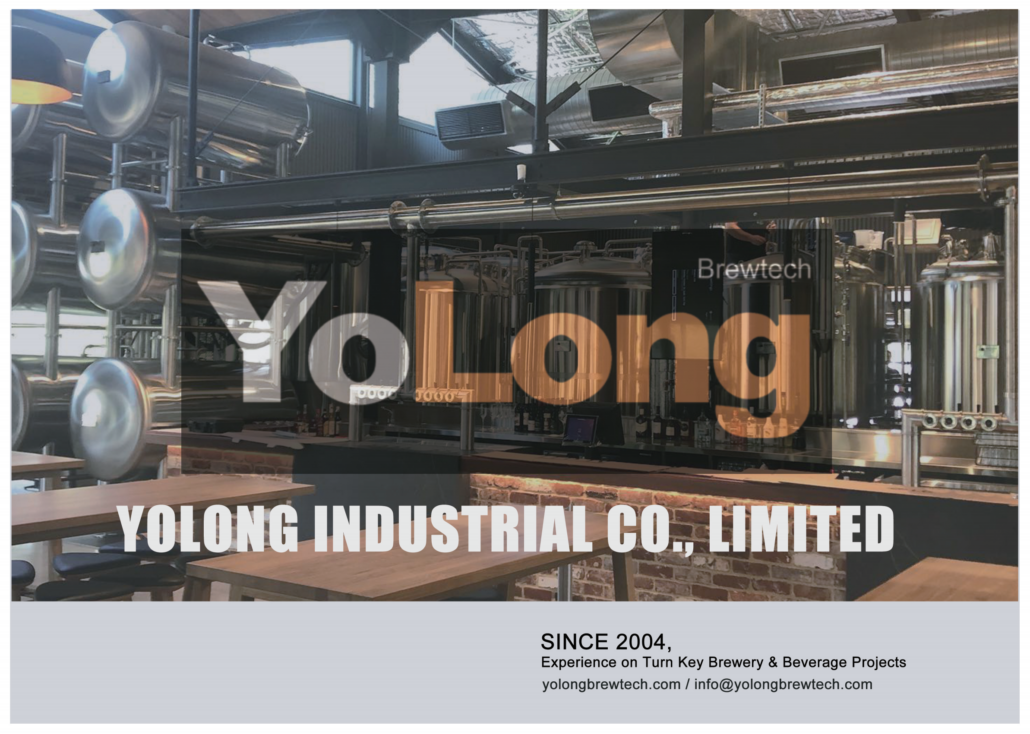
The Brewing Process in a 5 BBL System
Brewing with a 5 BBL system follows the standard beer production process but offers the flexibility and precision suited for craft brewing. Here’s a detailed walk-through:
- Mashing: The malted barley is mixed with hot water in the mash tun. Enzymes convert starches into fermentable sugars. This step sets the flavor profile.
- Lautering: The mash is transferred to the lauter tun. Here, the liquid wort is separated from the grain husks. Think of it as straining the essence from tea leaves.
- Boiling: The wort moves to the boil kettle, where hops are added for bitterness and aroma. Boiling sterilizes the wort and extracts the desired hop flavors.
- Fermentation: After cooling, the wort is transferred to fermentation tanks, where yeast is added. The yeast converts sugars into alcohol and CO2 over several days to weeks.
- Conditioning and Packaging: The beer is aged to develop flavors, filtered, carbonated, and finally packaged for distribution or serving.
Troubleshooting Common Issues with Beer Fermenters
Even with the best equipment, challenges can arise. Here are common fermenter problems and solutions:
- Temperature Fluctuations: Ensure glycol jackets or cooling systems are functioning properly. Calibration of temperature sensors is essential.
- Contamination: Maintain strict cleaning protocols and inspect seals and gaskets for wear.
- Pressure Imbalances: Regularly check pressure relief valves and adjust airlocks to prevent over-pressurization.
System Specifications and Customization Options
Capacity, Space Requirements, and Layout
Specification | Details |
---|---|
Batch Size | 155 gallons (5 barrels) per batch |
Footprint | Typically 150-250 sq. ft., depending on layout |
Material | Stainless steel (304/316 grade for hygiene and corrosion resistance) |
Design | Customizable layouts (inline, modular, or stacked) to optimize space usage |
Heating Options | Steam, direct fire, or electric heating |
Supplier and Price Range
Supplier | Price Range | Special Features |
---|---|---|
ABC Brewing Systems | $30,000 – $50,000 | Modular designs, advanced automation |
BrewTech Industries | $35,000 – $55,000 | High-efficiency heat exchangers, premium finishes |
CraftBrew Solutions | $28,000 – $45,000 | Compact layouts, robust warranty |
Premier Stainless | $40,000 – $60,000 | Fully customizable options, excellent after-sales |
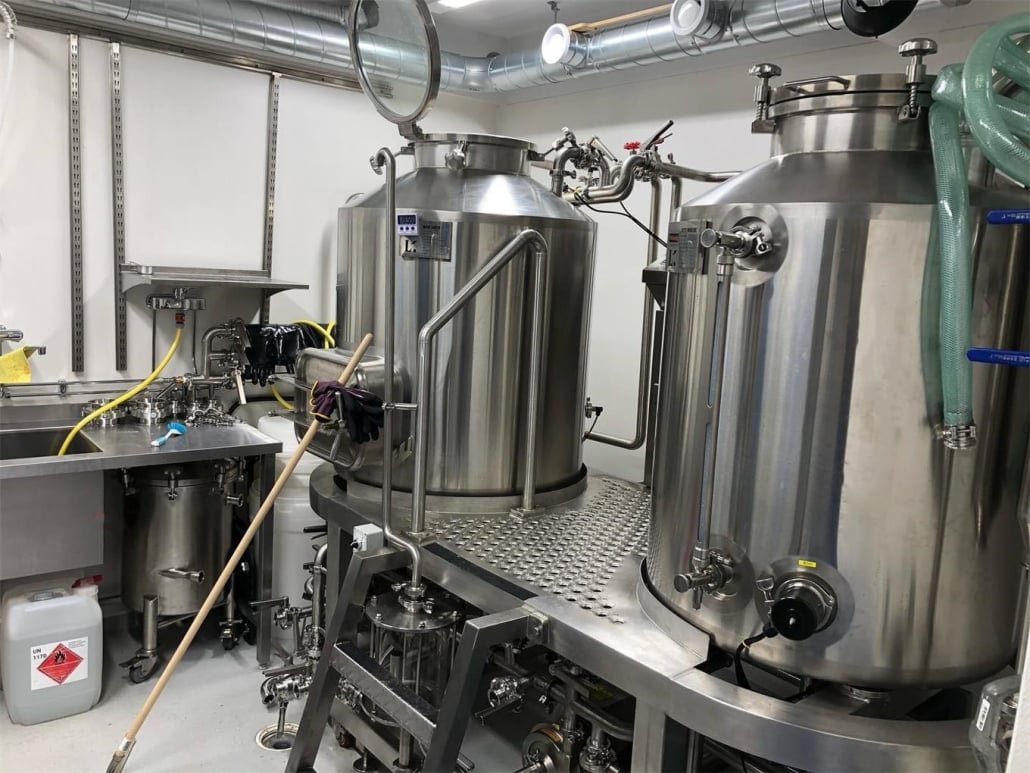
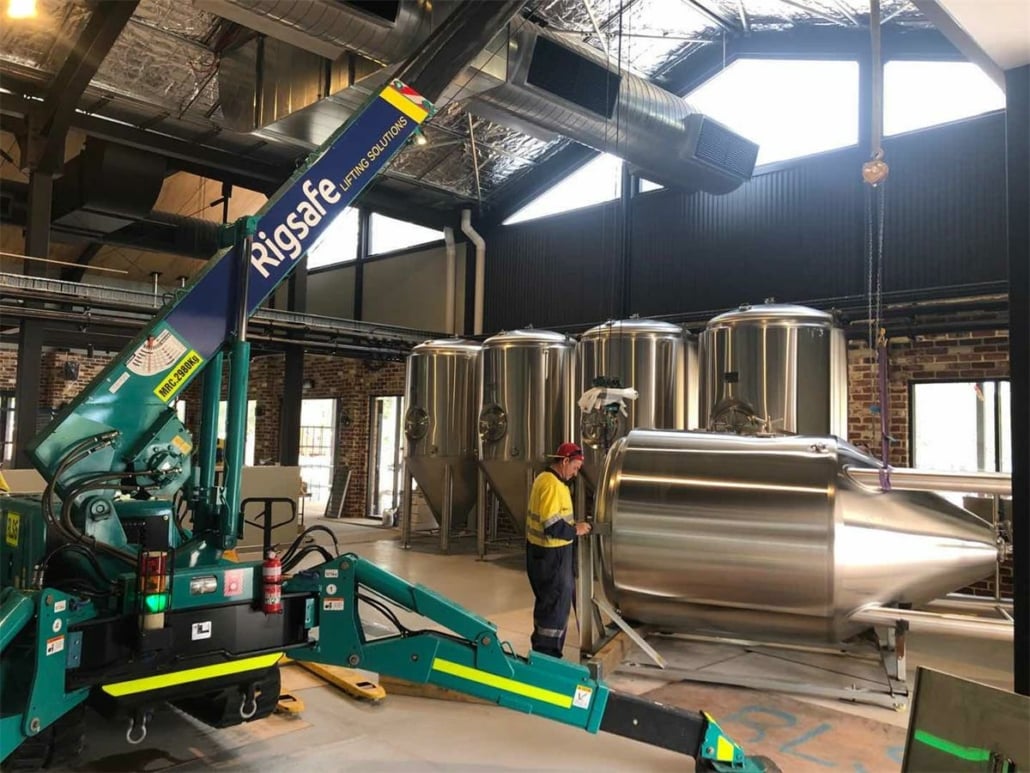
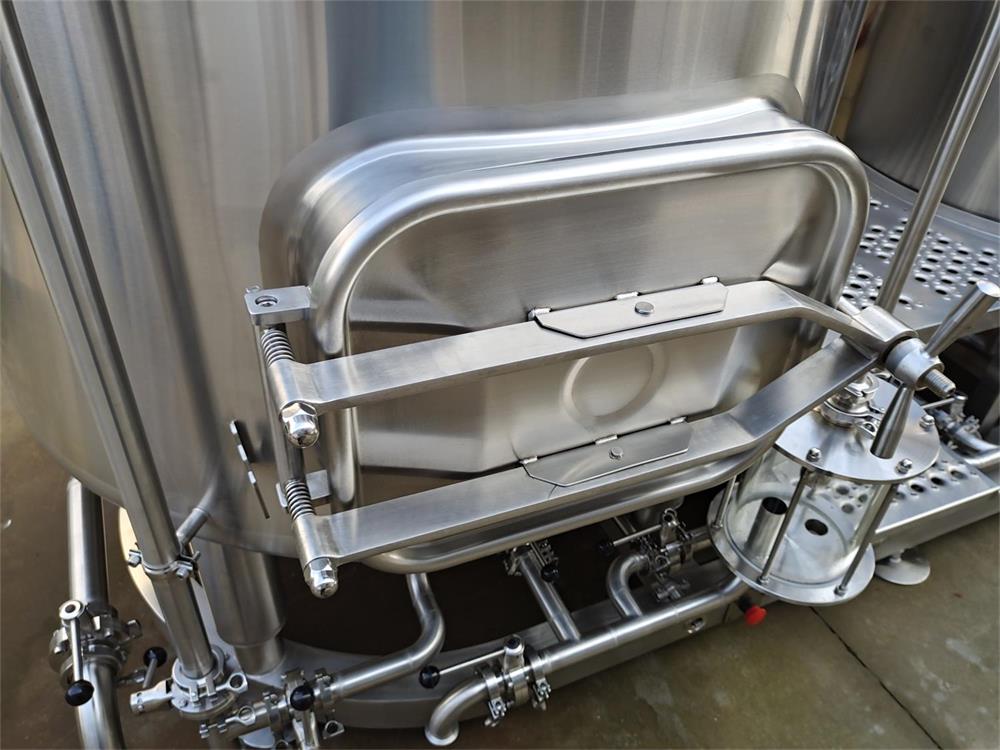
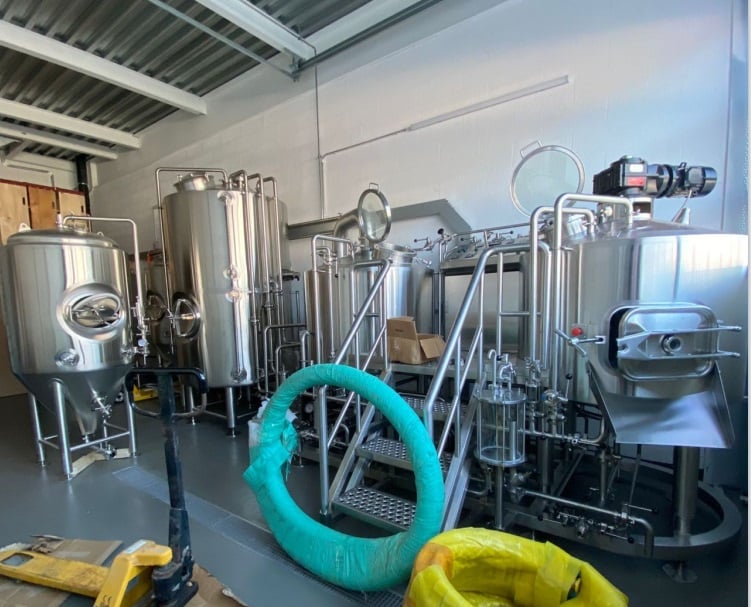
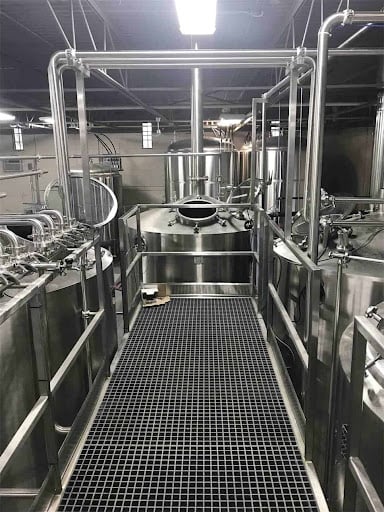
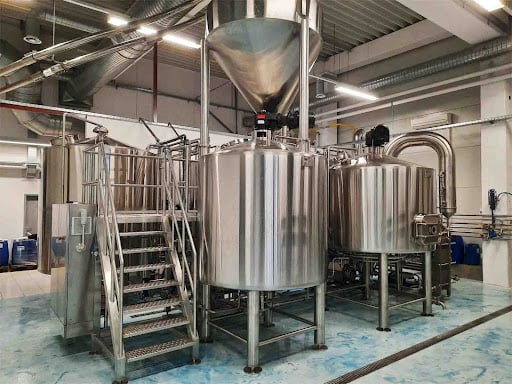
Installation, Operation, and Maintenance
Aspect | Details |
---|---|
Installation | Professional setup required; plumbing, electrical, and ventilation connections needed |
Operation | User-friendly interfaces; touchscreens and automation available for precision |
Maintenance | Regular cleaning with CIP systems; biannual inspections of gaskets, pumps, and hoses |
How to Choose the Right Supplier
Selecting a supplier for your 5 BBL brewing system is a critical step. Here’s how to make the best choice:
- Reputation: Research reviews and case studies. A proven track record is invaluable.
- Customization Options: Ensure the supplier can meet your specific layout and design needs.
- After-Sales Support: Look for comprehensive warranties and responsive customer service.
- Budget: Compare prices against features. The cheapest option isn’t always the best.
- Scalability: Choose a system that can be expanded as your brewery grows.
Factor | What to Look For |
---|---|
Customer Reviews | High ratings, positive testimonials, and repeat customers |
Support Services | Installation, training, and quick spare parts availability |
Quality Assurance | Certifications like ISO 9001 or adherence to brewing industry standards |
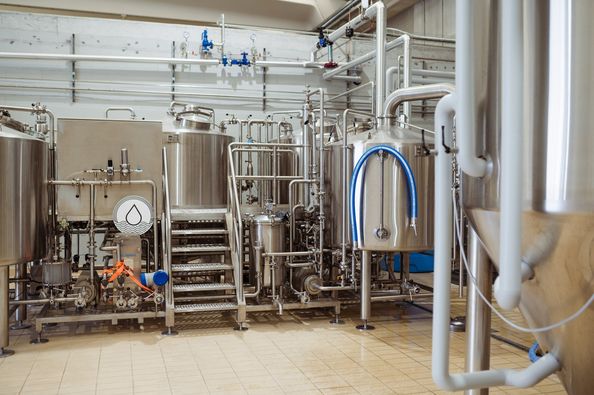
Advantages and Limitations of a 5 BBL Brewing System
Advantages
- Scalable Production: Perfect for testing recipes and producing craft batches without overcommitting.
- Cost-Effective: Lower upfront investment compared to larger systems.
- Compact Size: Fits in limited spaces, ideal for urban breweries or brewpubs.
- Customizable Features: Tailor the system to your specific brewing style and space constraints.
Limitations
- Limited Batch Size: Unsuitable for large-scale commercial production.
- Higher Manual Intervention: Smaller systems may lack full automation.
- Upgrade Costs: Expanding production might require significant investment in new equipment.
Aspect | Advantages | Limitations |
---|---|---|
Size | Compact, fits smaller spaces | Limited output per batch |
Cost | Affordable initial investment | Higher cost per gallon compared to larger units |
Flexibility | Easy recipe experimentation | May require manual adjustments |
FAQs
Question | Answer |
---|---|
What is a 5 BBL brewing system? | A brewing system with a capacity of 5 barrels (155 gallons) per batch. |
Who should use it? | Ideal for microbreweries, brewpubs, and small-scale craft brewers. |
What is the cost range? | Typically ranges from $30,000 to $60,000, depending on features. |
What heating options are available? | Steam, direct fire, and electric heating systems. |
How is it cleaned? | Cleaning-in-Place (CIP) systems are commonly used for sanitation. |
Can it be upgraded? | Yes, modular designs allow for scalability as production increases. |